Vervaet debuts rollerbed on Beet Eater 625 harvester
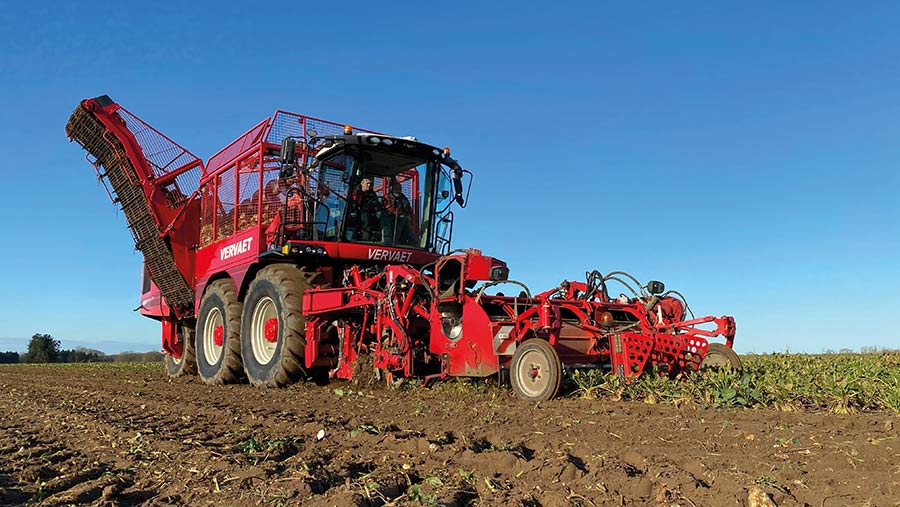
Sugar beet harvesting aficionados finally got a glimpse of Vervaet’s new rollerbed cleaning system, after the latest Beet Eater 625 Evo made its working debut at the annual demonstration day held by sole UK importer J Riley.
The addition of a roller option, as an alternative to the Dutch firm’s traditional turbines, was revealed last spring, and the first two units on British shores have been put to task this season.
In doing so, the company claims to be the only sugar beet harvester maker to offer both primary cleaning methods.
See also: Tips for buying a second-hand self-propelled beet harvester
This, it says, will help broaden appeal to existing Holmer, Ropa and Grimme owners, particularly on the Continent, where the system remains enduringly popular among those harvesting on light, sandy land.
Vervaet Beet Eater 625 Evo
Engine 15.6-litre Mercedes six-cylinder
Power 653hp
Transmission Hydrostatic
Top speed 40kph
Turning circle 8.5m
Bunker capacity 25t
Discharge time 50secs
Discharge height 2.5-4m
However, it is currently only available on the high-output 625 Evo and isn’t expected to be rolled out to the more popular and lighter-weight Q-series machines until next year. These models outsell the Beet Eater in the UK at a rate of roughly three to one.
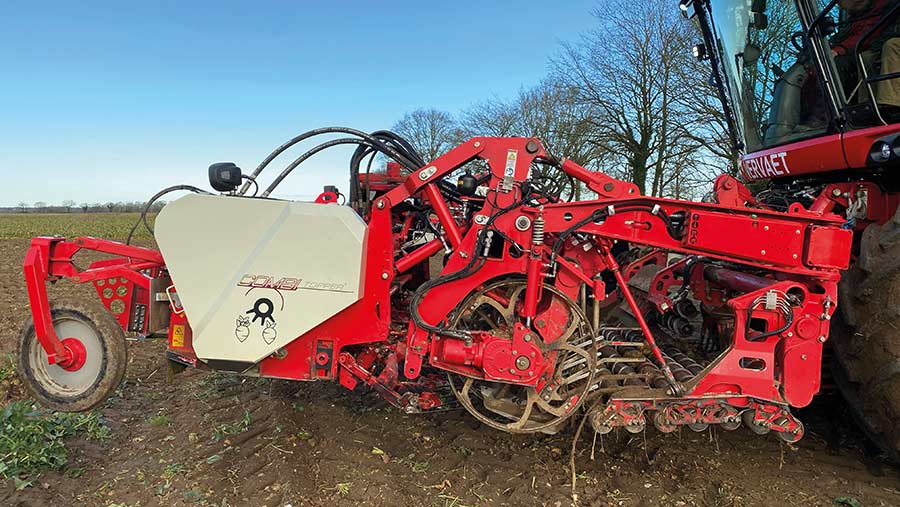
© MAG/Oliver Mark
Design change
The front end of the machine remains unchanged, with the same topper options, scalpers and lifting shares as before.
