What’s in Your Shed? visits FW 2023 Contractor of the Year
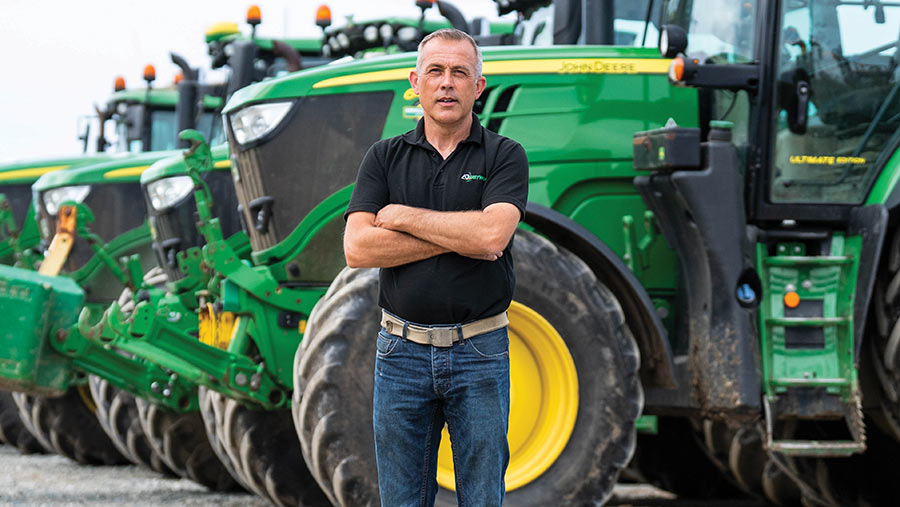
Kevin Heywood, Farmers Weekly’s 2023 Contractor of the Year, reveals the best and worst decisions he’s made in assembling a distinctly green machinery fleet.
We head over to Cornwall to check out his kit.
See also: On test: John Deere’s 6R 185 tractor
Business facts

© Emily Fleur
AJ Heywood, Marhamchurch, Bude, Cornwall
- Services offered Mowing, tedding, raking, baling, forage harvesting, ploughing, drilling, combining, slurry and muckspreading, slurry separating
- Staff 10, plus another 14 in the groundworks division
Kit list
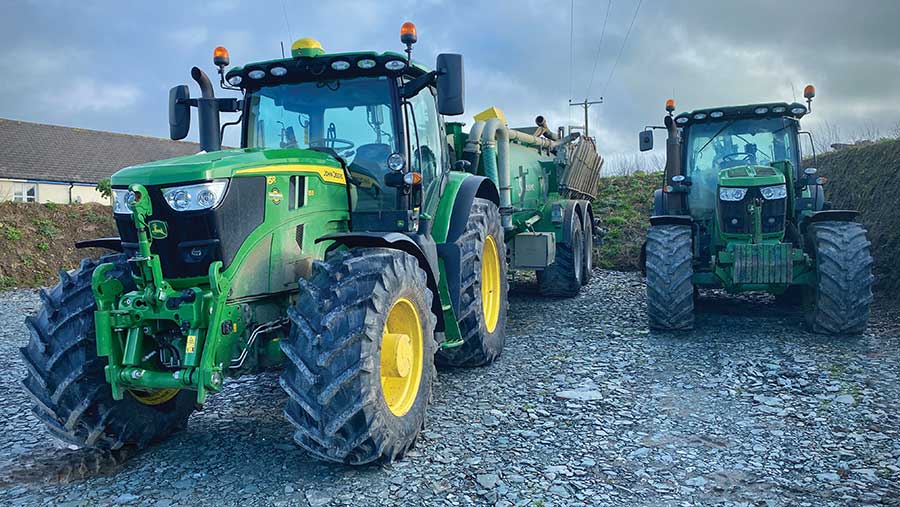
© MAG/Oliver Mark
- Tractors John Deere 6R 250, 6R 185 x2, 6R 155, 6155R x2, 6155M, 6150R, 6930
- Foragers John Deere 8600 and 8500
- Combine John Deere T550 Hillmaster
- Shovel JCB 419
- Mowers Self-propelled Krone Big M, Pottinger front and rear combination
- Rakes Krone 1400 and 1370 four-rotor, Claas Liner and Krone Swadro twin rotor
- Balers Claas Quadrant 2100, Massey Ferguson RB 3130F combi x2, Lely RP 245, Goweil square bale and McHale 991 round bale wrappers
- Cultivation kit Five-furrow Amazone and Vogel & Noot ploughs
- Drill Pottinger Aerosem 5002 FDD combi 5m, Amazone AD-P 303 combi 3m, Wox GreenMaster 3m
- Muck and slurry 12m Tramspread dribble bar, 3,500gal Samson tanker and 12m dribble bar, Ktwo Duo 1100 rear-discharge and Shelbourne Reynolds side-discharge spreaders, home-made slurry separator
- Fertiliser spreader Amazone ZA-M
- Trailers Ktwo Roadeo 18t push-off trailer x4, Marshall 12t, Agrimac 14t, AW Trailers 10t
- Other McConnel 6485 hedgecutter x4
How did you get started?
