Broadacre spot spraying kits: All you need to know
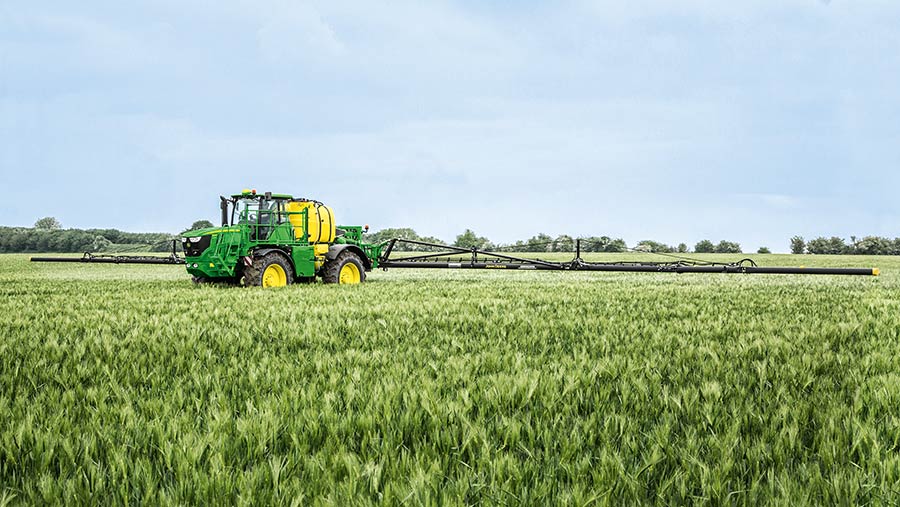
Weed identification has been a cornerstone of arable farming for centuries, but it may no longer rely on keen eyes, muddy wellies and an encyclopaedic knowledge of botanical enemies.
That’s because there are a handful of technology companies building weed identification kits for sprayers that spot target species and dish out an immediate blast of chemical.
The systems are only just being transformed from computer models to commercial offerings, but their makers claim they will slash herbicide costs by more than 80% compared with blanket field applications.
In many parts of the world, fence-to-fence applications have caused a surge in herbicide resistance that has damaged crop profitability – both through extra spray passes and in the exorbitant cost of effective licenced chemicals.
But by targeting specific weeds at single-nozzle accuracy, growers have the option of applying a more potent mix where it is needed, or to use products that might otherwise have a harmful effect on the crop.
Research at Wageningen University in the Netherlands suggests crops deliver better growth rates and yields where green-on-green spot spraying has been used because the plants expend less energy detoxifying the herbicide.
See also: 6 budget GPS guidance system options for farmers
Early iterations
Spot spraying isn’t an entirely new concept – the Silsoe Research Institute first trialled patch spraying in the late 1990s by treating 2x4m cells with different herbicides, though the project ended with the institute’s closure in 2006.
However, after a decade-long hiatus there are now four main players combining cameras and artificial intelligence in the so-called ‘green-on-green’ market – Bilberry, Carbon Bee Agtech, Blue River and Bosch.
Their systems work a bit like facial recognition technology to spot particular plants based on shape, colour and texture, before making a split-second decision on whether to spray or not.
Bilberry won the race to market by keeping things relatively simple. Its RGB colour cameras can be ordered on Agrifac, Berthoud and Dammann sprayers and, by the end of this year, could well be available with software to spot several weed species in growing crops.
Carbon Bee Agtech has taken a more high-tech approach by integrating sophisticated hyperspectral and infrared cameras into its hardware. The images they provide require more deciphering, so the system will inevitably take longer to get up and running.
However, the level of detail they provide mean they could also be used to detect plant diseases and nutrient deficiencies before they are visible to the human eye. The company has agreements with Kuhn and Berthoud.
Blue River, owned by John Deere, plans to start farm-scale testing of its spot spraying system this year. It has yet to reveal what type of sensors it is using but, like the competition, will start with detecting weeds on stubbles before offering targeted sprays in growing crops.
