Umbilical slurry spreading kit earns its keep for contractor
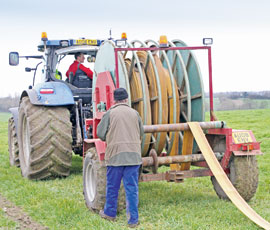
Why pull it when you can pump it, says one Suffolk contractor who specialises in providing an umbilical slurry spreading service. Andy Collings reports.
Richard Mortimer of A&M Contracting is a busy man. He uses his umbilical spreading gear to spread upwards of 60,000 cu m of slurry each year – and the likelihood is that this figure will increase in years to come.
He is based at Metfield, Suffolk, an area of the country that has a lot of pig herds as well as some large dairy units. Most of his customers are within a 15 mile radius.
“This is predominantly an Nitrate Vulnerable Zone, so the timing of the emptying of lagoons and stores is important bearing in mind the restrictions on applications,” he says. “I should think that 70% of the slurry we spread is from pigs and the remainder from cows.”
While the investment in umbilical spreading equipment is not quite as big as buying a large-capacity tanker and spreading unit, it can still be pretty steep when the cost of pumps, pipes, and spreader are taken into account.
Investment
One of the largest investments is the purchase of the 10cm-diameter pipe which can cost up to £10/m – and Mr Mortimer has 1,800m of it.
“Much of the ground we work on tends to be flinty and this can soon cause damage as the pipe is dragged along the ground,” he says. “We are always making repairs to them and I would think three years of use will see them having to be replaced.”
The business operates two home-made pumps, one of which is used as a spare should there be a problem. Both are powered by 210hp Cummins diesel engines and use Doda pumps which have outputs, depending on how far it has to pump, of up to 135,000 litres/hour. Operating pressure is 7-10bar.
At the business end is a SlurryKat 12m boom spreader, which has delivery pipes spaced at 25cm intervals along its working width. Slurry delivered from the trailing umbilical pipe passes through a flow rate monitor and two macerators before being distributed down the outlet pipes.
To avoid spreading slurry into tramlines, an on-board compressor is used to inflate ‘balloons’ to block the flow of slurry in the pipes where outlets are over the tramlines.
“I get on very well with this spreader,” he says. “I have an in-cab display which tells me just how much slurry I’m applying and a tractor guidance system which ensures I am driving in the right place.”
The spreader, which is attached to a New Holland T7060, fitted with wide Goodyear tyres, can also be used to carry a hose reeler – hose positioning and management is a major part of umbilical spreading.
“When I prepare for a job in a specific field I look on Google Earth and print off a plan of the fields and the slurry store so I can plan the best route for the hose,” he says. “When this has been run out to the field, decisions have to be made on how to spread without causing problems with the pipe twisting.
“When spreading on cereals we have to follow the tramlines, which is not so easy to organise as say, a grass field where we can run diagonally across it. And if there are telegraph poles there’s even more to think about.”
The normal application rate is 50cu m/ha which equates to a covering across the field of 5mm. That may not seem a vast amount, but he’s very conscious of the importance of keeping slurry from getting into field drains and ditches.
“Application rate is the result of the volume of slurry arriving at the spreader and the speed at which the spreader is operated,” he explains. “If it is a long-distance pump and/or the slurry is on the thick side, then the flow rate can be reduced and I have to drive at a slower rate – the in-cab monitor provides this key information.”
Blockages
At the start of spreading there is a tendency for the first few gallons of slurry arriving at the spreader to be very fibrous, to the point that it can block macerators and cause some annoying and unpleasant unblocking work.
Mr Mortimer says he is at a loss to explain why this happens and can only suggest that some form of separation happens while the slurry is passing through the pipe.
And when spreading has been completed, the normal practice is to connect a compressor to the hose and blow it clean before it is reeled back up.
“We did try putting a plastic ball down the pipe but the one we put in was never seen again, so now we use air,” he says.
Avoiding disease
One of the big issues is ensuring he does not inadvertently carry disease from one pig herd to another and he prefers to alternate between dairy farms and pig farms so the risk of any carryover is minimised.
The matter is further complicated by having a pig herd at home, so that the option of keeping his pipes, spreader and pumps on home ground is not available.
“I have to store the kit in off-lying places but the problem really comes when we have some maintenance to do – welding, for example,” he points out. “For this we have to bring in mobile welders and other gear, all of which is not too good.”
For the future, Mr Mortimer says he plans to invest in a radio-controlled pump that he can control from the spreading tractor.
“This would mean it could be a one-man operation – I would have the ability to control the pump remotely and be able to shut it down,” he explains.
“The system would also provide me with information regarding the engine’s oil pressure, temperature, speed and other management information. It will, if it works, be a useful system and, the bottom line is that operating costs would be reduced significantly.”
There are also plans to home build a 24m spreader, which would avoid having to run on cereals with 24m tramlines on every other run.
In terms of output though, he concedes it would be very similar to that of his 12m spreader – unless he can find a way of increasing the delivery rate of the pump.