6 areas to improve sprayer operator efficiency
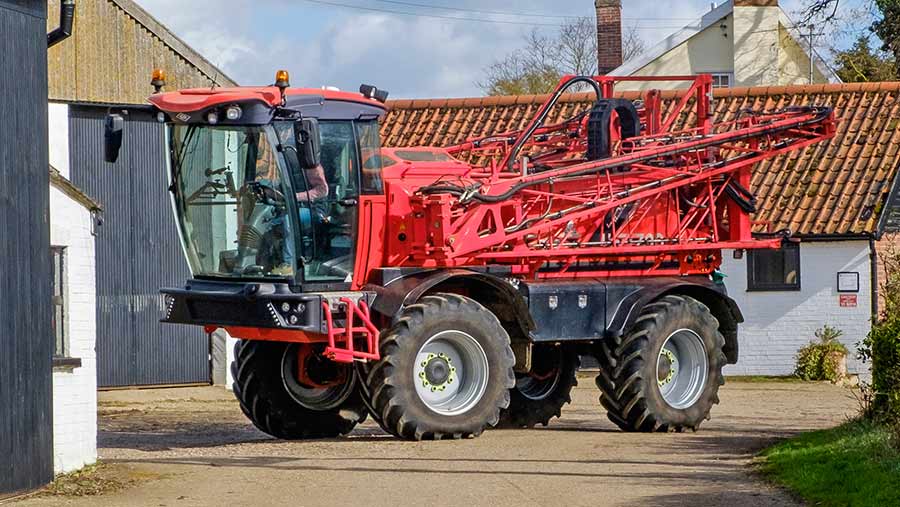
In order to hit crucial spray timings and ensure inputs work as effectively as possible, spray operators need to maximise their time spent in the field on good spraying days.
Of the 100% control that can be achieved by using a chemical product, almost half is dependent on the product being applied at the right time.
At the critical T2 timing, each day the spray is delayed past the optimum timing is equivalent to 0.07t/ha in yield, meaning just a week’s delay will lower yields by 0.5t/ha.
See also: Video: 7 pre-season checks every sprayer should have
However, the average spray operator spends just 30% of their time actively spraying, with the rest spent travelling back and forth to the spray store, organising chemicals and refilling the sprayer.
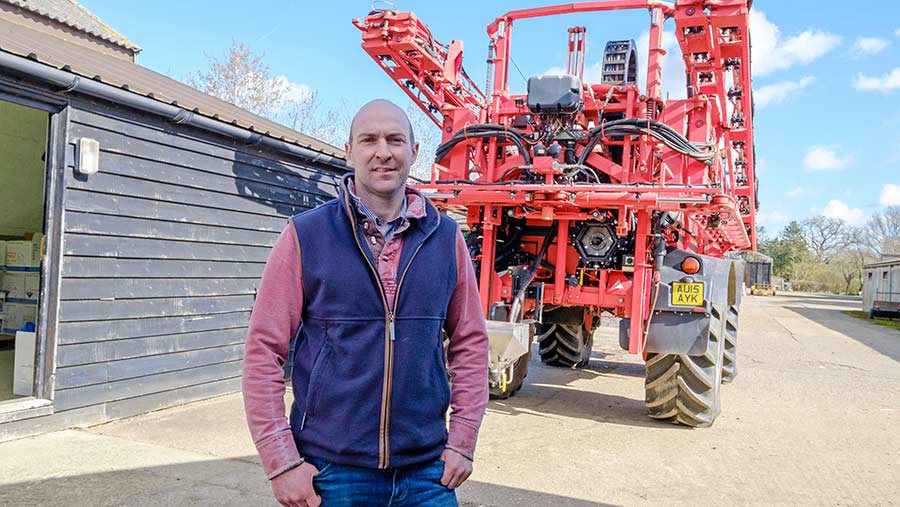
Nick Light © Jason Bye
For EJ Barker & Sons’ spray operator Nick Light, increasing his available spray time has been crucial as he has the complex task of applying inputs and operations on a field-by-field basis across 513ha at Lodge Farm, Westhorpe, Suffolk.
Alongside Syngenta application specialist James Thomas, Mr Light shares his top tips for increasing sprayer operator efficiency.