The last of the four is German tech firm Bosch, which has worked with BASF to develop a kit that it is now fitting to Amazone sprayers.
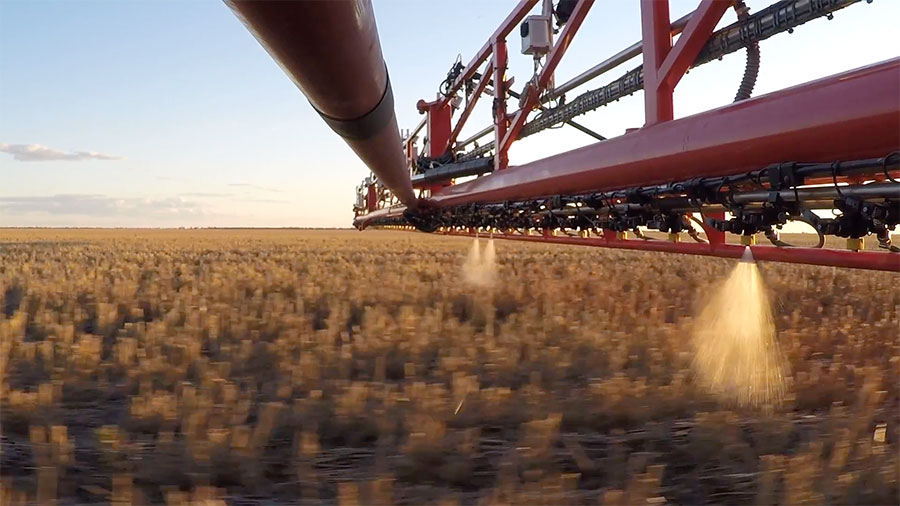
Bilberry AiCPlus spotspraying
Bilberry – Intelligent Spot Spraying System
System summary
- Status – Green-on-brown and docks in grassland (green-on-green) available now
- Camera – RGB at 3m spacing
- Working speed – Up to 25kph
- Used for – Herbicide applications
- Available on – Agrifac, Berthoud, Dammann and Goldacres sprayers
Few tech start-ups have influenced the agricultural industry quite as profoundly as Paris-based Bilberry, with its weed-identifying spot spraying kit now a premium option on self-propelled sprayers from Agrifac, Berthoud and Dammann, as well as Goldacres in Australia.
Though the company only started in 2016, it is the first to get a green-on-green system working in earnest on broadacre farms in Europe and Australia thanks to a fast-paced development plan.
Central to this has been the use of off-the-shelf hardware, including electrical components – cameras, cables and screens – designed for autonomous vehicles.
“Developers of this equipment have plenty of money and it’s a fast-moving sector, which means we can constantly update our hardware without having to design it ourselves,” says Bilberry CEO Guillaume Jourdain.
Similarly, the company uses software from GPS specialist Emlid to transmit information between the camera, computer, screen and sprayer.
However, the software that gets the components talking to one another is developed by Bilberry’s team of data scientists, as is the business end of the system – the complex algorithms that make sense of the information.
These are able to identify weeds by evaluating their colour, texture and shape, comparing them to a vast database to decide in a split second whether to activate the nozzle or not.
How does it work?
High-definition RGB cameras mounted at 3m intervals feed information into their own computer modules, which then talk to the sprayer’s rate controller.
These cameras detect red, green and blue bands of light, producing images that are almost identical to those seen by a person.
The basic rule is that if you can’t see the weed when standing above the crop then the camera will struggle as well – they have more or less the same resolution as a human eye, albeit with a faster brain.
Where the system is used solely for spotting weeds on harvest stubbles – so-called green-on-brown detection – colour is the most important factor. In these circumstances, the system has a hit rate of over 93% on plants bigger than 3cm.
For dealing with weeds in growing crops – the green-on-green scenario – the shape of the plant’s leaves provides a better means of identification. Developing the algorithms for this requires a more detailed library of pictures and data processing is more complicated.
