What’s in Your Shed? visits a Cumbrian farming family
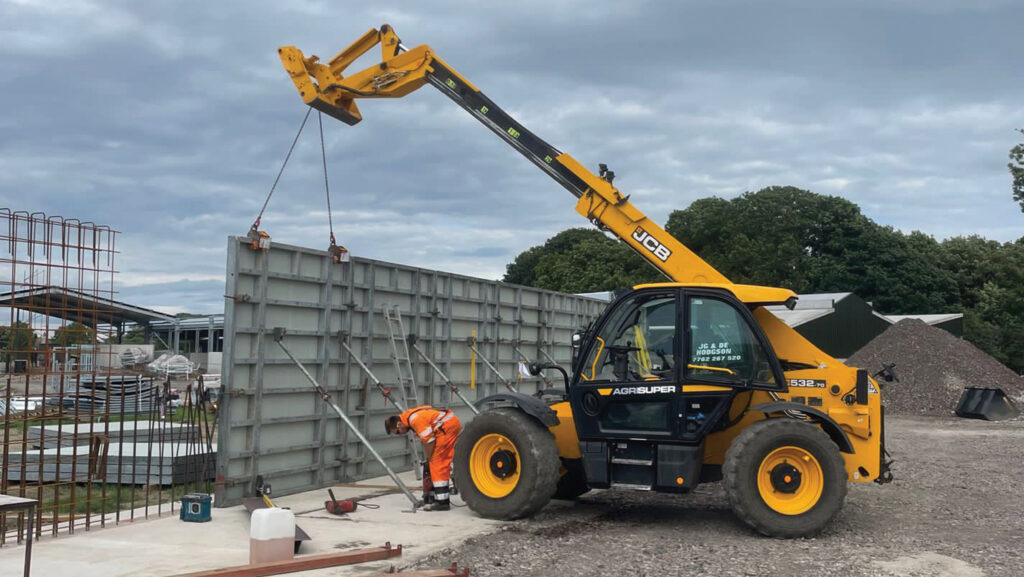
Tractor paint colour matters little to Cumbrian farmers and contractors Vaughan, Karl and Ryan Hodgson, who run a mixed fleet of Fendts, JCBs and John Deeres.
See also: Direct drills revisited: Mzuri Pro-Til 3T out, Avatar in
Farm facts: JG and DE Hodgson
Farming 160ha arable, 40ha grass, two x 57,000-bird broiler units
Contracting Cultivation and drilling, spraying, muck and slurry spreading, land drainage, poultry shed cleaning
Other Fabrication, construction, concrete and groundworks, caustic wheat production and bulk haulage
Staff Vaughan, Karl and Ryan Hodgson plus Tom Nixon, James Hollick, Aidan Jeffreys and Andrew Graham full-time. Matty Langcake and John Menzies part-time in the workshop
In the shed
Tractors Fendt 828, JCB Fastrac 4220, John Deere 6930
Combine Claas Trion 650 TT with 25ft header
Telehandlers JCB Loadall 542-70 and 532-70, 540-140 HiVis and Teletruk 35D
Sprayer McConnel Agribuggy A280
Drills 3m Horsch Express KR combination drill, 4m Horsch Pronto
Cultivation kit Kuhn Varimaster 123 five-furrow plough, Spaldings Flatlift subsoiler, 3m Horsch Joker with TG bar, 6.3m He-Va Cambridge rolls, AFT trencher, 3m Lemken Topas
Other Scania R580 V8 and Fruehauf bulk tipper, Herbst 14t dump trailer, Larrington 20t dump trailer, Larrington 24t tri-axle grain trailer, Keenan 400 Promix+ paddle mixer, McHale V6 750 round baler, 20t Mecmar grain dryer, Abbey 4,000gal tanker, Bunning 15t muckspreader, Amazone ZA-M Novis 24m fertiliser spreader, JCB JS140 zero tail swing digger and Z-45/25J Genie cherry picker
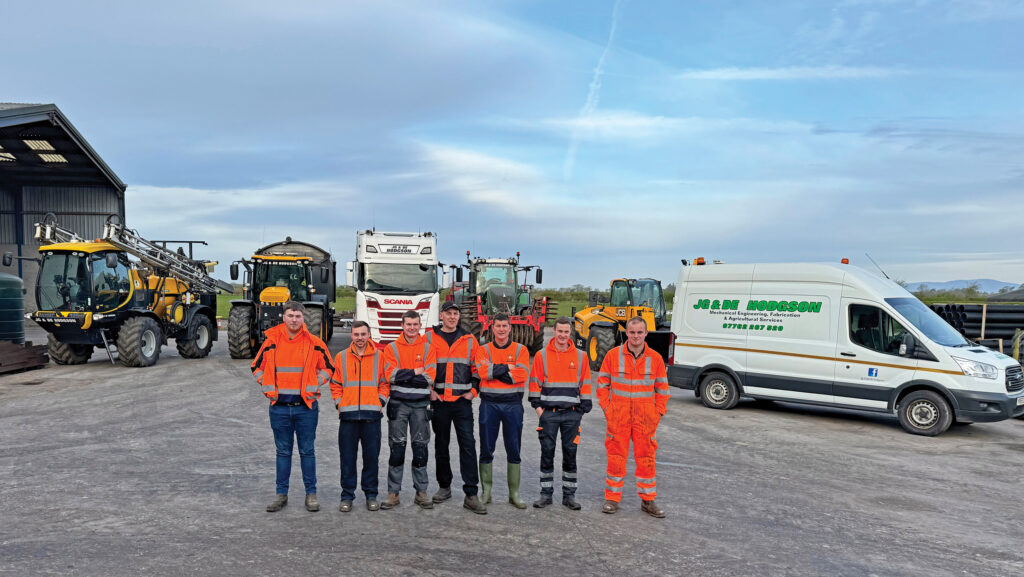
The team consists of Vaughan, Karl, and Ryan Hodgson, along with additional full-time and part-time staff © James Andrews
