What’s in Your Shed? visits Barnes Contracting
Devon-based Barnes Contracting buys predominantly used or ex-demo kit and then hangs on to it… unless the purchase turns out to be a pup.
Andrew Faulkner is given a yard tour by older brother, Bobby Barnes.
See also: Cheshire contractor’s five custom seed drills for SFI sowing
Business facts – Barnes Contracting
Main services: Foraging (2,400ha grass, 400ha maize, 100ha wholecrop), combining (400ha), drilling (600ha cereals, 500ha maize, 300ha grass), spraying (12,000ha), big square baling, slurry tanking and umbilical work
Other enterprises: Contract grain drying, rolling/crimping grain, tub grinding, steel-frame building construction, concrete laying, machinery repair service
Staff: Andy and Sue Barnes and their three sons – Bobby (general contracting), Mike (construction) and Rich (construction, combining and spraying) – plus 15 full-time staff (50% contracting, 50% construction) and some part-timers.
How did you get started?
Bobby: Pretty much straight from school, and it was the same for my brothers, Mike and Rich – although we did all mix working at home with an ag engineering course at Bicton College for the first two to three years.
My course also included a brief stint with former McCormick dealer, Graham Vowles.
The Barnes family originally came to be in Yarcombe, near Honiton, as my grandfather had a tenanted farm in the area.
Then my parents, Andy and Sue, bought Stopgate Farm, a small arable unit, as a greenfield site in the 1990s, and everything developed from there.
By 2006, when my brothers and I started to join the business, father was already contracting with a forager, combine and a couple of tractors, so this gave us a great initial base to build on.
Another boost came a few years later when a neighbouring contractor ceased trading, and we were able to pick up several of its former customers.
Today, we offer the full arable package – drilling, spraying and combining – as well as running two foragers and two wagons to harvest nearly 3,000ha of grass, maize and wholecrop, a couple of big square balers and a complete slurry service, both tankers/dribble bars and an umbilical set-up. We also contract dry and process grain.
Alongside mainstream contracting, we’ve diversified into steel-frame building construction, concrete laying and providing a general machinery repair service for other local farmers.
While we all get involved in every aspect of the business, my focus tends to be on the contracting, and Mike and Rich look after the construction side. Rich also manages the 12,000ha contract spraying operation.
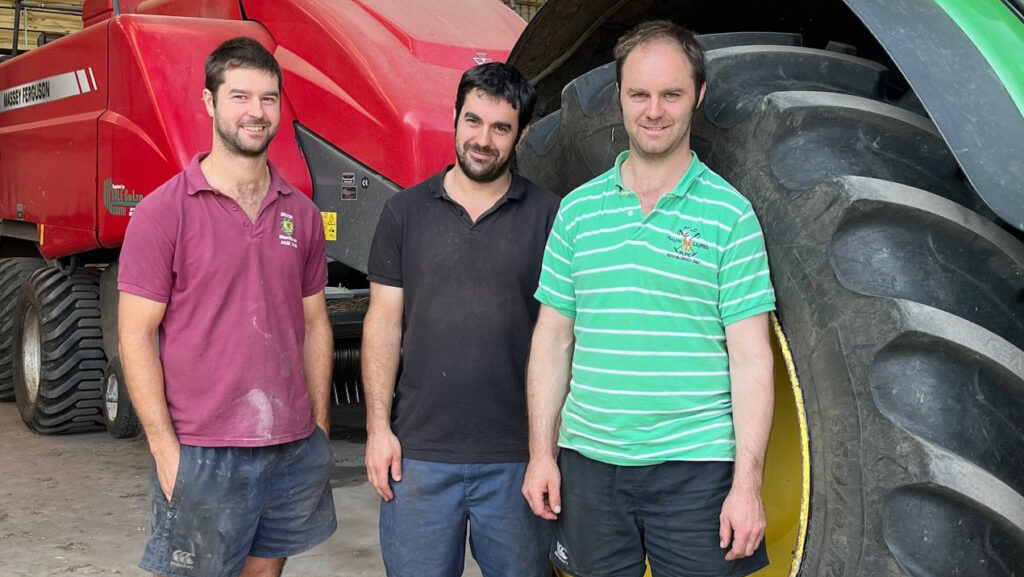
Rich, Mike and Bobby Barnes © Zehra Baker
How brand loyal are you?
