What’s in Your Shed? visits a Yorkshire arable farm
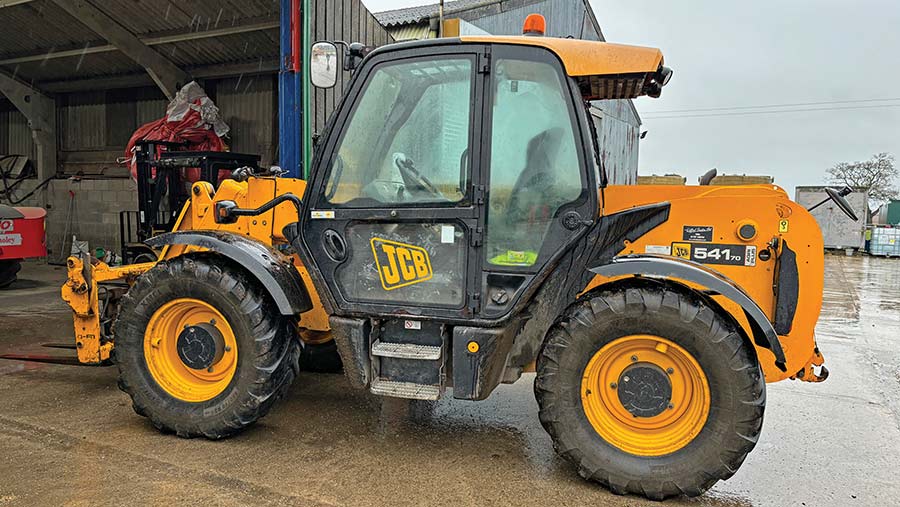
Lifting the lid on their machinery shed high and lows are Yorkshire arable farmers Michael and Will Scholey.
See also: How to adapt cut-price cultivators for low-disturbance system
How brand loyal are you?
We’ve had John Deere tractors and machinery for the past 30 years, partly because Ripon Farm Services has got a depot just down the road, but also because we like most of the kit.
Things have started to fall apart recently though. We’ve been disappointed with our last couple of combines – particularly the current one – and John Deere has a very arrogant and unhelpful approach to the problem.
We’re considering a move to Fendt tractors as a result, and Claas or New Holland will likely be our next combine provider.
Favourite dealer?
Dealers have got a tough job on their hands, getting pushed around by the big manufacturers on the one hand, and then also having to deal with the flak from customers when machines break down or won’t perform.
Ripon Farm Services has always given us a good service and the workshop goes out of its way to keep us going.
There are also some great independent outfits near us, such as Richard Burniston and Spruce & Hawe, both of which are handy for universal spares. Hydrapower at York comes in handy for hydraulic components and repairs.
Farm facts: CW Scholey and CM Scholey
- Farm size 1,070ha (335ha farmed by Will under CW Scholey and 735ha farmed by Michael under CM Scholey – some machinery is jointly owned)
- Cropping Winter wheat, winter barley, spring barley, beans, linseed, oilseed rape
-
Staff Steve Garnett and Roger Venton
Latest purchase?
It’s an ex-demonstrator John Deere 6R 250 that we got last season when it was on 120 hours.
At £215,000, it was a bit cheaper than ordering a brand new one, and we were still able to get a five-year warranty so we know roughly what the running costs will be.
During harvest it was hooked to our Perard Interbenne 27 chaser bin with Machine Sync set up so that the combine driver can take control and move it around for more efficient filling.
It then moved onto the 7.2m Sabre Tine drill, which it pulls with ease.
It’s really comfortable to drive and the controls are a step up from our other Deeres – the Command Pro joystick is particularly nice to use.
