Unusual harvesters: lettuce-cutting rig
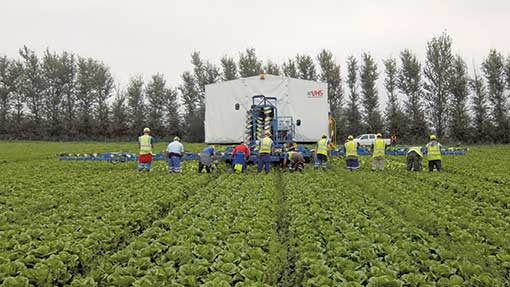
In the second of our series on unusual harvesting kit, Nick Wigdahl visited G’s Group fresh lettuce operation at Wissington, Cambridgeshire.
Ever wondered exactly how those identically-shaped lettuces get from the field to the supermarket shelf so quickly? The answer is that it takes a lot of manpower, organisation and sheer effort, not to mention some unusual machinery.
Planting is almost a continuous activity to allow harvesting to start in May and finish at the end of October. The black fen soil is ploughed, power harrowed, rolled and planted. The G’s group also grows in Spain, so is able to supply lettuces all year round.
There’s a difference between fresh and processed lettuces, too. Fresh lettuces are cut and packed in the field using a gantry up to 14m wide on to which the cutters – men and women –place the lettuce.
On the other hand, some lettuces are processed off the field, usually for washed packs or to fast food outlets.
JCB running gear
Spalding-based Vegetable Harvesting Systems is one of the leading manufacturers of rigs. Built to order, they are based on a JCB running gear and use a 120hp engine.
Four wheel drive and four wheel steering are standard but any similarity to the company’s Fastrac ends there – a reduction gearbox cuts forward speed to just 60m/ hour.
Double flotation tyres all round keep the rig moving in the soft fenland soil. Meanwhile, a generator bolted underneath the rig supplies power to the processing machinery.
How does it work?
The aim – not surprisingly – is to keep the lettuces off the floor and out of the dirt. The cutters cut the lettuces, strip off the outer leaves and place them on a cup conveyor on the gantry.
Lettuces move up into the packing area where they are transferred by hand to what’s called a flow wrapper. This packs the lettuces into cellophane packaging and applies all the necessary labels, including price.
At the rear, another team put the wrapped heads into boxes, make up the boxes from flat-packs, put them into pallets and transfer the pallets to the attached trailer.
A tractor reverses up to the rig and takes the trailer back to the cold store. The time it takes from cutting the lettuce to getting it into the cold-store mustn’t exceed two hours.
A typical rig will have a crew of around 23 people including the quality supervisor. There is no further processing once the lettuces leave the field, save for a period of storage in a cold store. The base price of this rig was £250,000. Add in two flow wrappers, the generator and a trailer and you won’t get much change out of £420,000.
Health and safety rules
Although the rigs may be working in the middle of muddy fields, the same regulations apply as if the workers were a static processing plant on an industrial estate.
The field manager checks the machine over in the morning including all stop-start buttons and the level of cleanliness. Meanwhile, the workers have their hands checked for rashes.
Watches and loose jewellery are not permitted and the workers have to use a hand- wash before entering the rig. Each worker’s hand knife is numbered and the knives are checked in and out at the start and finish of each session, including rest breaks.
The reason? The spectre of a knife finding its way into a packet of lettuce doesn’t bear thinking about when Tesco is your main customer.
Speed and output are king
Output on these machines is prodigious. The lettuce-packing units handle between 60 and 90 heads a minute and there are two on the rig. The packed heads are put into boxes of 10 and stacked 70 to a pallet. The trailers carry 16 pallets at a time so overall production is 50,000 to 70,000 heads per ten-hour day.
During the summer months the company can be supplying more than two million lettuces a week to its customers and that is just one variety.
Rigs are getting bigger, too, this one accommodating 12 cutters rather than the previous eight. But they still have to meet EU road regs of 3m wide, 12m long and 5m high. The rig’s outer wings fold on this new version and the flow-wrappers do not have to be unbolted.
The latest rigs also allow lettuces to be weighed and price labels printed on the rig rather than being supplied at a fixed price.
Why not automate?
Lettuce harvesting is one of the few harvest operations still carried out by hand, notwithstanding the impressive technology that takes over once the lettuce is on the conveyor.
Andy Wilson, sales director of VHS, points out that it is very difficult to replicate the hand-eye co-ordination of a skilled worker. It is not so much the actual cutting of the stem but the fact that the outer leaves need to be stripped and discarded.
Experienced cutters can even cut out the heart of a romaine lettuce as it stands so that a casual observer might think that the field had not actually been harvested.
The Human Factor
The slightly exotic tang of Eastern European music floats out over the fenland mist from the radio on the rig. Most of the workforce is from Bulgaria and Romania and they are seen as a valuable resource; many are in their fifth or sixth year.
Three-quarters return each year which means that experience is built up and productivity maintained. Our host for the visit was Artur Dworzansk from Poland. He started as a cutter seven years previously and worked his way through field manager to production manager.
His main problem? “When there is a dispute about Romanian or Bulgarian music, I switch it to Radio One”.