What’s your business setup?
The land part of the business is our 200ha farm near Wigton, Cumbria, which is made up of 160ha arable and 40ha grass.
But we have several other ventures running alongside. There are two 57,000-bird broiler sheds that rear chickens under contract for Frank Bird Poultry, we do a mix of contracting work and we produce 7,800t a year of caustic wheat.
This is sold directly or through consultants and merchants to dairy farms in the local area and south-west Scotland.
We are expanding all the time, moving into the east of Scotland and further south, with output set to increase to 10,000t or more.
Ryan heads up the fabrication, construction and civil engineering side of the business, which involves making and erecting steel-framed buildings, carrying out groundworks and concreting.
Recent projects include a rotary parlour installation and a 60x15m free-standing silage pit with 300mm-thick walls.
We also have a well-equipped workshop which allows us to carry out our own repairs to a high standard, as well as those for our customers.
It’s fitted out with mig, tig, AC/DC and stick welders so we can handle a wide of range of work.
Our aim over recent years has been to bring as many of the jobs we need to do on the farm in-house, which helps reduce costs, increase efficiency and reduce downtime.
As part of that, we bought a Scania tractor unit and Fruehauf bulk tipper so we can do our own haulage and some contract work.
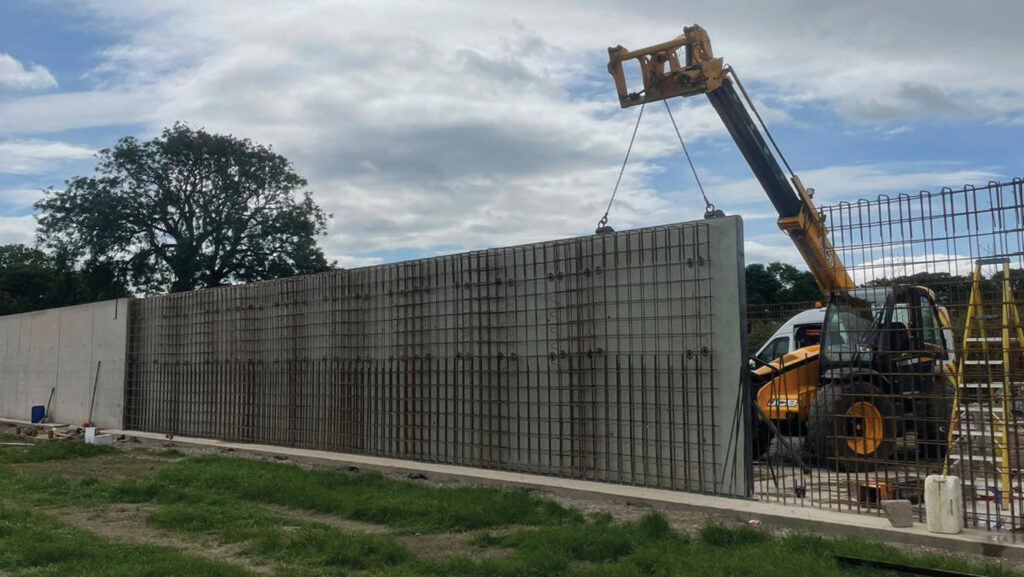
Ryan heads up the fabrication, construction and civil engineering side of the business, which involves making and erecting steel-framed buildings, carrying out groundworks and concreting © James Andrews
How brand loyal are you?
