What’s in Your Shed? visits an Oxfordshire contractor
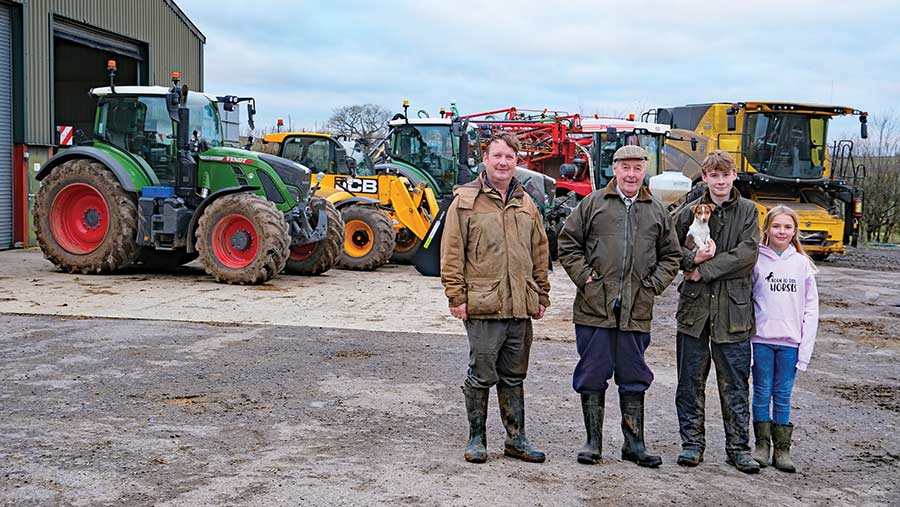
The search for a neater high-horsepower tractor prompted Oxfordshire farmer and contractor John Walker to make the switch from John Deere to Fendt.
We head over to Oxfordshire to find out what’s in the shed.
See also: Driver’s view: Claydon Evolution big improvement over Hybrid
Farm facts
S Walker & Sons
- Home farm 310ha
- Contract farming 500ha
- Cropping Wheat, oilseed rape, winter barley, legume fallow
- Soil type Limestone brash
- Stock 60 suckler cows, 55 sheep
- Staff John, Edward, Philip, Tom and William Walker and student Fred Shipway in the summer
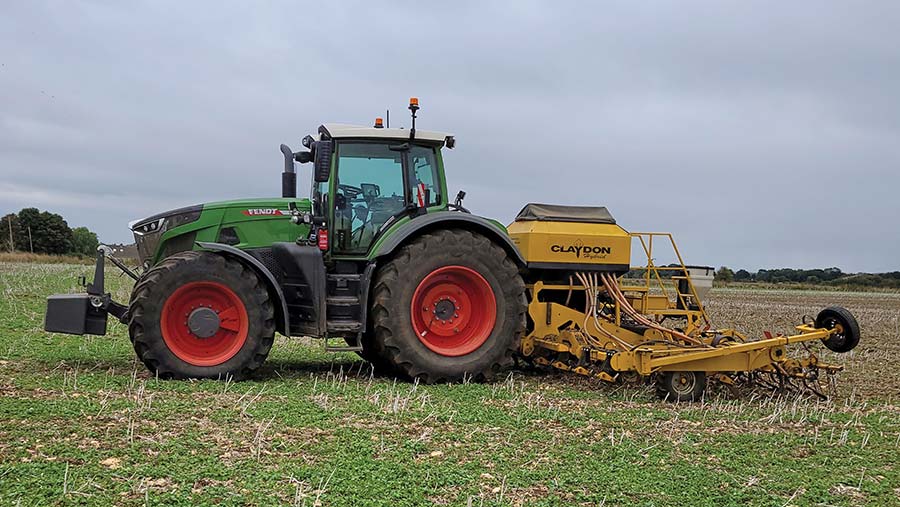
6m Claydon Hybrid on the back of the Fendt 936 © James Andrews
How brand loyal are you?
We’re more interested in the job a machine can do than the colour of the paintwork, but there are a few brands that we keep going back to.
On the tractor front, we’d had John Deere for years, but things changed when we needed a bigger model to pull our 6m mounted Claydon Hybrid drill.
Getting a Deere that was up to the task would have meant going for the 8R range and I thought they were just too clumsy to be useful for any other jobs.
