Video: Low-cost tool offers alternative to post-harvest spraying
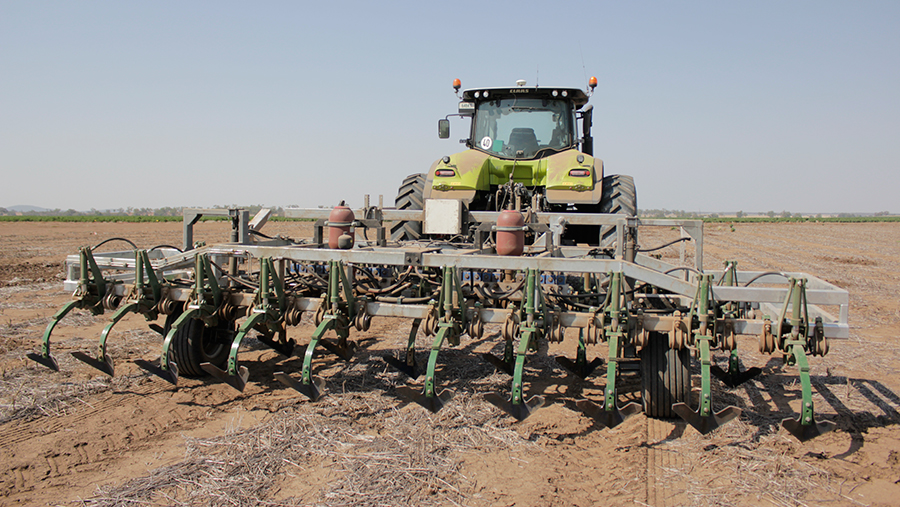
A novel Aussie-designed mechanical weed-seeking tool is set to go into commercial production this year, offering growers a non-chemical, less weather-dependent alternative to pricey stubble spraying regimes.
The Weed Chipper uses an infrared system sourced from established manufacturer Weed It to monitor the ground for live plant matter.
At the first sniff of a weed, it responds by activating a solenoid that swings individual tines into action for a split second, chipping unwanted plants out of the ground and leaving their roots exposed to burn off in the sun.
This mechanical, targeted-tillage approach to weed killing leaves farmers far less constrained by weather conditions compared with spraying, when hot, windy or rainy conditions regularly constrict working windows.
See also:Â New spot-spraying system could save growers millions on herbicides
What’s it based on?
The idea originated from a stroke of serendipity. While on a farm tour, Australian grower Ray Harrington (of Seed Destructor fame) booted a rogue weed while bemoaning the challenges of post-harvest stubble management and herbicide resistance. By luck, it turned out to be the first step in developing a weed-seeking tillage system.
The development project was put out to tender by the Grains Research and Development Corporation and won by the University of Western Australia (see “Where did it start?”).
After hastily assembling a crack team of farmers and designers, senior mechanical engineering lecturer Andrew Guzzomi decided the quickest and simplest route to development would be to adapt an existing toolbar.
A drawbar-mounted Trashworker on flotation tyres, built by old-school Aussie firm Shearer, was earmarked as the base unit because of its rock-solid reputation and ability to cope with rough ground.
It was stripped of its standard hydraulic break-back system and the designers set about developing sprung assemblies to hold the tine modules in a standby position 100mm above the ground.
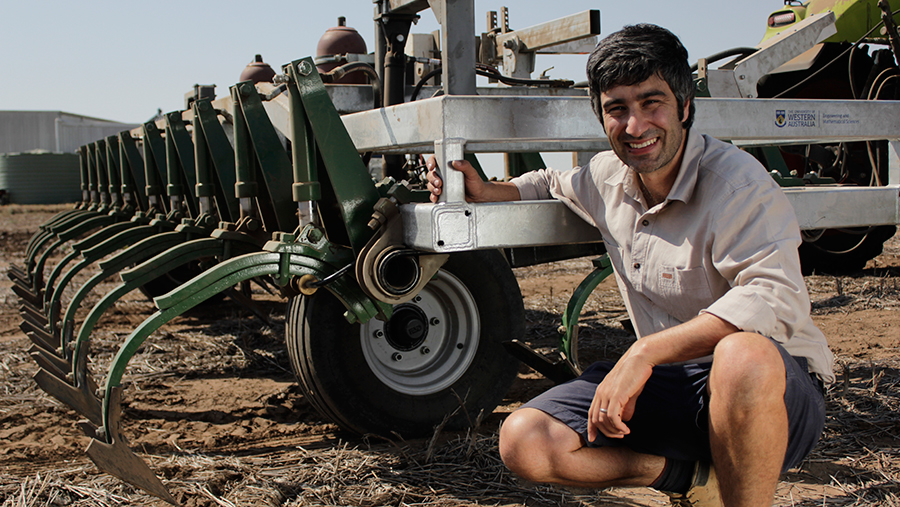
Andrew Guzzomi
The legs clamp to the Trashworker’s main 100mm box section frame via a torsional coil spring, which is contained within a mounting bracket to prevent it pinging across the field should it snap.
