What’s in Your Shed? visits a busy Somerset arable farm
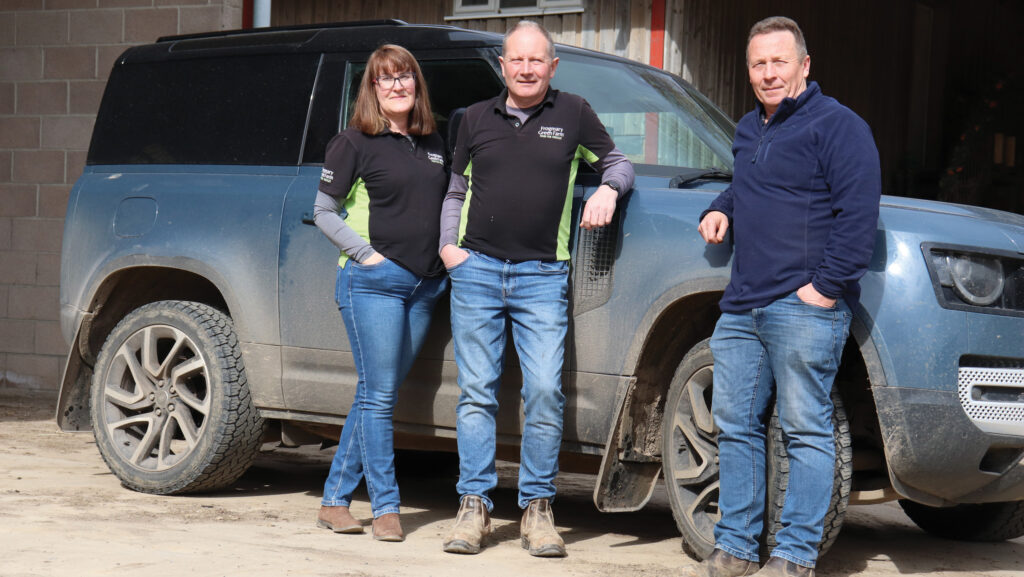
Keeping a hungry Somerset anaerobic digestion plant properly fed and operational requires a fleet of high-output, modern kit.
What’s in Your Shed? takes a tour of Bragg Farming’s machinery sheds with Nick Bragg and arable foreman Graham Glasper.
See also: On test: Fendt’s four-cylinder, 224hp 620 – small engine, big power
Business facts: Frogmary Farm, South Petherton, Somerset
- Farming operation: 400ha rented, 2,400ha contracting
- Cropping: Maize, winter barley, winter wheat, oilseed rape, sunflowers and grass. About 90% of the crops are fed into an Engie-owned AD plant at Frogmary Green Farm
- Other services: Frogmary Farm has a contract with Engie UK to procure all the crop intake and spread the digestate for the Frogmary plant
- Staff: Nick and Claire Bragg, plus 10 full time
How did you get started?
Nick: It’s the usual story of the small family farm not being able to support one more, so I had to do my own thing.
After leaving school, I started out with six sheep before progressing to rearing store cattle and eventually hiring out muckspreaders.
By 1994-95, I’d spotted a niche for hiring potato equipment to growers in Somerset.
First acquisitions were a de-stoner, bed former, bed tiller and harvester, and extra kit followed as demand and finance allowed.
I soon got fed up with the state in which much of the hired kit was returned, so this prompted me to offer a specialist potato contracting service – from bed forming to harvest.
Again, this expanded rapidly, such that by 2002 we were providing a full potato service across 280ha.
Over the next decade we had two major breaks. The first was in 2006 when I inherited Frogmary Green Farm (40ha) from my uncle.
With Frogmary as a base, we were able to set up a 110,000-bird broiler operation alongside the potato side.
We also eventually diversified into enterprises such as running a conference centre, classroom, shepherd huts, café, wedding venue and spa.
The second pivotal moment came in 2014, when we were approached by an AD operator to host a 600cu m/hour biogas plant at Frogmary – that’s enough gas for nearly 4,000 homes.
I’d become disillusioned with the feast/famine, high-risk nature of the potato business, and AD presented us with a more dependable alternative. So, we went for it.
Which pretty much brings us to today.
We’ve since packed up the potato business and have sold off the land and buildings at Frogmary Green Farm.
