What’s in Your Shed? Used kit key for Hampshire arable farm
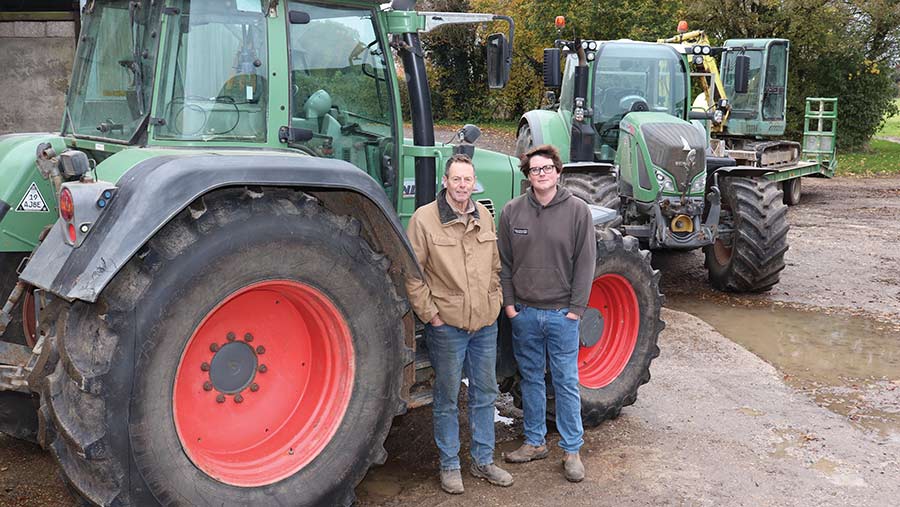
‘Buy used kit and maintain it well’ is the machinery fleet principle applied by Hampshire farmers Bob Ives and his son, Dan.
Diversification is also important to the business and includes a Land Rover servicing enterprise and consulting for TV programmes including Top Gear and The Grand Tour.
We catch up with the farming family in this latest edition of What’s in Your Shed?.
See also: On test: JCB’s new TM420S pivot-steer telehandler
Farm facts: Ashley Farm, Bentworth, Hampshire
- Farm size 120ha of owned land, plus 50ha of arable contracting for Bob Ives’ brother, Joe
- Cropping Wheat, oilseed rape, and grass in an environmental scheme
- Stock None
- Soil type Clay cap over chalk
- Staff Bob and Fiona Ives and son, Dan
How did you get started?
Bob: My father, Bill, is a first-generation farmer who was evacuated as a child during the war from London to Sussex, and fell in love with farming.
Years later, he and my mother, Peggy, ended up as tenants on the Herriard Estate, where my brother, Joe, still farms today.
From a 20-cow, 35ha holding in the late 1950s, it’s grown into a 260-cow, four-robot operation, producing almost 14,000 litres/cow a year.
Joe and I worked with father on the farm full-time from the 1980s. Then, with the third generation in mind, we amicably split the management of the business in 2018, even though we’re all still partners.
Joe and his family remained on the main farm, while I, Fiona and our son, Dan, moved to an owned 120ha arable unit, Ashley Farm, about six miles away.
We do the arable work for Joe, and it all runs remarkably smoothly. Fiona continues to look after the admin for both farms as well as for other farming clients.
With just 120ha of arable at Ashley, diversification is obviously important.
For many years I’ve acted as an off-road consultant and route planner for motoring programmes such as Top Gear and The Grand Tour, and Dan is building up a Land Rover servicing enterprise, specialising in older Discovery Tdi models and Defenders.
We clearly can’t justify running new kit on our acreage, yet the various diversifications mean time is still at a premium.
So our aim is to invest in high-output, second-hand machines that cover the ground quickly, we can service ourselves and won’t need changing in the foreseeable future.
How brand loyal are you?