That’s when the Fendt 936 came to our attention. It’s still a big lump of a tractor, but it’s neat enough that we can use it for general tasks such as carting grain if we need to.
Since then, our old 6930 has been swapped for a Fendt 718 and we’ve just got another second-hand 724, so our only Deere is a classic 2130.
We’ve also got a four-cylinder New Holland T6.140 that’s been a good tractor.
When it comes to implements, Kuhn is probably our go-to brand, as the equipment is usually well engineered.
We’ve also bought a couple of bits of Claydon kit – a straw rake and Terrablade hoe – to complement the drill.
Favourite dealer?
We like dealing with Jeremy Turney at Turney Agriculture, which is where our combine, drill and all the Kuhn kit comes from.
But we also get on well with Chandlers and use Tallis Amos or Farol if they’ve got parts we need.
Favourite piece of kit?
It has to be the Claydon drill, as it’s saved us so much money and time since we moved to the system in 2012.
Before this we were burning gallons of diesel pulling a Vaderstad Topdown, then going back through with a Kverneland TS tine drill, and it didn’t give us any better results.
In fact, yields have gone up slightly since those days.
We also like the fact that the Claydon gets the job done with minimal moving parts, unlike a Mzuri which we looked at briefly at the time.
The only downsides are that it’s heavy, meaning you need a big tractor on the front, and depth control can be a bit inconsistent.
However, since moving to a hydraulic top link, I’ve been able to tweak the angle of the drill on undulating ground to make it a little more even.
There’s also no half-width shut-off as standard, but we’ve managed to fit a new Kverneland lid on the distribution head that does the job.
We just need to keep an eye out for blocked spouts as the odd grain can trickle around the sides of the shut-off plates.
Least favourite piece of kit?
We still make a few small square bales with a 1995 Welger AP730, and although it’s a good machine, it can be a pig to get running right some days.
We’ve also been disappointed with the paint quality on our one-year-old JCB 542-70, which is already starting to flake off. The black paint is the worst, but there are also some poor patches on the yellow.
It’s unacceptable for a machine that costs £95,000, but JCB’s attitude seems to be that we should just put up with it. It’s a real shame as the handler itself is great.
Latest purchase?
It’s a Fendt 724 that was bought second-hand on 6,000 hours.
We wouldn’t normally buy a tractor with that much work behind it, but it’s come in as an extra machine to avoid us needing to hire one at busy times of year.
With rental machines costing about £13,000 for a 10-week stint, we’d only need to do this six times to cover the £75,000 cost of the investment.
It’s also been handy having an extra tractor in the quieter times, and we’ve got it hooked to the McConnel PA6565T hedgecutter for the winter.
I think it had been given a hard life, but Chandlers did a good job of smartening it up.
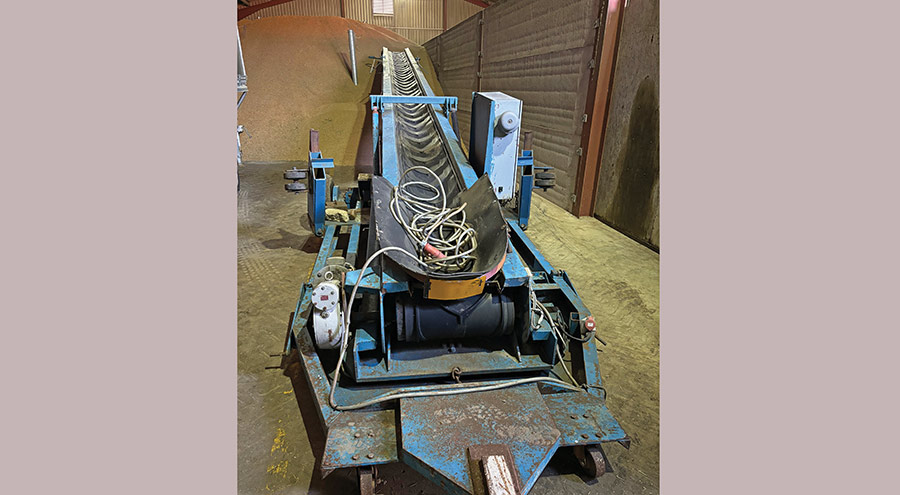
Oldest machine – a 1980s BW grain elevator © James Andrews
Oldest machine still at work?