Key points
- Long-range weather forecasting apps and real-time local data from an on-farm weather data station allows for better workload management
- Live data also means an operator can switch to drift reduction nozzles from the cab and continue in marginal conditions
- Group herbicides, fungicides and insecticides together in the spray store to reduce mistakes, labelled on a diagram of the spray store
- Label half-used bottles clearly and keep these at the front of the shelf to be used up first
- Avoiding foil tops can halve the time taken to open packaging, while reducing the risk of pollution
- Water storage will speed up re-filling and allow flexibility, while water bowsers will reduce travel time
- Co-formulated products make tank mixing simpler, and reduces the amount of stored product
- Check tank mixes to ensure efficacy will not be reduced
- Prevent foaming by ensuring the induction hopper is always partially filled, reduce engine revs or pump speed and add foamy products last
Real-time local weather data
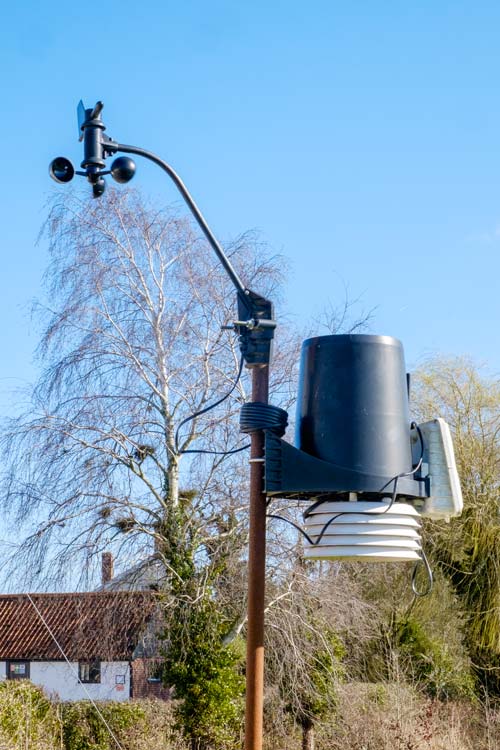
© Jason Bye
Good knowledge of local weather data, both current and in the future, allows Mr Light to manage his workload and capitalise on any spraying opportunities.
“Being efficient in other areas, such as packaging choice, will save you minutes, but planning ahead can save you hours,” he says.
A range of weather apps predict the weather for the week ahead, such as the BBC Weather app and Rain Alarm, while the farm’s weather station provides real-time data on wind, rain, humidity and temperature.
Humidity data pinpoints dew point on leaves, which means his sprays can be applied to a drying leaf and stick, rather than running off.
“Often workers stand in the yard where it’s quite sheltered, but you don’t really see the true picture,” he says.
By combining the data, Mr Light is better placed to choose an appropriate combination of nozzles to allow him to continue spraying when conditions change.
Mr Light gets the latest data from the weather station sent straight to his phone so he can monitor the wind speed from the cab.
A Duo React system means he can switch between a flat-fan and a 90% drift reduction nozzle, which are both mounted on the nozzle turret, with just a flick of a button.
“In a two-month period we only had five spray days. Using the higher drift reduction nozzles allows you more opportunity in marginal conditions,” he says.
Ensuring operators stick to the rules around wind speed is critical to helping to keep products on the market, says Mr Thomas.
Syngenta is currently developing an app that will tell operators which nozzles they should be using depending on real-time local data to help eliminate any gusts.
Organised spray store
A well-organised spray store located near the sprayer filler site can really trim the time spent filling.
Mr Light’s spray store is a converted pig shed, with the sprayer filling site located right outside on an old muck pad.
