Valtra tractors: Common problems and how to fix them
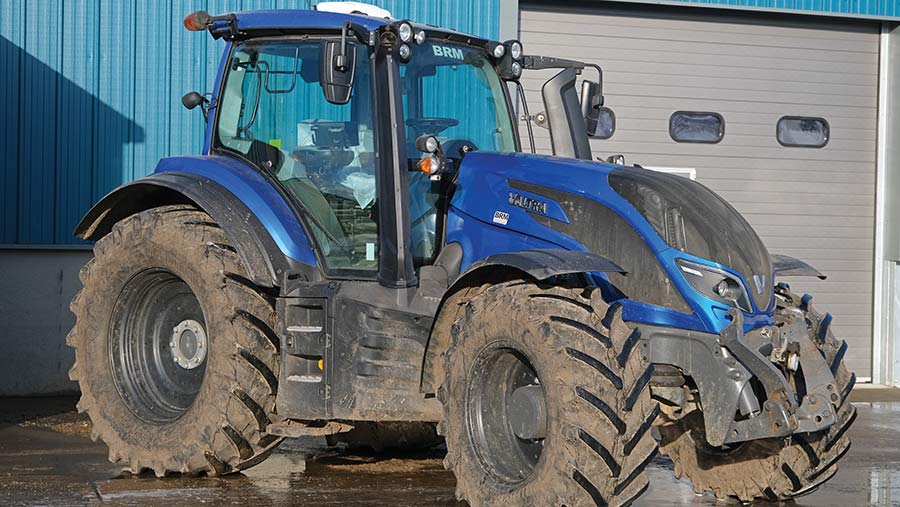
When Valtra joined the Agco stable in the early 2000s, it brought with it dependable Sisu engines that have since been given the parent company’s branding.
They are still solid performers and rarely give problems, so potential trouble spots on its tractors tend to be found in other areas, one of which is the transmissions.
See also: John Deere tractors: Common problems and how to fix them
Until recently, these were produced almost exclusively in-house and, although they’re generally reliable, they do have the odd weakness, particularly if maintenance is neglected or they’re abused.
Other niggles tend to be confined to ancillaries and a few minor electrical quirks.
We will mainly be focusing on the popular six-cylinder T4 and four-cylinder N4 models, which were launched in 2014 and 2015 respectively, and have only recently been superseded.
To get the lowdown on these models, we called on the expertise of Brian Robinson, owner of BRM – the longest-serving Valtra dealership in the UK – and service manager Peter Reed.
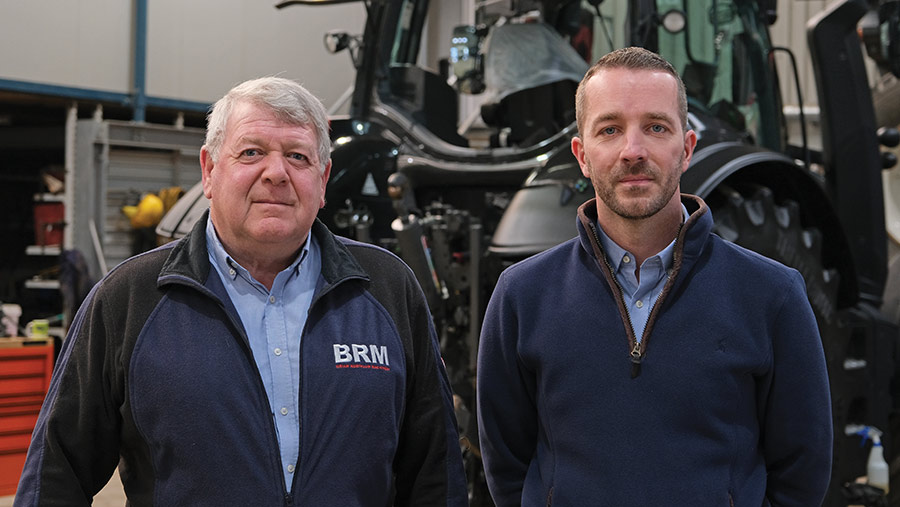
Brian Andrews (left) and Peter Reed © James Andrews
Transmission breather filter
A very simple service item that often gets missed is a small £13 filter that sits on the end of the transmission breather pipe.
