Magnetic crop spraying systems: future or fallacy?
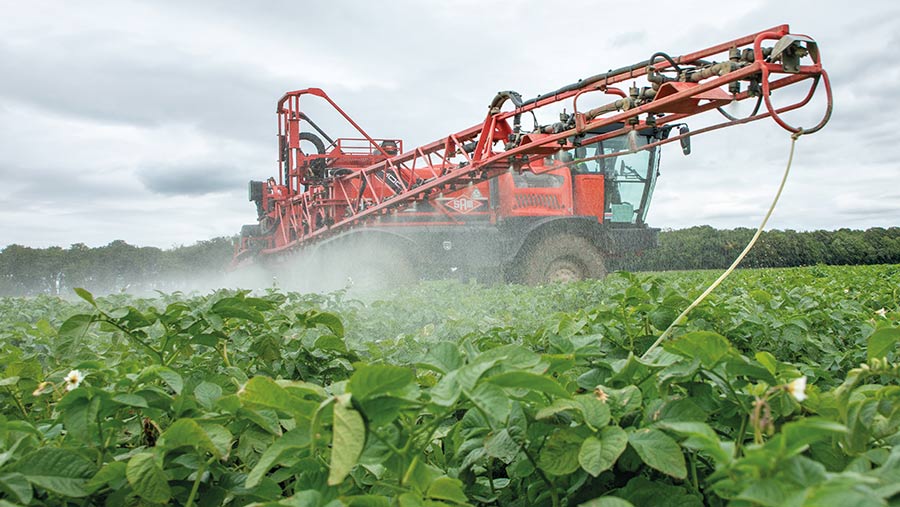
There have been plenty of attempts at engineering ways to reduce spray drift over the years and, like a fine droplet on a windy day, many have wafted off into relative obscurity, rarely seen again.
One firm trying to buck this trend and make its solution stick is Irish company MagrowTec, which claims its spraying system helps more droplets hit their intended target.
However, finding independent, scientifically robust evidence that demonstrates exactly how magnets can achieve this is hard, and conflicting farmer testimonies further muddy the water.
So, should UK growers be attracted to invest in a system that costs about £880/m to retrofit?
See also: Broadacre spot spraying kits: All you need to know
Conventional weakness
The major weakness of conventional crop sprayers is drift, with fine droplets produced through standard nozzles affected by boom height and taken off course by wind and/or warm temperatures.
Over the past 10-15 years, clever nozzle technology, such as air induction to increase the droplet size, has allowed operators to reduce the problem.
However, some argue that the larger droplets created by low-drift nozzles compromise coverage and distribution.
To remedy this, air-assisted sprayers use fans to force spray downward to hit the ground or better penetrate a crop’s canopy, attempting to find a balance between drift reduction and coverage.
The catch is that they can be tricky to set up correctly and require constant tweaking to suit conditions, so are not widely used.
Electrostatic sprayers have the same aim, but positively charge the spray with high-voltage electricity close to the point of droplet formation, making it more likely to land on neutral objects such as a plant or seed-bed.
Electrostatic systems are expensive and studies on drift, coverage uniformity and canopy penetration are lacking, so like air-assist, adoption has been relatively low.
These weaknesses seem to have been addressed by a magnetic spraying system from MagrowTec because, once fitted, the sprayer operates exactly as it did before, and it requires very little maintenance.
Initially developed by a Florida-based farmer who had become frustrated by the complexity of his electrostatic sprayer, commercial rights for the technology were acquired by agri-tech start-up Magrow (now MagrowTec) around 2012.
After going through four years of development and testing, it was marketed to farmers in 2016 as a solution to the coverage versus drift dilemma.