My dad branched out from dairy farming in 1979 when he bought a brand-new 955 International tractor and a little trailed forager.
Back then there were at least 10 dairies within five miles, so there was plenty of work.
By 1987 he’d wound down the 40-cow herd and sold the milk quota to buy his first self-propelled chopper – a Reco Mengele SF 5600.
He sadly passed away in 2006, in the week that I bought a near-new New Holland FX50 forage harvester. You’ll read plenty more about that machine further on.
I’ve continued to slowly expand in the years since, to the point that we’re now silaging about 3,000ha, combining 200ha, and doing plenty of ploughing, drilling and muckspreading between times.
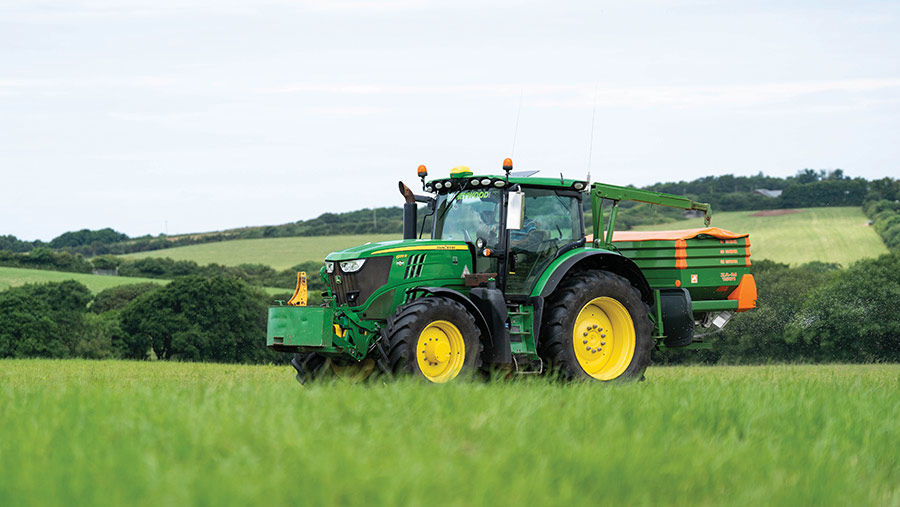
© Emily Fleur
How brand loyal are you?
Very. The self-propelled machines have been exclusively John Deere since 2009, when we replaced the aforementioned FX50.
It was the technology side of things that really swung it for me – I wanted the Harvest Lab nutrient monitoring system and Greenstar guidance, and we now have it all running through the Operations Center.
No other brand comes close to competing with Deere in that regard, and having all the information – where the machines are, what they’re doing, the quantity and quality of crop we’re harvesting – in one place makes it so much easier to manage both the team and our customers.
Some people might think it’s a big commitment to a single brand, but loyalty works both ways and on several occasions Deere has helped with out-of-warranty breakdowns.
Go-to dealer?
All the Deere kit comes from Smallridge Bros – it’s practically on our doorstep. Robert Cole is good for the Krone and JCB stuff.
