Farmer invention solves GPS kit compatibility problem
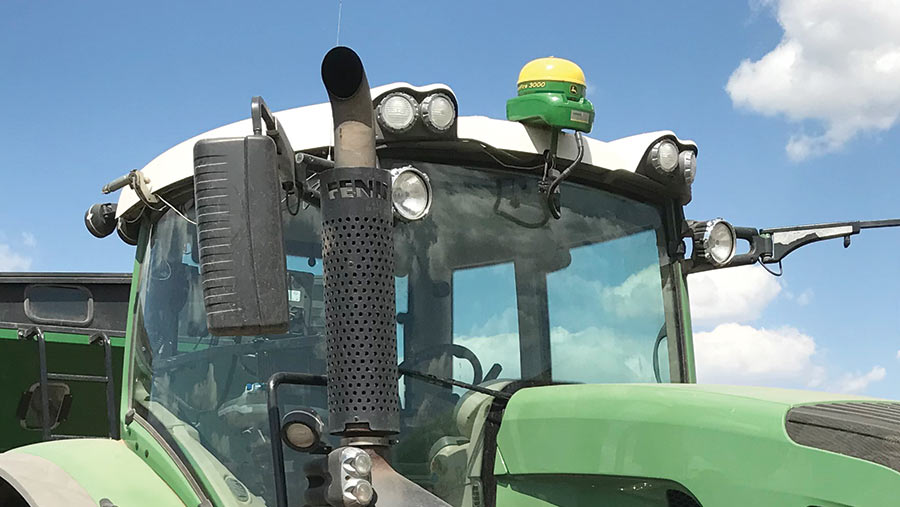
Canadian farmer Johannes Heupel has solved a problem that has been bugging farm businesses ever since farm GPS and yield monitors were invented – compatibility.
The software engineer-cum-farmer has developed a system called Agra GPS JD-Bridge which converts information from most tractor, combine and forager brands so it can to talk to John Deere’s guidance system and screen.
Put simply, it means you can run a Deere screen and receiver in your Claas combine to provide autosteer, make use of existing boundary and AB-line information, and collect/display yield data that can be sent straight into field records.
See also: 7 budget GPS guidance systems on test
Bridge in a nutshell
- Allows users to run a John Deere screen in the tractor, combine or forager cab
- Translates autosteer guidance and yield information into Deere’s computer language
- Bridges available for Claas, Fendt, Massey, Cat, Versatile and Krone
- JCB and Case bridges coming
- Sold through Thurlow Nunn Standen in the UK
- Costs £3,300 and should be dealer-fitted
How does it work?
Through hours of computer work Mr Heupel has cracked the codes on the Canbus system of most of the mainstream tractors and combines on the market, all while running his 2,500ha farm east of Edmonton, Canada.
His combination of wires and minicomputer plumbs into the machine’s Canbus (if the mere mention of this strange word sends your brain into meltdown, see ‘What is Canbus?’, below) to translate the information into Deere’s software language.
What is Canbus?
It’s the name of a network designed according to a particular set of protocols. Controller Area Network (CAN) is the protocol most commonly used on agricultural vehicles because it’s designed to cope with harsh environments.
These networks are a global standard to allow different control units to talk to each other, sending messages from different parts of the machine to report on how its performing.
This means everything is supposed to be compatible, but the information they transfer still takes a lot of figuring out.
Companies don’t provide code information for how to decipher the documentation systems, which means every piece of data is written in a near alien language.
Few of the big companies – the exceptions are JCB and Versatile – provide information to explain what all the code being sent between the machine and its control box is saying.
This means deciphering the information is a pain-staking procedure as the computers are sending thousands of pieces of information every second.
Added to that, all the machinery manufacturers run different documentation systems and none of the data formats are compatible, so each one has to be decoded separately.
The box then converts all of the information coming from the tractor or combine into something that John Deere’s computer can understand.
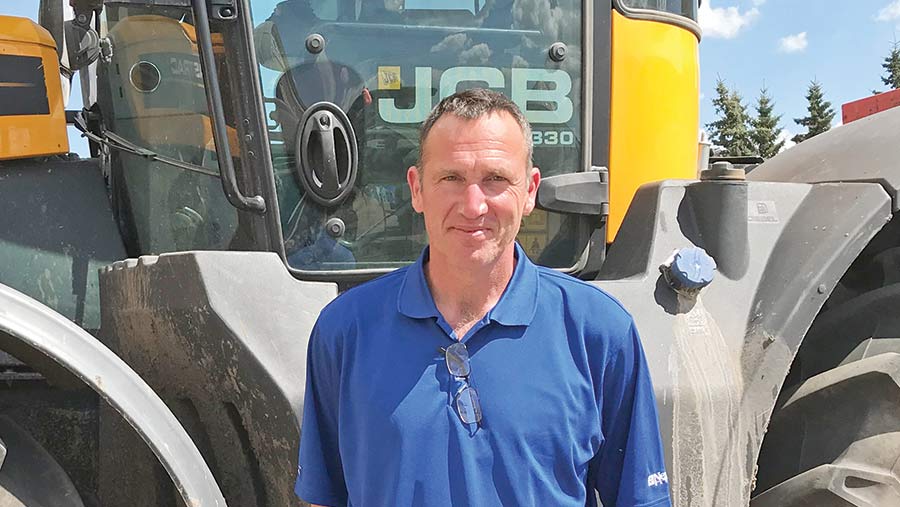
Johannes Heupel
In doing so, Mr Heupel had to work out what data on the Canbus related to each of the machine’s different functions.