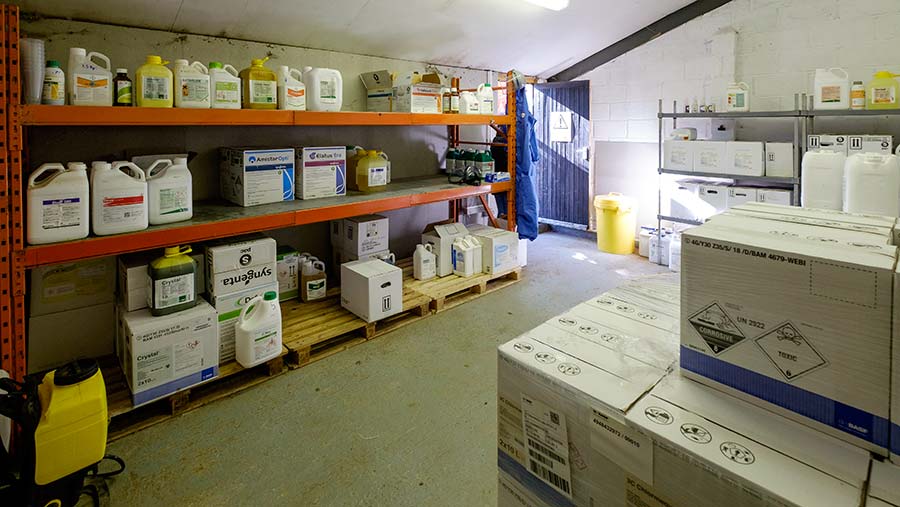
© Jason Bye
The store also has a roller-shutter door, which allows new stock to be brought in on pallets with a telehandler, before being arranged into groupings of herbicides, fungicides and insecticides to minimise mistakes.
Another way Mr Light avoids filling his sprayer incorrectly is by writing the combination of products needed on a sticky note and sticking it to the tank.
He then lays the products out and checks them against the note before starting to fill.
Any half-used products then have their quantities written on the bottle to help prevent future filling mistakes, before being placed at the front of the shelf.
This ensures old product is used first, and all stock is used within the two-year limit.
Packaging choice
Spray operators can halve the time taken to open a product by avoiding foil-topped bottles.
Foil tops must be manually cut off, washed and disposed of correctly to ensure neat product does not enter a watercourse.
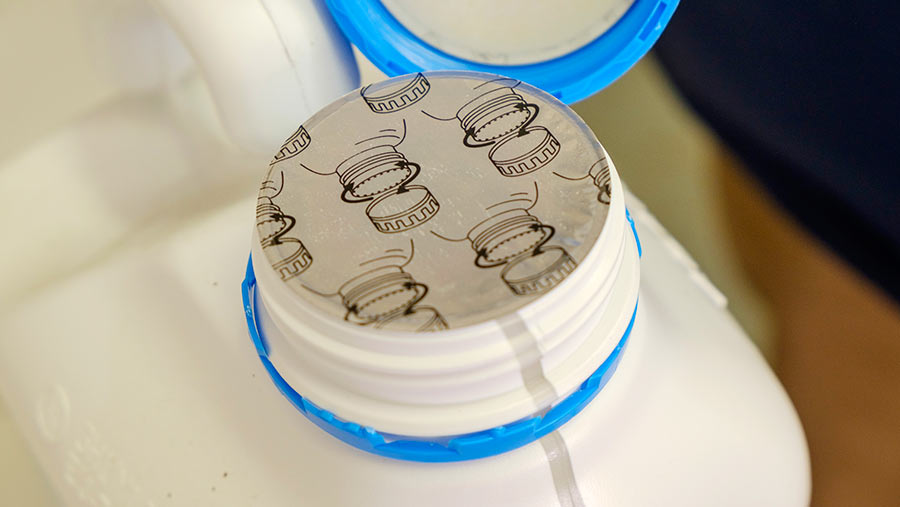
© Jason Bye
Due to the pollution risk, many manufacturers are already moving away from foils, but steering clear will also help avoid problems with glugging and the risk one could enter the tank.
While Mr Light’s first preference is for co-formulated products, if there is a choice, he will always opt for no foil.
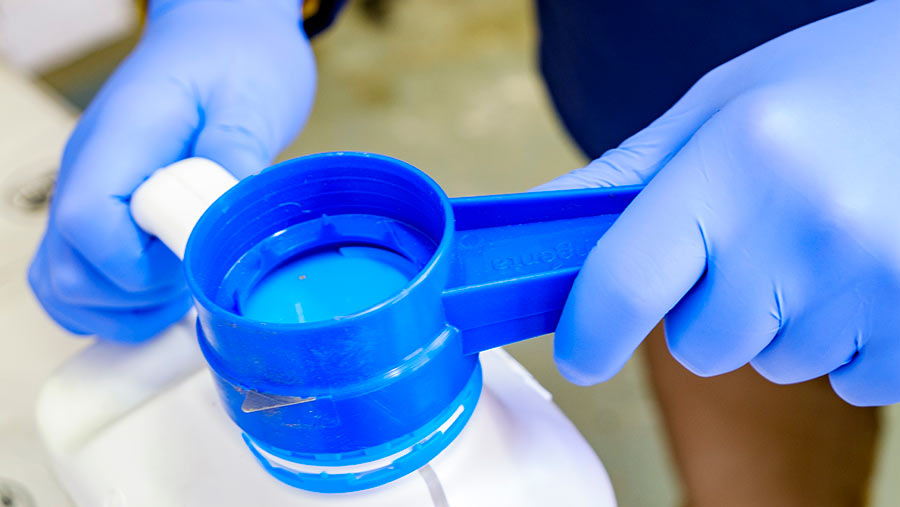
© Jason Bye
“Better packs with less kinks are easier to pour and wash out,” adds Mr Light.
