How a grower uses cultivations and precision tech to kill slugs
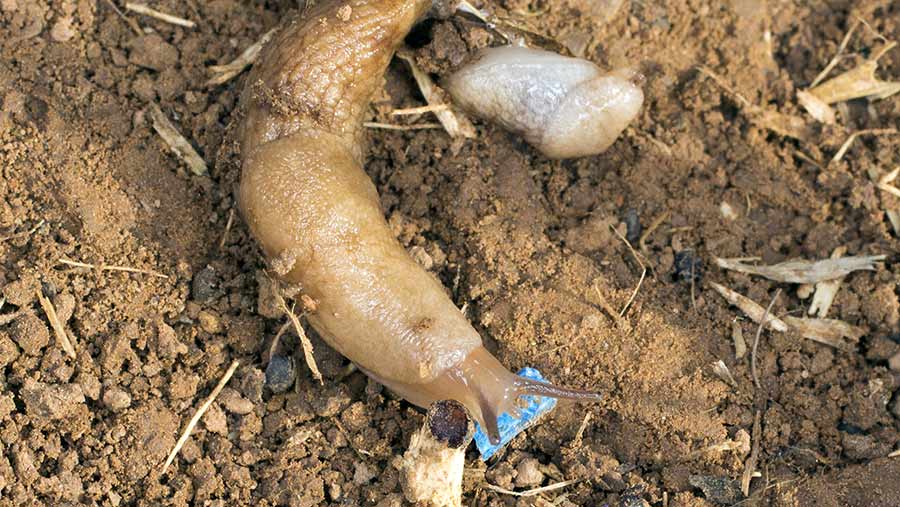
Slugs have been a major headache for North Yorkshire grower Graham Potter since he switched from a plough-based crop establishment system to direct drilling.
But with proactive implementation of integrated slug control methods – and some new technology – he has turned the tide against this damaging pest across his 200ha arable farm near Thirsk.
See also: Tips on killing slugs with ferric phosphate pellets
Soil health
Soil health has been a major focus for Mr Potter in recent years and part of his strategy to improve organic matter has been reduced tillage and the introduction of cover crops.
In 2013, the previous plough-press-drill system was ditched in favour of the Claydon tine-based strip-till drill.
Farm facts – W Potter and Sons, Topcliffe Grange, Thirsk
- Area – 200ha
- Soil types – Heavy clay and medium loams to blow-away sands
- Cropping – Winter wheat, oilseed rape, spring barley, fodder beet plus cover crops
- Establishment system – Claydon strip-till
However, with the slug’s habitat no longer disturbed by deep inversion tillage, crop damage increased and this forced Mr Potter to reassess his slug control strategy.
“The slugs got worse and worse when we started direct drilling, but as my understanding of the slug itself has improved, things have slowly gotten better,” explains Mr Potter.
His increased knowledge of slug ecology and behaviour has seen a number of techniques implemented to try to eliminate the problem without using pellets, which are used only as a last resort.
Stubble rake
The first is the use of a 7.6m Claydon stubble rake, which is deployed a number of times between harvest and the establishment of the following crop, particularly after oilseed rape when slug pressure tends to be at its highest.
This helps spread crop residue evenly across the soil surface, minimising any habitat favourable to the pest.
The rake also inflicts physical damage and exposes slugs and slug eggs to the elements or natural predators.
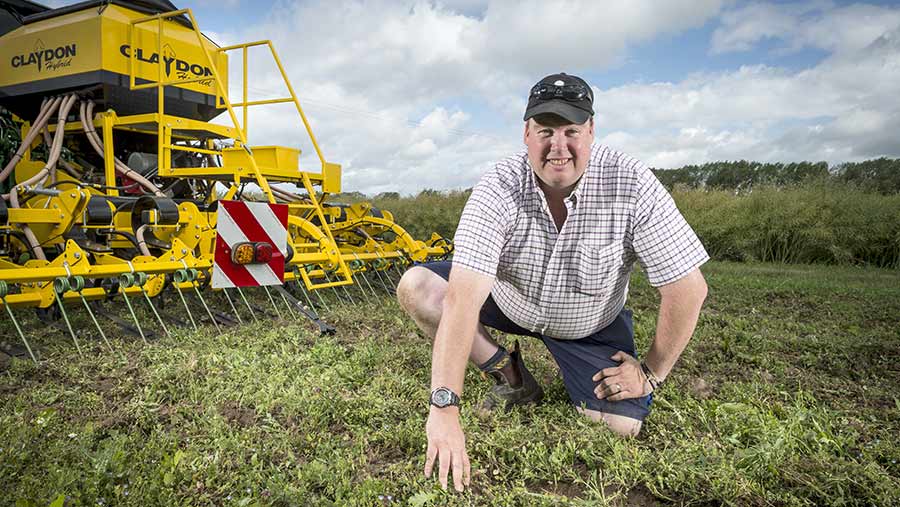
Graham Potter with his Claydon drill © Jim Varney
“It’s much more effective when hot and dry and we’ll take advantage of any hot weather to rake once harvest is over,” Mr Potter says.