Very. For us, it’s Deere tractors, New Holland combines, Claas foragers, JCB loaders and Bateman sprayers, and we don’t see any reason to switch.
We tend to buy nearly-new and older machines, service and repair them ourselves, and then hang on to them, so it makes sense to stick with what we know.
There’s some commonality, too, with the Batemans powered by Deere engines.
We’ve demoed other brands in the past, but have never really been tempted.
Demonstrations can also be frustrating, as, by the time you’ve swapped things around, set up the demo machine and the salesman has made his pitch, you rarely get as much done as if you’d just bladed on with your own kit.
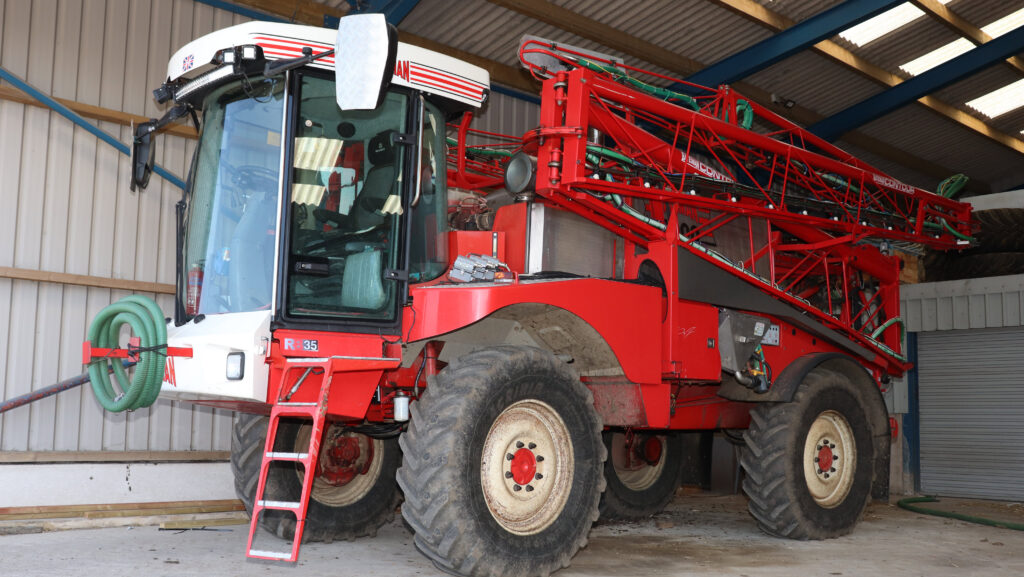
© Andrew Faulkner
Favourite dealer?
Deere dealer Hunt Forest is probably our favourite – its parts department is excellent – closely followed by Mason Kings (JD), Hamblys (Claas) and Buglers (New Holland).
On a par are Granit, Sparex and Bepco, which we use a lot, especially when it comes to repairing machines for other farmers.
These firms sell non-genuine parts, but they’ll also often supply genuine parts at discounted prices.