How it works
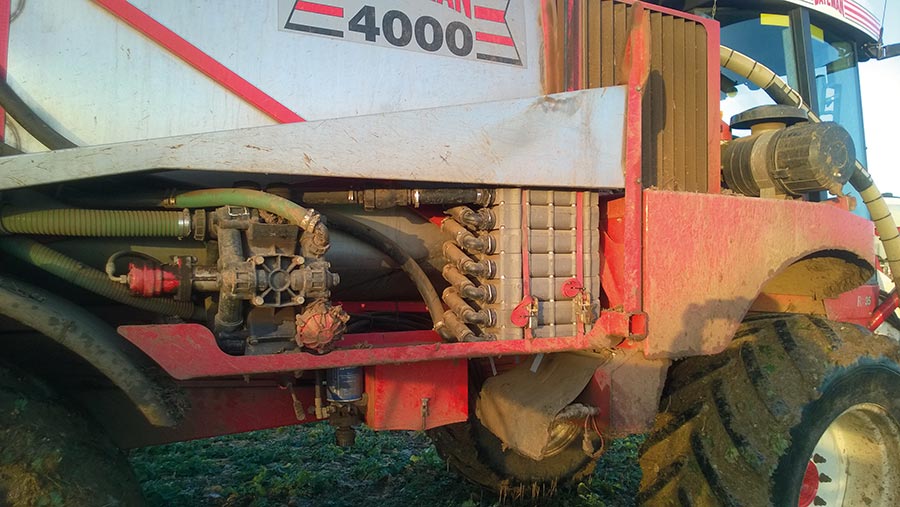
MagrowTec’s spraying system © Andrew Myatt
Spray droplets less than 100µm (microns) have low kinetic energy, so give excellent target coverage and low bounce and shatter, but they have high potential for drift and evaporation, and achieve poor canopy penetration.
Conversely, large droplets greater than 350µm have high kinetic energy, can penetrate a crop canopy well and have low drift and evaporation potential.
However, these larger droplets can bounce and shatter, leading to poorer coverage. This reduces efficacy for products such as contact-acting herbicides.
MagrowTec says a conventional sprayer produces more droplets in these undesirable sizes and fitting its magnetic system helps produce a narrower range, with more in the optimal 150-300µm band.
It does this by pre-conditioning the spray solution before it reaches the nozzle, first passing it through a manifold made up of several rare earth magnets, then rare earth magnet conditioning rods encased within the spray lines.
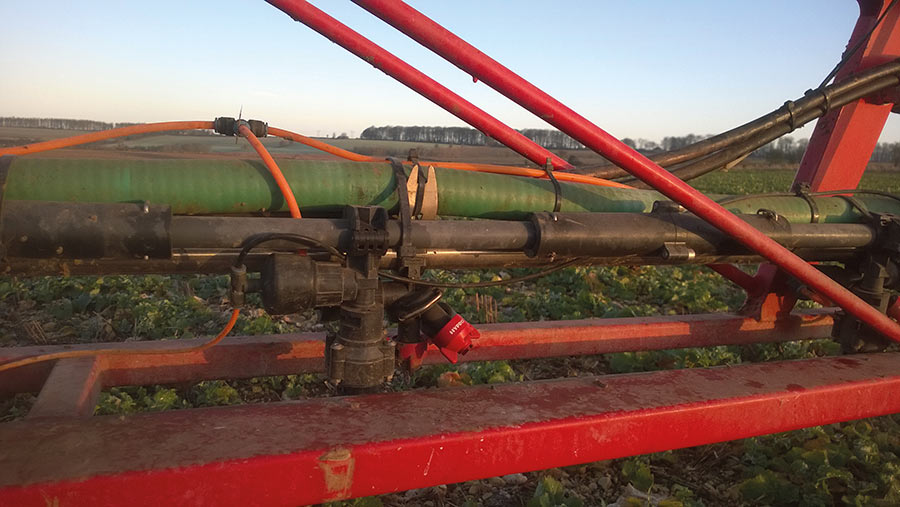
Magnetic rods © Andrew Myatt
The resulting spray is said to have a medium drift potential, while also improving coverage and canopy penetration, reducing bounce and shatter, and lowering the risk of rapid evaporation.
The science is complex and MagrowTec is guarded on the details to avoid giving away its intellectual property.
However, searching through literature, studies seem to suggest that conditioning of water with a magnetic field can strengthen hydrogen bonds, altering its surface tension and viscosity.