The oldest tractor is the John Deere 2130 which was bought new in 1976 for £2,460, including a Duncan safety cab.
It has been used for all sorts over the years, but its last proper job was pulling a muck scraper.
It had been parked up for years until my son William decided we should get it going, so we dragged it out and set about tidying it up.
There weren’t any significant mechanical problems – it’s only done about 6,000 hours – but the rear wheels had completely rotted out from their years of being caked in muck.
Some replacement centres were sourced from Nick Young Tractor Parts, but they weren’t quite the right fit, so we had to do a bit of cutting and welding.
It’s still not in showroom condition, but it works and it does the odd stint with the Haybob, as well as carting stuff around with a link box on the back.
Another oldie that gets far more work is a 1980s BW elevator. Half the grain gets loaded into the stores with this and it’s great for piling it high and working around the cooling pedestals.
It also seems to create a looser heap than when you push it up with a telehandler, which must help with air flow.
It only takes about 10 minutes to unload our 16t trailer, so it’s not much slower than tipping and pushing up either.
How long do you keep your machines?
There’s no set policy, but the main pieces of machinery tend to stay for about 10 years or until they’ve done roughly 6,000 hours.
It’s not always that straightforward though. For example, we only had our John Deere 7230R for a few years as we needed more horsepower and lift capacity.
All of our Fendt tractors, apart from the 724, have got a four-year warranty, so there’ll also be some decisions to be made when these are up.
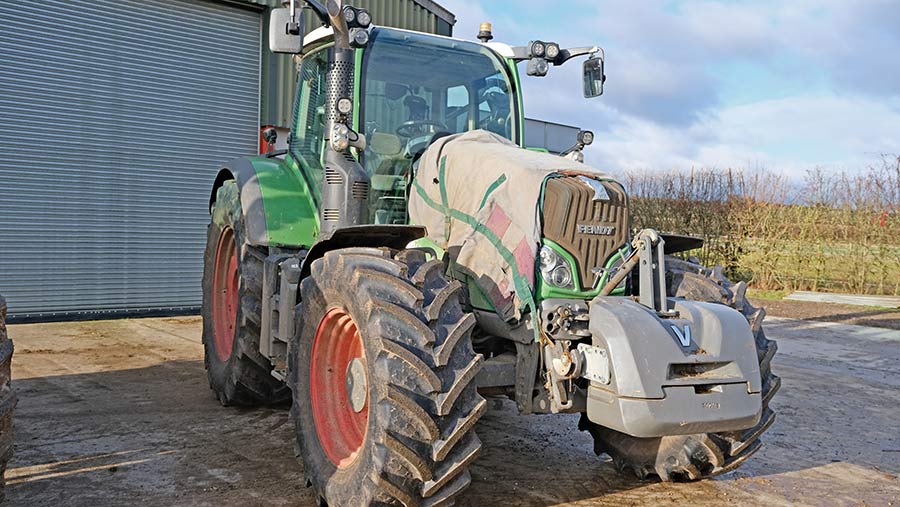
Latest arrival is a 6,000-hour 724 currently on hedgecutting duty © James Andrews
What’s next on your wish list?
As much as I like the Claydon, I’m keen to get a lower-disturbance drill to run alongside it, in the hope it will help us tackle some of the worst blackgrass fields.
Claydon does offer some disc and slimmer tine options for the Hybrid or Evolution, but I’m currently leaning towards a John Deere 750A or a Horsch Avatar, both of which we’ve had demonstrations of.
Horizon also came out to demo its DSX, but that seemed unnecessarily complex with its fancy air pressure system.
Whichever one we choose, the plan is to use it to plant directly into legume fallows, which we are going into through SFI.
Biggest machinery mistake?
Years ago, when we moved from a 12m to 21m sprayer, I set off around the headland, lost sight of the tramline and instinctively swung in to the 12m position.
This buried the boom deep in the hedge and we had to get a replacement section as it was bent beyond repair.
Dad also dropped into a collapsed roadside drain while hedgecutting with the 718 and a piece of protruding metal slashed the sidewall of the rear tyre. It’s running on Michelins, so the replacement cost about £2,500.
Most expensive repair bill?
