£50k Sabanto Steward kit gets Fendt 700s working autonomously
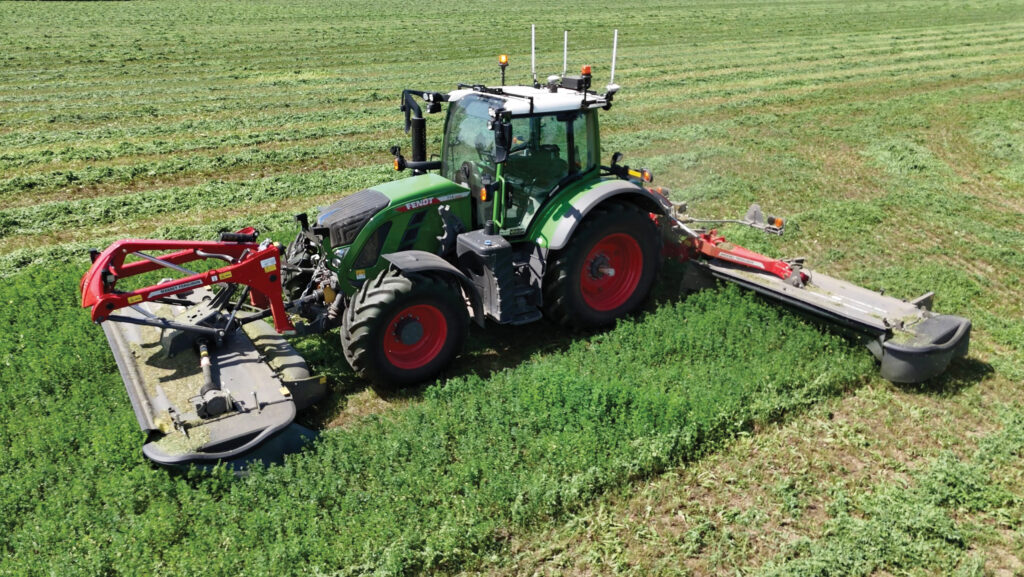
Long, lonely hours spent cultivating, drilling and mowing could be a thing of the past with the advent of a plug-in kit that can get any autosteer-ready tractor operating autonomously.
Not only will these machines drive themselves – and take care of the up/down, on/off controls of the implement behind – but they can do so without owners having to pay an absent-minded, TikTok-browsing yoof to occupy the seat.
This hands-off approach, in the most literal sense, obviously won’t be for everyone.
Taken seriously, tractor driving requires skills that cannot be replicated by a computer and, though driverless systems might be perfectly capable of maintaining an inch-perfect bearing, there’s no substitute for human eyes when it comes to adapting to inconsistent soil conditions.
See also: UK made kit converts any tractor to RTK autosteer for £3k
But there’s no getting away from the fact that labour is both more expensive and harder to come by. Which is why Illinois-based outfit Sabanto reckons its concept has legs.
So far, the company has developed conversion kits for 20 regular tractor models, with plenty more in the pipeline.
The name might sound familiar; the company featured in Farmers Weekly four years ago, when electronics engineer Craig Rupp set about automating a fleet of 60hp and 90hp Kubotas.
Initially, his intention was to offer them as a labour-saving, 24-hour contracting service, but the logistical headache of transporting the machines to the right place at the right time made that approach unworkable.
Instead, he has changed tack and is now selling the Sabanto Steward kits directly to farmers.