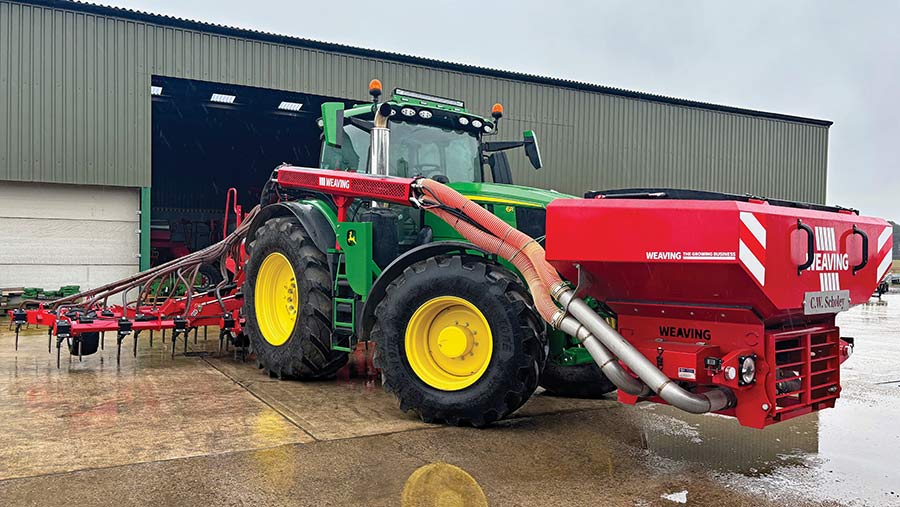
6R 250 with Sabre Tine drill © James Andrews
Oldest machine still at work?
That would be our 2009 JCB Loadall 541-70, which has been a great machine. It came to us on 1,000 hours when it was a couple of years old and it’s now worked 6,500 without any significant problems.
We’ve also got a 2017 541-70, that has been equally reliable.
We’re fans of the Loadall, so haven’t shopped around much. However, we did have a Kramer out on demo once which we thought was expensive for what it was.
How long do you keep your machines?
Generally, we’ll buy tidy ex-demonstrator or low-hour machines, but we make sure we have some warranty, ideally five years, included in the deal to help cushion us against any nasty breakdowns.
There’s no set replacement policy in place though, so once the warranty is up we’ll usually hang onto them for a while.
It’s a bit of a gamble, but the hope is that we can dodge the expensive problems and get a few cheaper years of ownership.
That said, if a reasonable deal for a replacement comes our way before that time, we may well go for it.
Favourite piece of kit?
The Weaving GD drills. We got the first one eight years ago when we decided to move away from a power harrow combination tine drill and they do a great job of getting crops in the ground without disturbing too much soil.
The undercut discs are particularly effective at burying seed and they’ve proved reliable and cost-effective to run.
That said, we have worked hard to build up organic matter and improve the state of the soil, which has dramatically improved the conditions they’re working in.
They’re not so good when the ground gets a bit sticky, in which case we often put them back in the shed and switch to using the Sabre Tine.
Least favourite piece of kit?
Our 2023 S790i combine has been a real disappointment. John Deere heavily advertises that this machine can cut 75t/hour and, after two serious discussions, we were assured that it was more than up to the job of harvesting our 1,070ha.
However, in the real world, it can’t get anywhere near that output, which meant we had to pay for a contractor to help us finish last year’s harvest.
Part of the problem is that it’s seriously down on power, so much so that we often couldn’t get it to unload on the move when the straw chopper was engaged.
But even when we were able to push it on, the losses would go through the roof.
It was so bad that Ripon Farm Services came out to do tray tests several times, which showed that it was achieving just 50t/hour with losses at 0.4%.
We then pushed it on as hard as the engine would allow and got it up to 54t/hour, but it was chucking grain over the back in heaps, with losses measuring 9%.
Their combine specialist did his best, but he couldn’t performance the output any further, so we were stuck with a significantly reduced output.
Eventually, John Deere’s northern combine specialist came out to see us and said he’d be “quite happy” with it achieving 50t/hour, and if we really wanted more, we should consider upgrading to an X9.
The cost of buying the S790i was bad enough at £32/acre (£79/ha) but moving to the bigger, twin-rotor machine would put it up to £51/acre (£126/ha), which makes no financial sense.
Cost aside, we were keen to have an X9 on demo to see how it would fit in with our system and we’ve been promised one for the last two seasons. We’re still waiting.
We seem to have reached a stalemate, so as soon as we’re able, we’ll be moving to a Claas or New Holland.