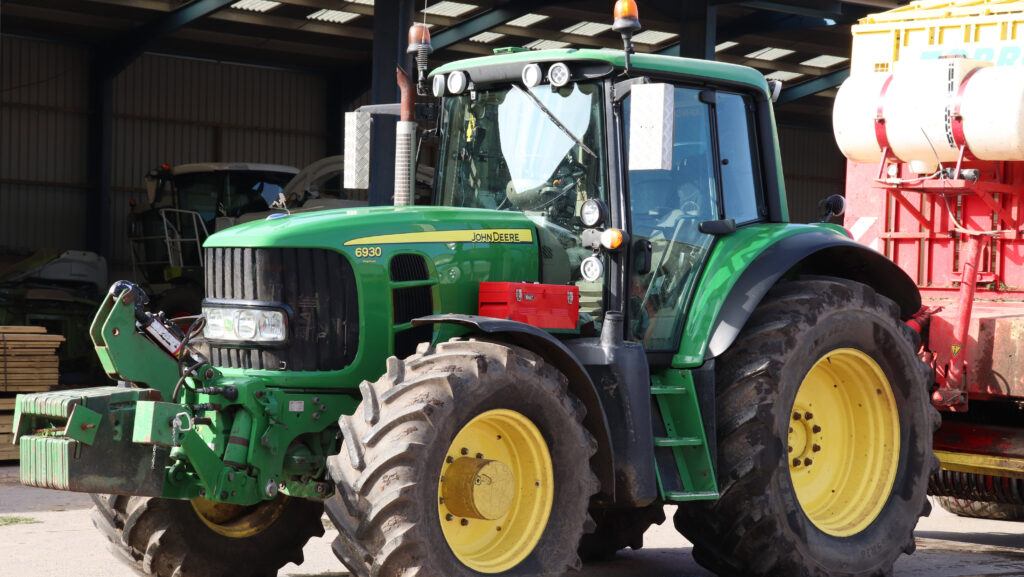
© Andrew Faulkner
Favourite piece of kit?
We’ve got several. We like the simplicity of the Claydon Hybrid drill, along with its ability to plant a wide range of crops at minimal cost while improving soil condition.
We bought it second-hand from Hamblys nine years ago and have spent very little on it since.
We’re also big fans of the ConceptAgri one-pass maize seeder. We purchased the first one off Lincs dealer RH Crawford and subsequently upgraded to a new six-row unit direct from the manufacturer.
The machine effectively subsoils, rotary cultivates, consolidates, fertilises and precision plants in the one pass.
Output is about 16ha/day, and it’s great at reducing soil erosion.
For out-and-out performance, though, it’s difficult to top the 12-row Claas Orbis maize header.
It’s hugely impressive to see 30ft of maize heading up the spout in a single pass, and, on the front of the Jaguar 970, we’ll knock off almost 40ha in a day.
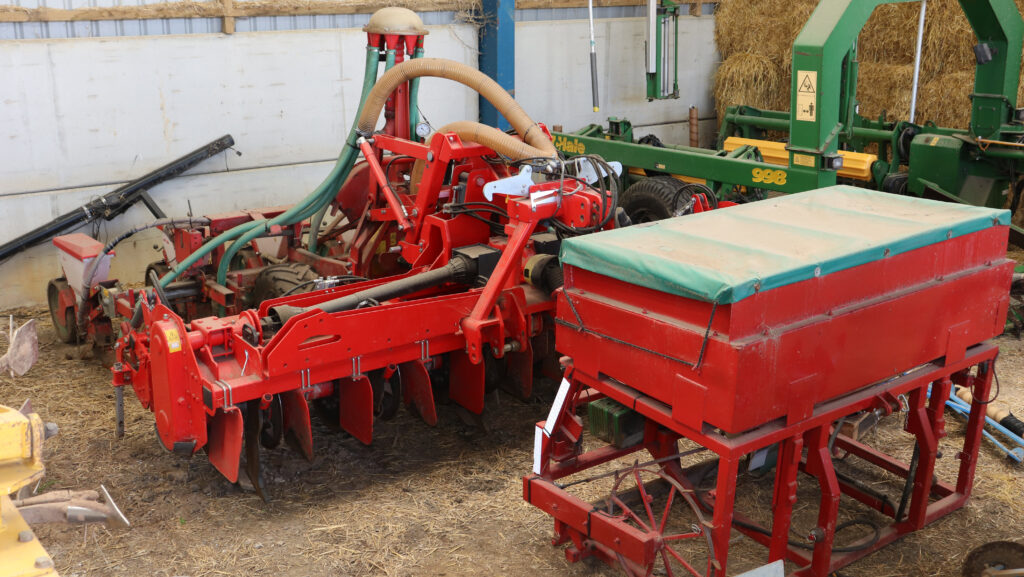
Six-row ConceptAgri maize seeder subsoils, rotary cultivates, fertilises and plants in the one pass © Andrew Faulkner
Least favourite piece of kit?