The “MagrowTec effect” alone is said to reduce drift by about 70% and increase coverage by 20-40%, depending on the crop.
The firm says this leads to yield improvements in certain situations and has enabled some operators to reduce the chemical dose by 25% for some applications without losing efficacy.
The knock-on is a better margin for the grower.
Other benefits include lower water rates, better environmental compliance, and enhanced spray windows, owing to its ability to work more effectively in higher winds.
However, taking time to search for independent studies finds little evidence to back up the headline-grabbing figures and additional claims.
Drift reduction
MagrowTec’s system is classified as a 97.5% drift reduction technology (DRT) in the Netherlands under the country’s regulations to minimise drift into its many watercourses.
The 2017 Wageningen University study that led to this classification tested it against Dutch, UK, and French national drift standard reference spray techniques.
The Dutch and UK standard is a sprayer operating at 50cm boom height and 50cm nozzle spacing at 6.5kph forward speed, using TeeJet XR110 04 flat fan nozzles at 3bar pressure. Water rate is 300 litres/ha.
The French system operates at 70cm boom height and 8kph forward speed using TeeJet XR110 02 flat fan nozzles at 2.5bar pressure. Water rate is 230 litres/ha.
Nozzle types tested with MagrowTec system at Wageningen
- Setup 1: Standard flat fan Hypro 11003 + TeeJet UB8503 end nozzle
- Setup 2: TeeJet AI 110 03 (50% DRT) + AIUB5803 end nozzle
- Setup 3: Lechler ID-120-03 (90% DRT) + IS 80-03 end nozzle
Drift results
Results showed that the French reference system resulted in the highest spray drift deposition in ground collectors.
This was followed by the Dutch-UK and MagrowTec systems with a standard flat fan nozzle, which were similar. The MagrowTec with 50% and 90% DRT nozzles resulted in the lowest spray drift deposition.
Airborne spray drift at 5.5m from the last nozzle was also measured, and the results showed a very similar pattern.
However, examining the trial protocols, the sprayer fitted with the MagrowTec system was operated at 40cm boom height, which is 10cm lower than the applications using the French and Dutch-UK reference systems.
The closest like-for-like comparison in the trial is the standard flat fan at 50cm boom height and MagrowTec with standard flat fan at 40cm, and drift reduction results were comparable.
As boom height has a significant influence on spray drift, operating 10cm lower could have shown the MagrowTec system in a slightly more favourable light in this trial, which was commissioned and financed by the Dublin-based firm itself.
On page 27 in the final Wageningen University report, the authors state:
“Because of the setup of the spray drift measurements as a package of combinations the effect of the magnetism of the [MagrowTec] system alone could not be discriminated.”
Controversial technology
Silsoe Spray Applications Unit research manager Clare Buttler-Ellis tells Farmers Weekly that it is difficult to understand how a magnetic system for sprayers might work.
She says there have been several theories over the years, but none are widely accepted among the research community. This means the potential for magnetic fields to affect spray droplets remains controversial.
“We continue to watch this space with interest. So far, I haven’t come across any credible evidence that magnets can influence the performance of a spray application.
“What I would really like to see are some independent experiments, using recognised measurement techniques, simply comparing deposits, efficacy or drift for identical systems with and without the magnets, so that we can see their direct effect unambiguously.”
Another UK source, who didn’t want to be named, says evidence to support claims on chemical dose reductions is particularly important because plant protection products are subject to years of development and testing to optimise efficacy in the field.
This includes the recommended label dose, which has a degree of wriggle room for the user so efficacy is maintained if the crop or target organism is under-dosed during application.
Therefore, it’s possible that a MagrowTec user could be happy with control of a disease when applying 25% less chemical, but might have been equally pleased with the same dose applied through a conventional sprayer in the same conditions.
MagrowTec chief financial officer Mel Hurley says he is aware of scepticism about magnetic spraying. However, the company stands steadfast by the technology.
“All we can do is keep producing positive sets of results from the trials we do with real growers, and other stakeholders in the spray industry, in the field.