So far, the company is only selling this system for identifying docks in grass crops, though extensive trials are taking place to improve its ability to spot other species.
“In Australia, our priority is wild radish, as herbicide resistance is building and growers only have access to one effective product – Velocity (bromoxynil + pyrasulfotole) from Bayer – which is very expensive”.
“We’re starting our biggest trial programme in June for this specific weed, followed by other tests in Europe,” says Mr Jourdain.
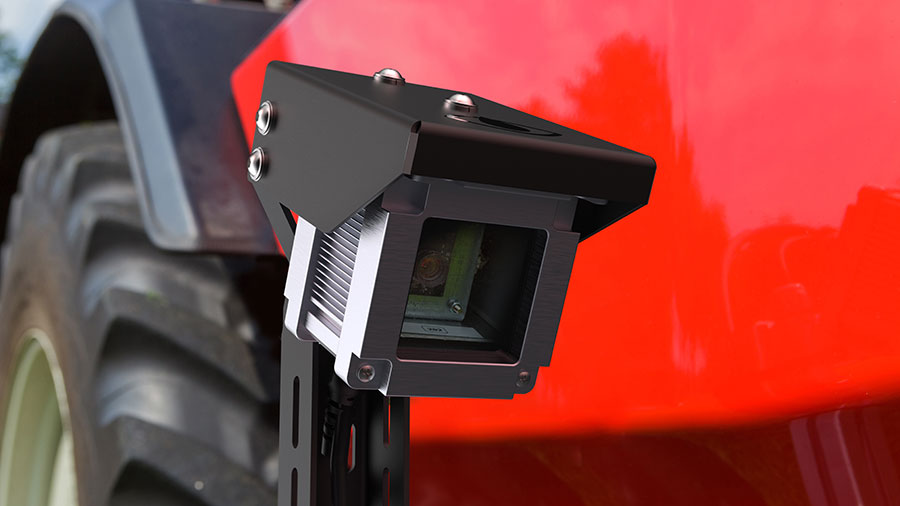
Bilberry AiCPlus camera
When will it be available?
The green-on-brown system can be specced on new sprayers for a one-off cost determined by the manufacturer. “The starting point could be about £60,000, but that can go up to £100,000 with wider booms and all the options,” says Mr Jourdain.
Bilberry aims to have more green-on-green applications available next year, but there is no word yet on how many, nor which ones – it all depends on the success of the trials.
Mr Jourdain suggests that buying the software may involve a subscription-type contract. For farmers, it could mean paying annually for access to a particular set of algorithms with the aim of targeting specific weeds, such as wild radish.
“For Bilberry, that kind of pricing structure allows us to keep updating and improving the software. This work costs money, but it also guarantees that there are benefits to farmers in the long term.”
What’s the future?
Expanding the botanical library to identify other weeds is the priority, but the colour cameras are also able to monitor green area index. This is a useful factor in determining crop nitrogen requirements.
Further down the line, the company is eyeing more sophisticated camera systems to detect crop stress before it is visible to the naked eye, which could allow for targeted fungicide applications.
Hyperspectral cameras, such as those used by fellow French firm Carbon Bee, can detect up to 200 colours to provide far more detail on crop conditions. However, this is “two or three years away”, according to Mr Jourdain.
Carbon Bee Agtech – Smart Striker
System summary
- Status – Trials under way
- Camera – RGB, hyperspectral and infrared at 3m spacing
- Working speed – 18kph, but 25kph on commercial versions
- Used for – Herbicides, fungicides, fertiliser
- Available on – Kuhn, Berthoud
Carbon Bee, based in south-east France, has taken a more high-tech approach to spot spraying by incorporating three types of sensor on its Smart Striker.
Like Bilberry, it uses RGB cameras to distinguish weeds in stubbles or growing crop.
However, Carbon Bee can go one step further by spotting stresses within the crop. This is achieved by the second element of the lens clusters – high-definition hyperspectral cameras.