That’ll be the Kuhn Merge Maxx belt merger. The sad thing is that the machine does a fantastic job when it’s working – both in grass and straw – but it has been so unreliable.
This is mainly down to the tine bars, which are long and shear off near the cams.
On average we’ll break three or four bars in a season, and during the winter service we’ll probably replace another four or five because they’re cracked.
It’s the downtime during the season that’s the biggest frustration, although we’ve now got the two-man job down to about a couple of hours.
All the bands have to come off, along with the affected tine bars and bearings, and then everything refitted again. It’s a right pain.
Latest purchase?
We generally review what’s needed every winter. In 2023-24 we added a couple of tractors plus an ex-demo Pottinger Combiline 6010 silage wagon, which was bought for £83,000 off Smallridge Brothers.
The three-year-old, 4,000-hour 6155R was a private deal, while the fully-loaded 23-plate, 1,100-hour 6R 185 came from Mason Kings for £125,000.
That’s more than we were looking to spend, but it still represents a £30,000 saving on new.
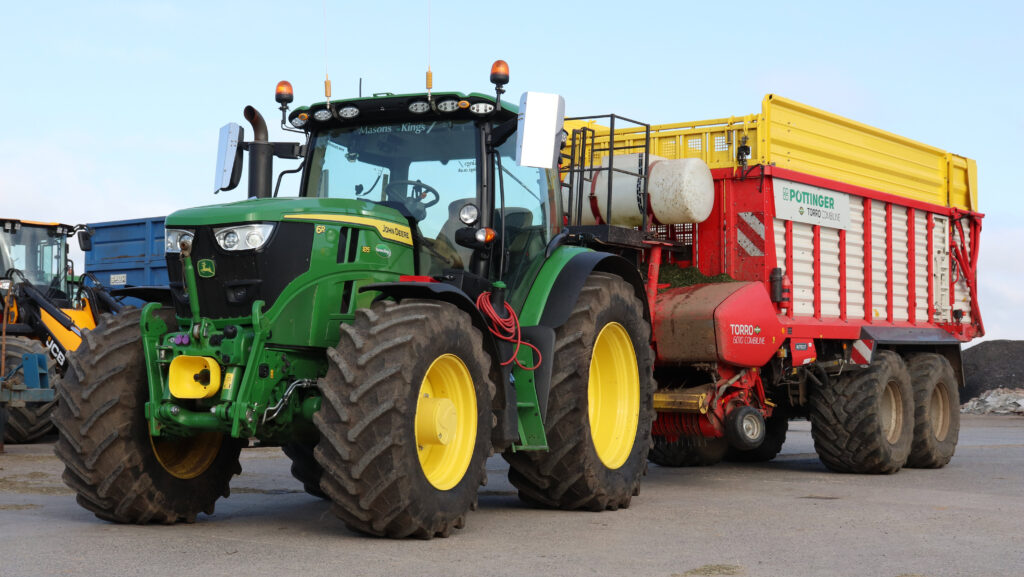
The latest additions to the Barnes fleet are this JD 6R185 and Pottinger Torro Combiline © Andrew Faulkner
Oldest machine still at work?
Our three-leg subsoiler is more than 30 years old and a bit like Trigger’s broom – the frame’s been beefed up, the legs have been changed to Flatlift types and it’s now got a rear crumbler roller.
Our other real old-timer is a 51-plate JD 6910 with more than 17,000 hours… and it’s still racking up another 1,000 hours every year.
It has a loader, front linkage, and a 50kph PowrQuad box, and is regularly called on for trailer work, pulling a feeder wagon, raking etc.
On reliability it’s had two engine rebuilds, a PowrQuad clutch pack, hydraulic pump and a Bosch VP44 injection pump rebuild.