This has enabled us to fully focus on arable farming as well as procuring the Engie-owned plant’s feedstock and spreading its digestate.
In total, we rent 400ha and grow crops on contract and spread digestate on a further 2,400ha.
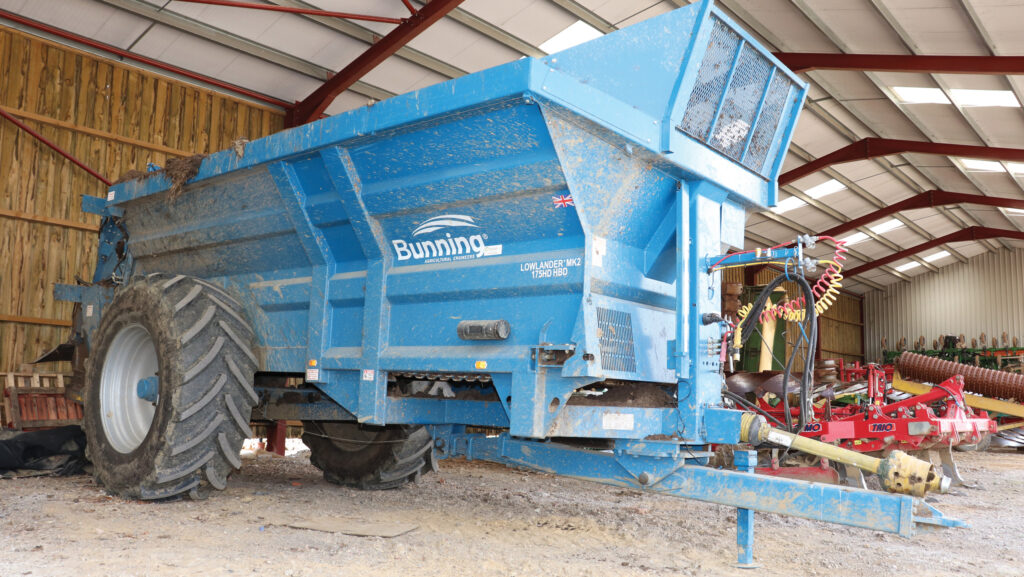
© Andrew Faulkner
How brand loyal are you?
Extremely. We’re probably a little unusual in that we use one main dealer, Compass Tractors, at Bridgwater, and it supplies about 90% of our equipment.
That includes Fendt tractors and combines, Krone foragers, JCB handlers and shovels, Amazone drills, Samson tankers and Sumo cultivation kit.
For us, it’s a case of if it works, why change? Our first potato tractor was a 260hp Fendt back in the early 2000s, and I’ve stuck with the brand ever since.
We keep the tractors for 12 to 18 months, at which time Compass is looking for the optimum resale price. When we’re both happy with the value, the tractor is replaced.
Just as importantly, our operators like the Fendts, and they’ve proved reliable. Given our acreage and workload, downtime must be kept to an absolute minimum.
