Video: Revolutionary driverless Robotti sets to work on UK soils
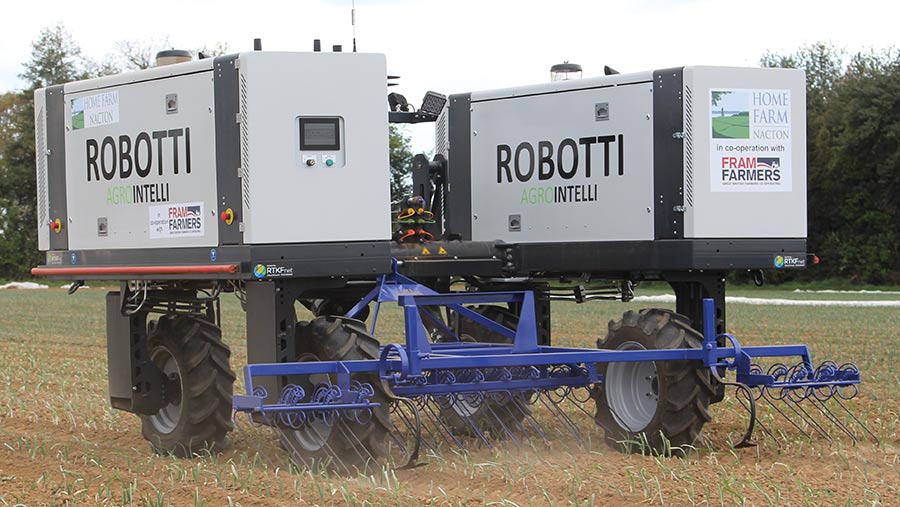
A large Suffolk vegetable grower is the first UK owner of a novel Danish autonomous tractor, having been convinced of its potential to save labour and increase output when weeding vegetable beds.
Home Farm Nacton, on the outskirts of Ipswich, took delivery of Agrointelli’s £150,000 Robotti in early April, and after a few weeks in the workshop, it has been set to work hoeing fields of leeks.
See also:Â Video: Autonomous tractor set to revolutionise field work in Canada
For most British farmers, the fabled transition from high-output machines that currently work the land to swarms of little robots zapping weeds as soon as they emerge remains on the periphery of reality, with little evidence of the systems being used in earnest on a large scale.Â
However, the Robotti concept shares many similarities with the sought-after Dot platform originally developed by Canadian firm Seedmaster, and subsequently sold to American GPS giant Raven.
Commercial versions of the U-shaped machine are already successfully working on drilling, spraying and spreading tasks in North America, where there is a chronic shortage of labour.
The team at Agrointelli says it is prioritising European organic growers who work on arrow-straight veg beds. While this is a niche market, it is expected to be a stepping stone to broader-scale arable crops.
The company has good reason to be confident, too, as 15 of them are already working across Europe and a total of 50 are scheduled to be on farms by the end of the year.
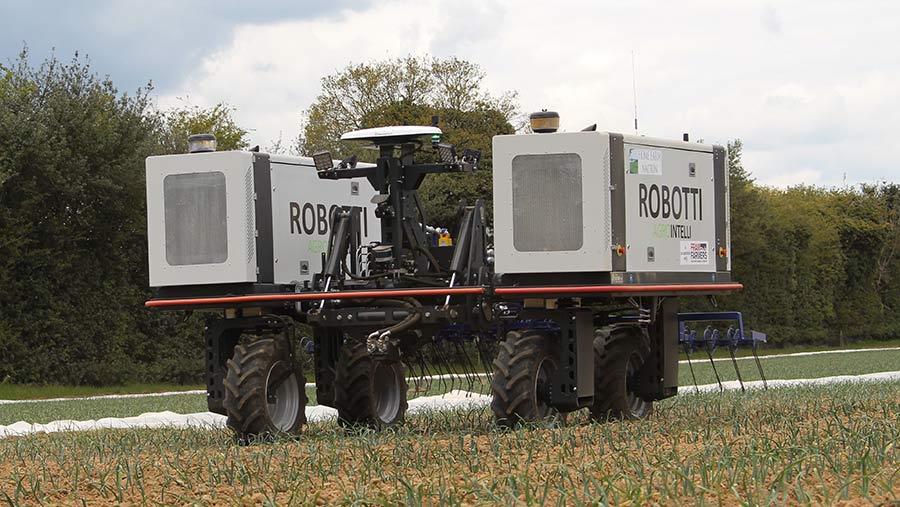
The Robotti has been put to work hoeing leeks at Home Farm Nacton in Suffolk © MAG/Edward Mowbray
Familiar components
The driverless machine isn’t an entirely alien development, and there are plenty of similarities with conventional tractors. For starters, it has a pair of orthodox diesel engines and a three-point linkage, as well as pto and hydraulic outputs to run regular farm implements.