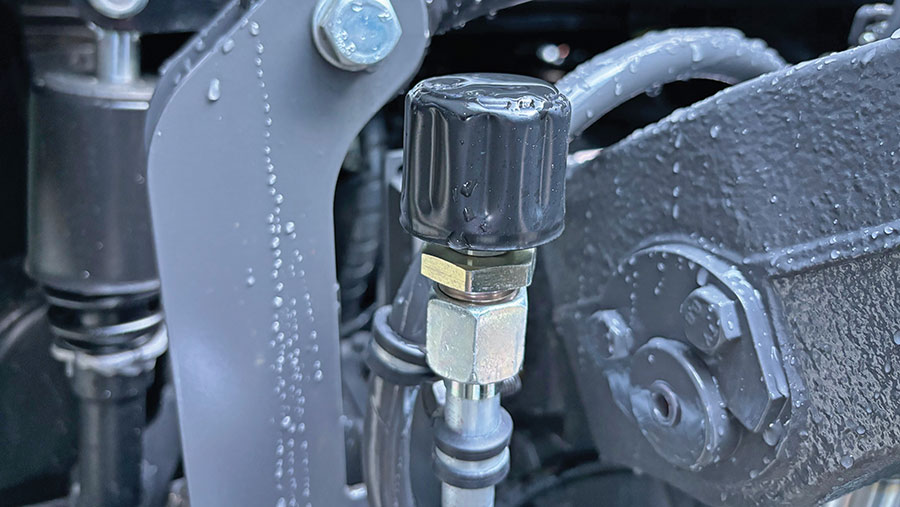
© James Andrews
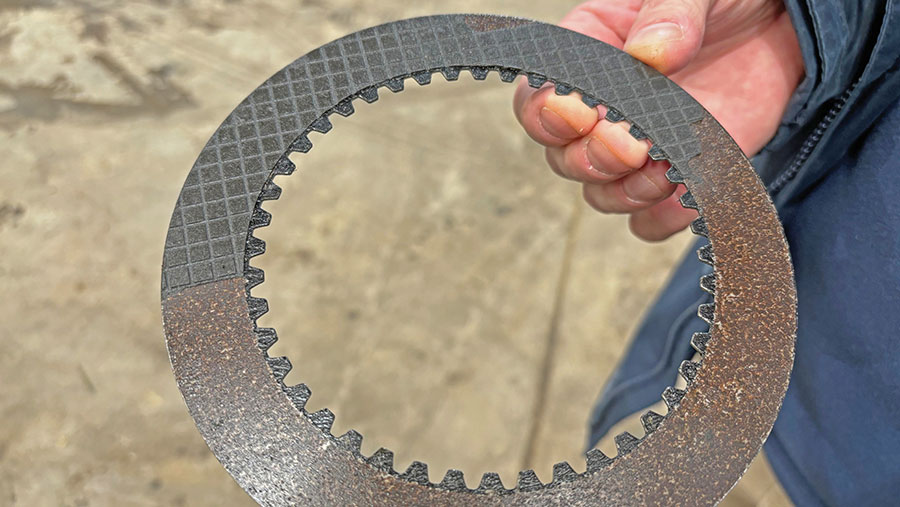
© James Andrews
It’s fitted on most Valtra tractors and should be changed every 2,400 hours. If neglected, it will eventually block, resulting in a build-up of condensation that, after a while, will cause the clutch plates to delaminate.
