John Deere E-Premium adds a bit of spark to 7430 and 7530 tractors
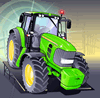
Tractors and electronics are a bit like chocolate and chilli – not something you’d necessarily choose to mix but, when combined, the outcome’s not quite as bad as you might have expected.
The boffins at John Deere’s German HQ just seem to keep adding more electronic wizardry to their tractors. But unlike all that complex engine technology that’s come along in the last 10 years, this time they promise the advantages will be tangible – the operator will actually feel the benefit.
Late last year the green giant unveiled its plans to develop a tractor that uses electrical power to drive all the equipment that isn’t central to the business of actually propelling the machine forward. As a sideline, the extra spark that “E-Premium” tractors generate could potentially power electrically-driven implements.
The motive? If you cut down on those things that constantly sap power from the engine, you’re more likely to have all the grunt it can produce when you need it. When you don’t, there’s the potential for fuel savings of up to 5%, according to Deere.
What’s involved:
1. Crankshaft Generator
Strapped to the back of the flywheel, directly between the engine and the main clutch pack, the water-cooled generator pumps out up to 20kW of raw electrical power.
2. Power Electronics Control Box
Converts electricity to correct format and distributes it to where it’s required.
For example, two sockets at the rear provide 5kW for 230volt single-phase tools and the same for heavier duty 400volt three-phase kit. In theory, you’ve got mobile workshop power where and when you need it.
3. Vehicle Controller
This is the tractor’s brain. It monitors everything that’s going on and incessantly chats away to the power electronics box to co-ordinate how much electrical power is needed and where it needs to be delivered to.
4. Battery
Just like a standard tractor’s battery this stores power for start up.
5. Fan Drive and coolant pump
No more belts and pulleys here. The fan and low temperature coolant pump are powered by electric motors that vary their speed according to engine temperature. The fan reacts instantaneously unlike the traditional viscous-coupling connected units used in most modern tractors. That means there’s no lack in cooling and it doesn’t run when it’s not needed.
6. Air-brake compressor
Rather than running constantly and letting off steam when the pressure gets too much, the air-brake compressor now kicks in and out as more wind is required. A magnetic clutch engages its drive when the pressure in the circuit’s reservoir drops.
7. Air-conditioning compressor
Moved to directly under the driver’s seat, the air-con unit gets away from the heat of the engine bay. Electric drive means it runs independently of engine speed and can reach maximum cooling capacity even at idle.
Spreader advantages:
- Electric drive means disc speed – and therefore spreader accuracy – can be maintained irrespective of engine rpm
- Doing away with the pto-shaft makes the close-coupled spreader much easier to fit – simply plug and play
- Calibration safety – discs no longer need to spin when calibrating the spreader
So how does it all work?
Those clever white coat-clad Germans have chucked the standard alternator in the scrap-bin and opted for a crankshaft-driven generator strapped to the engine flywheel, just ahead of the main clutch-pack.
This provides power for all the usual stuff plus:
- An electrically-driven cooling fan
- An electric coolant pump for the transmission and charge air coolant
- An electrically-powered air-conditioning compressor
- A belt-driven air-brake compressor with electrically engaged clutch
- Two external power supply sockets (5 kW @ 230V and 400V)
What are the benefits?
By switching from direct belt-drives to electric power for things like the air-con compressor and cooling fan, their operation then becomes independent of engine output.
That means they don’t have to run all the time, making for small but worthwhile savings in fuel consumption.
Conversely, their output can be boosted when the engine is only running at low revs.
In that way the operator can actually get more out of the engine, according to Deere.
For example, the main cooling fan can run flat out even at low engine speeds. This means the engine’s power-boost function can run right down to 1250rpm rather than the usual cut-off point of 1700rpm because of the extra cooling provided by the electrically-driven fan.
This also allows the power-boost – available for pto and transport work – on E-Premium tractors to be 10hp greater than standard versions. (see graph)
By making engine auxiliaries electrically-powered, they can be sited right where they’re needed. The air-con compressor moves to directly under the cab, away from the heat of the engine. In the future other elements of the main cooling pack could potentially follow suit.
John Deere says that’ll lead to significant improvements in cooling efficiency – a factor that will allow its engines to reach the next stage of emissions regulations – Tier IV – more easily.
E-Premium advantages
- Up to 5% fuel saving
- 35hp power-boost – 10hp more than standard tractors
- Power-boost curve starts at 1250rpm instead of 1700rpm
- Provides improved transport acceleration performance
- Increased load response for pto work
- 230V single-phase and 400V three-phase power sockets to run external electrical equipment (5 kW) when stationary
- Reverse-fan function to clear radiator/grille (manually controlled)
- Components located exactly where they’re required – e.g. air-con compressor directly under cab
The future? Electrically-driven implements?
There’s one big advantage to electrically-powered kit: its speed can be maintained – or adjusted – completely independently of the tractor engine’s rpm.
According to Deere the future’s bright for this technology. Any implement that isn’t really power-hungry and that traditionally uses a pto drive has the potential to switch to electrical power.
That’s particularly important where the drive speed needs to remain at a set level. For example, sprayer pumps need to maintain a set pressure to ensure constant rates, even when the tractor begins to grumble climbing a hill. No surprises, then, that engineers at John Deere’s Dutch sprayer plant are looking at ways to integrate electric drives into their machines.
Other bits of kit that could well benefit include things like bale-wrappers, precision planters and drills. Electrically-driven devices on such implements would allow much finer control and do away with ungainly chain-and-sprocket set-ups.
Although there isn’t yet any electrically-powered kit on the market, German fertiliser spreader specialist Rauch – which makes spinners for Kuhn – is probably the closest to getting there.
On display for the first time at last year’s Agritechnica show in Germany, it currently has machines under field evaluation.
The Axis EDR uses the E-Premium tractor’s 400volt socket to power its twin spinning discs and a 12volt supply to drive the agitators and rate controller.