Power is provided by the tractor’s hydraulics. On 6m, 20-tine models, it supplies oil to a pair of hydraulic blocks, each with its own 10-litre accumulator. When a camera detects a weed, it activates a solenoid, triggering the release of high-pressure, high-volume oil to a particular tine ram.
When engaged, oil at 80bar pressure forces the hydraulic ram to extend, momentarily firing the leg through its pivot and into the ground. Bump stops prevent over extension and, with the help of the spring, the tine then rapidly recoils to its standby position – a process that takes less than half a second in total.
There should be enough oil power to operate up to six tines at once, says Dr Guzzomi, though there needs to be occasional lulls in weed density to allow the accumulators to recharge.
The shares, or ‘sweeps’ are 450mm wide and mounted to legs spaced 300mm apart, which provides plenty of overlap. Currently, the system uses V-shaped duck foot sweeps that do a neat enough job of chipping the weed out of hard, baked ground.
However, they are better suited to traditional tillage systems, so Dr Guzzomi is looking to add the option of a flatter, squarer body – similar to a garden hoe – that can slice under plants to a depth of roughly 50mm.
How do the cameras work?
Weed chipping activity is initiated by a network of cameras mounted on the toolbar.
The system is actually an off-the-shelf fitment from Weed It and offers the same green-on-brown weed detection as used by many Aussie sprayer operators targeting weeds in post-harvest stubbles.
Typically, they are carried on a fixed beam and positioned to look straight down into the canopy.
They work by shining a beam of broad-spectrum infrared light at the stubble to detect live plant matter. Chlorophyll responds to the
red light by absorbing it and emitting near-infrared back on to the sensors, which decide whether to activate the nozzle solenoid or not.
On the Weed Chipper, this controls individual rams in a hydraulic system, rather than a spray nozzle, so Dr Guzzomi had to tinker with the numbers in the control screen relating to liquid viscosity and application rate to get it to work as desired.
He also programmed a time delay to match the speed of work so that the tine is engaged exactly as the weed comes into striking distance.
The cameras are mounted 1.5m above the ground, with each one monitoring a path of the same width. So, with the tines set at 300mm centres, one camera controls five sweeps.
To do this, the beam from each camera is split into five bands. Sensitivity can be adjusted in the control box, but they should comfortably be able to detect weeds from two-leaf stage.
There will also be the opportunity to develop this system as more sophisticated camera kit becomes available. Of particular interest is the green-on-green software built by French firm Bilberry, which can detect weeds in growing crops and offers the potential of inter-crop work.
However, in the short-term, at least, price is the stumbling block. Even Weed It’s well-established system doesn’t come cheap – buyers can expect to pay AUD$5,000/camera (£2,600), plus the same again for the control unit. On a 6m machine, that’s £13,000 before any metal has been welded.
However, that is still significantly cheaper than any sprayer equipped with the same kit.
Can it work at speed?
The selective nature of the Weed Chipper means it suits relatively low weed densities of around 1/10sq m in fallow conditions.
Farmers coming across a really dense bank of weeds should, at the very least, slow down, but it probably makes more sense to map it and return with a full tillage implement. Operating lots of the legs at once will drain the hydraulic accumulators, which will need time to recharge.
Working speed is typically 10-15kph. It’s a mechanical system, so beyond that, the mass and inertia involved in periodically digging into the ground may eventually take its toll on the metalwork. There’s also the reliability of the cameras to consider – their eagle-eyed skills diminish as the pace increases.
The plus side versus spraying is that it can dig out sprawling weeds up to 70cm in diameter, which may otherwise offer resistance to contact herbicides. It’s also a far more lightweight setup – particularly as it can be run on a modestly sized tractor – so reduces the impact of soil compaction.
What’s the future?
A production-ready 6m model has been hitting farms across Australia and there’s apparently an agreement in place with a machinery manufacturer to take the concept to market.
However, there are bound to be minor tweaks to the final product. Most notably, it is likely to result in a custom toolbar built specifically for the job, which may feature fewer rows given it doesn’t have to deal with a lot of trash.
Production will centre on 12m models to suit the tramline system on Australian farms, but there’s also the potential to run a 6m rig with Swarm Robot’s driverless tractor. Other possible high-tech avenues of development include pairing it with Bilberry’s green-on-green camera system that can detect weeds in green crops.
As for the UK, the company says it needs to conduct trials to check it can achieve adequate weed kill-off in the UK’s cooler, damper conditions.
Where did it start?
The process has been funded by the Australian Grains Research and Development Corporation. It uses levies from its grain producing members to invest in research and development projects that have the potential to improve profitability for grain growers.
Its motivation was to combat the snowballing challenge of herbicide resistance, and it was during farm tours addressing this issue that the idea of a selective mechanical tool was conceived.
The University of Western Australia (UWA), led by mechanical engineer Andrew Guzzomi together with weed scientist Michael Walsh from Sydney University, won the contract and enlisted the help of some of Australia’s top growers and industry advisors to develop the idea.
It’s not unusual for Australian universities to develop products that are taken on commercially. And unlike in the UK, much of the development is focussed on broadacre systems that can be applied now, rather than futuristic robots that don’t necessarily suit existing farming infrastructure.