“However, we don’t get too many hot days in Yorkshire, so we also rake at night when slugs are active on the soil surface to get a better effect when conditions are cool and damp.”
Rolling and drill depth
With each tine coulter in the strip-drill system loosening a narrow band of soil, this can provide an easy route for slugs to move down rows and feed on seed.
Recognising the importance of seed-bed consolidation, Mr Potter has taken to double-rolling after drilling where slug risk is high, first in the same direction as the drill, then a second pass at 90 degrees to close up the slot.
This helps with seed-to-soil contact for rapid establishment and reduces the ability of the slug to move within the seeding zone.
Trials run by Mr Potter comparing no roll, one roll and two rolls showed much improved control from two passes.
In areas where he knows there is a slug problem, Mr Potter also reduces the forward speed from 8kph to 5kph to improve soil consolidation.
Mr Potter also uses drilling depth in high-risk areas to hinder the pest’s ability to get to seed and cause damage.
Typically, wheat would be drilled about 2.5cm deep, but depth is increased to 3.8cm-5cm in slug-prone areas or in wet seasons.
Soil maps
An early adopter of precision farming technology, Mr Potter began using an electroconductivity (EC) scanner some time ago to produce management zones based on soil types across his farm.
His soils vary from heavy clay to blow-away sands, and this gave him the chance to marry up the EC map zones with observed slug risk.
This has been underlined more recently by drone images taken when damage is seen in the crop, allowing thin, slug-grazed patches to be mapped and saved for future reference.
Most observers would assume that the heaviest soils would present the highest slug risk, but Mr Potter’s work has uncovered that his medium loams suffer the most crop damage.
Using these EC maps together with variable-rate seeding technology, he has been adjusting seed rates based on soil type for some time.
However, he is now layering slug risk data over the top of seeding maps and adds an extra 20-30kg/ha of seed where slug risk is high.
“It helps to negate the losses caused by hollowing and has made a big difference to plant populations since we’ve been doing it,” he says.
Variable pellet application
In addition to increasing seed rates in hotspots, Mr Potter is combining EC mapping, slug risk and yield data to produce variable-rate slug pellet application maps.
This enables him to apply a higher rate of ferric phosphate pellets in problem areas on medium soils, and less where risk is low, without exceeding the overall maximum individual label dose.
“The heavy land might only get 4kg/ha, but where we know it’s bad, we will go up to 7kg/ha,” Mr Potter notes.
Ferric phosphate switch causes no concern
Graham Potter is not losing sleep over the ban on metaldehyde use from June 2020, having switched to ferric phosphate in autumn 2017.
Mr Potter’s is a monitor farm for Yorkshire Water and part of the Sustainable Landscapes project, which aims to reduce the amount of metaldehyde polluting raw water supplies across the region.
“Control has been fine with the ferric phosphate,” he says. “The only difference is that you don’t see dead slugs like you do with metaldehyde, as they go under the soil surface to die.
“It is just a case of going out and checking the crop for damage or if the pellets have been eaten to know if you’ve done any good,” he explains.
Graham Potter’s slug control tips
- Seed-bed consolidation is king for improved slug control
- Double-roll seed-beds where slug risk is high
- Decrease forward speed when rolling for improved consolidation
- Consider increasing drilling depth in high risk fields/seasons
- Use precision technology to map slug risk and target management
- Consider higher seed rates in high risk areas
- Ferric phosphate pellets provide effective alternative to metaldehyde.