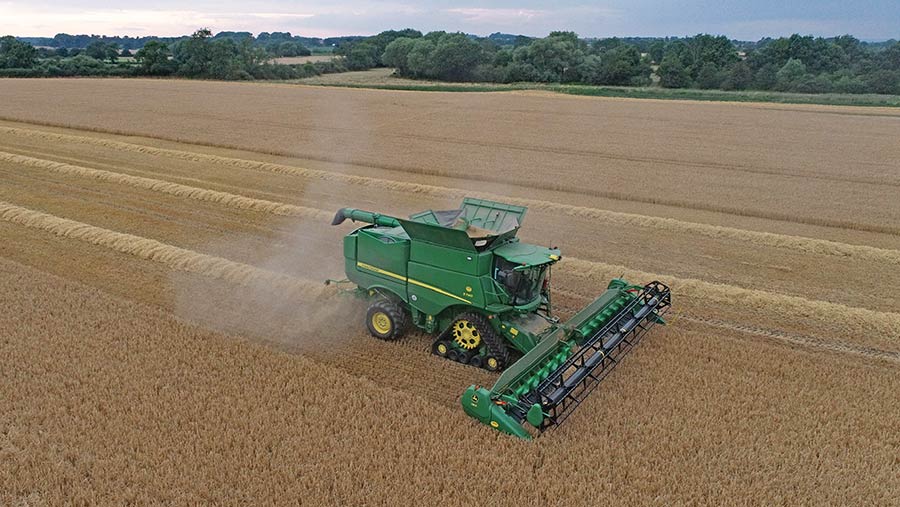
John Deere S790i Combine © James Andrews
Next on your wish list?
We’ve got a lot of cultivation kit – mostly old McConnel Shakaerators that we’ve customised to do different jobs – but there’s always room for more.
At Lamma we spotted a Dalbo Maxiroll with a double Guttler press at the rear, and the option of spring straw rake tines, levelling paddles or fixed tines on the front.
It could prove handy for getting a weed seed chit on ground that’s too tough for the straw rake to make much of an impression, while also packing the ground down to create a nice level surface for the GD drills.
The levelling paddle option might be good for knocking down furrows on the ground we rotationally plough.
Hopefully, Dalbo will bring a demonstrator out for us to try this spring.
Biggest machinery mistake?
A few years ago, one of our previous sprayer operators picked up the wrong can when filling the tank and managed to burn off 70 acres of beans.
Most expensive repair bill?
We had a John Deere 6930 that we hung onto for longer than usual and it suffered catastrophic engine failure when it got to 8,500 hours. A whole new block had to be fitted at a cost of £8,000.
Soon after that, a crack developed in the exhaust manifold that set a wiring loom on fire, at which point we decided its luck was up and we sold it on.
Most overpriced spare part?
So many parts are ludicrously expensive, but the most overpriced one we’ve come across recently was a £4,000 replacement wiring loom for the Kuhn fertiliser spreader.
Best invention?
Our oilseed rape drill has probably been one of the best. It’s based on a 3m McConnel Shakaerator converted to low-disturbance legs, with a Kuhn power harrow mounted in the middle and a set of Weaving double-disc coulters at the rear.
The legs loosen the ground to 6 or 8in and we set the power harrow very shallow so that it creates a fine surface tilth without damaging the soil structure.
Seed is delivered to the discs via a Techneat Terracast V2 applicator and we fitted large GD press wheels behind to consolidate the ground. We can also pipe liquid fertiliser behind the discs from a front-mounted tank.
It only cost about £7,500 to build and it gets the crop off to a good start without us having to spend a fortune on establishment, only for the flea beetle to hammer it.
Another neat one is a bracket to hold the Sabre Tine’s drill pipe on the side of the 6R 250, which a local engineer with a laser cutter made up for us.
In the shed
- Tractors John Deere 6R 250, 6215R x3 and 6195R with loader
- Combine John Deere S790i with 10.7m (35ft) draper header
- Sprayer 36m Chafer Interceptor
- Drills 6m Weaving GD x2, 6m Weaving Sabre Tine with JJ Metcalfe legs for drilling beans, 7.2m Weaving Sabre Tine with front tank, 3m homemade oilseed rape drill
- Cultivation kit 3m McConnel Shakaerator x4 with various combinations of JJ Metcalfe legs, 4.5m Sumo Multipress with Belotta spring tines, 7.5m Mzuri straw rake, 6.5m Vaderstad Carrier with Crosscutter discs, six-furrow Kuhn Vari-master 153 plough, 6m Kuhn power harrow
- Telehandlers JCB Loadall 541-70 x2
- Trailers Perrard Interbenne 27 chaser bin, Bailey grain trailers 16t x2 and 18t
- Other Kuhn Axis 50.2 HEMC fertiliser spreader, 5.7t Kubota digger
What couldn’t you live without in the workshop?