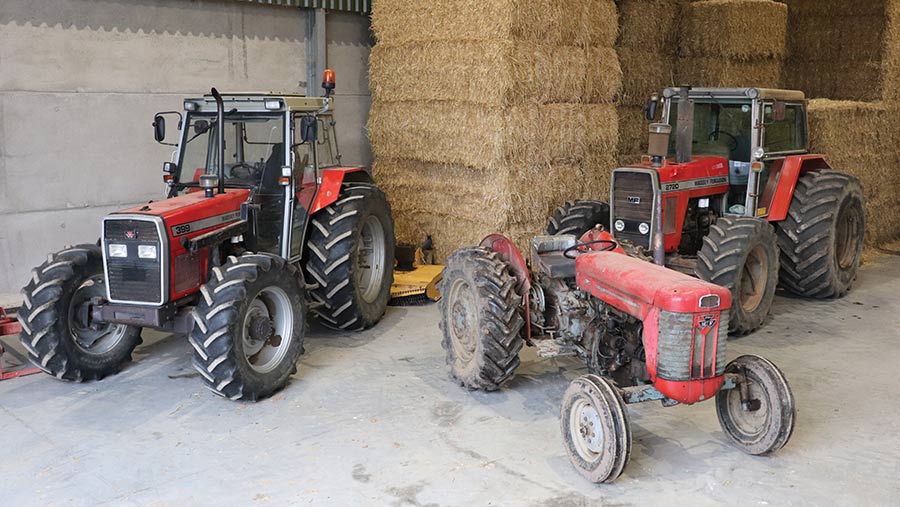
© Andrew Faulkner
Agco and JCB are our brands of choice for tractors and telehandlers. For some reason, Dan and I have a shared aversion to anything green/yellow.
Father ran Masseys through the 1960s and 70s, bought from long-defunct dealer Wallis & Stevens in Basingstoke, and we still have four older Massey classics at Ashley for jobs such as log splitting, topping and rolling.
These include an MF 399 loader tractor imported from Denmark at a shipped price of £14,000, and a 2720 that came up from Cornwall for £12,000.
We went for our first Fendt, an 818, about 20 years ago, and now operate this alongside a seven-year-old 724, which arrived here in 2020.
Dan: On telehandlers, our choice has been rather limited because of our preference for pivot-steers for their manoeuvrability, central driving position and the steering’s side-shift capability.
Plus we don’t need to stack any higher than 5m. We’ve been through Matbro and Manitou but have now settled on JCB.
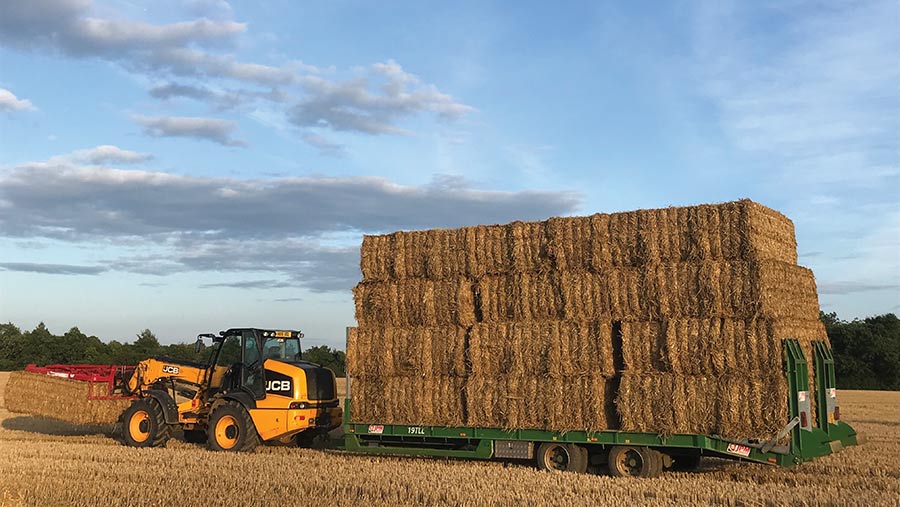
JCB © Andrew Faulkner
Favourite dealer?
There are several. Mike Garwood is local and really helpful; if you drop in with a burst hydraulic pipe, the workshop staff will stop what they’re doing to sort you out.
Haynes Agri at Micheldever is excellent, too, with parts manager Kevin Hunt providing a much appreciated same-day delivery service. For Agco bits, the arrival of Crawfords in the area has been a very handy addition.
Dan: Another favourite is Land Rover specialist Keith Gott, whose parts staff have exceptional knowledge and are rarely stumped.
Favourite piece of kit?
Bob: Probably the Fendt 724. It’s our only tractor with auto steering and is also more comfortable than the 818 over a long day.