A couple of years ago, we were saddled with a £20,000 bill for a new header frame after hitting stone buried in rock-hard ground. The knife escaped, but the lower section was completely trashed.
We managed to finish the season by cutting with the table pushed fully forward and our insurer, NFU Mutual, thankfully covered the cost.
Another steep one was a £4,500 repair on the Welger conventional baler, when the connecting rod snapped and buried itself in the plunger.
The insurance covered it again, even though the baler wouldn’t be worth much more than that.
Most overpriced spare part?
I’ve just had to shell out £1,100 for a 30cm-long double-yoke pto shaft for our Spearhead topper, which is ridiculous. It should be £300 tops.
What couldn’t you live without in the workshop?
The Oxford arc welder. It might be old, but it does a great job and gets us out of all sorts of holes. A good angle grinder is a must too and we’d seriously struggle without a compressor these days.
We’ve actually got airline adapters on of most of the tractors, so we can inflate tyres and blow out radiators or cab floors without having to go back to the yard.
What’s your everyday transport?
It’s a 2007 Isuzu Rodeo, which has been on the farm since it was a couple of years old. It was decidedly flat to start with, but since we had it remapped it’s been a lot better.
Reliability has been good over the 96,000 miles it has travelled and it hasn’t suffered from corrosion yet.
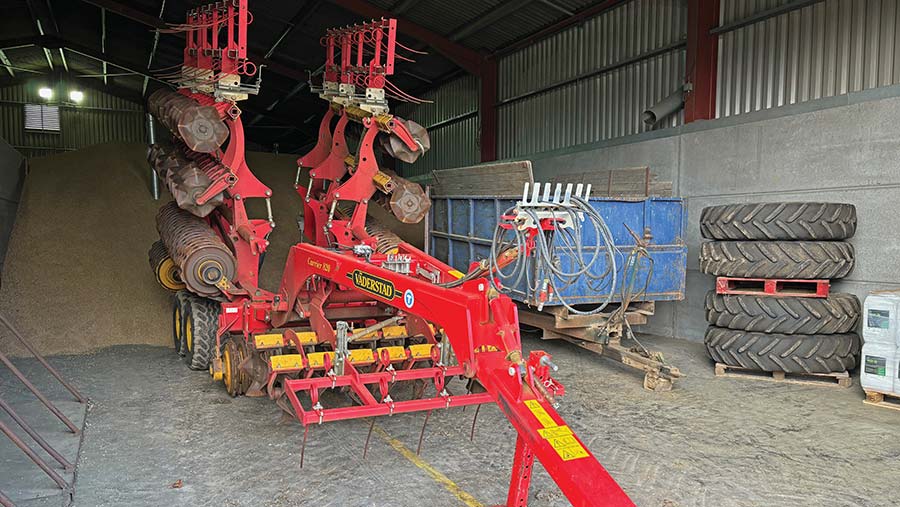
An 8.2m Vaderstad Carrier remains part of the cultivator fleet © James Andrews
Best tractor you’ve ever had?
We had a John Deere 7810, which was brilliant and only lost £12,000 in the 11 years we owned it.
But as good as it was, it can’t hold a candle to the Fendt 936. The power of this tractor is something else, and the level of technology on board makes the work so much more accurate.
You obviously can’t compare the two directly as they’re from different eras, but I know which one I’d rather be driving.
Worst tractor you’d ever had?
It wasn’t a bad tractor as such, but I never really got on with the John Deere 7230R we had before the 936.
Part of the problem was that it wasn’t really gutsy enough to handle the Claydon drill, but because it was quite a big tractor physically, it felt like it should.
Cab noise was also higher than I was expecting, particularly the howling ventilation fans in the roof.