On the tractor front, not very. We have a Fendt 828, a JCB Fastrac and a John Deere 6930, which we think are some of the best tractors for the jobs we are doing – the machine itself and the value for money is more important to us than the brand.
That said, we are fans of JCB telehandlers and have four different models for various parts of the business.
We have a 532-70 that works mainly on the farm, a 542-70 for our caustic wheat facility, a 540-140 for the construction work and a Teletruk 35D for the workshop.
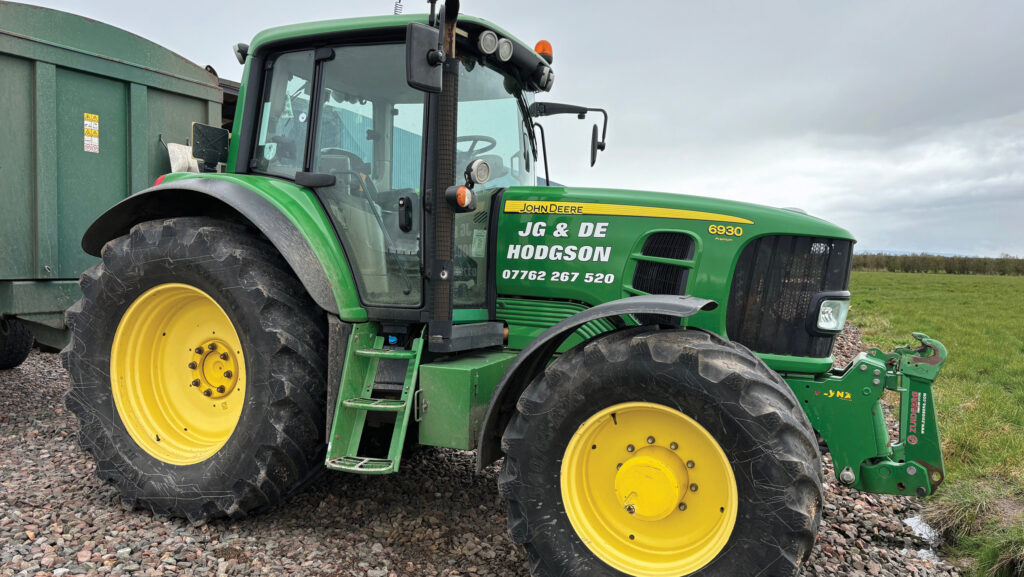
© James Andrews
Favourite dealer?
Scott JCB Carlisle has always provided excellent support. We have also been impressed with the level of service from PV Dobson at Kendal, having had a bad experience with our more local Fendt dealer.
Rickerby is another firm we respect and like dealing with – it has a great reputation for service and backup locally, which is the main reason we have just bought a new Claas combine.
Favourite piece of kit?
The Fendt 828. It’s a great all-rounder, performing well in the field and on the road. It is also surprisingly manoeuvrable for its size and really nice to drive.
It hasn’t been without its faults, though. We bought it from Chandlers when it was a year old on just 1,500 hours and 200 hours later the engine started giving trouble.
The tractor was still under warranty, but the nearest Fendt dealer let us down badly with its level of support and attitude. We have now switched over to PV Dobson at Kendal, which fitted it with a new engine.
We haven’t had any problems in the 2,000 hours worked since, other than a leaking hydraulic pipe under the cab, and we still think it’s a great tractor.