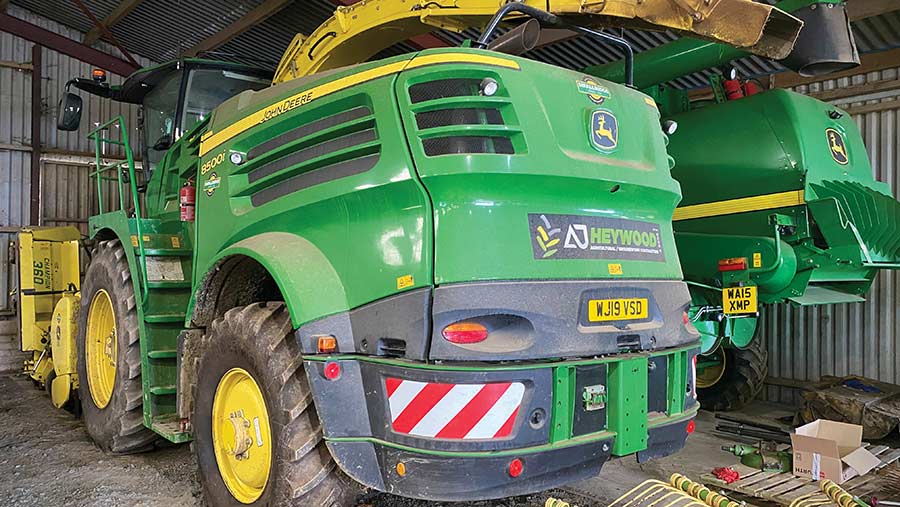
© MAG/Oliver Mark
Favourite machine?
Even though I gave up full-time driving a few years ago, I’d have to pick the two 8000-series foragers. They’re so much more comfortable to sit in than the boxy, cramped cab of the old 7000s.
Granted, the 7000s were more forgiving in that they didn’t need to be quite so finely tuned, but everything is that much easier on the new ones.
That’s particularly the case with the processor – switching from maize to grass, or vice versa, used to take half a day, but it’s now more like half an hour.
Least favourite?
The New Holland FX50 forager. Four of us trekked up to Cumbria to look at it in 2006 and, after shelling out £80,000, I had high expectations.
Sadly, they were short-lived. It was down on power for about two years, until the dealer finally agreed to put it on a dyno. It was no surprise to me that it was 100hp short of its maximum.
Iffy injectors were to blame but, because we’d bought it privately, I had a real battle to get New Holland to cover any of the cost. In the end, we paid for two new injectors, at £1,500 apiece, and they covered the other four.
But by then I’d lost faith in the machine, so I moved it on in 2009 for £50,000.
That’s when we bought our first John Deere forager, a 7450. I paid just £105,000 for it which now looks like a brilliant bit of business, given the new ones are nearer £300,000 and they still do pretty much the same job.
Latest purchase?
A Krone Big M self-propelled mower. I’ve always loved the concept and have been mulling it over for the past decade, but I could never make the sums add up.
Until now, we’ve run two front-and-rear combinations that often struggle to keep ahead of the foragers.
So, the plan was to upgrade – it just came down to a set of triples or the Big M.
I work on the basis that you need 100hp for each mower bed, so the 6250R that we’ve got for buckraking and drilling isn’t quite big enough.
And the cost of 300hp tractors is horrendous. I was quoted £230,000 for the tractor and another £80,000 for a top-spec set of Krone mowers with mergers, which is about £20,000 more than the Big M.
There’s always the argument that we could use the tractor for other jobs. But it’s such expensive horsepower that the hourly depreciation would exceed the amount it could earn running a silage trailer or muckspreader, so it would be parked up most of the time anyway.
For the lesser jobs, I bought a 6155M on 450 hours for £89,000. By my reckoning, it should cost me roughly £15/hour to run, compared to nearer £80/hour for a 300hp tractor.
I visited a contractor in Dorset running a Big M before I committed to buying one, and I was really impressed.
It’s 450hp, so it can cruise along effortlessly at 18kph. It was only drinking about 5 litres/ha and was cutting more than 60ha/hour. That’s more than the two front-and-rear combis combined, but with one less tractor and driver.
Plus, it’s fitted with mergers so we can throw three rows into one in dry years. That means we’ll be able to mow in the morning and cut enough to keep the foragers moving all afternoon.
As it’ll only be doing about 400 hours a year, I see it as a 10-year investment.
Oldest machine still at work?
A 2011-built Deere 6930 – here since new and not likely to leave anytime soon.
It’s done 12,000-hours and, bar the obligatory head gasket, hasn’t been too much trouble.
It tends to do a bit of raking, wrapping and hedgecutting but, as it owes me nothing, I’m not fussed if it’s sat idle for a month or two each year.
Plus, my 11-year-old son has his eye on it for when he leaves school, so I’ll be in trouble if I sell it.
How long do you keep your machines?
The tractors and foragers are on a semi-flexible four- or five-year cycle.