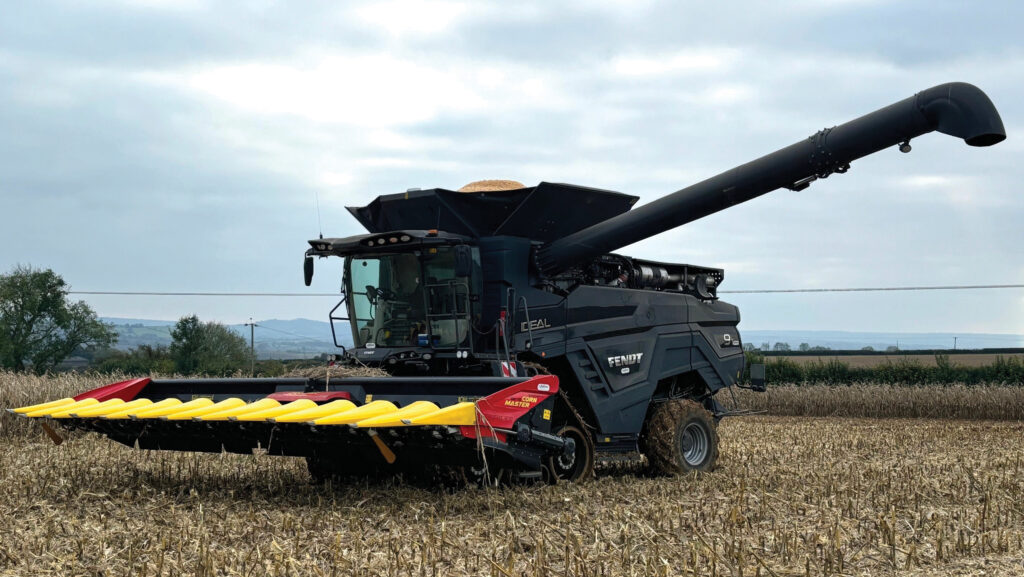
Fendt Ideal 9T combine switches between grain and maize headers © Graham Glasper
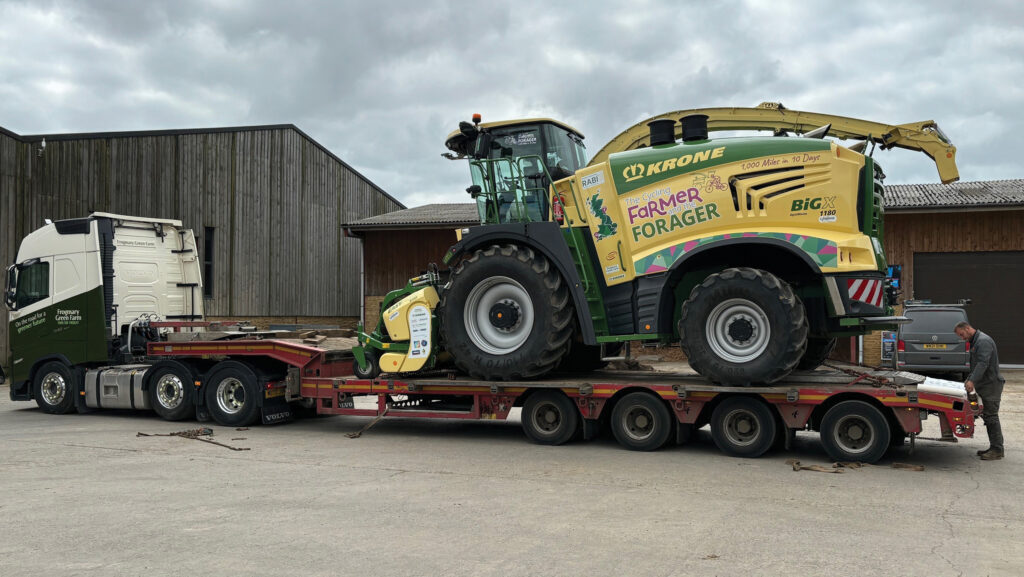
Krone Big X 1180 forager © Andrew Faulkner
Favourite dealer?
No surprise here: it’s Compass. The firm’s managing director, Justin Nichols, set up the company in 2004 at a similar time to our expansion, so effectively our two businesses have grown together.
Where we’re changing the tractors so regularly, he’s continually looking for the best resale, for a figure that works for both of us. It’s a good relationship.
The Compass workshop and fitters are excellent, too. They’ve been known to work through the night to get the forager up and running again, for example.
Admittedly, we do use other dealers on the odd occasion, such as the recent purchase of an eight-furrow Kverneland plough from C&O Tractors, and a 12m Amazone Condor drill from Crawfords in Kent.
Graham: It’s also worth mentioning the service we get from Bateman on the sprayer.
The workshop will always call back within 30mins even when they’re flat out, and their service vans are running around all over the country.