Deere’s combine yield monitoring, for instance, is done by counting impacts on a small plate sensor at the top of the clean grain elevator, so he sat in the grain tank tapping the impact plate while monitoring which numbers were changing.
What’s in the box?
Inside the box is a powerful chip computer, which was programmed to act as the middleman between the Canbus and the screen, translating information at super-speed as the machine trundles along in the field.
There are dozens of different versions of this computer, designed to work with specific model ranges from each tractor brand.
It has minimal memory space – just 32kb – because it’s all about transferring information very quickly rather than storing any data.
Instead, data can be stored on the cloud, downloaded to the farm office, or uploaded to services such as MyJohnDeere.
The board also has a mini USB connector to update the computer periodically, along with a steering controller, a couple of Canbus transmitters to talk with the tractor’s system, voltage regulators and capacitors.
What does it mean to me?
In basic terms, the monitor thinks it is in a John Deere combine, so all of the Lexion’s data is translated and processed as normal.
It means operators have access to existing field boundary information and AB lines in the tractor, combine or forager, no matter the make of machine.
That’s particularly useful for getting the most from Deere’s MachineSync system, which shares information between screens, including guidance maps and field coverage.
It can also be used for priority unloading as those on grain cart duty can see the exact location of all the combines in the field, and help to synchronise the speed of the combine and grain cart for perfect offloads.
What can’t it do?
Bridges are specific to particular model ranges, so if you’re lucky enough to own a Fendt 700, 900 and 1000 then each one uses a different connector to tap into the individual Canbus networks. Obviously, the same goes for plumbing into machines from different brands.
New harnesses are being added all the time – a Quadtrac-friendly version has just been launched – and all of the bridges will get a software upgrade for Deere’s new 4640 screen once it is fully available.
However, the systems are only designed to process autosteer/guidance and yield information. It’s a far more complicated job to tap into the machine’s other controls, not least because they vary so differently between brands.
Take combines, for instance; Deere’s S680 is a rotary and the Claas Lexion 780 is a hybrid, which makes them very different to control and manage. It means all machine functions (including engine and transmission details) have to be viewed and controlled through the harvester’s standard screen.
That’s not to say it’s impossible to monitor engine performance and alike through a JD screen, but it runs through a different Canbus system so would take a whole lot of development work with little benefit for the end user.
It’s here the potential for compatibility pretty much ends.
Where can I buy one?
It’s no surprise the harnesses have proved seriously popular, so much so 600 have been shifted in North America alone.
They’re now sold through regular machinery dealers around the globe, including Cambridgeshire-based Thurlow Nunn Standen where the units cost £3,300 apiece (installation adds a bit more to the price).
Selling through tractor dealerships obviously opens the doors to a vast network of farmers, but also means any problems later can be pinned down quickly (they’re often tractor related, rather than gremlins in the harness itself).
So far, there are systems for Claas, Fendt, Massey Ferguson, Cat, Versatile and Krone. A Case-IH Quadtrac version has just been released and JCB-friendly units are in development.
Dealer support has proved strong, as it gives salesman from other brands a chance to muscle in on farms that have traditionally been dominated by John Deere. Instead, customers can stick with the guidance system and software that they’re familiar with, while having the freedom to shop around and pick a machine based on performance or price.
Claas now offers tractors that are harness-ready from the factory – such has been the scale of demand from customers – with the bridge part retrofitted prior to delivery. However, the company charges £1,500 (€1,696) for an unlock code.
Equally, John Deere seems happy, says Mr Heupel, as it keeps their GPS systems active on farms where they might be priced out of combine, tractor or forager sales.
Where did it start?
Johannes Heupel has spent most of his working life in the world of technology, developing software while playing a big-part in the family’s farm.
He has built his own computer in the past and also developed FarmerGPS, a software system designed to provide tractor guidance that is compatible with any regular receiver on the roof.
His guidance-on-the-cheap kit runs through a Windows-based tablet via a standard cable or Bluetooth and includes a 3D view of the field and light-bar-style guidance.
It can also deal with things such as switching the sprayer on/off, form field records that can be downloaded straight to Excel and even be rigged up with an autosteer system.
It took almost two years to get his first Deere-Claas bridge prototype up and running, which he now runs on his Claas and Deere combine fleet.