I’m not governed by warranty as I only ever take the standard 12 months – we’ve got a decent workshop and engineering division that can deal with most major breakdowns.
But it’s always a balancing act between spending too much money and holding on to kit too long. I don’t like the gap between residual value and replacement cost to get too wide.
The 8500 was due to be changed last year, but it ended up being out of action for most of the campaign while we tried to sort a problem with diesel getting into the sump.
Given it effectively skipped a year’s work, I decided to hang onto it for another season.
Next on your wish list?
The Big M was top of the list, but I’ve now scratched that itch.
If anything, it would be nice to have a second 419 loading shovel instead of a tractor and buckrake.
Looking further ahead, I’m interested in drone technology for spraying and fertiliser spreading.
It would certainly make it easier to cover the ground in February and March when you can hardly walk on the fields.
Most embarrassing incident?
I was in the FX50 and, as I came over the brow of a steep hill on the A39, I pulled the hydrostat back to slow up.
But a driveshaft collar had come lose, so it only braked on one wheel and sent me flying through the hedge and across an earth bank. One of the wheels came off its rim and turned the tarmac over like a plough furrow.
It could have been a lot worse – but I was convinced the forager was jinxed.
Biggest machinery mistake?
The FX50 was a bad buy, as was the 2013 purchase of a W-series John Deere combine.
No-one could work out what the problem was – it would either produce a clean sample and lose a load of grain out the back, or fill the tank with chaff and straw.
I swapped it for a T550 Hillmaster just two years later and, after a few tough discussions, Deere agreed to keep the monthly payments the same. Everyone recognised it was a troublesome machine.
Most expensive repair bill?
The final nail in the FX50’s coffin was when the long driveshaft, which runs from the gearbox to the front drum, snapped in half.
The bent section continued to spin and tore the machine to pieces, demolishing the fuel tank and a load of hydraulic hoses.
Fortunately, the dealer managed to rebuild it in a couple of weeks and the damage – about £25,000’s worth – was covered by the insurance.
Most overpriced spare part?
Almost everything. We’ve got the advantage of an in-house engineering division, which means we can often machine things ourselves, but I always go to the trouble of pricing up off-the-shelf parts just in case I’m in for a nice surprise.
Pto guards are the thing that really bug me. Given they’re an essential safety item, £400 seems extortionate, and they often fall to bits after six months on a muckspreader.
They should be cheap enough to allow us to keep spares on the shelf, just like you would with oil filters.
Maybe there’s a niche market for someone to transform waste bale wrap into new guards…
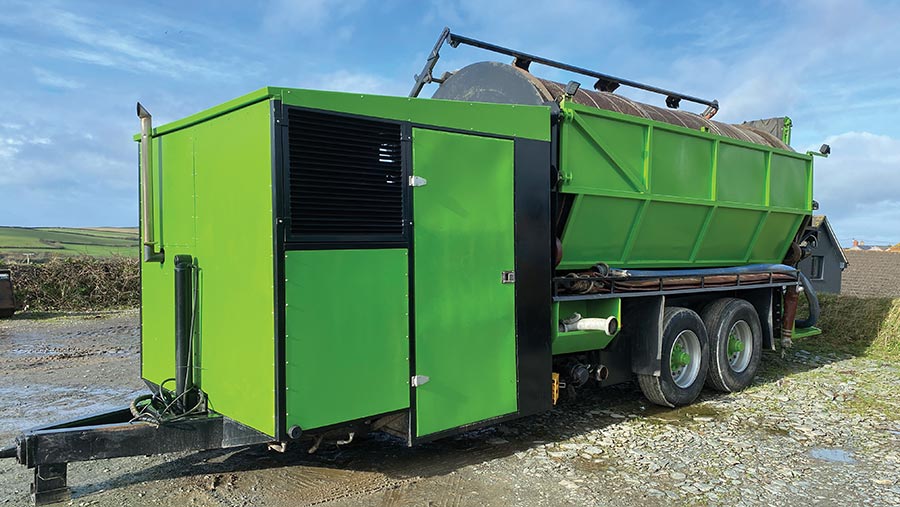
© MAG/Oliver Mark
Best invention?
A trommel-style slurry separator, which cost us about £40,000 to build over a couple of years. It’s a new service, so it’ll take time to build up the workload, but I’m hoping customers will see the benefits of separating the liquid and fibrous fractions of dairy waste.
What’s your everyday transport?