Filling efficiency
Filling from water tanks rather than relying on mains pressure significantly speeds up the turnaround time, so Mr Light refills directly from two 10,000-litre storage tanks, which hold enough for five tank loads.
To avoid using the local hard water, to which pH buffers and wetters must be added, the tanks are filled with filtered rainwater collected from the sprayer store’s roof.
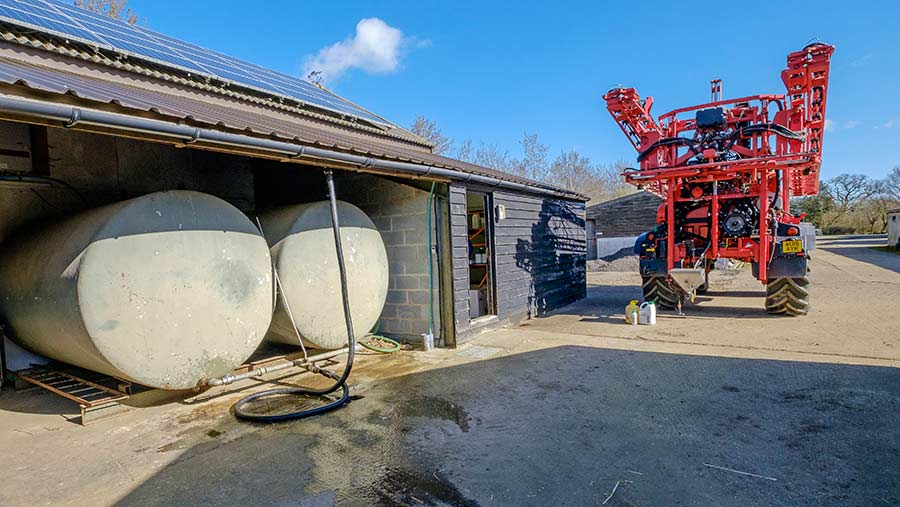
© Jason Bye
About 30% of the collected water is used to flush through the system’s filter, while the rest is stored in a 1,000-litre tank, which is kept in the dark to prevent algae growing, before being automatically transferred to the bigger tanks when needed.
The farm is currently investing in a much larger tank to give greater harvesting capacity in the future.
Another worthwhile investment was a bowser in the form of a D-mount tank strapped to a straw trailer.
“Work by John Deere in North America revealed that 40% of the average sprayer’s time is spent doing something other than spraying,” says Mr Thomas, with a sizeable chunk spent travelling back and forth from the field to the spray store to refill.
“If you eliminate a travel time of 30 minutes for a 1,000-litre sprayer by using a bowser, there is the potential for a 35% increase in output over an eight-hour day,” he adds.
Having the bowser means Mr Light is able to cut out a 15-mile trip to fill up from the furthest part of the farm, saving half an hour.
However, the bowser can also seriously speed up his work rate when he is spraying fields nearer the yard, meaning that if there is a short time window for spraying, he can get the job done, saving around half a day.
Chemicals can be pre-mixed in the tank, but this requires a lot more plumbing and cleaning.
Although expensive, the tank will pay for itself, and Mr Light recommends buying a new one as old ones can contain rubbish.
Tank-mix efficiency
Mr Light has greatly reduced the amount of product stored, the time he spends manually tank mixing, and packaging by having a policy of using co-formulated products with two modes of action instead of straights.
Products that can be used on a variety of crops, such as in both wheat and barley, also helps streamline the store.
