What’s in Your Shed? Diverse arable kit caters for niche crops
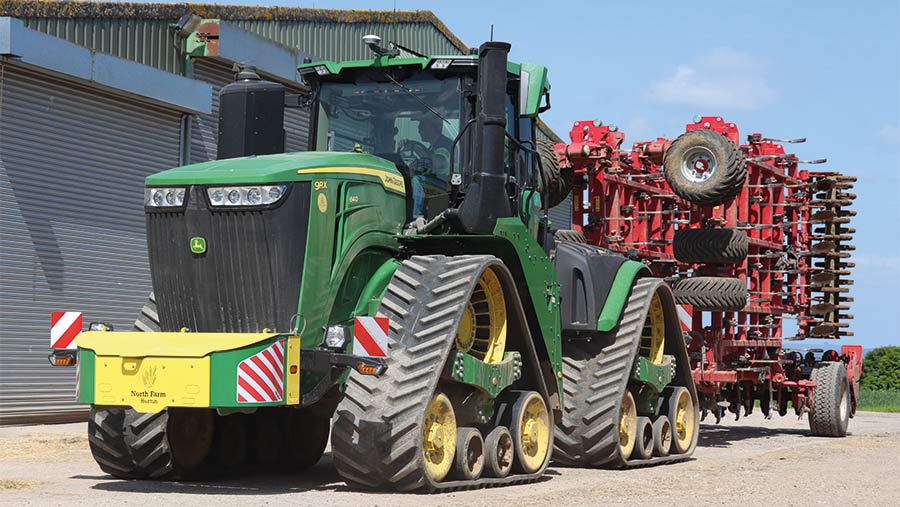
Dorset farmer Peter Snell takes Farmers Weekly on a tour of the machinery sheds at North Farm, Horton – the base of the family’s 1,422ha arable operation.
See also: Video: Driver’s view – Tom Hawthorne’s Big Bale Transtacker
How did you get started?
Peter: It’s almost a cliché, but farming really is all I’ve ever wanted to do.
After leaving Seale-Hayne Agricultural College in 2002, I did a bit of travelling – driving a combine in Australia, and milking cows and carrying out forestry work in New Zealand – before returning to the family farm to work full time in 2003.
At the time, we were milking about 300 Holsteins, but for various reasons we ended up selling the cows and milk quota in 2005 to focus on crop production on the farm’s 244ha of owned arable ground.
That area has since grown to 1,422ha through a combination of rental, contract-farming and stubble-to-stubble agreements, all within an eight-mile radius of our base at Horton.
We’re still looking to expand and would travel farther for the right opportunity.
Our point of difference is that, as well as conventional combinable crops, we specialise in the production of more niche crops, such as herbage seed, grain maize, marrowfat peas and sunflowers, to maximise overall arable profitability.
This also explains the diverse range of kit that we’re operating.
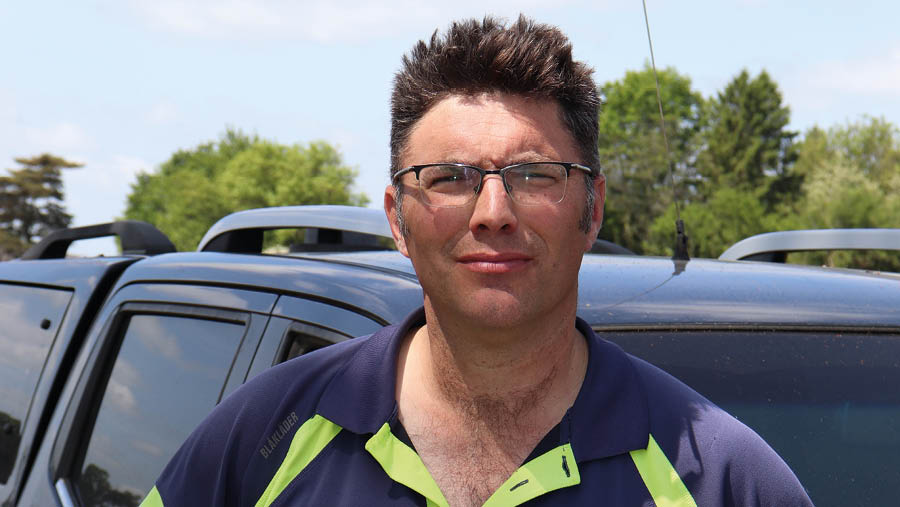
Peter Snell © Andrew Faulkner
Farm facts: North Farm, Horton, Dorset
- Farm size: 1,422ha of owned, contract-farmed, rented and stubble-to-stubble
- Cropping: Wheat, oilseed rape, spring barley, herbage seed, grain maize, marrowfat peas, sunflowers
- Soil type: From free-draining loam over chalk to heavier areas of clay
- Staff: Four full-time workers, seasonal casuals, plus Peter Snell and wife Tora
How brand loyal are you?