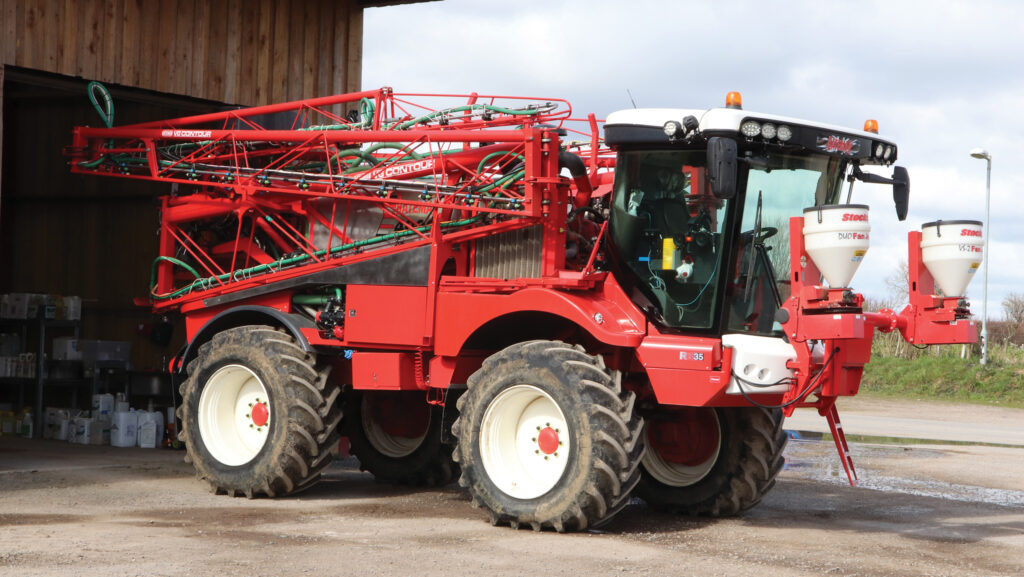
Bateman RB35 sprayer © Andrew Faulkner
Favourite piece of kit?
Nick: The Fendt 942s are fantastic bits of kit; just a great combination of power and comfort.
With their air braking, CVT transmission and suspension, it’s like driving a truck on the road. Though they’re large compared with the 700s, they’re still versatile enough for trailer and top work.
Graham: For me it’s the Bateman. Again, it’s comfortable, but it’s also an easy machine to use compared with some others.
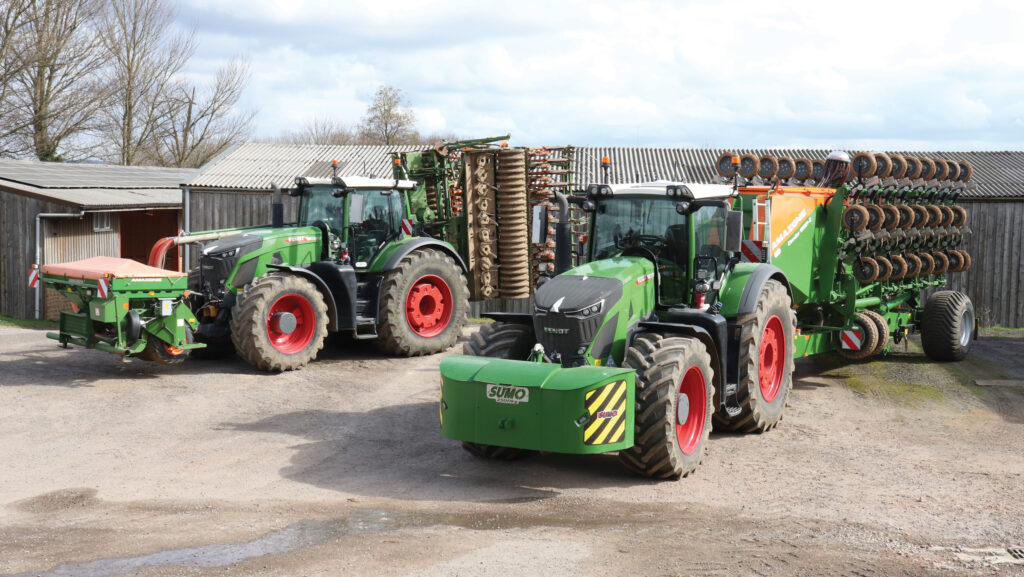
© Andrew Faulkner
And your least favourite?
Nick: Even though we don’t have one anymore, it’d be JCB’s 8000-series Fastrac. We persevered with Fastracs for six years, but never really got on with them.
They felt underpowered for their weight, we suffered loads of gearbox issues, and they struggled with oil supply for running implements such as the Bunning spreaders. Put simply, they don’t compare with a Fendt.
Latest purchase?