The only complaint from a driving point of view is that you need to really stand on the brakes to get them to work. Even then, they are still nowhere near as good as the Fastrac’s.
Before buying it, we also priced up a John Deere 6250R. It was a nice tractor but was a bit more expensive.
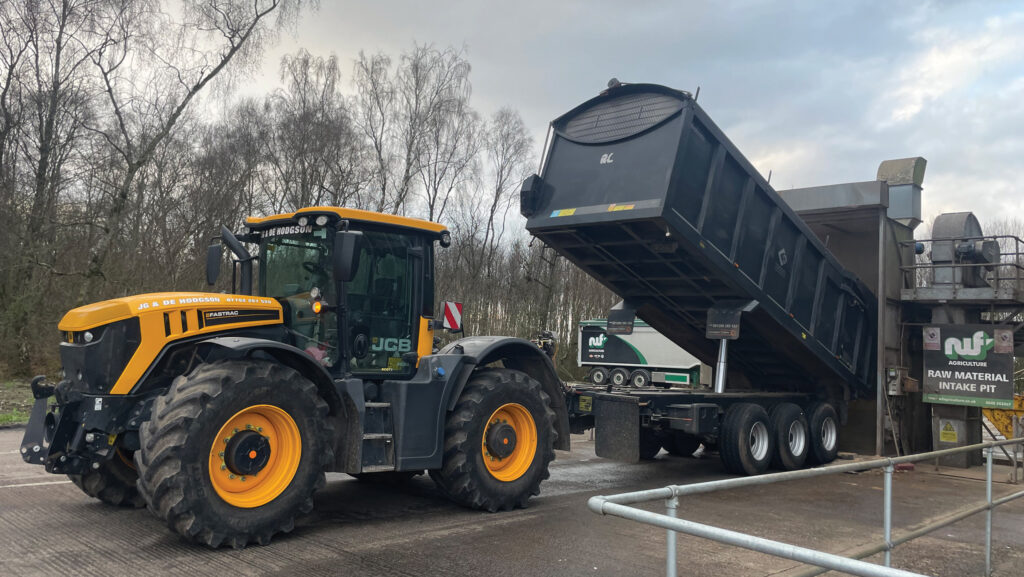
© James Andrews
Least favourite piece of kit?
Years ago we had a PZ Haybob for tedding and raking, neither of which it was any good at.
None of us much like operating our widened Camon rotavator, either. The machine itself is fine, but we use it for turning the chopped straw bedding in our broiler units which is a warm, dusty job.
It is worth it, though, as it really freshens up the litter, improves welfare and the birds love it afterwards.
Latest purchase?
There have been a few new pieces of kit recently, the biggest of which is a Claas Trion 650 six-walker combine on tracks with a 25ft header.
We have used a contractor in the past, which worked well, but with more permanent staff we are now able to do the job in-house.
At about £300,000 it was a huge investment, but one we think will pay off over the life of the machine.
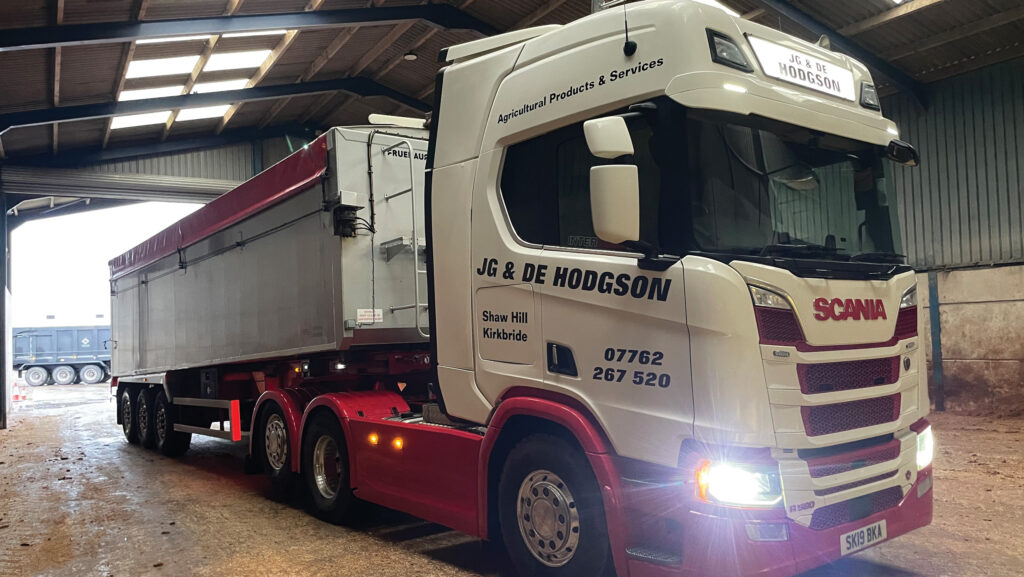
© James Andrews
Another is the 2019 Scania R580 V8 tractor unit with 2016 Fruehauf bulk tipper, which has allowed us to start doing our own haulage and really streamlined the caustic wheat side of the business.