These can see huge detail in up to 200 colour bands, identifying weeds by comparing their spectral signature (the light reflected back from the plant), shape and texture with those in the firm’s vast database of botanical information.
Fritzmeier uses a similar type of camera on its crop sensors to monitor normalized difference vegetation index (NDVI) or green area index (GAI). Both are useful for determining nitrogen requirements and crop stresses caused by disease – things Carbon Bee intends to offer in the future.
The third sensor in the package uses infrared. It is employed predominantly for detecting live plant matter on stubbles but, as plants send a lot of information in the infrared spectrum, can also see diseases invisible to the human eye.
The advantage of the triple sensor cluster is that it gathers information across a much broader wavelength than those that rely solely on RGB cameras.
“It means green-on-brown, green-on-green and nitrogen analysis based on green area index or NDVI are all possible without changing any of the hardware,” says Carbon Bee Agtech’s Victor Delaune.
The downside of the extreme level of detail is that the systems used to process the information are far more complicated and time consuming to develop.
But that doesn’t necessarily translate into a more expensive product, says Mr Delaune. Though the end price is determined by sprayer manufacturers, Carbon Bee at present charges less than €1,500/m (£1,310/m) for the hardware on prototype versions.
There’s a further licensing fee of €10,000/year (£8,740).
“These numbers will probably change depending of the policy of the manufacturers but we’re fighting to keep the prices as low as possible to make it accessible to the customers.”
How does it work?
In the cab, operators simply select the application, such as detecting a brassica in cereals.
All of the information required to process the images is in the sensors, which then talk to the sprayer controller to engage individual nozzles.
“We can form spraying maps that mark all the weeds in the field, which farmers can use to make future decisions,” says Mr Delaune. “They can also be combined with yield or soil maps to assess the spread of weeds or disease and how they have impacted yields.”
The sensors are capable of working at speeds of 25kph on stubbles or 17kph in green-on-green scenarios, detecting weeds from the two-leaf stage.
When will it be available?
The company has conducted trials in Europe and is relatively close to having a green-on-brown system commercially available, with strike rates close to 100%.
Green-on-green systems will be a longer wait, particularly those involving more challenging weed/crop combinations such as grasses in cereals. Its four test machines have so far delivered a strike rate of 80-90%.
Nitrogen and fungicide spot spraying projects are also in the works.
Alongside the spot spraying system, Carbon Bee is running extensive trials looking at multi-dose applications. These involve a low rate blanket application across the field, which would be adequate to knock out small, undetectable weed seedlings. When the cameras spot a target weed species, the rate at specific nozzles is upped automatically.
Current estimates suggest this system will cut herbicide use by 50-60%. That’s some way short of the 80-90% savings of spot spraying but offers an appealing halfway house for farmers looking to move away from blanket applications.
Blue River – See & Spray
System summary
- Status – Trials starting this year
- Camera – Unknown
- Working speed – Unknown
- Used for – Herbicides
- Available on – John Deere
Californian start-up Blue River was the subject of a $305m (£231m) takeover by John Deere in 2017.
Prior to the deal, Blue River had made its name with the See & Spray system for thinning lettuce crops. Working at slow speeds for sub-2cm precision, it selects undesirable plants and coats them with a toxic salt solution.
It was this ability to make and act on in-field decisions using AI and machine learning, rather than the particular application of lettuce thinning, that convinced Deere to part with its cash. Since then, the aim has been to adapt and develop the system to work on broadacre sprayers.
It’s not the first time that the company has invested heavily in the precision agriculture market, having acquired leading GPS specialist Navcom – subsequently responsible for the creation of the Starfire guidance system – back in 1999.
“Though we were working with deep learning and AI prior to the acquisition, Blue River had assembled a critical mass of expertise on how to apply it to an agricultural problem,” says general manager of the See & Spray division, Than Hartsock.
Though things have gone ghostly quiet since the takeover, work to adapt the cameras and deep learning models to differentiate between weeds and crop in agricultural conditions is apparently moving at pace.