We bought the 724 three years ago with about 5,000 hours on the clock, on new 710 tyres and with some warranty remaining.
We paid £83,000 for it, and, given the way that prices have rocketed, it’s probably worth around £90,000-£95,000 today.
Dan: I love the JCB pivot-steer. It does literally everything, from hoisting an engine out of a Defender to loading grain into trucks and hauling 36 bales on our JPM low-loader. It’s now clocked 4,100 hours.
The seat bushes could do with sorting, and we regularly pack the tired centre pivot with grease. We’ll replace the pivot at some stage, but it’s a big job.
Least favourite piece of kit?
If we don’t like it, we get rid of it. The 27ft JPM low-loader is a prime example. I mucked up initially, thinking a 24ft-long model would comfortably accommodate three, three-bale packs along its bed.
When Morgan Machinery delivered the 24ft version, we discovered that the trailer wouldn’t take those nine bales, so, after a quick call, Morgan agreed to swap it for a 27ft model for a small premium plus the extra transport. We were seriously impressed with the service.
Latest purchase?
To match our 36m tramlines, we bought a 9.3m set of Cousins Contour rolls with 24in rings at Lamma 23, to replace a 20-year-old 8m set.
A chance conversation on the show stand revealed that Cousins had a shop-soiled set back at its base for £17,000, whereas the new equivalent would have been mid-20s.
We did the deal on the stand, and then sold our old 8m rolls on Facebook for £4,000.
Oldest machine still at work?
That’s definitely the 1955 Ferguson TEF 20. My father bought it for my 16th birthday as a project, and it’s still in use today, pretty much permanently coupled to a Hy-Crack log splitter.
The 1959 MF 65 was an eBay purchase and powers a 5ft Spearhead topper. It’s ideal for getting under low-hanging branches and cutting narrow tracks.
How long do you keep your machines?
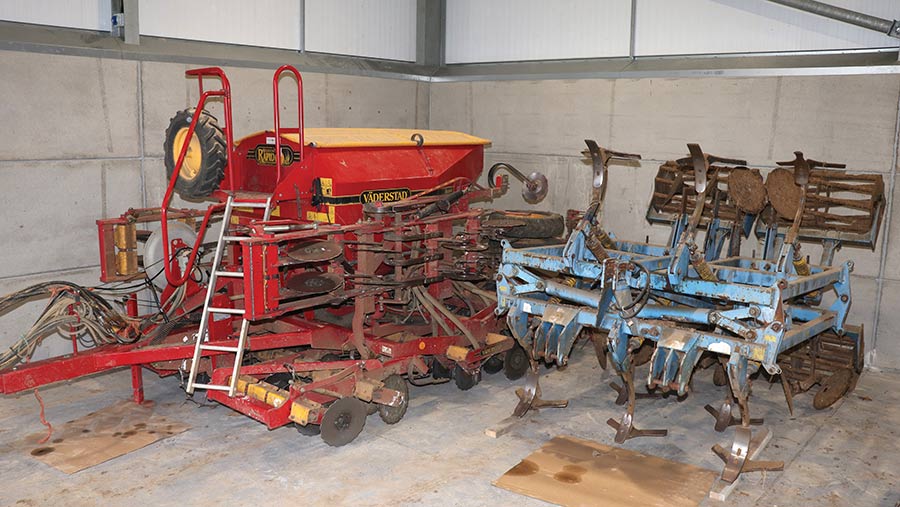
4m Vaderstad Rapid © Andrew Faulkner
As a rule, we buy to keep. For example, we’ve only had two drills since the late 1980s, and they’re still in use today: a 4m Vaderstad Rapid, with a 3m Accord/Maschio power harrow combination as back-up.
We’re always looking around at other second-hand options but are unlikely to be shelling out £150,000-plus on a 12m Horsch Avatar any time soon.
Next on your wish list?
It’s probably a drill. We’re in no rush, though. The ability to direct drill wheat into maize stubble – not this year, obviously – would be useful, so something like an older Horsch Sprinter with narrow points or perhaps even a mounted Triton front/rear combination might work.
Dan: A 4m low-disturbance subsoiler would be a welcome upgrade on our 3m Flatlift, which takes a lot of pulling and is only effective in a very small soil-condition window.