It’s more about the best machine for the job, based on performance, reliability and strong residuals.
That said, in recent times we’ve tended to buy Fendt and Deere tractors, Horsch cultivation kit, JCB telehandlers and New Holland combines.
However, we would look elsewhere. The current Fendt 828, for example, is on its third engine and due for change next year.
Though Fendt has stood by us over the 828’s engine issues, I’m beginning to question whether the brand’s premium price is justified.
We ran Claas combines for many years, but switched to New Holland in 2019 after an excellent demo of a CR10.90 during the previous harvest.
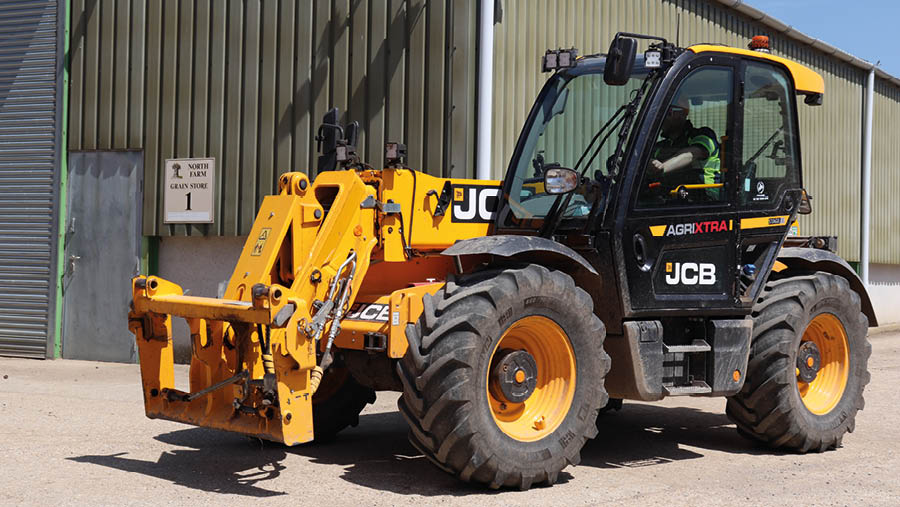
JCB 542-70 loadall © Andrew Faulkner
Favourite dealer?
In no particular order, our top three are Buglers at Wimborne (New Holland), Hunt Forest at Dorchester (John Deere) and Redlynch Agricultural at Milborne St Andrew (Fendt).
Bugler has been exceptional on combines, and, when it came to buying the two current CRs, they and New Holland were by far the most flexible on us fitting third-party headers from the likes of MacDon and Geringhoff.
And they also offered a seven-year warranty.
Of the smaller dealers/engineers, we use AR Diesels to look after the MAN truck and trailers.
Scott Mowlem services the 14t Volvo digger, and Arjay Contracts has carried out a number of bespoke fabrication projects, such as a maize slitter and wheel extenders for the Fendt 724.
Favourite piece of kit?
Probably the CR combines for their versatility and output. With our diverse spread of crops, we’re operating them for at least four months of the year, so they’re worked hard and often in tough conditions.
I like the CR’s ease of access for clearing blockages and have also been impressed by its track performance when harvesting grain maize late in the season.
Least favourite piece of kit?