This can result in a gut-wrenching £5,000-£6,000 bill to have all the clutch packs replaced, which is particularly galling when it’s so cheap and easy to avoid. BRM has to carry out roughly two such rebuilds a year.
Forward/reverse clutch packs
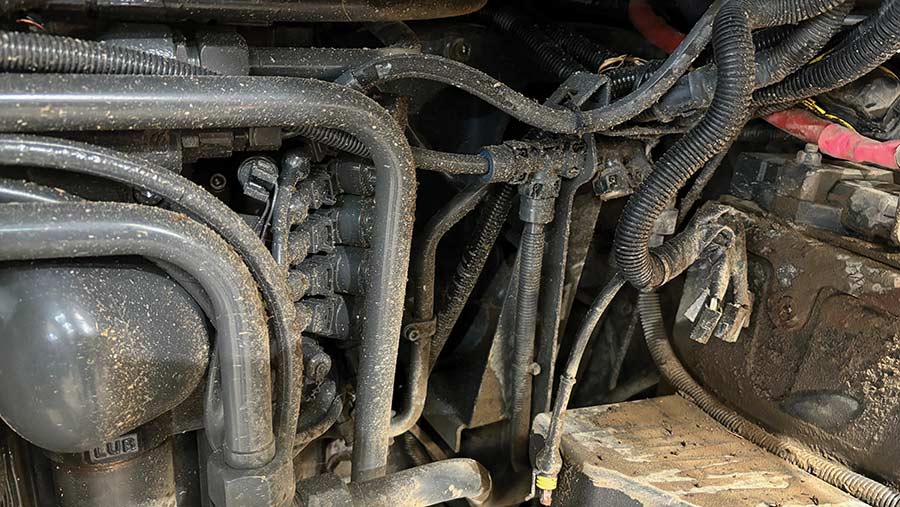
© James Andrews
All Valtra-built transmissions contain three sections, with a powershift box at the front, or a hydrostat unit on Direct models, a forward/reverse clutch pack in the middle, and a mechanical range box at the rear.
The front and rear sections tend to give very little trouble if properly maintained, but the clutch packs in the forward/reverse box can wear out if the tractor is driven inconsiderately.
One of the biggest causes of premature failure is starting off in too high a gear, particularly if backing a heavy trailer into a shed by riding the clutch.
Not only does this file away the friction material, but it also causes a build-up of heat that can degrade it yet further.
The repair job takes about 35 hours as the tractor needs to be split to get the box out.
Front gearbox seal
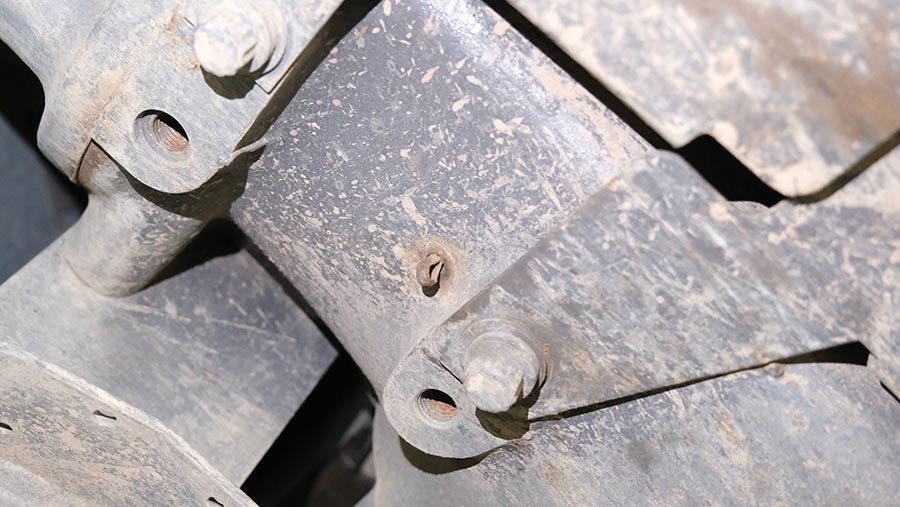
© James Andrews
One weakness that can’t be resolved by fastidious maintenance or careful driving is the front gearbox seal.