Most recent arrivals are a new Volvo truck, the Kverneland 6300S eight-furrow plough and a JCB 560-80 Loadall.
The Volvo is an extra tractor unit, the KV replaces a six-furrow Ovlac to help cover the acreage and make better use of the 942’s 400hp, and the 560-80 is to replace a smaller model to handle a recently acquired 4t grain/maize bucket.
We’ve tried other handler makes such as Manitou and Merlo in the past but ended up with JCB – again, largely down to reliability.
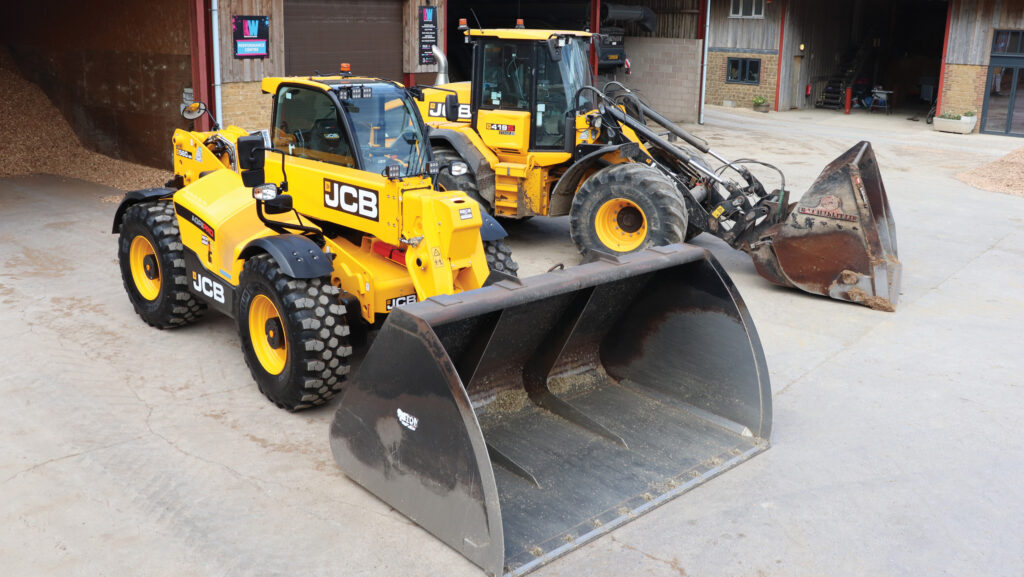
Latest addition to the fleet is a JCB Loadall 560-80 © Andrew Faulkner
Oldest machine still at work?
That’ll be grandfather’s Massey Ferguson 135, which he bought new in 1965.
I refurbed it when I was at college, and it’s still put to work on jobs such as splitting maize film, hauling a small water bowser and participating in tractor runs.
We’ll never get rid of it; it’s like a member of the family.
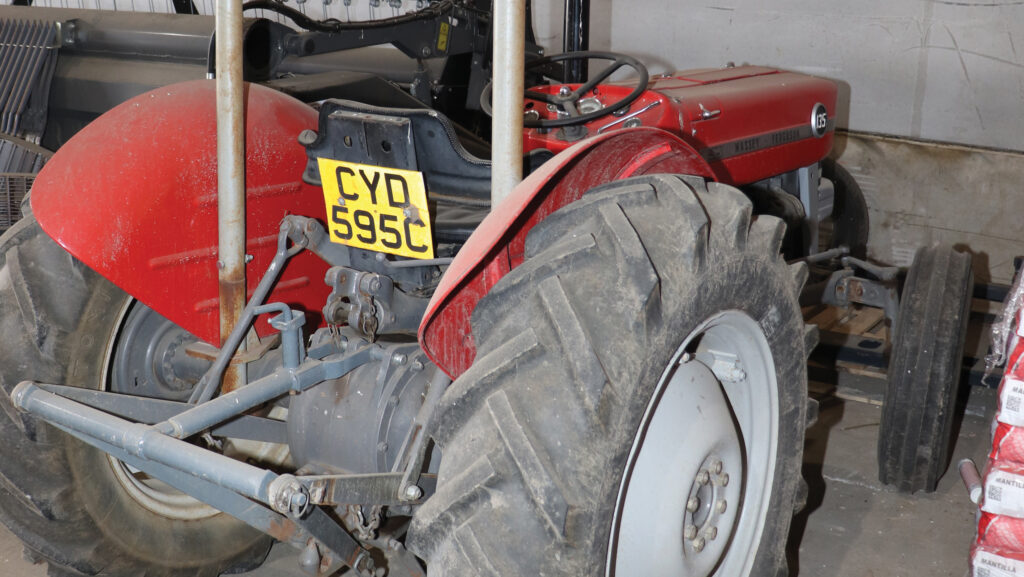
1965 MF 135 © Andrew Faulkner
How long do you keep your machines?