I’ve currently got a 17-plate Mitsubishi L200 that’s on 85,000 miles.
The lads used to pinch my old one for work and eventually wrecked it, so I didn’t fit a tow hitch on this one for three years and I try to keep the key in my pocket.
That said, it’s probably due an upgrade. I’d love a commercial-spec Defender 90.
Best tractor you’ve had?
The first tractor I drove after I left school – a Case 1056 XL.
It was only 105hp, but the raw power was unbelievable and the long wheelbase meant it always found loads of grip. I’m convinced it would out-pull a modern 150hp tractor.
I loved the fact that you could slide the door windows open to hear the engine bark and, on occasions, we slid the exhaust off to save catching it on low shed roofs, which made it sound even better.
In terms of modern tractors, it’s probably the 6195R. It’s a nice all-rounder for baling, drilling and ploughing.
And the worst?
We’ve never had a really bad one, but I’ve spent longer than I’d like in a customer’s 120hp Landini.
I once took over from him on maize carting and I had to really talk myself out of doing the two-hour round-trip back to our yard to get something else.
I couldn’t even shut the door without trapping my hand in the mechanism and, when I later used it to sow grass seed, there wasn’t enough oil pressure to simultaneously run the pneumatic fan and lift the rear linkage.
Most surprisingly useful feature you’ve found on a machine?
Hydraulic top links are now a must-have. At about £500, the cost is a drop in the ocean compared with the price of the tractor and it makes hitching up so much easier.
Auto-steer has also been a game changer, and we’ll be putting Greenstar on the Big M – albeit via a Solsteer bridge kit.
Most pointless piece of farm technology?
I can’t see the advantage of weather stations. No doubt they’re good at gathering data, but I don’t know what you’d do with that information. And normally the customers tell me if it’s going to rain, so I don’t need the technology. Plus, customers are always keen to tell me when it’s going to rain.
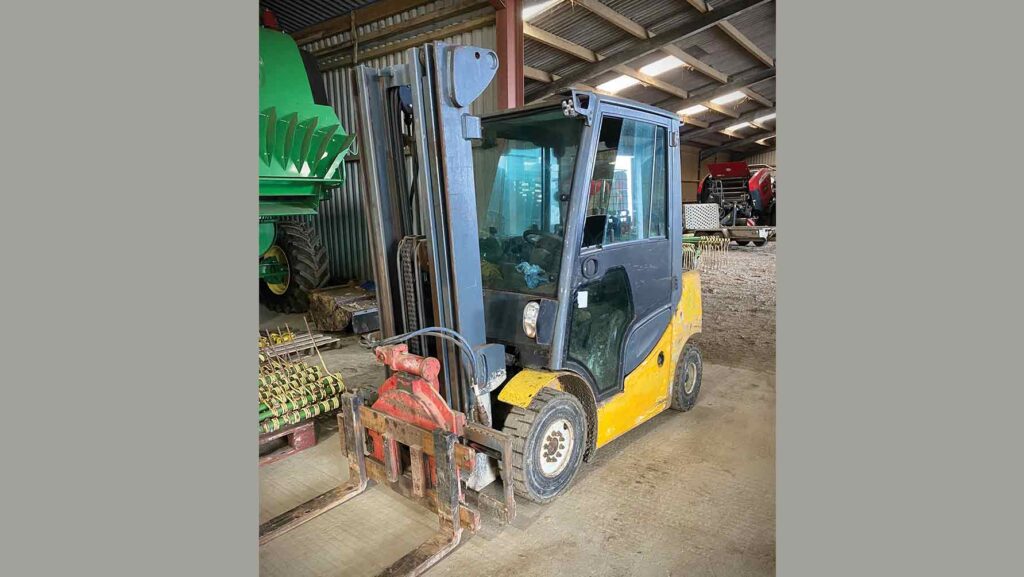
© MAG/Oliver Mark
Biggest machinery bargain?
The workshop forklift came free from a food factory – we just had to pay someone £150 to pick it up.
It’s proved invaluable since we got it back into working order, particularly as we’ve got a rotator on the headstock for fitting heavy components to the foragers and combine, and it has a linkage that allows us to pick up rakes and move trailers about.
The Farmers Weekly 2024 Contractor of the Year
Farmers Weekly 2024 Contractor of the Year Award is sponsored by Rural Asset Finance.
Enter yourself or nominate someone now on our Awards website.