More likely is that I’ll build our own out of a 4m rigid Shakaerator frame and fit low-disturbance points. One of the advantages of a ring-fenced farm with wide gateways is we can run cheaper non-folding equipment.
Biggest machinery mistake?
Particularly memorable is overloading a silage trailer with muck that, when tipped, got jammed in the auto tailgate.
This meant the trailer wouldn’t lower, and, to cap it off, I managed to pop the tractor’s front tyre off its rim while trying to extricate the outfit. Not a good day… at all.
Dan: Growing peas may not classify as a machinery mistake, but I’m sure our old TX68 would disagree. It suffered all sorts of abuse when trying to lift a heavy crop off the deck a couple of years ago.
The peas yielded well at 4.5t/ha, but we won’t be growing them again in a hurry.
Most expensive repair bill?
More of a narrow escape. We were extremely concerned when the Fendt 818 started dumping its transmission into neutral.
The original diagnosis was that we’d need to fit a new Vario box at an overall cost of £14,000, but then a second opinion from Essex-based PHR put the fault down to a wiring issue.
We ended up just replacing the loom at £2,000-£3,000. Much relief all round.
Most expensive spare part?
Topper blades seem overpriced to us. We paid £1,600 for a used 3m Bomford rotary topper in decent condition, but it cost more than £600 to replace its six blades.
Best invention?
Simple and not really an invention: we do love our home-built personnel cage and big bag lifter. Even simpler are the half-moon extensions on either side of the grain bucket, which dramatically reduce the amount of spillages. There’s no need for excessive bucket shaking to level the contents, either.
What couldn’t you live without in the farm workshop?
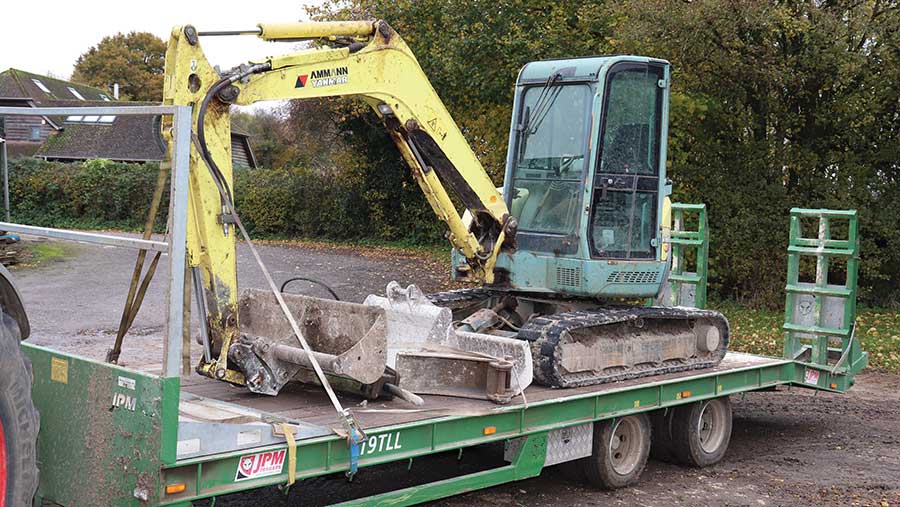
Yanmar digger © Andrew Faulkner
Several years ago we coughed at £600 for a bag of assorted Makita cordless tools, but it was money well spent. The air-powered grease bucket is great, too, especially when servicing the Yanmar digger.
Over-greasing is a potential downside on some kit – get heavy-handed and you’ll pop the caps off bearings.
Favourite and least favourite jobs?
I’ve got to an age where I try to avoid the tasks I don’t like – such as clamping silage. In contrast, clearing a field of big bales with the JCB and JPM low-loader is really satisfying.
One person can shift a lot of bales in a day. There’s a sense of achievement.
Dan: Much the same. I enjoy operating the TM, especially on bale hauling. A day on the Yanmar excavator is also great, although you need ear protectors. She’s not the quietest.
Combining peas ranks as my least favourite job, for the reasons already mentioned.
What’s your everyday farm transport?