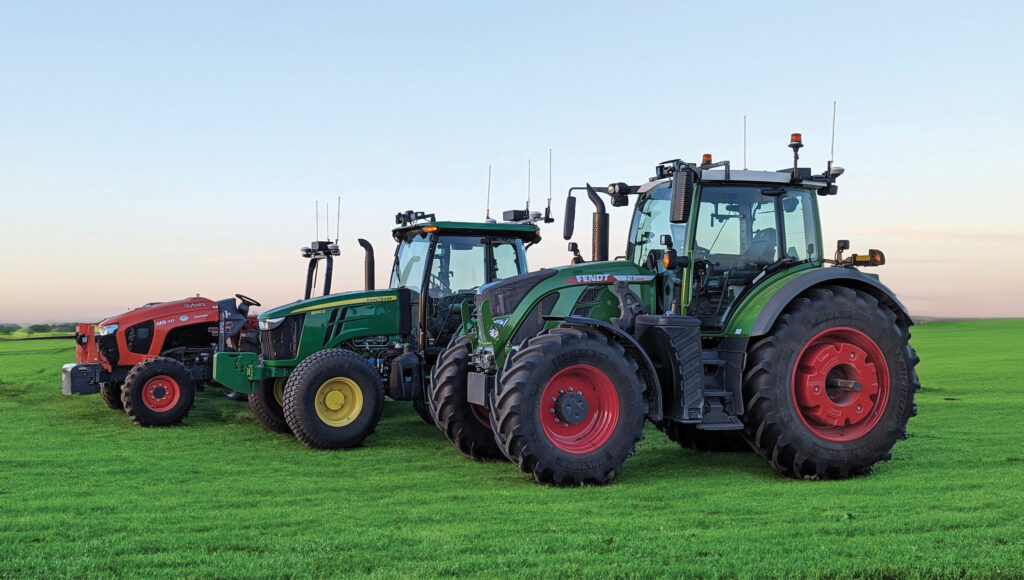
© Sabanto
There are 300 such systems currently operational in North America, most of which are fitted to low-spec, sub-150hp models run in gangs of four or five to replace a single high-horsepower tractor.
This “smaller is better” approach offers the best return on investment, says Sabanto, with one operative tasked with babysitting and refuelling the fleet.
“Autonomy really pays on high repetition jobs where you’re running the tractors all day for a significant chunk of the year, rather than one big tillage machine for a couple of months,” says Sabanto’s Mike Burdick.
Upfront cost of a basic 150hp model might be 20% of a crawler and, says Mike, a posse of them could comfortably outwork it – especially when labour isn’t a factor.
“Plus, it only takes one US$20 [£16] sensor to put a tractor out of action for a day; not a big deal when you’ve got four others also working, but a major problem if it’s your sole machine.”
“So, our approach means less downtime, lower purchase and maintenance costs and, because the tractors are so much smaller, less soil compaction,” he adds.
What tractors?
With than in mind, the company has centred its initial efforts on 80-150hp tractors.
Currently, bespoke kits are available for John Deere’s 5075E, 5085E, 5100E and 5090E, the 5090M, 5100M, 5115M and 5120M, and the 6E range that encompasses the 6105E, 6120E, 6135E.
Then there’s the original version for the Kubota M5s, and another for Fendt’s 700-series, making a total of 20.
Most have been assembled off the back of customer requests – one of whom had 10 tractors converted in a single batch.
The process of building each model-specific system takes about three months, and Sabanto will happily turn its hand to any, provided it gets a minimum order of five units.
One for mid-sized Deutz-Fahrs is currently in the works.
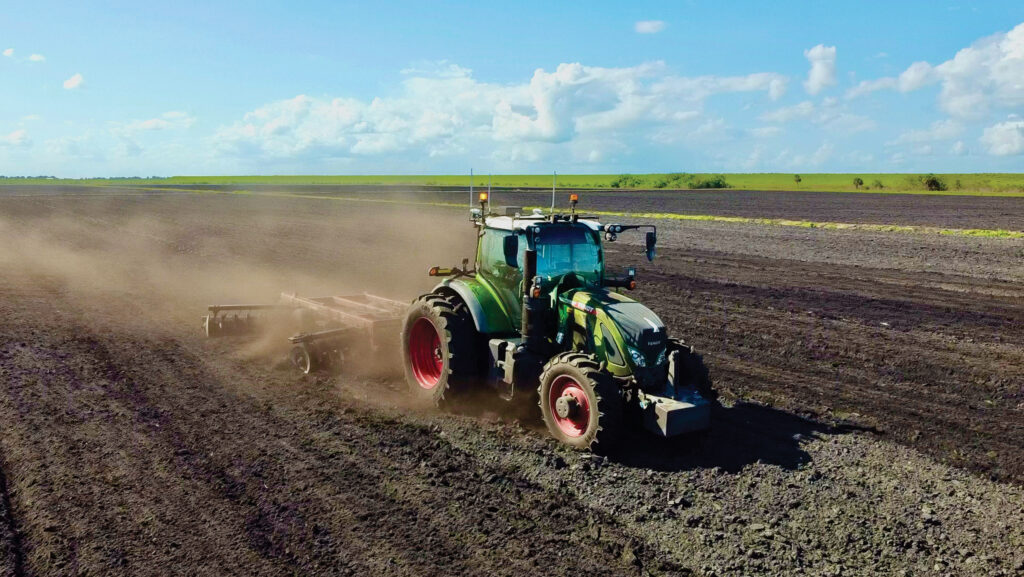
© Sabanto
How does it work?