A Roc front-mounted merger, which we used for turning straw behind our previous Lexion 780 combine.
To be fair, it wasn’t the machine’s fault – it simply couldn’t handle the quantity of material from the 13.8m header. Not my best purchase.
Latest purchase?
The 12m Dalbo Maxiroll Cambridge rollers with levelling boards and an Avadex spreader.
We’ve also got a 12m Horsch Serto disc drill due to arrive in October, even though it was ordered back in September 2022 – not ideal, but Horsch has agreed to lend us a machine this autumn if ours is delayed again.
Going ahead, the plan will be to work the ground with the Joker discs and/or Cruiser cultivator, spray off and then drill with the Serto.
Behind the grain maize, we’ll continue to plough. We like the concept of no-till but not the slugs, and growing herbage seed means we can’t afford to get a problem with grass weeds.
In the shed
- Tractors: John Deere 9RX 640 and 6610; Fendt 943 Vario MT, 828 and 724
- Combines: New Holland CR10.90 (x2) with selection of headers – 12.5m MacDon draper (x2), 16-row Geringhoff maize header, 7.3m Shelbourne Reynolds stripper, MacDon PW8 pick-up header
- Sprayer: Agrifac Condor self-propelled (36m/5,000-litre)
- Telehandlers: JCB Loadall 542-70 and 550-80
- Drills: 12m Horsch Serto, 12m Horsch Sprinter, 6m Kuhn power harrow/drill combi
- Cultivators: 12m Horsch Cruiser 12XL (tine), 12m Horsch Joker 12RT (disc), Dalbo Maxiroll rolls (12m), 6m Cousins V-Form subsoiler
- Fertiliser spreader: Kuhn AGT trailed pneumatic spreader (36m)
- Other kit: MAN 4×4 tractor unit and trailers/bowsers, 14t Volvo excavator, Perard Interbenne 27cu m chaser bin, and selection of tedding/raking kit for grass seed hay

4×4 tractor unit © Andrew Faulkner
Oldest machine still at work?
By some margin, that’s the 1950s Foster threshing machine, which we still run through the winter to process 16ha of thatching straw. We feed sheaves in and get combed straw out.
The thresher is reliable-ish, and we can generally fix most things on it ourselves. The knotters are increasingly temperamental, and we’re gradually replacing bits of the woodwork.
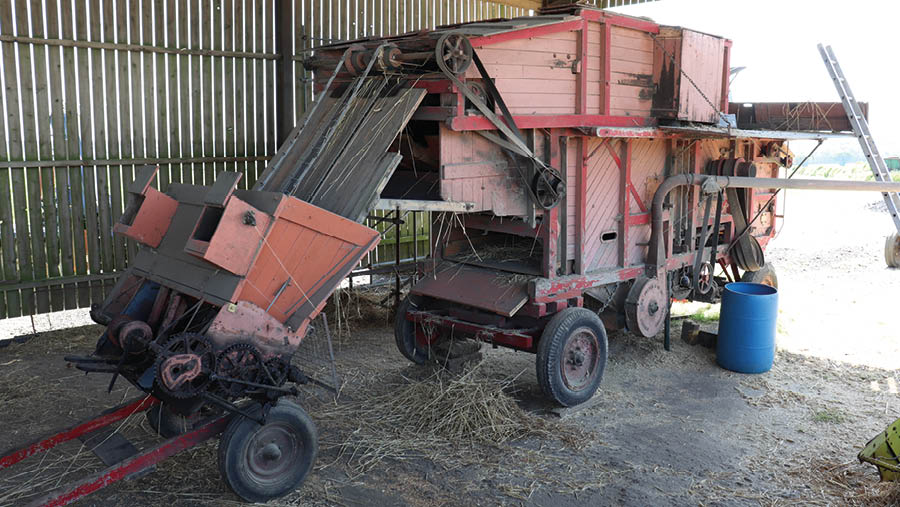
1950s Foster threshing machine © Andrew Faulkner
How long do you keep your machines?
There’s no hard and fast policy. The tractors are typically kept for seven to eight years, and the combines are similar at seven years.