On HiTech tractors, you can see the seal and any failures will result in a puddle of oil under the tractor when it’s parked.
But all other models have the seal covered by the bell housing, meaning it’s far more difficult to spot.
In fact, the only tell-tale sign is a weep of oil coming out of a hole on the bell housing, which should have a split pin in it.
The seal itself is cheap, but replacing it takes a couple of days.
Powershift circlip failure
Another frailty that has been fixed on tractors built from about 2020 is a circlip on one of the shafts in the powershift box.
This can snap without warning, causing a loss of drive, and it’s a good four-day job to replace it.
The problem doesn’t seem to be related to the number of hours a tractor has worked, but those that have had a new clip fitted have a considerably lower risk of it failing again.
Many tractors will have had this update, but there could still be some out there that haven’t. Anyone experiencing this problem should contact their local dealer to see what the best approach is to getting it repaired.
Water pump inner bearing
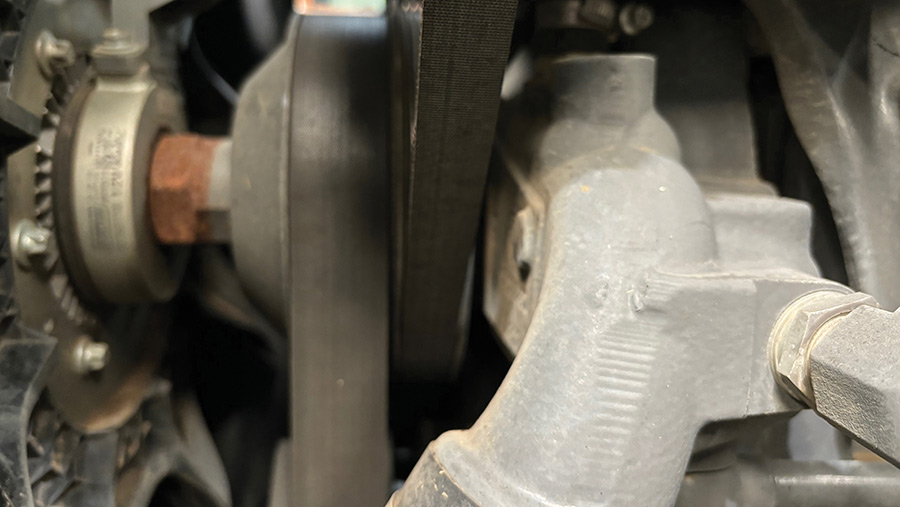
© James Andrews
Water pump bearings are known to fail on tractors built before 2018, causing the fan to drop and catch on the guard.
Operators should be able to hear this and, occasionally, the dropping pulley will throw off the alternator drive belt, causing a warning light to flick up on the dash.
Replacement pumps cost £525 for six-cylinder tractors and £400 for four-cylinder models.
Idler pulley bearings can also pack up, giving out an irritating squeak in the process.
These cost about £120 and they’re simple to replace.