“The reality is [that] on the ground, we are seeing positive, consistent results both in terms of efficacy, coverage, water reductions, rate reductions and as I say, in certain jurisdictions, where it is applicable, they are seeing drift benefits as well.
“If we didn’t see the results on a consistent basis, then we wouldn’t be progressing the way we have been,” says Mr Hurley.
The firm is now focusing most of its efforts in US, Australian and Dutch markets, where it has had some penetration, particularly on farms growing cotton and potatoes.
It remains to be seen whether the system will ever be commonplace on farms here in the UK, where there is still no authorised dealer, six years post-launch.
Using the technology
Andrew Myatt, farm foreman, Stowell Park Estate, Gloucestershire
Former Farm Spray Operator of the Year Andrew Myatt found no significant benefit after testing a MagrowTec system over a 12-month period.
Mr Myatt was first introduced to the potential of magnetic spraying technology at the Lamma machinery show and was impressed by the claims of improved coverage and reduced drift.
However, as it was early days for the technology, he wanted to prove the concept on-farm before considering a purchase. MagrowTec agreed and installed a system to his Bateman RB35 for a trial period.
The pre-conditioning manifold was tucked neatly in front of the pump on the right-hand side of the machine and twin lines were installed, one fed via the manifold and fitted with magnetic rods, and one without.
This allowed Mr Myatt to easily switch between the two to set up strip trials across the farm. These were run over the course of the 2016-17 season in a range of crops, including winter wheat, oilseed rape, winter barley and spring barley.
The MagrowTec-treated and untreated blocks were then taken to harvest, with yield data collected and analysed by farming company Velcourt’s R&D team.
Results showed no significant difference in crop performance between treatments.
A drift comparison trial was also conducted during the season using a range of conventional and air induction flat fan nozzles commonly used in UK crops.
Mr Myatt says there were moments when the magnet-conditioned spray appeared less drifty, but otherwise it looked like any conventional sprayer and there were no significant differences between systems.
With the business keen on scrutinising every investment in machinery or technology, the data from the trial allowed it to do so before committing to buy the MagrowTec kit.
“You always have to ask – what will we get in return? The system isn’t going to give us improved yield, less drift or more spray days.
“I’ve tried to find information on the science, and there was not a lot of evidence supporting what they are trying to achieve. We gave it its best shot in fair trials with proper protocols over a 12-month period and found no justification for its use.”
Lena Bleeker, Friesland, The Netherlands
Near the north coast of the Netherlands, Lena Bleeker says her 300ha farm is saving about 25% on chemical use since adopting the MagrowTec system in 2017.
The business produces seed potatoes, sugar beet, wheat and onions and was first introduced to the MagrowTec system back in 2014.
The agri-tech start-up was looking for growers to make up an advisory board to provide it with practical advice as the product was being developed, and to host trials.
Lena and her husband Gosse Schuiling– who carries out a proportion of the spraying and sits on the advisory board – agreed to compare the machine against their farm standard.
In the trial, the MagrowTec system applied late blight fungicide sprays to potato crops using with 25% less chemical than usual.
“We saw no difference [in disease control]. The crop was the same and all healthy, but with less chemicals. That was our goal and we proved that it could work,” explains Mrs Bleeker.
When the business was in the market for another sprayer, it opted for a 51m Agrifac Condor and had the MagrowTec system fitted from new, based on evidence in the trial.
It has since had another MagrowTec retrofitted to a 32m trailed Amazone, which carries out all the application work on a satellite farm near Groningen.
Mrs Bleeker says the farm has made similar savings across almost all applications and crops, with only residual herbicide applications applied at full dose.
“You earn your money back in three to five years, depending on the amount of chemical you use already. At a time when costs are increasing, it’s even more beneficial to look at this system.”
Another major plus has been the simplicity of MagrowTec, as there is no requirement for additional power like other spraying systems, maintenance is almost zero and the operator only requires one set of 110-03 flat fan nozzles for most applications.
“We are also using less water, so spraying more hectares with the same tank and using less labour. Before, we [typically] used 250 litres/ha, but now we use 200 litres/ha.”