Versions have even been fitted to some of Deere’s self-propelled sprayers, which will be “in the field this season” for testing.
“These systems thrive on data, so the more exposure the equipment has to different conditions the more reliable and valuable it will be for farmers.”
How does it work?
John Deere is frustratingly tight-lipped about the technicalities of what it describes as its “see, decide and actuate” system.
What is clear is that the company has been making use of technology from other industries – self-driving cars, in particular – to speed up the development process.
“But this equipment is only so useful,” says Mr Hartsock, “and many of the components will still have to be developed in-house because the vibration and dust of a field environment presents such a unique challenge”.
Though Deere has offered no insight into the type of camera or sensor it is using, early iterations will allow for green-on-brown detection, with later updates adding green-on-green spraying. This follows the same path as that of Bilberry and Carbon Bee, so it’s fair to assume there will be similarities in the choice of hardware.
Deere’s advantage over the competition is that it builds both elements – sprayers and spot spraying kits – so will be able to adapt quickly to operator demands.
To achieve accurate, plant-level applications, the system will most likely be partnered with Deere’s Exactapply pulse width modulation system. This allows for variations in application rate without altering the spray pattern – ideal for a weed-targeting on-off applications and variable rate blanket treatments.
Like other spot spraying systems, early estimates suggest it could slash herbicide application rates by up to 90% and its aim is to deliver “performance equal or greater than that achieved by broadcast sprays”.
When will it be available?
A small number of units will be working this season to collect more data, fine-tune the sensors and actuation system, and monitor performance.
There’s no word on when it might be on sale, but next year’s Agritechnica event is a plausible date for the launch of early prototypes.
It’s too early to talk about pricing, says Deere, but the company insists it will offer “significant savings” for farmers by spraying the right amount of herbicide on the right plants.
The system could also be applied to other field passes, particularly as Deere acquired Monosem in 2016. The French firm builds inter-row hoes that could be equipped with the technology.
Bosch/BASF – Smart Spraying
System summary
- Status – Available to sprayer manufacturers next year
- Camera – RGB at 1m spacing
- Working speed – 14kph
- Used for – Herbicides
- Available on – Amazone
German companies Bosch and BASF have put their financial clout behind a complete spot spraying package.
Development work started in 2016 and initially involved Bayer, whose database of 3D weed images formed the central element in the building of algorithms. However, Bayer subsequently agreed to sell its digital farming projects to rival BASF so as to complete the $66bn purchase of Monsanto.
The collaborative effort sees Bosch provide all of the hardware, including the cameras, image processors and spray controllers – much of which has already been developed for automated driving.
This talks to Xarvio’s Field Manager, which records information collected by the cameras to provide growth stage estimates, disease and pest risk and biomass maps that help determine fertiliser requirements.
The two companies announced at last year’s Agritechnica show that they were to fit the equipment to Amazone sprayers.
How does it work?
Bosch uses RGB colour cameras mounted at 1m intervals, which scan the soil in 25cm-wide bands.
Amazone’s PWM-specced sprayers carry a standard spray line for full-width applications and a second fitted with Spotfan 40-03 nozzles, set at 25cm spacings.
These have a 40deg spray angle to minimise the overlap across bands, which Amazone says will reduce the risk of resistance problems caused by underdosing at the outermost points of each nozzle’s reach.
Processing modules attached to the camera decide when to open the PWM valves, with the process of recognising and spraying a weed taking just 300 milliseconds.
For now, the algorithms can only distinguish weeds from crop, though they apparently deliver a theoretical strike rate of more than 99% at speeds up to 14kph. However, like most of the other systems in development, the real-world hit rate is likely to be 5-10% lower because weed plants are undetectable when hidden under the crop canopy.
Information about prevalent weed populations is stored and processed by Xarvio’s software to help plan future applications, in terms of both quantity and type of chemical.
Trials have indicated savings of up to 90% in pre-emergence and 20-60% in post-emergence applications, depending on crop type, rotation and timing.