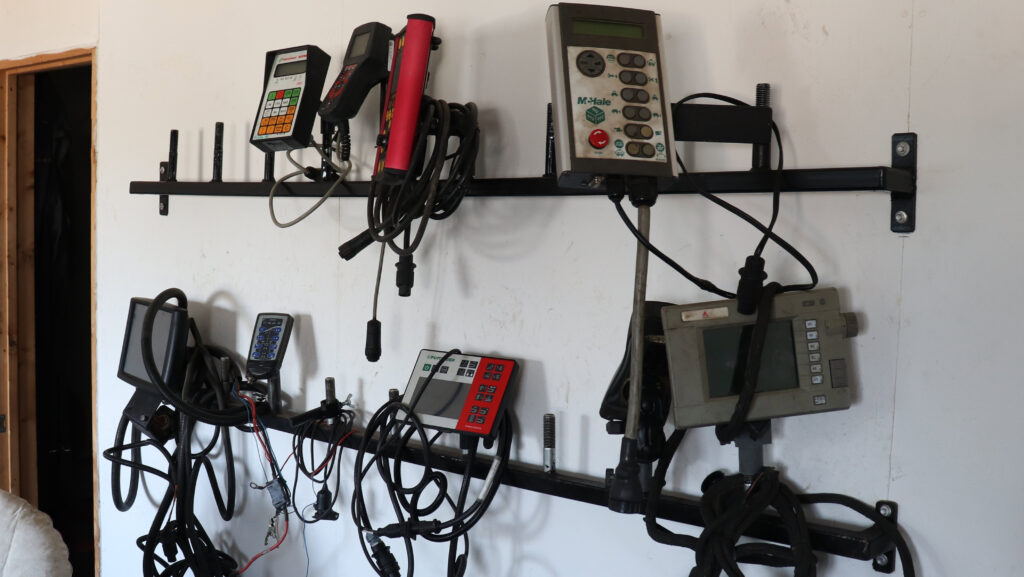
When not in use, all implement control boxes are stored on this rack in the office © Andrew Faulkner
How long do you keep your machines?
The past 15 years have been a period of steady growth for our tractor fleet, adding an average of a tractor each year and not selling the old ones.
Proving the point, we’ve only got rid of three tractors – a 6420S, 6820 and 7710 – since I’ve been back home.
Our general policy is to buy Deere tractors with 1,000 or so hours, getting someone else to take the initial depreciation hit, and go for a reasonably good spec – front linkages, 650 rear tyres and so on. We also tend to stick with 150-220hp-ish models.
The drilling 6175R, for example, is chipped to 220hp, while the 6215R is remapped to 260hp at the shaft to cope with the 9m Krone triple mowers.
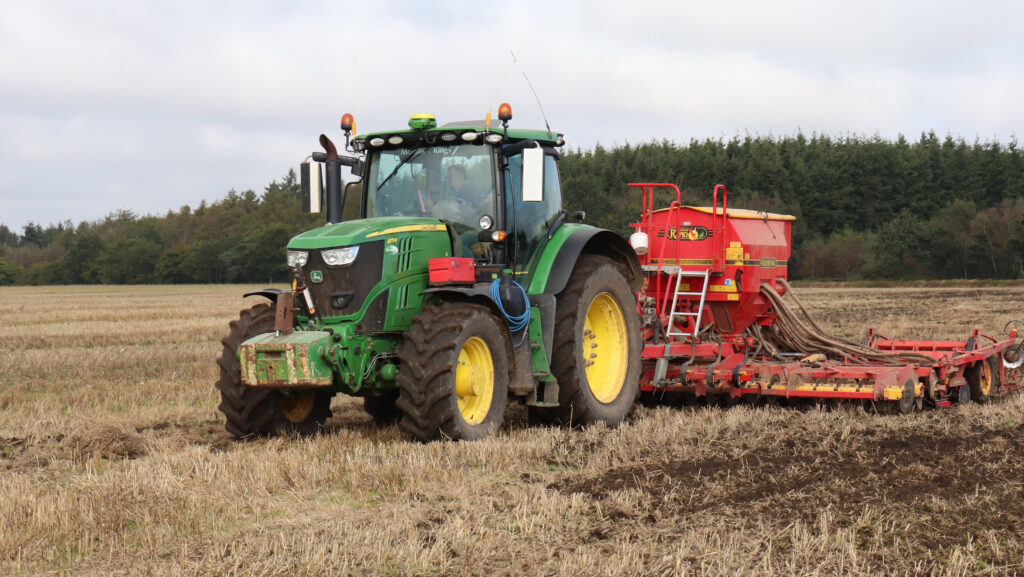
The main drilling rig pairs a JD 6175R with a 6m Vaderstad © Andrew Faulkner
We can’t see the point in investing in higher horsepower, heavier depreciating tractors, which only use that extra grunt for a very limited period; we’d rather extract the max out of a smaller tractor.