The three-cylinder, 75hp Kubota engines sit on opposite sides of the frame, but instead of powering the functions in equal measure, one is dedicated to propelling the Robotti while the other takes care of the pto and hydraulic demand.
For tillage work, it’s effectively a 75hp tractor, as both engines can’t be used to share the workload on the same task. So on less power-hungry hoeing duties, only one of the blocks will be worked anywhere near hard.
The upshot is relatively low fuel consumption, with Agrointelli suggesting a thirst of just 3-6 litres/hour at a forward speed of 5kph, which can be maintained 24 hours/day.
By opting for regular diesel and hydraulic systems, servicing and maintenance can be completed locally without the involvement of a specialist and the risk of having to wait for parts to be shipped in from abroad.
A three-point linkage is the sole means of attaching implements and it is mounted at the front of the machine for better weight distribution. It is fixed in position, so there is no chance of it drifting into the crop during work.
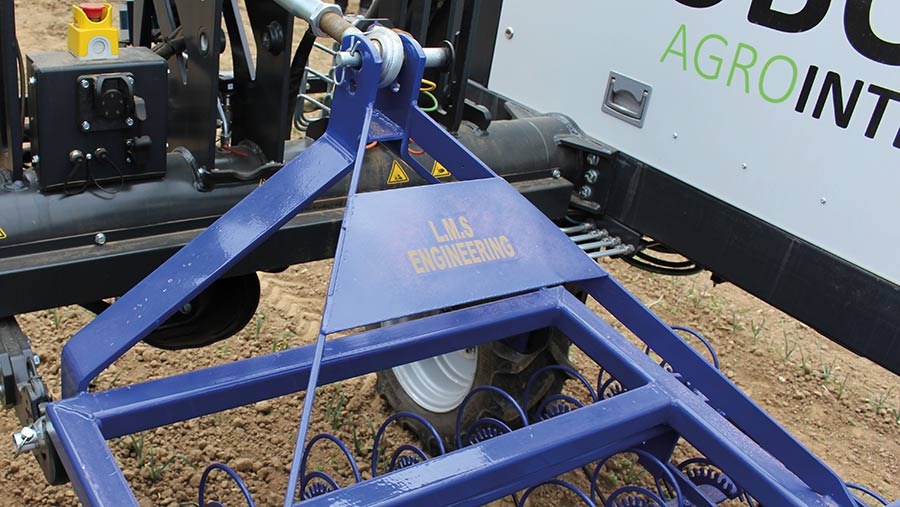
Modified equipment is mounted on a three-point linkage © MAG/Edward Mowbray
Only the front set of wheels turn and each has its own hydraulic motor, with encoders governing speed and directional changes.
Operator’s view
Andrew Williams, farm director at the 1,940ha Home Farm Nacton
We had been talking for some time about getting into robotics – it will reduce the amount of hand weeding we have to do later in the season and, as it is getting harder to source labour, this will be taking on the jobs that no one wants to do.
We started talking to Agrointelli in November, placed an order in December and took delivery in early April. It is purely a weeding tool, but we would like to adapt a single-bed onion drill next spring and, in time, purchase a spot sprayer to reduce chemical use. We’ve already spent quite a bit of time in the workshop tweaking implements to make sure they work effectively.