Secondary coolant pump failure
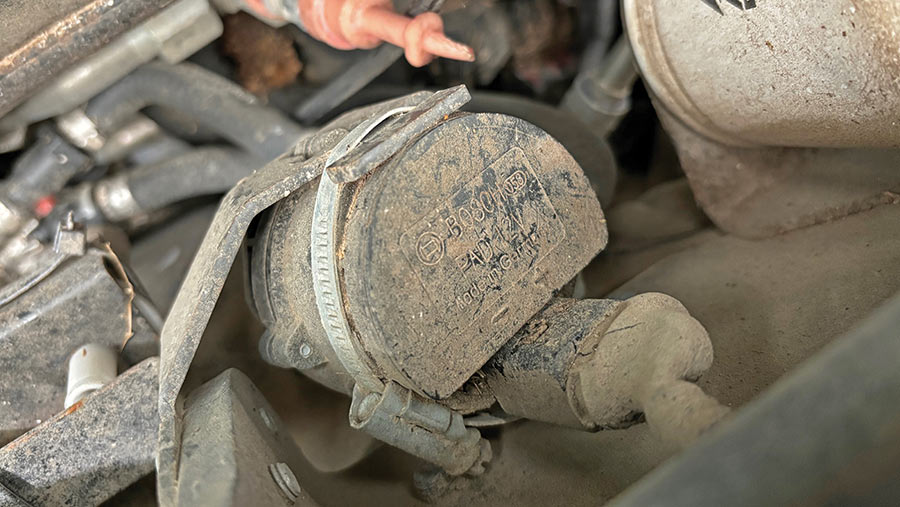
© James Andrews
If the air conditioning on N4 tractors suddenly stops working, the likely culprit will be a seized secondary coolant pump, which sits at the top of the engine bay near the windscreen.
This is because it blows a fuse when it fails, and this is shared with the air-conditioning pump.
The cheapest fix is to unplug the unit and replace the fuse, as its only role is to supply warm water to the lower cab heater, which, although very welcome in snowy Finland, isn’t generally required in the UK.
HiTech hydraulic pumps
Unlike higher-spec Active, Versu and Direct tractors, which have separate hydraulic pumps for the tractor’s on-board functions and spool valves, HiTech models have just one.
And the amount of pressure put on this single open-centre unit can prove too much, causing it to fail. Ironically, of the HiTech’s two available pump outputs – 73 litres/min and 90 litres/min – it’s the latter that gives the trouble.
Therefore, BRM recommends any failed units are replaced with the smaller version, which gives such a similar performance that most operators won’t notice the difference. The job costs about £1,500 in total.
Cab fan resistors
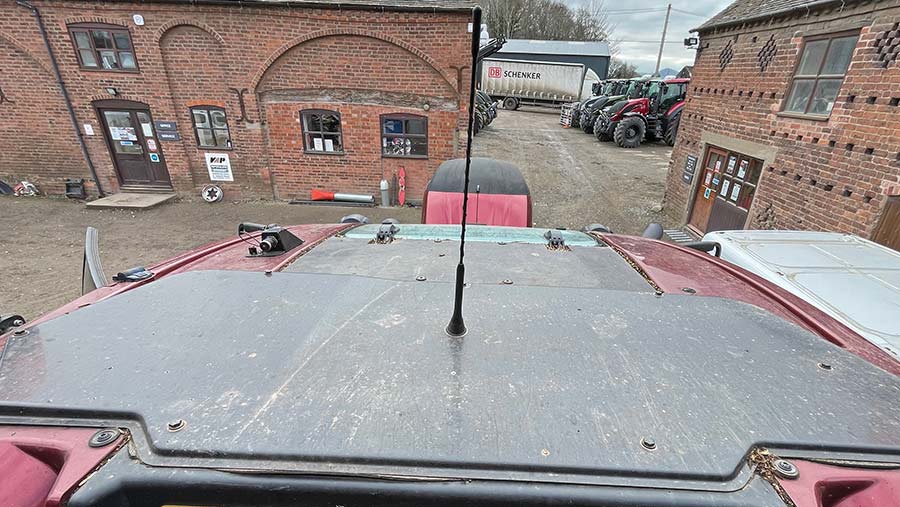
© James Andrews
If the cabin air filter gets blocked, it can blow the roof fan resistor, causing it to only run flat out on speed four.
Replacement is simple, by lifting a panel on the top of the roof, and they only cost about £25.
AdBlue problems
Like all tractors fitted with an AdBlue after-treatment, Valtras can give trouble.
However, the fact they don’t have an AdBlue quality sensor means they aren’t as finicky as some systems.