Our tractors don’t clock huge annual hours – 750-1,000 for the crawlers, 1,000-1,200 for the wheeled units – and we look after them, so they’re still worth good money at resale time.
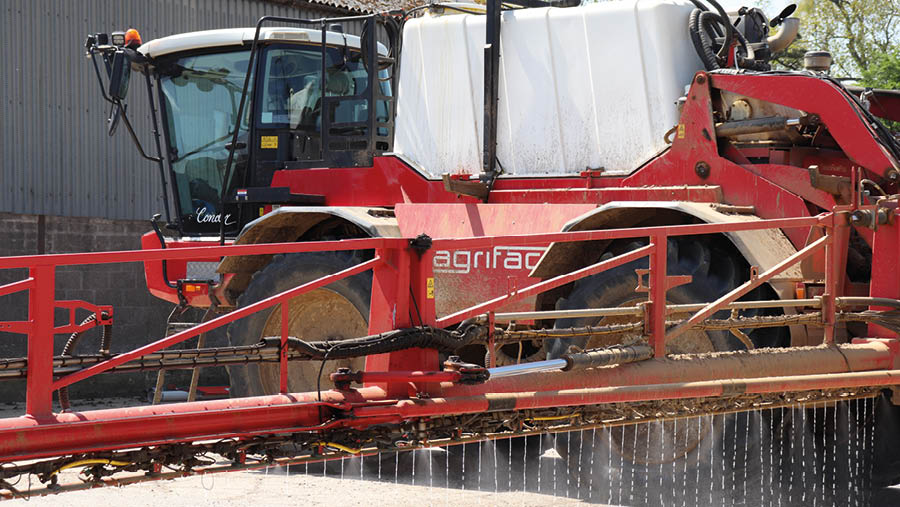
Agrifac Condor 4 © Andrew Faulkner
Next on your wish list?
A slightly unusual request, perhaps, but we’d like some Y-droppers for the Agrifac sprayer. They hang on the boom and are an effective way of applying late-season nitrogen through June and July, when the plant needs it most.
Currently, all the N is applied in the seed-bed in April/May, to avoid the risk of leaf scorch from later blanket applications.
Also, a new threshing machine would be nice. That’s a pipe dream, though.
Biggest machinery mistake?
Not too common an occurrence, but very frustrating when it does, is getting the combines stuck when harvesting grain maize late in a wet year.
It’s tempting to grab the last bit of crop in a boggy corner, yet we generally regret it when we try. In the past, we’ve had both crawlers hitched up to a bogged combine to extract it – a potentially costly job if tackled in the wrong way.
Most expensive repair bill?
All repairs seem to be eye-wateringly expensive. Particularly frustrating are NOx- and AdBlue-related issues, which, in my view, aren’t necessary.
All of this emission tech is choking modern diesel engines that are already efficient, and we’re burning even more diesel to clean the DPF filters.
We recently had a £5,000-£6,000 bill on the Fendt MT to replace a faulty emissions sensor, and most of the cost was in the time to remove one of the tracks to get at the part.
Fortunately, the 9RX, CR combines and sprayer are all covered under service/warranty agreements.
Most expensive spare part?
All wearing metal is increasingly expensive, and component prices for main-brand tractors are getting scary, too.
Best invention?
Admittedly simple, but the clamshell presses for tying up bundles of thatching straw are especially useful.
And one of several Arjay Contracts modfications on the farm is a bucket for bagging up grain maize into 0.5t dumpies.
These bags are then sold to local shoots for pheasant feed.
What couldn’t you live without in the farm workshop?
Cordless impact guns make such a difference when changing wearing metal, and we also find regular use for our 100t hydraulic press.
When all else fails, it’s handy to have access to a decent selection of hammers.
Favourite and least favourite jobs?
Managing the operation and sorting logistics are rewarding, but only when the job’s going to plan. I also miss combining – again, when the harvester is running smoothly – because you’re there to witness the culmination of nine months’ work.
Grain store cleaning is definitely at the bottom of my favourites list.