As mentioned, the tractors are typically kept 12 to 18 months until Compass has hit the resale sweet spot. Everything else, including the trucks, is on a four-year cycle, depending on reliability and resale value.
We’ll also buy nearly new where it makes sense. For example, the Bateman self-propelled was bought at 18 months old from a local dealer/farmer who generally takes a new sprayer every 18 months.
Next on your wish list?
Probably another two trucks over the next couple of years.
We currently run four, which carry out about 70% of our on-road produce movements – hauling feedstock back to the AD plant, ferrying digestate out to lagoons or fields, shifting machines on lowloaders, etc.
We’d like to get that up to 85% of movements so that the tractors are increasingly off the road.
I also need to do more research into mobile loaders/elevators for field-loading the artics. Ideally, we need to find something that’s easy to move around and, importantly, reliable.
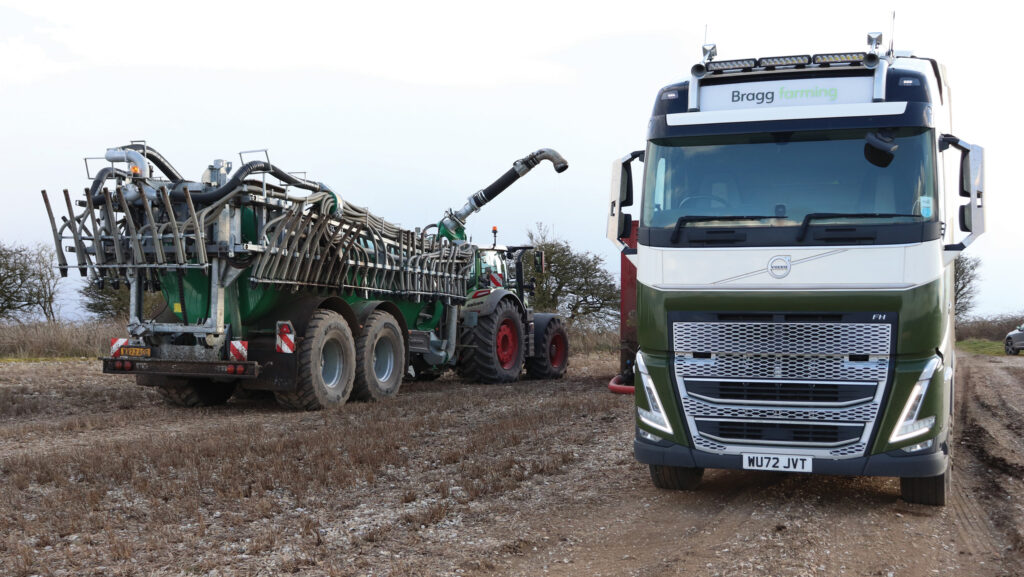
Feeding an AD plant and spreading its digestate dominates the workload © Andrew Faulkner
Biggest machinery mistake?
A former operator managed to drop the wheels of a loaded 18cu m Joskin tanker off the side of a concrete track on a made-up piece of ground.
The tanker’s steering system crabbed, parting tanker from tractor and sending it down a slope.
Fortunately, the tractor stayed upright on the track and no-one was hurt, but we had to hire in mats and two cranes to recover the tanker and its contents from the bottom of the slope.
In total, it was a four-day rescue job. Not happy, but it could’ve been worse.
Most expensive repair bill?
We’ve been really lucky in that we haven’t suffered anything too major – one of the big advantages of running a fleet that’s pretty much always in warranty.
Priciest spare part?
Again, running most of our equipment within a warranty period means we rarely suffer with expensive repair bills and downtime.