BRM reckons most problems are simple to fix, without owners having to resort to having the arrangement removed.
Fractured hydraulic pump elbows
Active, Versu and Direct tractors run their external hydraulics off a load-sensing pump, and the cast elbows supplying this will occasionally fracture.
The result will be sluggish hydraulic performance, such as trailers being slow to tip.
The elbow costs about £150 and it’s a one-day job to replace, which involves taking off the right rear wheel and gaining access to the pump via the transmission side cover.
Pto and creep selector switches
Water is not the best friend of pto and creep speed sensors, which are positioned on the rear pto housing, so overzealous pressure washing can be the end of them.
In fact, some owners have been able to stuff all three in one enthusiastic session.
If the pto won’t start or you can’t change the speed, it’s likely that one or more of the pto selectors have given up.
Symptoms of a failed creep selector switch will either be the tractor not setting off at all, or not being able to select the creeper range.
N4 engine balancer unit
Some dealers in hilly areas have reported problems with the balancer unit on N4 tractors seizing if the engine is over-revved. However, BRM hasn’t had any instances of this in its area.
The shaft in question sits at the base of the engine and has a shaft with oval gears at either side that counteracts the forces of the pistons to keep it running smoothly.
It turns at twice the speed of the crank and the gears can jam solid and stop the engine if it’s forced to spin too fast.
Sensible drivers shouldn’t need to worry about this, but those that let the tractor rev off the gauge when being pushed down a hill with a heavy load could end up with an expensive repair bill on their hands.
The fault doesn’t damage the rest of the engine, but the balancer unit will need to be replaced, which involves splitting the tractor and lifting the engine off the chassis.
The unit itself costs £650, but there’s also a considerable amount of labour involved.
SmartTouch software glitches
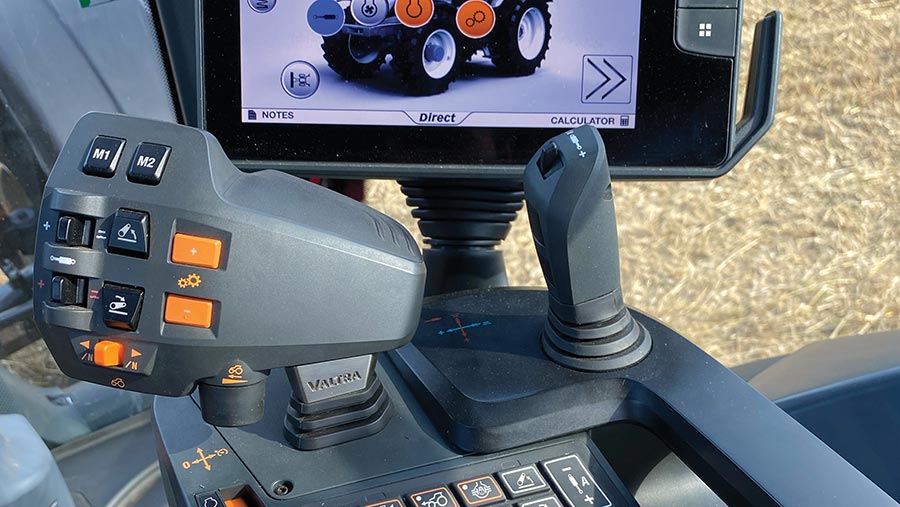
© James Andrews
When Valtra introduced its SmartTouch armrest on tractors built from 2017 onwards, it was a huge step up from the N4 and T4s’ first offering, which was carried over from the previous generation.
It works well, but some early versions can suffer some software glitches that will need sorting by plugging in a laptop.
S-series cab suspension
Our only notable mention for Valtra’s flagship S-series tractors, which until recently were built by Massey Ferguson in Beauvais, France, is the overly complex cab suspension system with four sensors and four airbags.
Sensors are prone to failure and they cost about £200 each.