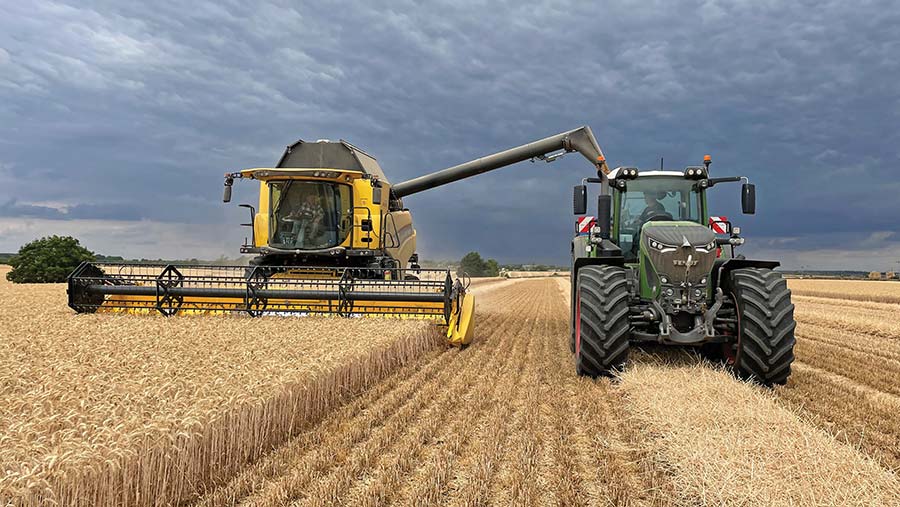
Eating cereals… the New Holland CR7.90 © James Andrews
Most surprisingly useful piece of farm technology?
Most of our kit now runs on isobus and it’s great that we can shuffle implements between tractors without having to keep moving control units around. It also helps cut down on cab clutter.
Most pointless piece of farm technology?
Agronomy firms trying to convince you to sign up for fancy software systems that give 20-odd layers of information on a map.
I’m not against field mapping in general – we’ve had the farm zoned and have saved a fortune by applying variable-rate P and K – but the level of information some companies try and flog you is simply ridiculous.
Biggest machinery bargain?
I bought a fully functioning Meijer Holland flat-eight bale sledge at a farm sale for just £10 and we’ve got years of use out of it. It goes to show that there is still the odd bargain out there.
In the shed
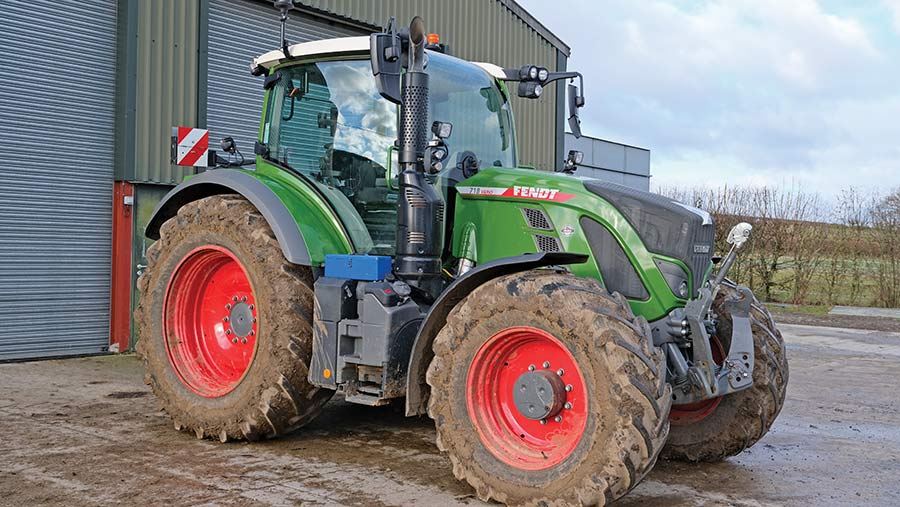
Fendt 718
- Tractors Fendt 936, 724 and 718, New Holland T6.140, John Deere 2130
- Combine New Holland CR7.90 with 7.5m header
- Telehandlers JCB Loadall 542.70 Agri Xtra and Manitou 630
- Cultivation kit 8.2m Vaderstad Carrier, 3m McConnel Shakaerator, 7.5m Claydon straw rake, 6m Claydon Terrablade hoe, six-furrow Kverneland plough and press
- Drill 6m mounted Claydon Hybrid
- Sprayer Bateman RB26 with 36m boom
- Forage equipment 3m Kuhn mower, four-rotor Kuhn tedder, twin-rotor Krone rake, Haybob
- Trailers 16t Stewart, 14t AS and 10t Richard Western grain trailers
- Other Kuhn fertiliser spreader, BW grain elevator, Kuhn bale spreader, McConnel 6.2m topper, 3m Spearhead topper, McConnel PA6565T hedgecutter, 20t Master mobile grain dryer