We tried out a Unimog before buying the Scania but didn’t get on with it. One of the problems was that the back end could get pushed around by large trailers.
The JCB Loadall 540-140 HiVis arrived new this year too, as we wanted a long-reach model for the construction work.
Also worth mentioning are a second-hand AFT100 drainage trencher that we spied on Facebook for £22,000 and a used Lemken Topas 3m front cultivator that we picked up for just £2,400.
The latter allows us to carry out single-pass grass seeding with our Horsch Express KR combi drill, which gives a great finish and is a huge time- and money-saver for customers.

© James Andrews
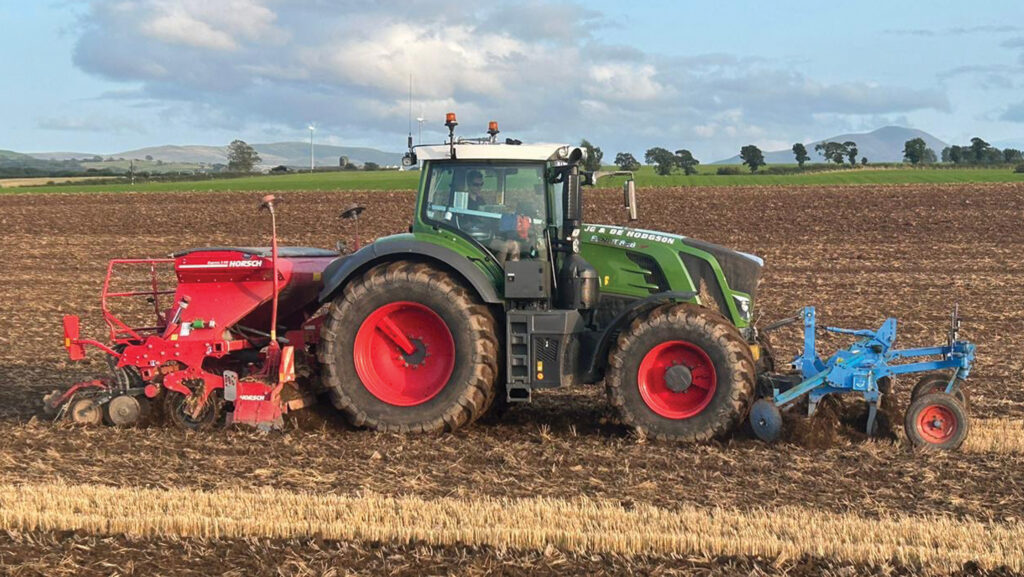
© James Andrews
Oldest machine still at work?
Because of the restricted height in our broiler sheds, our old Massey Ferguson 135 is still the tool of choice for feeding, scraping out and washing down.
Ryan restored it when he was at Newton Rigg College, but some of the non-genuine Agriline parts he used are now giving us trouble, which is disappointing.
Nothing can really touch it for the poultry shed work, though. It runs on the merest whiff of diesel and it’s surprisingly nice to drive for a tractor that is more than 50 years old.
We also have a couple of refurbished 3t Marshall wooden-sided tipping trailers to go behind it, which come in handy for small jobs.