What’s your everyday farm transport?
A 66-plate Nissan Navara doublecab. I tend to buy trucks new and keep them for about 10 years, clocking about 150,000 miles over that time.
This is my second Navara, and they’ve both been good – albeit we had to do a bit of chassis welding on the first one.
Next time, I guess I’ll end up in a Ford Ranger or Hilux, as the new pickup options are now pretty limited.
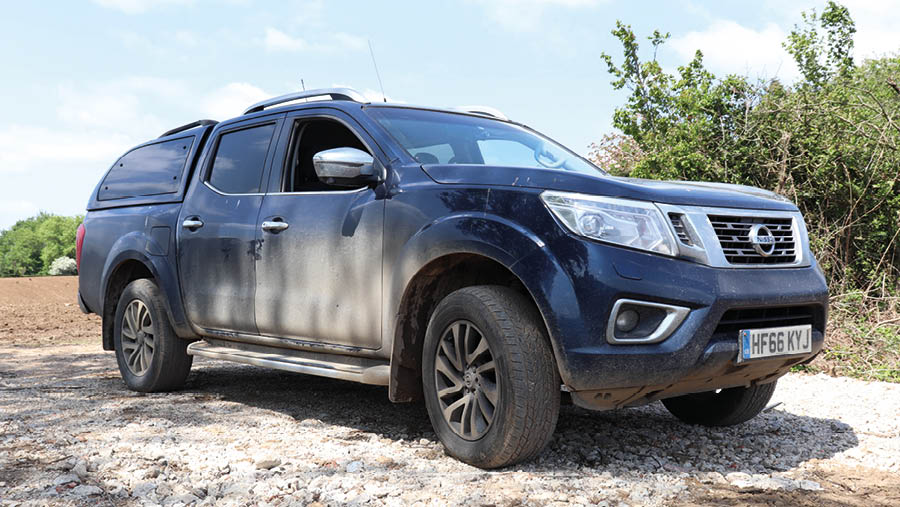
Nissan Navara © Andrew Faulkner
Best tractor you’ve had?
I loved our Claas Challenger 95E; it was so simple – almost built to be rebuilt.
We bought it at 12 years old in 2012 for £45,500, kept it for four years and then sold it for £27,500 to become a lifeboat tug in the Netherlands.
The W-plate John Deere 6610 is also a farm favourite. It’s been with us from new and has now clocked up about 12,000 hours.
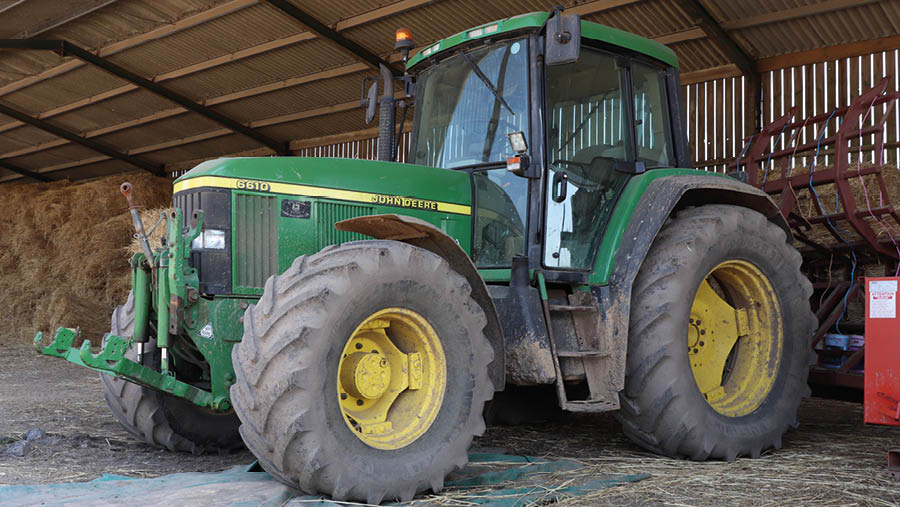
Bought from new, the W-plate John Deere 6610’s role is now more yard than field tractor © Andrew Faulkner
Worst tractor you’ve had?
