Dairy goes electric with Avant e6 pivot-steer telehandler
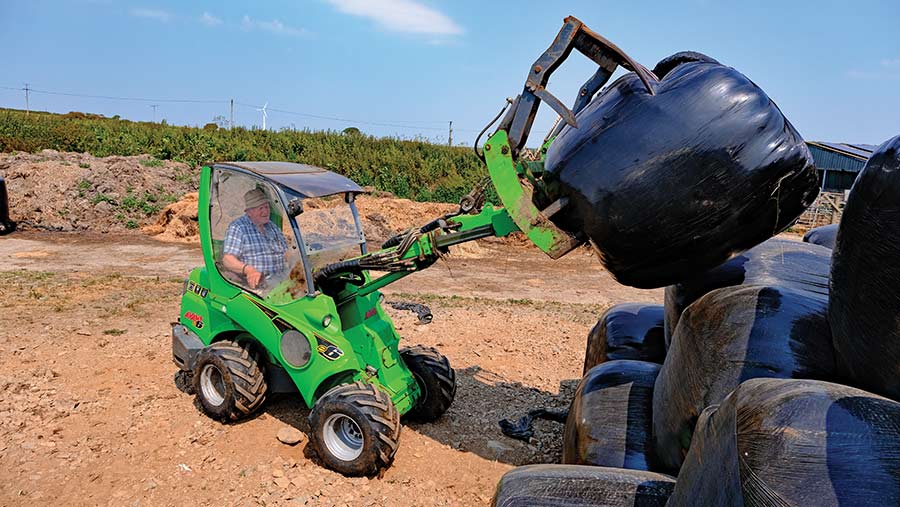
After 40 years of running Bobcat skidsteer loaders on his 60-cow organic dairy farm near St Davids, Wyn Evans opted for a completely different type of materials handler.
Not only is the Avant e6 a pivot-steer machine with telescopic boom, but it’s also powered by electrons rather than fossil fuels.
Due to the compact proportions of the farmyard and small field sizes averaging just 1ha, the machine carries out more than just handling duties, turning its hand to inter-row hoeing and using a riddling bucket for lifting fodder beet.
We had a chat with Wyn and his grandson, Ben Kimberley, to find out how the machine has performed during its first four years on the farm.
See also: On test: JCB Teleskid v Norcar a7545 mini pivot-steer
Caerfai Farm’s Avant e6
- Year 2019
- Hours worked 2,361
- Motor 6kW drive motor and 3kW motor for hydraulics
- Batteries 13.8kWh lithium ion
- Max lift height 2,790mm
- Lift capacity 900kg
- Transmission Three-speed hydrostatic
- Top speed 10kph
- Cab Partly enclosed
Why an Avant e6?
I’m big fan of renewable energy and have a few banks of solar panels that generate a peak power of 70kW, as well as a 10kW wind turbine and some battery storage.
To make the most of that energy, I keep the house warm using a ground-source heat pump, run an electric car and have an electric Ubco motorbike for getting around the farm.
So, when the electric loaders started coming out, I saw another opportunity to use more renewable energy and cut down on fossil fuels.
I was also finding the skidsteer hard to climb in and out of, so a side-access machine was appealing on that front, too.
At the time, Avant and Weidemann were the only brands offering a suitable electric model, but I ruled out the latter as it was about £12,000 more expensive, which I couldn’t justify.
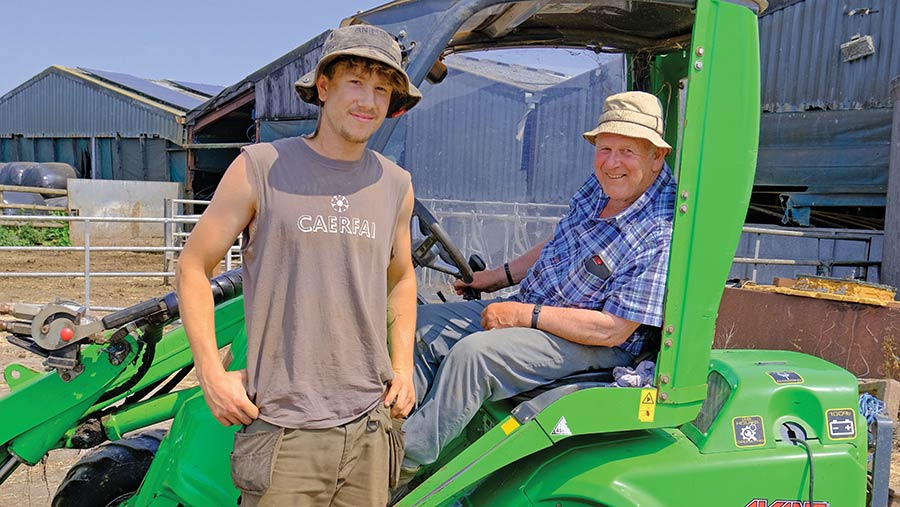
Ben Kimberley (left) and Wyn Evans © James Andrews
Before committing to buy, I had a demonstration from the head of Avant UK to see how it would fit in with our system.
We found it could do everything the skidsteer did and he seemed happy that it would be up to the job. It was also smoother to drive, more manoeuvrable, and the telescopic arms made it considerably more versatile.
Off the back of that performance, I bought a new e6 from the then dealer Border Bobcat, which set me back just under £40,000, including a rapid charger, a bucket and fork with grab.
It has a different style headstock to most machines, so I also bought back plates to adapt our range of skidsteer attachments.
These include pallet tines, a bale squeeze, a slurry stirrer, a yard scraper, an inter-row hoe, a riddle bucket for lifting our fodder beet and an auger bucket for feeding it out.