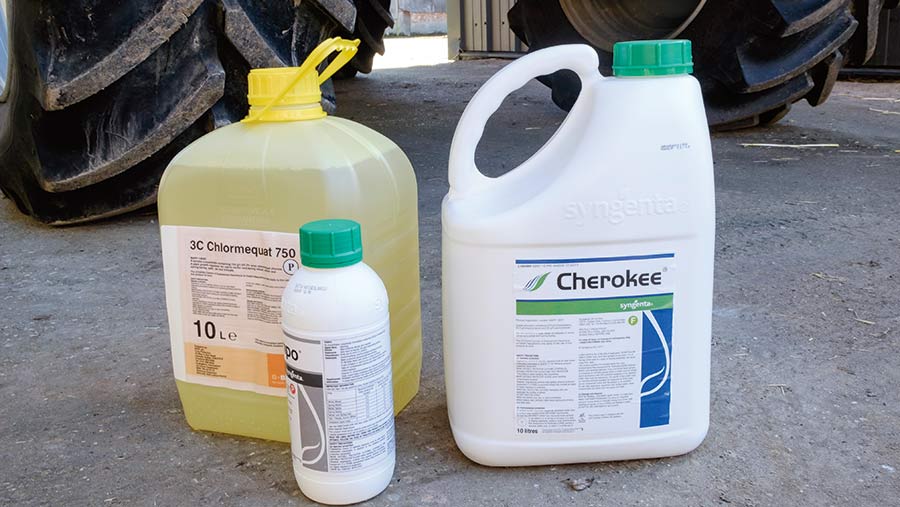
© Jason Bye
Although looking to increase efficiency wherever possible, Mr Light has actually separated his micronutrients and his fungicides out into different spray passes, as combining them was reducing fungicide efficacy.
Normally the problem is only from an efficacy point of view, but there can also be a physical effect on the sprayer, as Mr Light has found in the past, with a poor mix blocking up the sprayer, filter and nozzles.
This was due to trying to suspend a lot of micronutrients in too little volume of water. “It can turn to sludge, or set like concrete in the bottom, and takes half a day to unblock,” says Mr Light.
Sprayer operators that are unsure of tank mix compatibility can always check with their agronomist or use one of the tank mix apps, says Mr Thomas.
“All of the suppliers provide technical helplines, which are free and can be massively helpful, ensuring you’re not about to make a mess and block the sprayer up.”
Sprayer sense
Product incompatibility can also result in excess foam, which will come out of the top of the tank.
Foam is not good for the environment, and will prevent the sprayer operator being able to fill any further, but there are some simple steps that can be taken to avoid it.
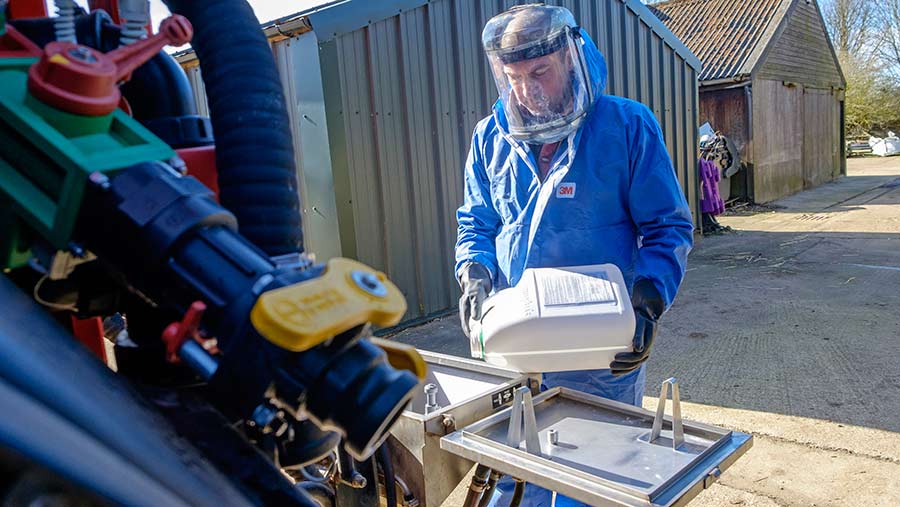
© Jason Bye
Mr Light recommends making sure the induction hopper has water in it at all times so that it is not sucking in air.
Decreasing engine revs or pump speed will reduce agitation, which can also be a cause, and putting inherently foamy products into the tank mix last will also help.