Development involves deciphering the canbus code so that Sabanto’s software can send its own messages to the tractor.
This allows operatives to set and alter almost every element from a smartphone, via the firm’s “vehicle mission control” app.
This includes firing up the engine, selecting a direction, altering the revs and working the pto, hydraulics and brakes.
The only thing beyond its realm is a mechanical gear change on manual or powershift transmissions.
And because there are very few alterations inside the cab, operators can still drive the machine to the field and complete a boundary lap, ready for a clever path-planning algorithm to do its thing.
Once flicked into “auto”, it works a bit like an ultra-sophisticated headland management system.
“It’s possible to programme different straight-line, turning and transport speeds – up to a 13kph limit – and it’ll lower and lift the implement at the start and end of each bout.
A field-to-field transit mode has also been developed, allowing the tractor to follow a designated path beyond the field boundary.
“In theory, this means it could work several fields in a ring-fenced block without any operator intervention.
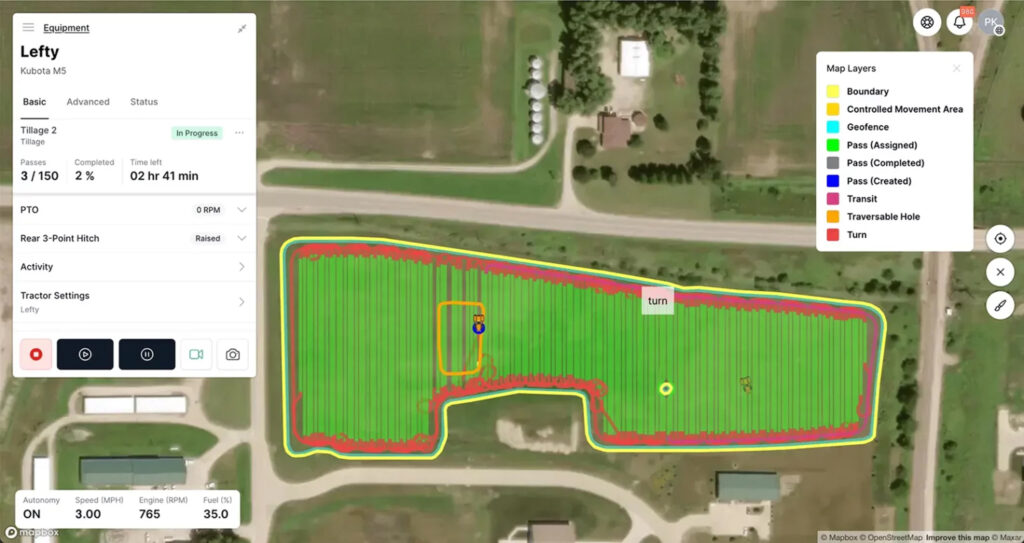
© Sabanto
What’s the catch?
The art of tractor driving is as much about observing the workings of the implement as it is piloting the machine.
Without the means to assess the quality of the job in hand, nor spot blockages or broken shear-bolts, use cases are limited to relatively simple applications with few variations in ground or crop conditions.
However, Sabanto is working with a clutch of implement manufacturers to develop sensor-laden attachments that will spot any problems.