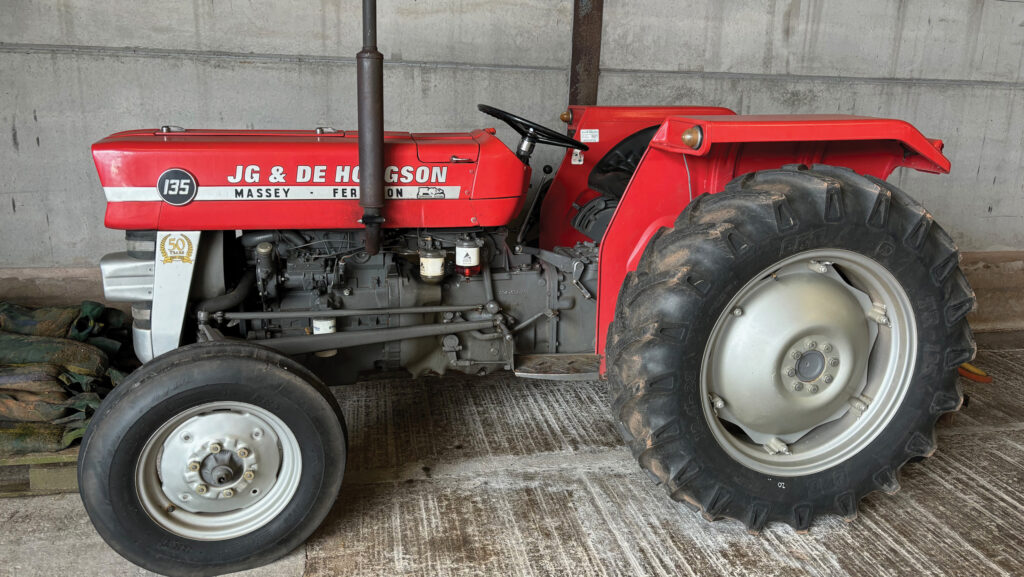
Massey Ferguson 135 © James Andrews
How long do you keep your machines?
Frontline tractors and the Loadalls tend to stay with us for four or five years, but the rest only get moved on when they become unreliable, expensive to repair or we see something that will do the job better.
We maintain all our kit to a high standard; it all gets thoroughly washed after use, put through the workshop, sprayed with a diesel/oil mix and then stored in the dry.
Next on your wish list?
It would be nice to get a blower trailer for the lorry, so that we could haul our own chicken feed. We use about 3,500t a year, so it would be a considerable saving on transport costs.
Another chicken shed is a possibility – plans have already been approved – to take our capacity up to 171,000 birds.
It would cost well over £700,000, but it should work out significantly cheaper if Ryan and his team can undertake the whole project.
We’d also like a round bale squeeze trailer for delivering bales more efficiently and, most importantly, safely.
However, they are a bit pricey and the metal ones seem heavy to take on the land. A strap-sided version might be a better bet.
Biggest machinery mistake?
Karl: I had a little incident a few years ago when driving down an icy hill with the Fastrac and a load of chicken muck in tow.
As I eased off the throttle, the transmission slowed down too much, causing the wheels to lock and the tractor to start sliding.
The trailer jack-knifed, popped off the hitch and slid into the verge, snapping the Suzies [air lines], pipes and lighting cable in the process.
No one was hurt but it took us half a day to recover as we had to take a digger to the scene to empty out the trailer before we could load it onto a low-loader and take it home for repair.
Vaughan: Years ago, I was leading silage with a Marshall QM14 silage trailer, which I managed to tip over on the road. Thankfully, a flattened road sign was the only casualty.
Ryan: Recently, I backed into the workshop welding jib with the top of the works van, putting a massive dint in the top panel. It was hugely embarrassing, but we soon repaired it ourselves.
Most expensive repair bill?
The solenoid for the gearbox cooling fan failed on our old Kellands Agribuggy 2500. Kellands hadn’t fitted a warning buzzer or temperature gauge on this model, so we kept driving until it packed up.
That landed us with a £4,500 bill for a completely new gearbox.
Most overpriced spare part?
There’s a small, insignificant-looking T-piece gearbox on the Camon rotavator we use in the poultry sheds. It failed recently and cost a staggering £950 to replace. But, as it’s nine years old, we can live with that.
Best invention?
After finding out that a Grange toolbar to go in front of our 4m Horsch Pronto would be about £30,000, we decided to make our own.
We already had a 3m TG bar for our Horsch Joker, so we bought two extra legs and Ryan and Tom made removable side extensions to increase it to 4m.