But once plucked from terra firma, the beet is placed on a bed of seven full-width rollers. These replace the standard twin front turbines to simultaneously clean and move the beet through the machine.
The middle five rollers carry smooth spiral augers – the first two pushing the crop outwards and the last three arranged to tease it back towards the centre. Shorter rollers either side of the throat form a back wall that also helps corral the crop towards a cleaning turbine mounted between the wheels.
The advantage of this system, says Vervaet, is that it offers the potential of marginally quicker forward speeds in forgiving conditions and is also gentler on the beet, without the operator having to go through the rigmarole of changing pigtail tines and rail gates as they would with turbines.
Instead, roller speed can be varied from the cab to suit different conditions. The first six of them are controlled as one group, with the seventh able to spin in reverse to provide a more aggressive final clean of the crop.
From the rollers, there’s a series of six turbines running front to back in the bowels of the Beet Eater. These provide plenty of cleaning capacity ahead of the ring trace, the company says – particularly as their speeds can be altered.
This means there’s no transfer web and all the potential trouble that it can bring – jamming in claggy clay soil, reducing ground clearance and periodic breakdowns.
The rest of the machine is as before, with the 2018-launched Evo version running a 15.6-litre Mercedes engine tuned to 653hp. Bunker capacity on the 625 is 25t.
In terms of demand, Vervaet expects turbine cleaners to account for roughly 70% of UK sales. Volatile exchange rates mean prices are currently pretty variable, but a rollerbed carries a premium of roughly £15,000 over an equivalent turbine machine.
Driver’s view – Robert Wright
The first rollerbed Beet Eater to land on UK soil went to contractor Robert Wright, based near Holt, north Norfolk, who harvests 1,400ha annually.
Having run 11 different Vervaet self-propelleds since the late 1990s, he was well positioned to assess the merits of the latest 625 Evo.
“I’ve always loved the performance of the six-wheel drive Beet Eaters,” says Mr Wright. “They might drink more fuel than the Q-series – usually a bit below 30 litres/ha – but the upshot is that they always have the power. It’s a real Rolls-Royce of beet harvesters.”
There were several reasons why he wanted to switch to a rollerbed cleaning system, most of which were based on ease of use.
“I like having the shares in one row – they’re staggered on the turbine version – because it feeds the crop more smoothly and it flows tidily through the machine.”
“The whole lot is more open, which makes it much easier to see what’s going on from the cab. And I also think I’m getting a bit more root into the bunker because the ends of the tap roots don’t seem to snap off as frequently.”
However, there are some downsides, including running costs, which are expected to be higher.
“The spirals on the rollers will wear, but how quickly depends entirely on the conditions. Based on my experience so far, I expect them to last about a season and a half.”
According to Mr Wright, there has also been no impact on travel speed in switching to the rollerbed.
“It’s ease of use, rather than overall output, that justifies the cost. Over the course of a season that counts for a lot,” he says.
Telematics offers view from afar
Vervaet has launched a new Connect telematics system in the UK, allowing owners to view various performance stats from a smartphone or computer.
The system has been developed in-house and will be fitted, in its most basic form, to all machines as standard.
This means that performance and operating data can be transmitted to an online MyVervaet portal, allowing those granted access to monitor machine location, working speed, engine power usage, fuel consumption and hectares worked.
It is also possible to see a live feed from the in-cab screen and, with the necessary permissions, make changes to machine settings.
On sugar beet harvesters, there’s the option of including yield mapping as part of the telematics service, while on slurry applicators owners can view application maps and total volume applied.
The Connect system also allows dealers to access error code alerts and service records, allowing for remote diagnostics and quicker wireless software updates.