I also made a cubicle sweeper out of a cow brush, which is far easier than doing the job by hand.
How has it performed?
For such a small machine that runs on batteries it’s amazing what it can do, but it has been plagued with problems.
If I was giving it a rating out of 10, it would still scrape a seven though, so I’ll run through the good bits first.
Running costs (excluding repairs) are virtually nothing, compared with the old Bobcat, which used to burn about 50 litres of diesel a week, or 2,500 litres a year.
We also had to put a new set of tyres on it every year and the Avant is still on its originals after 2,361 hours.
Officially, the e6 is only rated to lift about 900kg, but it’s just about powerful enough to pick up 1t.
Even at full reach, we can get a round silage bale off a three-high stack, although we do have to slide it off as we retract the boom. It can also stack bales three high, providing they’re not too wet.
When it first arrived, it came with foam-filled tyres, which were designed to make it more stable when lifting.
The problem was that they were rock hard and gave it a terrible ride, so we had them swapped for a normal set of flotation tyres.
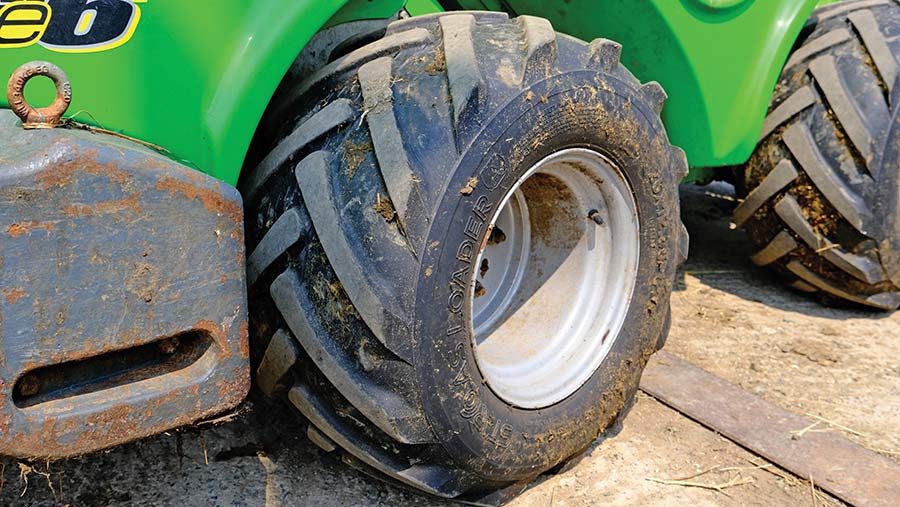
© James Andrews
It’s now much more comfortable, but we’ve had to tie some extra weights on the back to keep the back end down when lifting heavy loads.
Battery capacity has also proved to be ample and there’s been no noticeable drop in performance over the years. You do have to adopt a slightly different mindset when operating it though.
Run time is dependent on how much pushing and lifting power you need, and you can save energy by selecting the right mode for the job you’re doing.
There are two ways of doing this, as it has a separate 6kW electric motor to power the hydraulic pump for the wheels and another 3kW unit to power the boom and steering.
Typically, we run the wheel motor in the middle of three settings, which gives a good balance of speed and economy around the yard, only flipping into the top speed when we need to travel longer distances.
As for the hydraulics, these have a hand throttle arrangement and the more revs you give the motor, the faster the hydraulic performance is.
It’s difficult to give an exact run time as it varies from job to job, but we have managed to stack 90 silage bales with it on less than a full charge.
When working, the display in the cab gives an accurate reading of how much charge is remaining, which we find very useful.

© James Andrews
Regular charging is another way to maximise operating time. We rarely run it from a full charge to empty, instead plugging it in often to keep the batteries topped up, particularly if the solar panels and turbine are producing a surplus of energy.
The loader was originally ordered with an expensive DC fast charger that would get the cells from 20% to 80% charge in just one hour, but this has since packed up and is proving difficult to get repaired.
Luckily, connecting the in-built AC charger, which plugs directly into the mains, keeps it topped up well enough.
Reliability
Now for the not so good. There has been a string of problems that started with the battery management system packing up.
This happened when the machine had done just 800 hours and, because it was integrated into the battery pack, the whole lot had to be changed.
Thankfully this was replaced under warranty, as I shudder to think how much it would have cost.
Other repairs that were outside the warranty included a snapped inner boom, worn pivot bushes, a cracked chassis and a failed driveshaft, although Avant did cover the cost of the parts for the latter.
One of the drive motors failed too, costing about £1,600, and the cooling fan gave up. But we found a replacement for this online and fitted it ourselves to save a few quid.
For the times it’s been out of action, the new local dealer, Davies Implements, has been helpful enough to either lend us or let us hire another machine to keep us going.
Interestingly, this is usually the Avant 528 diesel equivalent, which seems old-fashioned, noisy and fumy compared with the e6.
We’ve just gone through nine months without any serious problems, so hopefully it’ll now stay that way.
What could be improved?
We don’t have many complaints about its performance, although it would be nice to have an extra 200kg or so of lift capacity to make it more comfortable picking up heavy silage bales.
Build quality and reliability is a bigger concern though. It might be fine for lighter work, but it needs to be a bit tougher to stand up to regular use on a farm.
When the time comes to replace it, I will be looking for something similar.
Although, one dealer has told me it’s now only worth £6,000 and another has valued it at about £12,000, so the depreciation has been sharp and the cost to upgrade will be considerable.
Other compact pivot-steer loader brands to consider
- Schaffer
- Weidemann
- Tobroco-Giant
- Manitou/Gehl
- MultiOne
- Blaney
- HZM
- Knickmops
- Heracles