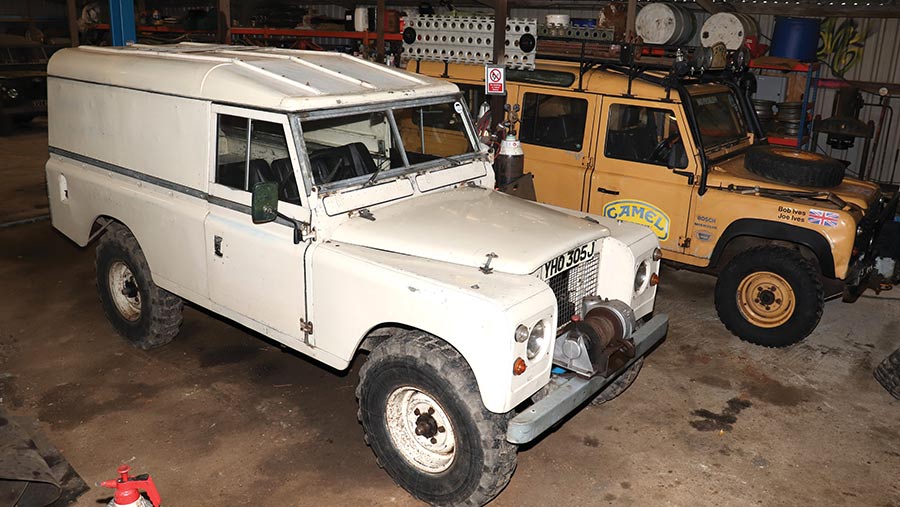
© Andrew Faulkner
Courtesy of Dan’s sideline, there’s a selection of older Defender and Discovery Tdi models to pick from, although the usual choice is a 27-year-old Disco.
For longer journeys I have a three-year-old, new-shape Defender 110, which I love. Despite it only having the already-discontinued four-cylinder diesel, you can do 400 miles in comfort, and it’ll return around 30mpg.
Dan: I tend to use the old Discovery. I’m also working on a 4.2-litre V8 Holden HQ 74 ute that I brought back from Australia in 2015, along with a Land Rover and an IBC full of tools.
Back then the 40ft container cost £3,000 to ship; today it would be about £9,000.
Best tractor you’ve had?
We’ve had some good ones, but top of the list is a 150hp MF 6480 Dyna-6. Over its 13,000 hours with us, it required just the one minor gearbox repair. That was it.
We only part-exchanged it for the 724 three years ago because we needed more power.
The 818 has been good, too. Just the previously mentioned wiring loom replacement in almost 10,000 hours.
Worst tractor you’ve had?
That would be an MF 6499 Dyna-6. Over its 10-year life with us, it cost about £25,000 in repairs and parts, largely down to transmission issues that were never fully resolved. We had several bills of £4,000-£5,000.
Biggest machinery bargain?
Daft as it may seem, it’s probably the Fendt 724. The peculiarities of the second-hand market through the Covid period mean the tractor is valued at about £10,000 more today than we paid for it in 2020.
And we’ve had 1,200 trouble-free hours out of it. A close second is the set of Cousins rolls.
Best and worst pieces of technology on a machine?
Open the new Defender’s door for a better view when reversing a trailer, and the vehicle slams on the brakes. Why?
Conversely, the best bit of tech is the Varioguide auto steering on the Fendt 724. I was sceptical at first. Not anymore.
In the shed
- Tractors Fendt 724 (2016), Fendt 818 (2004), MF 2720 (1984), MF 399 (1996), MF 65 (1959) and Ferguson TEF20 (1955)
- Combine New Holland TX68 Plus with 7.3m header
- Sprayers Spraying is carried out by local contractor Scribeland with a 36m trailed Horsch
- Telehandler JCB TM320 S pivot-steer
- Drills 4m Vaderstad Rapid, 3m Maschio/Accord power harrow/drill combi
- Cultivation kit 5m Lemken Heliodor disc/press, 3.8m Farmet cultivator, 3m Kockerling PC tine, 3m Spalding Flatlift, 9.3m Cousins Contour rolls (shared)
- Fertiliser spreader Amazone ZA-TS 4200 (36m) (shared)
- Other kit 5.5t Yanmar Vio 55 excavator, 16t Ktwo Roadeo trailer, 19t JPM low-loader, 3m Bomford topper