The leg assemblies were pricey – about £1,000 each – but it saved us a fortune compared with buying a separate implement.
The combination gives us the option of direct drilling when conditions are right and we’ve already had some good results with wheat and oilseed rape.
It hasn’t been out much this last season, though – the plough and combi drill have been a godsend.
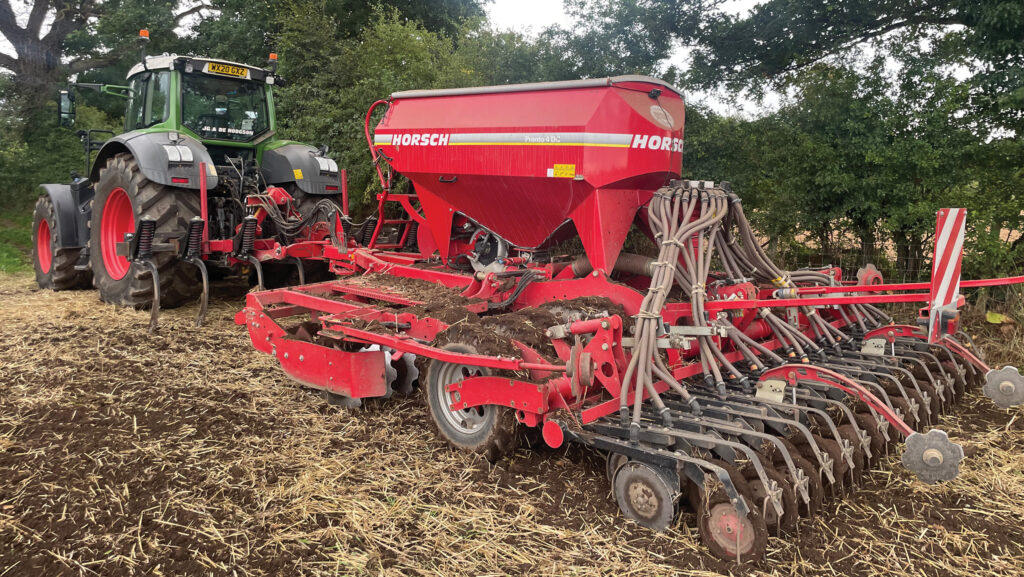
© James Andrews
What couldn’t you live without in the workshop?
The welder, hydraulic press and battery impact wrench are the essentials. But we also have a 10t Spaldings air-assisted jack, which is amazing for changing the sprayer wheels efficiently and safely.
What’s your everyday transport?
We managed for years having a farm pickup, but we were missing having a decent towing vehicle, particularly for the construction side of the business.
A local farmer was selling his 2019 Toyota Hilux Invincible which was tidy and on just 26,000 miles, so we went for it.
It’s a good truck and comfortable to drive, but it would be nice if it had leather rather than cloth seats as they would be easier to keep clean. Instead, we recently bought some leatherette covers for them.
Fuel use isn’t the best, either, with mpg averaging mid-20s when there’s nothing on the back and about 18 with a heavy trailer in tow.
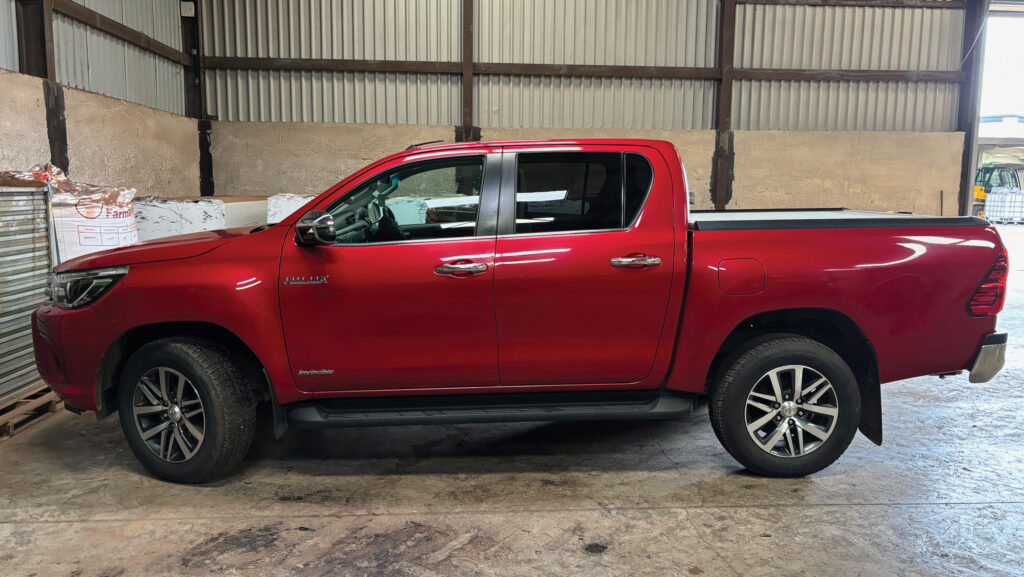
© James Andrews
Best tractor you’ve ever had?