Mapping and chipping clearly have warranty implications, but we’re not too worried about that either.
Manufacturers tend to find a way of wriggling out of warranty claims, so we’ll often forego them, preferring to negotiate the purchase price down if we don’t take the warranty.
Much the same goes for the other kit – buy nearly new and hold onto it until it becomes uneconomical or something else better suited to the job comes on the market.
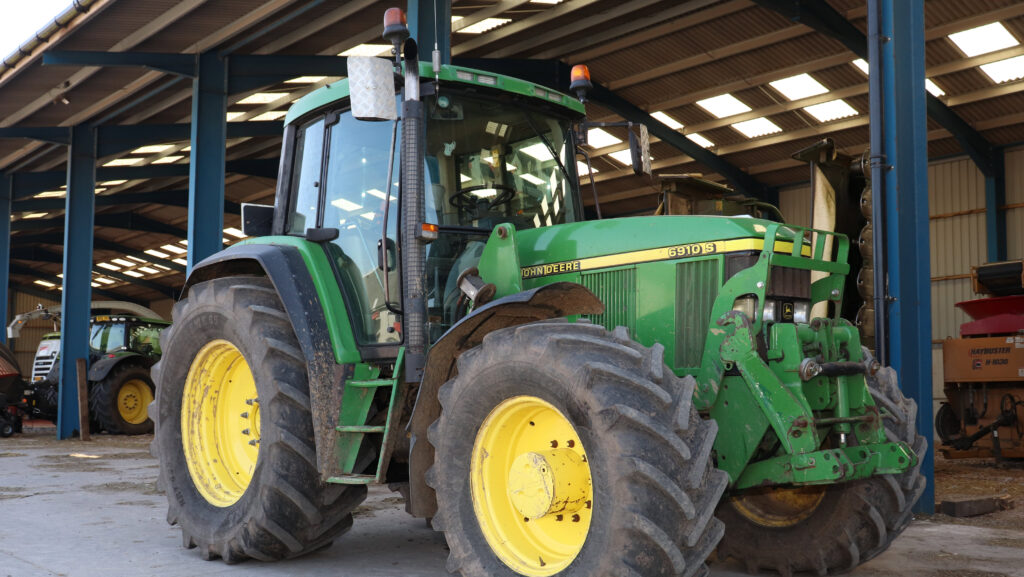
Best Barnes tractor award goes to this 16,500-hour John Deere 6930 © Andrew Faulkner
Next on your wish list?
A 6m wholecrop header would be good. We’re currently running a 4m, and, even though we’re only cutting 100ha, it would still be handy to have the extra output at a time of year when we’re busy on grass and other jobs.
On a similar theme, we’re toying with upgrading the 24m Bateman RB26 to another 36m RB35 to boost spraying capacity in the spring.
We can still spray at 24m with the 36m booms when required, but, even in this part of the world, it’s surprising how many businesses have moved, or are planning a move, to 36m.
Biggest machinery mistake?
Four years ago we bought a five-year-old, three-axle AW grain/silage trailer from Lancashire for about £14,000.
We did the deal over the phone and only noticed when it turned up in our yard that the axles were very narrow.
First day out, in a not especially challenging gateway, I managed to tip the trailer over and dump 20t of maize in the road. No particular drama, but it was a little embarrassing.
Anyway, we’ve since sorted it by replacing the front two axles with wider units and slightly extending the existing rear steering axle.