One of these is turf mower maker Trimax, which is integrating vibration, motion and heat detectors into its equipment – information that can be processed to make automatic in-field decisions.
There’s also the foggy issue of liability in the case of an accident.
Responsibility for autonomous vehicles lies with the farm owner, but there’s little in the way of legal regulations and no certification that declares them safe to work with.
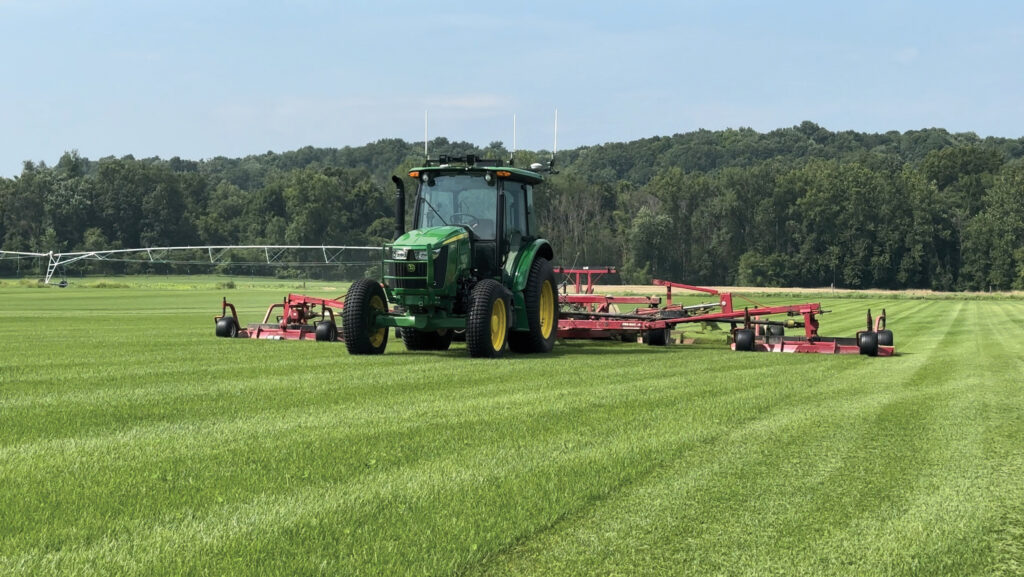
© Sabanto
Installation
The major attraction of Sabanto’s system compared with bona fide field robots such as Agxeed and Agrointelli is that it’s purely a retrofit.
Leaving the designing, building and selling of tractors to established manufacturers means buyers can pick the specific machine that they want, service it conventionally, and revert it to original condition should they choose to sell it.
Installation is a two-day affair, followed by a calibration that takes all of five minutes.
On the roof goes an antenna for the remote kill switch, and two more for the pair of RTK-ready Trimble AGA25 receivers.
This twin setup allows them to triangulate against one another, maximising the reliability of the sub-4cm guidance under a partial tree canopy.
Navigational data is paired with information from a ruck of sensors and video cameras, all processed by a control module outside the cab that talks to the tractor’s steering and power systems.
The four colour cameras on the roof also provide a full field view to the operative’s smartphone and, along with a handful of infrared sensors, help detect any unexpected obstacles.
They are currently only tuned to spot something protruding about 30cm off the ground, meaning any wet patches must be noted beforehand.
However, it does have a “bog down” feature, which initiates an alert should wheel speed exceed the GPS-monitored forward speed.
Other safety systems include enforced geofences, a handheld kill switch, and an on-tractor emergency stop.
Buying it
The gear required for this setup has, unusually, dropped in price – it’s now US$65,000 (£50,000) including installation, followed by a US$10,000 (£7,700) annual subscription that includes the cost of the guidance.
Kits have hitherto been sold in the US and Canada through Trimble’s Vantage dealer network, but the company is open to European exports, particularly as the region has no shortage of 100-200hp tractors ripe for conversion.
The Agco-owned guidance specialist also happens to have a financial interest in Sabanto.
And, with Agco having made no secret of its intention to tap into the retrofit technology sector, it might not be long before the Steward is available at a dealer near you.