Even though the operators like them, the current Fendt 828 and its 828 predecessor would be among the worst for reliability.
As mentioned earlier, to Fendt’s credit it recognises there’s a problem with the 828 engine and has stood by us over both tractors.
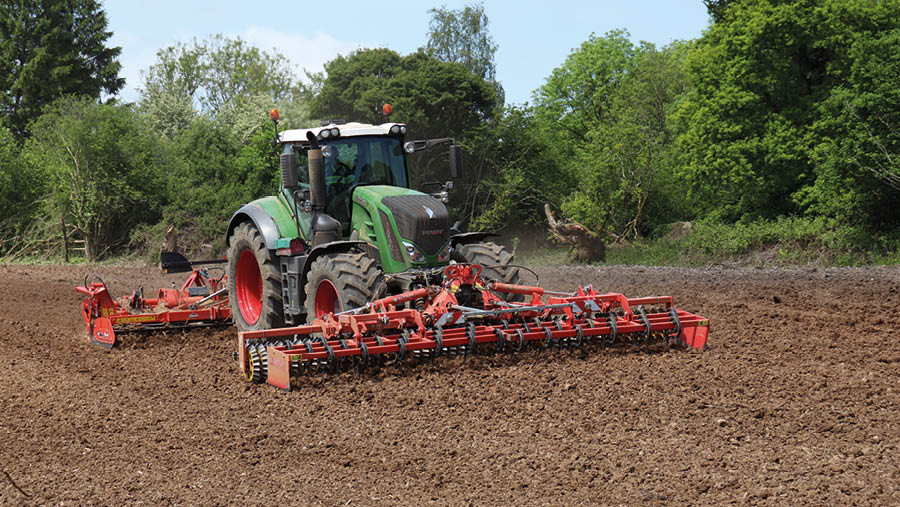
Fendt 828 © Andrew Faulkner
Biggest machinery bargain?
Along with the JD 6610, the 12m Simba rolls would have to be right up there. We paid £8,500 for them second-hand back in 2007, and 16 years on they’re still worth more than £6,000.
They’re now only called on largely as a backup to the new Dalbo Maxiroll.
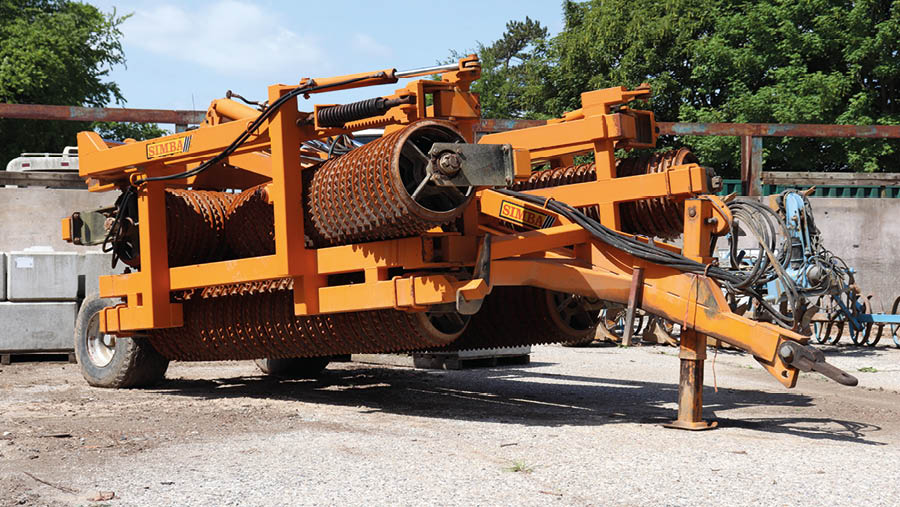
12m Simba rolls © Andrew Faulkner
Best and worst pieces of technology on a machine?
Top of my hate list is much of the emissions cleaning technology, which in some cases causes more problems than it solves.
The best is auto-steer, when it’s working. Our base station has some blackspots, so we’re looking at investing in a mobile unit.