We’ve also stepped the spring hangers – narrow on the rear, wider at the front – so the rear retains its steering capability. It’s now one of our more stable trailers.
Most expensive repair bill?
An £18,000 final bill to fix a 6175R was particularly painful.
All error codes initially pointed to the AutoPowr unit, so the tractor went off to a transmission specialist in the Midlands, but they were unable to find the fault.
They had the transmission in and out of the tractor a couple of times with little joy. In the end it turned out to be the hydro pumps in the front of the AutoPowr unit.
We also had one bad week with Bateman wheel motors. One went on the main sprayer at a cost of £6,000, and then the smaller RB26 had to have a couple of new units, at £2,500 apiece, three days later.
That was a few years ago, and we haven’t had a motor problem with the Batemans ever since.
Most expensive spare part?
The main hydro pump broke up on the Claas Jaguar 970. The bill for the pump, without labour, was £11,000, which seemed a staggering amount of money to us.
Best invention?
We’re more modifiers than inventors, although, in terms of the work it saves, we’re proud of our bagging-off bucket.
There’s a hydraulically operated hatch in the bottom and four hooks underneath, so one person can dig into a heap of rolled corn, fill a 500kg or 1,000kg bag and lift it straight onto a trailer.
It means we don’t need to bag up too much product in advance of a collection.
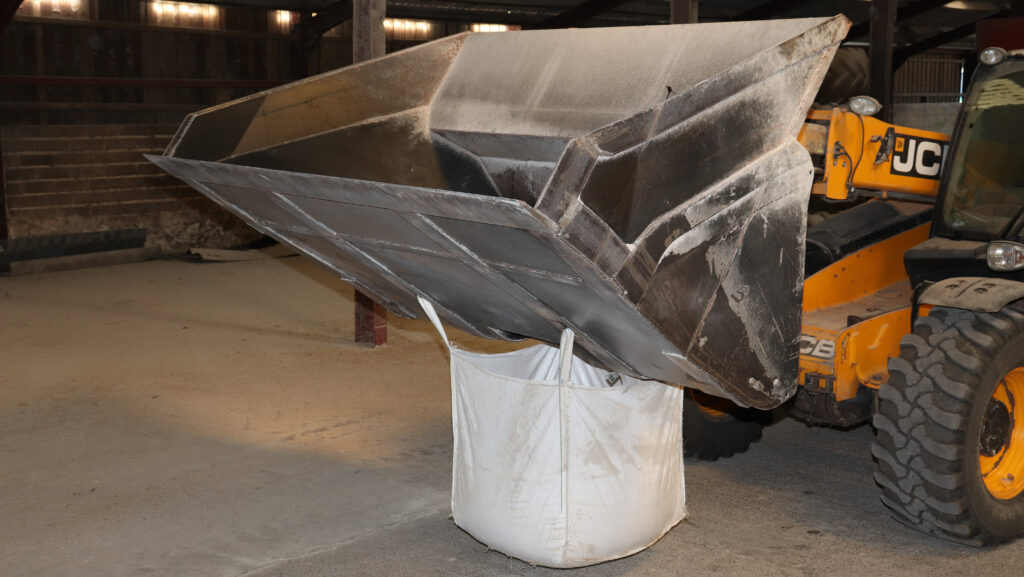
Bag bucket can shovel up the material, fill the bag and then stack it on a trailer © Andrew Faulkner
What couldn’t you live without in the workshop?
That would be our Jaltest diagnostics laptop, which enables us to calibrate DPF, AdBlue and SCR systems on any tractor. It can also calibrate linkages, test engines, perform regens, diagnose error codes and provide wiring diagrams.
In many instances we can now identify and fix faults in the time that the dealer would have taken to travel here.
We bought it for £8,000 from Granit a couple of years ago, and, even though there’s an ongoing subscription charge, we reckon it’s already paid for itself.
Favourite and least favourite jobs?
Bizarrely, one of my favourite jobs is repairing a puncture or fixing an oil leak by the side of a road. It’s something to do with the pressure of having to sort a problem quickly.