When will it be available?
The companies are conducting field tests in row crops – predominantly maize, sugar beet and soya – across Europe and the Americas, with the aim of supplying sprayer manufacturers on a commercial level next year.
However, this won’t be able to target specific weed species – something Bosch says will happen further down the line.
Amazone already sells a green-on-brown system, called the Amaspot, which was developed by Dutch firm Romatron and is used on the Weed It
Weeds on post-harvest stubbles
Infrared-based spot spraying kits have been a popular choice for Australian farmers looking to target weeds on post-harvest stubbles with general weedkillers such as glyphosate.
The two big names – Trimble’s Weedseeker and Romatron’s Weed It – work by measuring infrared reflectance.
Red light is absorbed by chlorophyll in the foliage of plants, resulting in near infrared (NIR) light being reflected back to the sensors. The system recognises an increase in the ratio of NIR to red light and triggers a nozzle solenoid valve to deliver a spray of herbicide.
Both can be used day or night, and the equipment has also been adapted to work on mechanical alternatives, such as the Weed Chipper.
In Europe, the Rometron technology has been adopted by Amazone as the Amaspot system.
Other systems
The four companies featured above might be making plenty of noise, but there are several alternative systems in development and on the market that offer something slightly different.
Autoweed
Status: on sale
Autoweed, based in Queensland, Australia, offers an in-fallow and green-on-green weed detection and spot spraying system.
Its modular kit is designed for relatively small farms and can be retrofitted to any boom, including those used on ATVs and UTVs for paddock spraying.
To keep costs down, the system runs off-the-shelf hardware. Central to this are the RGB cameras from Flir Systems that provide the deep learning models with high-resolution images to assess the colour, shape and texture of plants.
These are compared with the tens of thousands of labelled images in Autoweed’s database to decide whether to trigger a nozzle solenoid or not.
The company says this delivers an average detection rate of more than 90% and, during trials looking at turnip weed in oats, it achieved a 95% herbicide reduction versus blanket spraying.
Other components used in the construction include Nvidia Jetson processors, use of Google’s Tensorflow deep learning library, and Teejet solenoids and spray equipment.
The system will soon be on sale and costs roughly AUD$5,000/m (£2,500/m), including detection units, spraying parts and the job of retrofitting the kit.
Cambridge Consultants
Status: concept
Another low-cost option, though still a long way from full production, is the Farfaza system developed by Cambridge Consultants in the UK. It uses a combination of hardware components that cost just £77 to assemble.
The secret to this, the company says, is running an AI platform that requires far less processing power, which means it can be deployed on cheap, rugged hardware.
It works by looking for differences in plant texture between the crop and any grass- or broad-leaved weeds, rather than trying to match shapes and sizes of weeds with a huge image dataset.
When proving the concept, the system was trained on just 60-100 images and its demo model can accurately spray ivy leaves on an artificial grass background moving at up to 8kph. However, this is too slow for broadacre farms and it hasn’t yet been bolted to a crop sprayer for testing over thousands of hours in a range of conditions.
Cambridge Consultants has stepped back from developing the technology any further – instead it is looking for machinery manufacturers to take the technology into a commercialisation phase.
Tillett and Hague
Status: on sale
Bedfordshire firm Tillett and Hague developed one of the earliest spot spraying systems for high-value horticultural crops, specifically targeting broadleaf weeds such as volunteer potatoes in carrots and onions.
It was developed in response to the loss of active ingredients and was available for commercial production in 2014, six years after work began.
It is designed to spot spray contact herbicides such as glyphosate to 5mm accuracy on plants as small as 3cm across, making it far more targeted than other systems featured in this article.
It uses modestly priced RGB cameras and reasonably powerful fanless PCs to run its hand-coded, data-crunching algorithms.
“To keep the cost of hardware and processing manageable we work with relatively low-resolution images,” says Nick Tillett, who has been working on machine guidance systems since 1993.