We’d be lost without the Oxford mig welder, pillar drill and hydraulic press. They’re all essential bits of kit for us.
What’s your everyday transport?
The old farm runaround is a 1998 Defender 90 300tdi that’s done 270,000 miles on the original engine, gearbox and clutch, despite doing lots of heavy towing during its lifetime.
Chassis corrosion is its only Achilles heel, and we’ve got to the point where we’re putting patches on top of patches.
Our main vehicles are a 2017 VW Amarok V6 that belongs to Michael and Will’s 2021 Ford Ranger Wildtrak.
The former was bought second-hand for just £16,000 when it was on 81,000 miles and it’s been brilliant.
There’s bags of power which makes it great for towing, but you can still get more than 35mpg if you take it easy on a long run.
The Ranger is nice to drive too, but it lacks power when pulling heavy trailers.
Best tractor you’ve ever had?
Like most people that have had one, it was our John Deere 7810 with a powershift transmission.
The engine sounded fantastic and it had plenty of low-end torque for pulling the heavy cultivation kit we had at the time. It also had the weight to put that power down, with heavy cast wheel centres.
We bought it second-hand when it was on 1,000 hours and it did 7,000 more with us without giving any problems. The only reason we moved it on is that it wasn’t as comfortable to drive as the newer models.
And the worst?
We had a John Deere 7280 for a while that was clumsy for its power and always seemed sluggish and numb.
It stayed with us for a couple of years, but we sold it when it started jumping out of first gear.
Most surprisingly useful feature you’ve found on a machine?
When we bought our Chafer Interceptor self-propelled sprayer, we shelled out for pulse-width modulation and it seems to have been a worthwhile investment.
Straight away, we could see the benefit of the turn compensation evening out dosing on corners, and the fact we can go when conditions are less than ideal helps increase the number of spraying days.
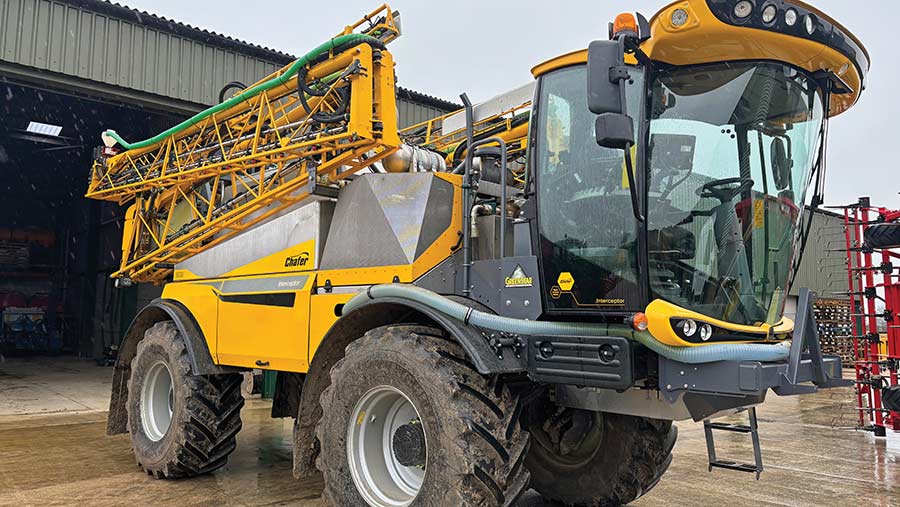
© James Andrews
Most pointless piece of farm technology?
When we have to pay John Deere unlock fees for features like SF3 or section control, there are usually a few other functions thrown in that we’re never going to use.
It would be nice if they could just provide the functions we want, and do so for a lower price.
Biggest bargain?
The Amarok pickup (mentioned earlier) was a good buy and our modified McConnel Shakaerators have been great value for money.
But the biggest bargain is probably the Kuhn 3002 power harrow that we useon the oilseed rape drill and Weaving 3m cultivator drill. It was in great condition and only cost £1,500.