I’m still apprehensive about leaving it for 24 hours/day, though. If it is hoeing and a tine rattles loose at 11pm and takes out a row on every pass until someone checks it at 6am, it could be very costly. We’re working on a solution, possibly by fitting extra locking collars on the tines.
We will have to be more disciplined about using GPS for Robotti to work effectively, and mapping the whole farm on the Agrointelli system seems to be the way forward.
Defining boundaries
One of the biggest differences with a cabbed tractor is the setup procedure required before the Robotti enters the field. This takes place on Agrointelli’s online platform and starts with a shapefile of the mapped field – ideally one that has been created specifically for the job. It is possible to import existing files, but this can lead to reduced accuracy, the company warns.
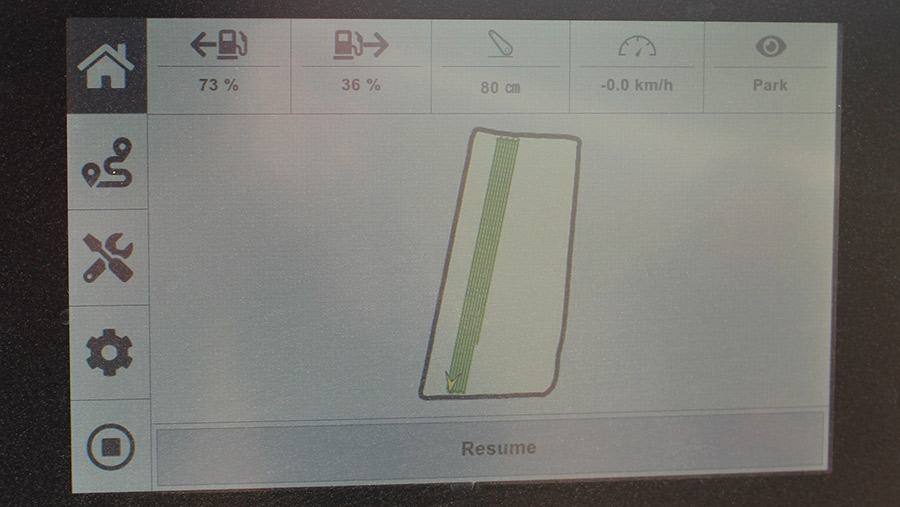
The Robotti uses accurate guidance maps © MAG/Edward Mowbray
The system needs information about the task being performed, implement used, working width and whether the pto is to be activated. Headland turn details are also required to keep it following the desired path.
RTK guidance is sent via the internet to a 4G modem on the tractor, which has a SIM card that can connect to whichever network has the strongest signal.
Growers can then choose the Robotti’s route through the field, either working down every bed or missing alternate rows to increase the ease and speed of headland turns. This plan is saved to the cloud and downloaded by the “operator” when in the field.
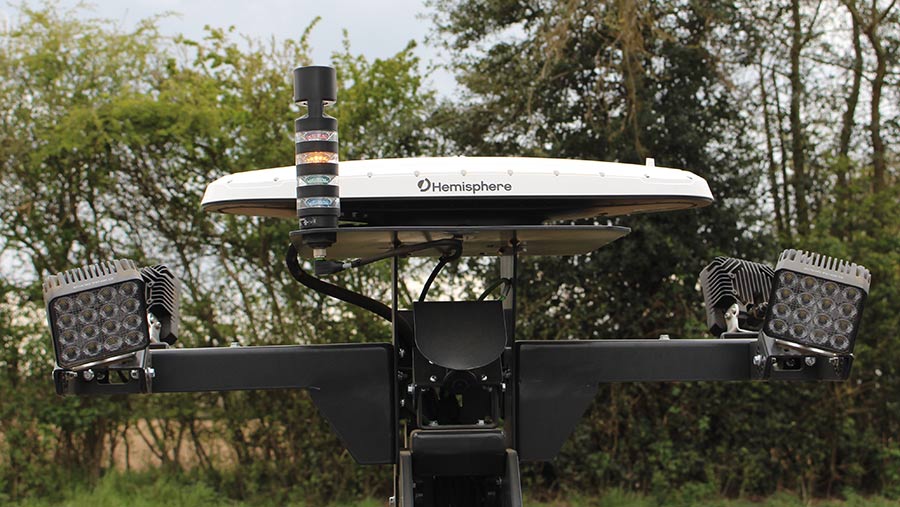
RTK guidance keeps the machine running arrow-straight on veg beds © MAG/Edward Mowbray
Safety
As with any autonomous machine, there are more safety and emergency shut-down features than you can shake a stick at. It will come to an immediate stop should the red barrier around the front and sides come into contact with an object, and there are also various rapid stop buttons.