Crop rows are located using algorithms originally developed for inter-row cultivation guidance. Weeds are then discriminated from crop plants by combining evidence based on position relative to crop rows, size, shape and, to a small degree, subtle colour differences.
“There can be significant colour variations depending on crop conditions,” says Mr Tillett. “Reflection from the tractor’s paint, crop nutrient demand, moisture and herbicide applications can all influence the colour detected, and we can’t afford to get it wrong.”
The system is sold on the front-mounted frame of Garford’s Robocrop Spot Sprayer. Boom widths range from 3m to 9m and maximum working speed is 5kph.
So far, the low work rate and high cost of the technology has meant relatively slow take-up, says Mr Tillett, but interest will probably rise as growers’ armoury of herbicides diminishes.
A 6m Robocrop Spot Sprayer costs between £75,000 and £100,000. As well as veg crops, the company has some machines working in wide-row cereals and sugar beet.
Agrointelli and Ecorobotix robots
Status: prototypes
A string of start-ups are working to combine spot spraying kits with autonomous robotic applicators, though most are better suited to smaller scale horticultural work.
One of the most advanced is the Robotti from Danish firm Agrointelli, which can cover up to 3ha/hour. It uses cameras to detect weeds, but also has an injection spray boom capable of changing the herbicide mixture and dosage on the fly.
Swiss outfit Ecorobotix is working on its own version called Avo, which is solar powered and has the capacity to treat up to 0.6ha/hour.
The system works at sub-1cm precision and applies very small doses of herbicide to target weeds, reducing spraying volume by up to 90%.
Analysis
Any business clocking thousands of spraying hours annually will be attracted by the prospect of slashing up to 90% from its herbicide expenses, but the initial cost of the equipment – estimated to be well over £100,000 – could prove a bit too much to swallow.
If Tillett and Hague’s progress in the higher value vegetable market is anything to go by, spot spraying hardware costs have proved a major deterrent, despite herbicide options shrinking, resistance rising and chemical prices soaring.
In an arable context, the financial risks will only be intensified, with crop values lower and growers more sensitive to machine costs. These farms are unlikely to see spot spraying in its purest form, either – their scale and the type of nozzles they are used with means the system is more likely to apply a variable rate according to weed prevalence, rather than pinpointing individual grass weeds.
However, hardware prices might start to drop as the components, used widely in autonomous vehicle development, are produced on a mass scale.
Financial incentives may also be available in years to come, particularly given the UK government’s keenness to pursue environmentally considerate farming systems, in which targeted sprays certainly have a role to play.
The biggest slow-up at the moment could actually be the manufacturers themselves. In many cases, they’ve been making plenty of noise in a bid to attract funding, but many of the green-on-green systems – particularly those with the sophistication to target weeds such as blackgrass in wheat – remain further from production than their developers seem willing to admit.
Direct injection
The holy grail of spot spraying is to combine it with the direct injection of a chemical.
This involves administering the correct dose of neat chemical into the spray line before delivery so, in theory, different weeds could be hit with different mixes.
This would solve one problem with spot spraying – knowing exactly how much chemical to pre-mix without prescription maps (which would otherwise remove the real-time element) and therefore avoiding lots of waste.
However, the system is fraught with challenges, not least that of changing chemicals instantly and keeping spray lines clean.
Building the algorithms
A computer’s ability to identify particular plants in a growing crop relies on developers gathering, sorting and labelling millions of pictures.
All of the elements that make up each image – such as plants, soil and stones – must be identified in thousands of different situations to take account of plant growth stages, soil conditions, crop heights, stubble lengths and weather conditions.
The artificial intelligence or machine learning component that enables green-on-green detection in these systems relies on devilishly complex mathematical formulae, or algorithms. This means they are able to learn for themselves, without being given commands.
The more images that are tagged and processed to form the basis of the system, the more reliable the dataset is and the more accurately it will identify weeds.
The biggest challenge in building such systems is the variability of field conditions, where sun, clouds, shadows, moisture and soil colour constantly change.