Potatoes growers have two seasons to get stores up to scratch
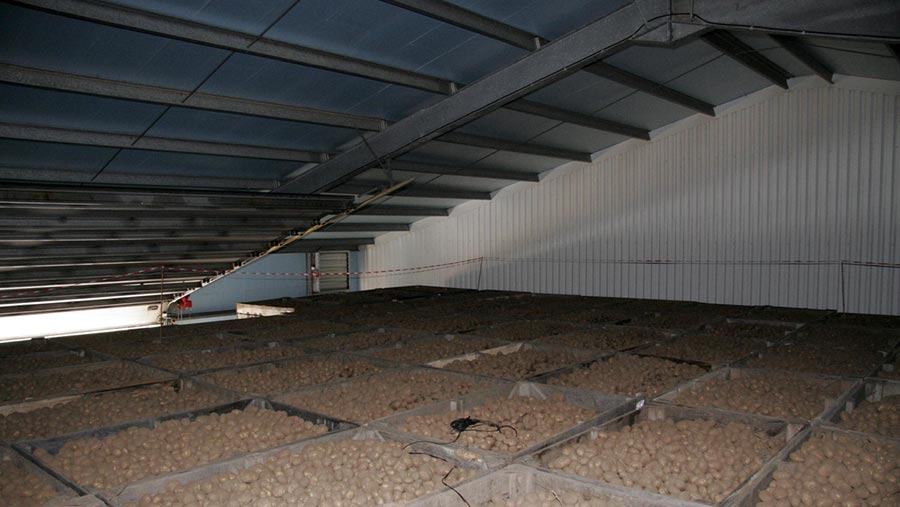
Potato growers have just two seasons to ensure their potato stores are up to scratch to comply with anticipated tougher rules on the use of a key sprout suppressant.
To help farmers prepare, AHDB Potatoes launched its “Be 2017 ready campaign” at the British Potato Industry Event earlier this week in Harrogate.
The aim is to encourage growers to start now preparing for the lower doses in 2017, explained Mike Storey, AHDB Potatoes head of research and development.
See also: Lower limit for potato sprout suppressant CIPC introduced
He sees a two-prong approach to deal with the reduction in the maximum dose for CIPC (chlorpropham) use in potato stores – lower total doses and air recirculation.
Dose decline
The suppressant has been under stewardship for the past seven years due to residues being found in potatoes, with the last exceedance being in February 2014.
But the sector now needs to prepare for the total maximum dose falling to 36g/t.
“Maximum doses have already been decreasing under the ‘Be CIPC Complient’ campaign since 2012 from the maximum of 63g/t,” said Mr Storey.
For the 2015-16 season, the new statutory limits, approved by the Chemical Regulations Directorate, are 30g/t for the fresh market and 50g/t for processing, including chip shops and peeling.
And the maximum dose will continue to fall over the next two seasons from 50g/t to the EU level of 36g/t for processing.
It is likely that statutory label requirements will further limit the dose used on crops stored for the fresh market, he said.
Store modifications
For the fresh sector, refrigeration and use of spearmint oil can help, but Mr Storey acknowledges the challenge is with processing potatoes, which have to be stored at higher temperatures. Especially those for crisping, which can be in store right up to July.
But AHDB Potatoes fieldwork shows that it can still be effective at the EU limit of 36g/t.
Mr Storey explained that you sometimes get both hot and cold spots (over and under application) and it is the cold spots where less has been applied that drives the next application.
That is why lower rates can still be effective, but Adrian Cunnington of Sutton Bridge Crop Storage Research stressed that good air recirculation is crucial to ensure effective treatment.
“You have got to have active recirculation to get uniform movement of air,” he said.
Therefore, if industry is to cope with lower doses and growers have not modified their store adding active recirculation, they will need to take action. Mr Storey stressed that it is likely there will be a future label requirement for active recirculation.
Mr Cunnington said the aim of the modifications is to get as much active into the boxes and avoid it all going up into the roof space, as it can then fall down on the top boxes.
Fans need to go slower to gently stir the air and direct it into pallet gaps.
“When fans go too fast, the active sticks to the blades and you lose active,” he explains.
Then a plastic curtain stops the air going around the sides, ensuring more goes through the potatoes instead of short circuiting the system.
Where refrigeration units are fitted, Mr Cunnington said farmers will need extra fans to do the CIPC application.
Again there is the risk of losing product in the refrigeration unit, reducing the effectiveness of the application.
Farmers wanting to know more can visit the CIPC stewardship webpage.