A Lidar (light detection and ranging) scanner surveys the immediate area in the direction of travel by sending light pulses that determine the proximity of any obstacles. If anything gets too close, the vehicle will come to a halt. Â
Front and rear cameras link to Agrointelli’s website so the operator can view the robot’s exact location and field progress, and there are also red, orange and green indicators on top of the machine that give owners a quick visual indication whether everything is OK.
The Robotti is CE marked and Home Farm Nacton says this has helped the National Farmers Union secure an insurance policy to cover it when working autonomously. These are virgin waters – not only for farmers, but agricultural insurers, too. Â
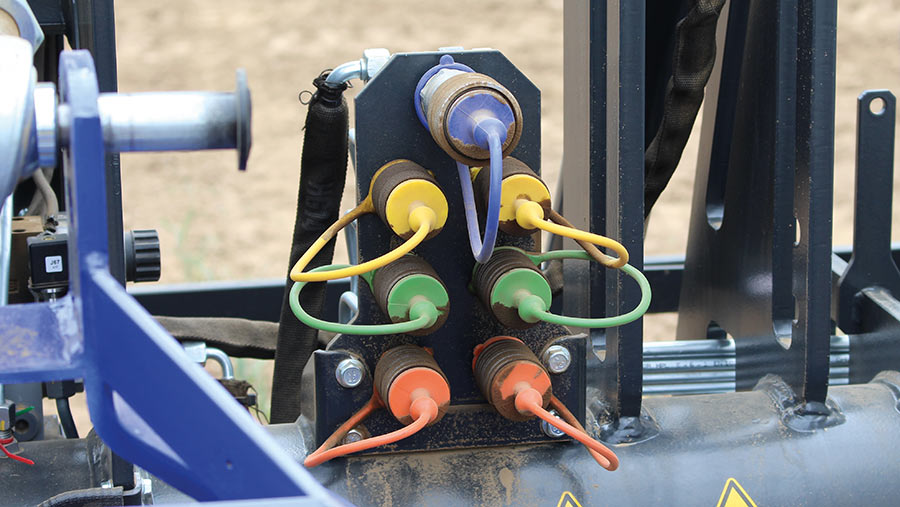
Standard hydraulic couplings simplify the process of attaching implements © MAG/Edward Mowbray
However, one catch is that it is 3m wide and needs transporting between fields. Frustratingly, it weighs 3,000kg, so is too heavy for a pickup and trailer combination. It is also limited to a 5kph top speed due to UK safety regulations, but is actually capable of 8kph.
The UK importer, Warwickshire-based Autonomous Agri Solutions, is working hard to iron out the inevitable teething issues with bringing such a novel machine into the country.
What is Agrointelli?
The Robotti project has been in existence since the early 2000s, when it started as a research collaboration between several universities. In 2010, it was taken on by Danish manufacturer Kongskilde, which kept the project until 2015, when a breakaway company – Agrointelli – was formed by a number of ex-Kongskilde employees.
This is when the Robotti project gathered pace. Roughly 30 prototypes were trialled, starting with a 25hp unit, moving up to 50hp and then to the 150hp, twin-engine setup that is commercially available today.