For similar reasons, I don’t like the chore of billing in the office when the sun’s shining and everyone else is busy outside.
I’m also not that keen on combining – it’s a slow job in 2-4ha fields, you can’t start cutting too early, you can’t go on too late and the narrow roads around here make it a nightmare to get around.
On top of that, the rate of £125-140/ha doesn’t reflect the hassle and costs involved. The reality, however, is that it’s a service we have to offer.
What’s your everyday farm transport?
An 06-plate Ford Focus with 150,000 miles on the clock. I bought it four years ago for £260 and have added another 70,000 miles.
I just can’t see the point in shelling out thousands on a truck that doesn’t earn anything. Much better to spend the cash on another tractor.
Best tractor you’ve had?
The best and most productive tractor we’ve had is probably the 12-plate JD 6930 PowrQuad, which has been remapped to 200hp at the shaft.
We bought it privately for £52,000 in 2014 with 1,700 hours, and it’s now showing 16,500 hours.
Granted, it’s suffered from the normal Deere issues – variable turbo and EGR faults – but, other than that, it’s been very reliable.
It’s powerful for its size, smooth and great to drive, particularly now that we’ve added Autotrac.
And the worst
That’s the 6420S we sold 10 years ago. We only had the tractor for a couple of years after paying £17,000 for it at Shaftesbury Machinery Sale, but over those two years it suffered a series of electrical issues and brake problems, and we had to replace the forward clutch, TLS valve and transmission pump.
The list goes on. It must have had a hard former life.
Biggest machinery bargain?
The already mentioned oldest tractor takes this prize.
We paid Shaftesbury dealer Robert Coles £27,000 for the 2,700-hour 51-plate 6910 in 2006, and it’s now on 17,000 hours.
Bizarrely, it’s worth more today than we paid for it 18 years ago.
Best and worst pieces of technology?
Like everyone else, we love GPS and Autotrac, which make life much easier for the operator and increase overall efficiency.
In contrast, all engine after-treatment systems are our pet hate.
They choke performance and are the root cause of many modern engine problems. There must be a better way of cleaning up emissions.
Biggest bugbear?
Main current gripe is Deere’s recent insistence that a tractor must be serviced by its dealer to validate the warranty.
We bought the 1,100-hour 6R 185 with a warranty to 2,250 hours, and the tractor is now on 1,700 hours.
At 1,400 hours the diff bolts sheared – a warranty claim – and we’ve been told by the dealer that they must now change the oils and filters for the warranty to be maintained.
I get that they want us to use Deere filters and oils, but to say that we’re not capable of spinning on a few filters is almost insulting.
In the shed
Tractors John Deere 6215R, 6175R (x3), 6R 185, 6155R, 7530, 6930, 7810 and 6910
Combines New Holland CX840 (7.3m header) and CX760 (6m header)
Balers MF 2170 (90x120cm) and Case IH LB334P (80×87.5cm)
Foragers Claas Jaguar 970 with grass pick-up and 12-row Orbis maize header, Claas Jaguar 830 (grass only)
Forage wagons Pottinger Torro Combiline 6010, Pottinger Torro 5100
Handlers, diggers JCB 435, 535-125 (x2), 541-70, 531-70, 536-60 (x2), and Kubota KX080-4 excavator
Sprayers Bateman RB35 (4,000-litre/36m) x2, RB26 (3,000-litre/24m)
Drills 6m Vaderstad Rapid, 4m Lemken power harrow combi, 4m Claydon Hybrid, 8-row Vaderstad Tempo, 6-row ConceptAgri one-pass maize seeder (subsoiler/rotary harrow/Kverneland maize seeder)
Other kit 18,000-litre SlurryKat tanker (15m dribble bar), 13,500-litre Redrock tanker (7.5m dribble bar), Bunning rear-discharge spreaders (x2), 9m Krone triple mower, Claas Liner 3500 four-rotor rake, 10.95m Kuhn Merge Maxx 1090 merger, HayBuster 1030 tub grinder, Genie cherrypickers (x3)