However, £1,800 for a new Fendt windscreen is one of the downsides of that curved glass, and I’m always staggered by the cost of replacement wing mirrors.
All tractors and trucks now have mirror guards, which is an improvement.
Best invention?
We’re not inventors. There’s no time, as the AD work is full on for most of the year; the plant always needs feeding and never stops producing digestate.
That said, we’re currently converting an old 9,000-litre milk tanker into a trailed water/fert bowser. Fitted with a Honda petrol engine, it should increase the efficiency of our spraying operation.
What couldn’t you live without in the workshop?
One of our operators, Big John, spends winter months in the workshop, and he’d say there is nothing in there he could live without.
To be fair, it’s well kitted with the usual stuff – MIG welder, plasma cutter, compressor. He’s an excellent welder, which is great for the occasional strengthening of kit as well as repairs.
Favourite and least favourite jobs?
Nick: For me, it’s anything that gets me out of the office, which, nowadays, is so rare that I’ve been badged “The Apprentice”. Stick me on a 942 with a drill or cultivator and I’m happy.
Least favourite is dealing with complaints from the general public – an occupational hazard when working over a large area.
Working late, making noise in a field, dust, lorries too large for narrow lanes… we get them all (keyboard warriors).
We have a responsibility to clean up mud on the highway, yet we’ll even get abuse from motorists for delaying them while we’re doing so.
Graham: I like most jobs, but combining and ploughing are the main favourites, especially when they’re going well.
The new KV plough has made a big difference to output and leaves a great finish.
What’s your everyday transport?
Nick: A 71-plate Land Rover Defender 90 Commercial with 38,000 miles on the clock.
I bought it second-hand at 32,600 miles, and I’ll probably run it for another 18 months, by when it’ll be up to about 80,000 miles.
The Defender is more comfortable than my previous pickup, and I’d happily drive it to Scotland and back. I love it.
Best tractor you’ve had?
The best we’ve had would be the current pair of 942s, for all the reasons outlined earlier. They’re great to drive and reliable.
And the worst?
Again, we’ve already mentioned them. We shouldn’t have persevered with the Fastrac 8000-series for as long as we did.
Biggest machinery bargain?
Probably our Simba SL600 disc/tine/press cultivator that we bought from Warwickshire firm Amtec (formerly Ellis Machinery) 18 months ago.
We paid £16,000 for the machine, and then refurbed it ourselves with new wearing metal, new bearings, some fabrication work and a complete respray. It’s covered a fair amount of ground already and has gone well.
Best and worst pieces of technology?
Nick: Mobile phones rank as both my best and worst. I’d clearly struggle to operate without them, but they’re also the source of most of my grief.
Social media is another hot topic – for all its pluses, there are plenty of negatives.
Graham: GPS is fantastic when it’s working, but we’re increasingly having problems with the signal dropping out, especially near to the Yeovilton air base.
Biggest bugbear?
Nick: It has to be the weather… and the ever-shortening windows for getting on the ground, not only for conventional arable work but also for spreading digestate.
It’s the overriding reason why we operate such a large and regularly updated fleet.
Kit list
- Tractors: Fendt 942 x2, 728 x2, 724 x2
- Combine: Fendt Ideal 9T (10.7m grain header)
- Forager: Krone Big X 1180 with grass pick-up and 12-row X Collect maize/wholecrop header
- Handlers: JCB 419S shovel, 560-80 and 542-70 Loadalls
- Sprayer: Bateman RB35 (4,000-litre/36m)
- Mowers: Krone Easycut F320M front and B950 rear
- Drills: 12m Amazone Condor, 6m Amazone power harrow combi (front/rear), eight-row Amazone ED 6000 Super and four-row Samco
- Cultivators: 4m Sumo Quatro disc/leg, 5m Sumo LDS subsoiler, Kverneland 6300S eight-furrow plough, 6m Simba SL disc press, 6m Kuhn power harrow x2
- Digestate: Samson TG20 tanker with 24m dribble boom, 18m SlurryKat umbilical system, Bunning Lowlander Mk2 rear-discharge spreader
- Other kit: Volvo x3 and Scania artics with D-Tec tankers, bulkers and a low-loader; tractor-towed trailers include AW x2, Hi-Spec x2 and a Rolland