Without doubt, our John Deere 2011 6930. It had all the usual problems in its earlier years – head gasket, EGR cooler and turbo – but it’s a brilliant, reliable and powerful tractor that’s easy to drive.
We bought it new and for years it was our frontline machine, but now it’s on 9,000 hours and so it acts as more of a backup.
That said, it still racks up quite a few hours running the Keenan mixer wagon and pressure washers.
It’s also been chipped to just over 200hp and it pulls like a train as a result.
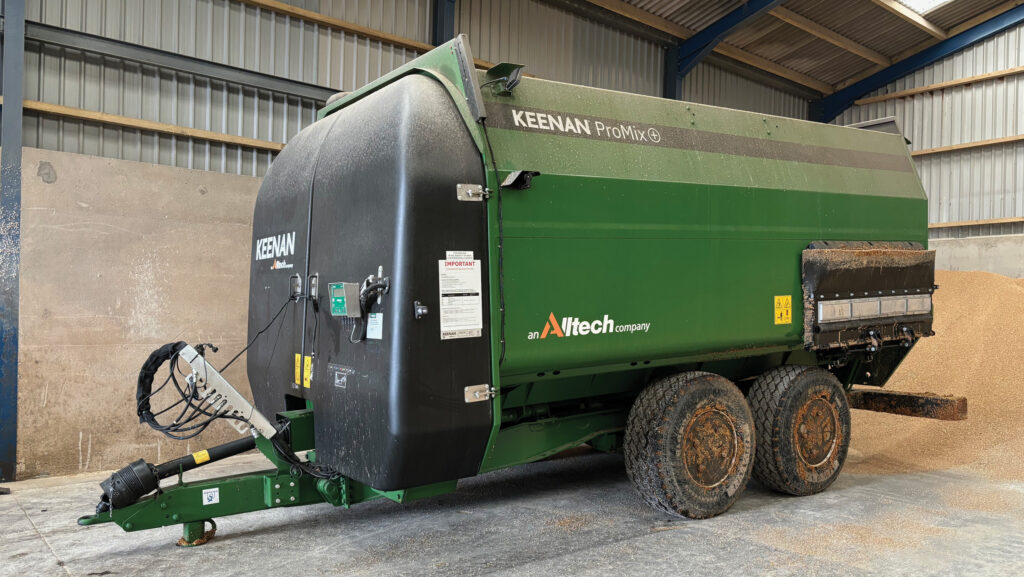
© James Andrews
And the worst?
Years ago, we had a Case 885XL that was a bad starter and gutless when it did get going.
Our first Fastrac 4220 was also plagued with problems, such as a failed front diff, snapped rear wishbone, leaking hub seals and loads of failed sensors.
It was a proper Friday afternoon tractor – thankfully, the current one has been far better.
Most surprisingly useful feature on a machine?
When we first got the Fendt, we were manually setting up the implements each time we put them on. Then we realised we could save multiple profiles – what a useful feature that is.
Most pointless piece of farm technology?
We’ve got an unlock code for section control on our AgLeader RTK GPS screen. It isn’t much use on our 21-year-old Amazone fert spreader.
Biggest machinery bargain?
Our 2003 Amazone ZA-M Novis fertiliser spreader has been the best value. It’s basic and simple, but we have looked after it and it still gives an accurate spread pattern on its annual tray test.
Machinery aside, our best long-term investment has definitely been the two broiler sheds.