VIDEO: Forklift designed for poultry producers
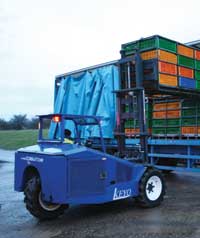
Irish specialist forklift manufacturer Combilift is launching a new machine which has been specifically designed to meet the needs of the poultry sector.
“Until now the majority of forklifts used for handling live poultry have been modified versions of mainstream models, such as counterbalance or truck-mounted vehicles,” said Combilift managing director Martin McVicar.
“But after taking the exact requirements of catching, handling and transportation into account, we have developed a purpose-built machine which makes the whole process speedier, quieter and more streamlined.”
The Combi-RT includes a clear view, three-stage mast with full free lift. Its low profile allows it to work under the low level eaves inside the poultry house, while the large diameter tyres, with differential lock and 300mm (12inch) ground clearance, enable the machine to operate smoothly in all manner of litter conditions.
These features, together with a small turning radius, contribute to reduced disturbance of litter, which is also advantageous when thinning. Its smooth controls of both drive and mast functions results in gentler handling of the full modules, contributing to lower stress levels.
Development of the new machine was based in part on feedback from Keyo Agricultural Services, one of the UK’s largest providers to the poultry processing sector. Keyo director Mark van den Bos said the machine offered a high level of operator comfort in a typically harsh environment.
“Drivers spend long periods in the cab and the Combi RT’s deep suspension seat is very beneficial to their comfort and reduces fatigue for enhanced health and safety. The offset driving position and excellent visibility through the mast also affords a good view of the modules and enables them to be easily slotted into place on the trailer.
“This is a tough application where feathers and dust can easily get into vehicle parts,” he adds. “The Combi-RT has been engineered to minimise these risks – the radiator and oil coolers are fully sealed, as is the rear wheel arch which prevents dirt build up in the chassis. The hydrostatic drive means that there are no mechanical brakes to adjust or repair, and access to components for servicing is very straightforward, keeping maintenance costs down.”