Ecorobotix spot sprayer slashes chemical costs by over 90%
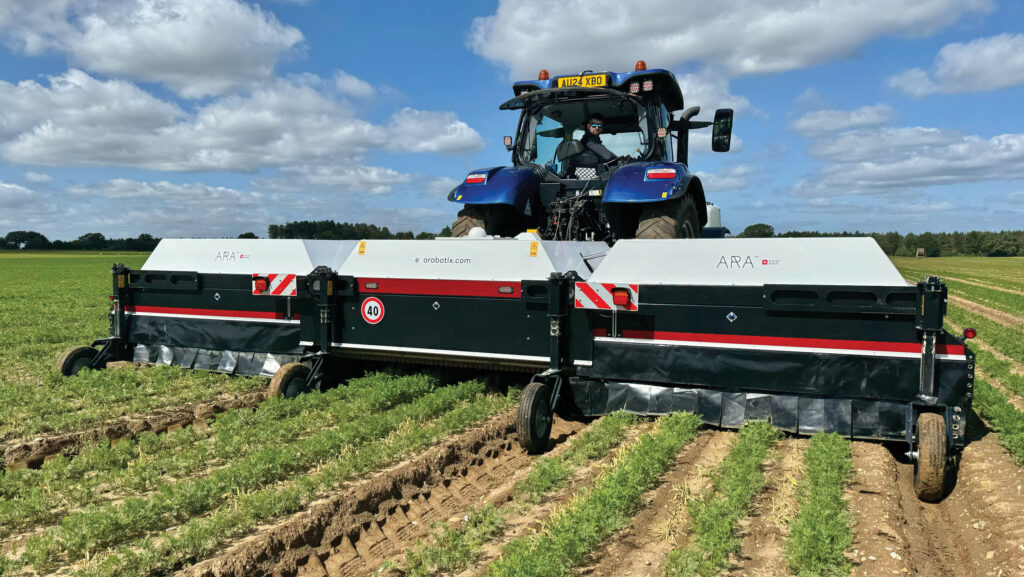
East Anglian agronomy outfit Vegetable Consultancy Services (VCS) has reported chemical savings of up to 96% over the 1,000ha of contracting and demo work it has completed with an Ecorobotix spot-sprayer this year.
Hidden under the hoods of the 6m-wide Ara are six cameras and processors that analyse every bit of greenery they detect, deciding in a split second whether to initiate a chemical blast from one or more of the 156 closely spaced nozzles.
These ultra-accurate applications promise to slash expenditure on plant protection and nutrition products, either by hitting only weeds with selective herbicides or crop plants with insecticides, fungicides and foliar fertilisers.
See also: Video: Retrofit Mojow tractor kit automates arable fieldwork
As a result, the initial outlay of roughly £106,000 can be clawed back in between two and three years.
The only long-term expense to factor in is an annual £5,500 Ecorobotix subscription, which grants access to the specific crop algorithms required by the buyer and the essential on-board image processing software.
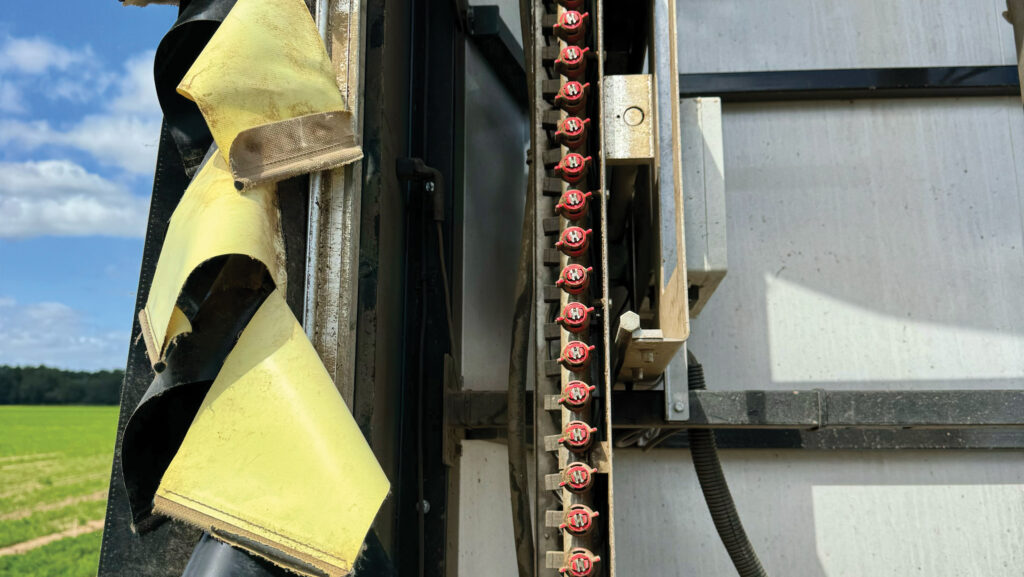
© MAG/Oliver Mark
Growing market
VCS facilitated the sale of 12 Aras in the UK last year, which are already working on farms in Norfolk, Suffolk, Cambridgeshire, Lincolnshire and Kent. A similar number of machines are on track for delivery by spring 2025.
Most buyers are employing the system to target weeds in high value veg crops, but VCS has also used it successfully to knock out thistles and docks in grass crops, and will soon be testing on broad-leaved weeds in cereals.
Better still, Ecorobotix is currently working to fine-tune what might be considered the holy grail of arable algorithms – hitting individual blackgrass plants in wheat.
Success on this front will inevitably drive calls for wider variants than the sole 6m, triple-canopy offering, though that won’t be easy given it already measures 2.8m-wide when folded for the road.
The current software package includes modes specifically designed for sugar beet, onions, maize and oilseed rape, and there’s also a “beta” version for carrots that is free to use while company completes the final stages of development.
In work, operators select the crop and target weed type – such as dicotyledon or monocotyledon species in onions – on the in-cab tablet.
This ensures that herbicide products are only sprayed on plants they are liable to kill, drastically reducing wastage.
There’s also a “safety zone” setting that forms a virtual buffer of 2-16cm around crop plants, which will be of particular value when spraying non-selective herbicides.
How does it work?
The six colour cameras under the canopies each cover a 1m bout and, as they have their own light source, they can function at night just as effectively as in daylight hours.
They shoot roughly 20 images a second, with leaf colour and shape analysed instantly to differentiate between crop and weeds.
Plants only need a couple of true leaves to be identifiable – they can be just 1-2mm in size – so those at the cotyledon stage can be hit early and effectively.
When a target is detected, the necessary solenoid-activated nozzles open for 0.4sec, each one blasting the spray mix over an area of roughly 6sq cm.
As these are spaced 4cm apart, bigger plants sometimes require two nozzles to open simultaneously to ensure complete coverage.
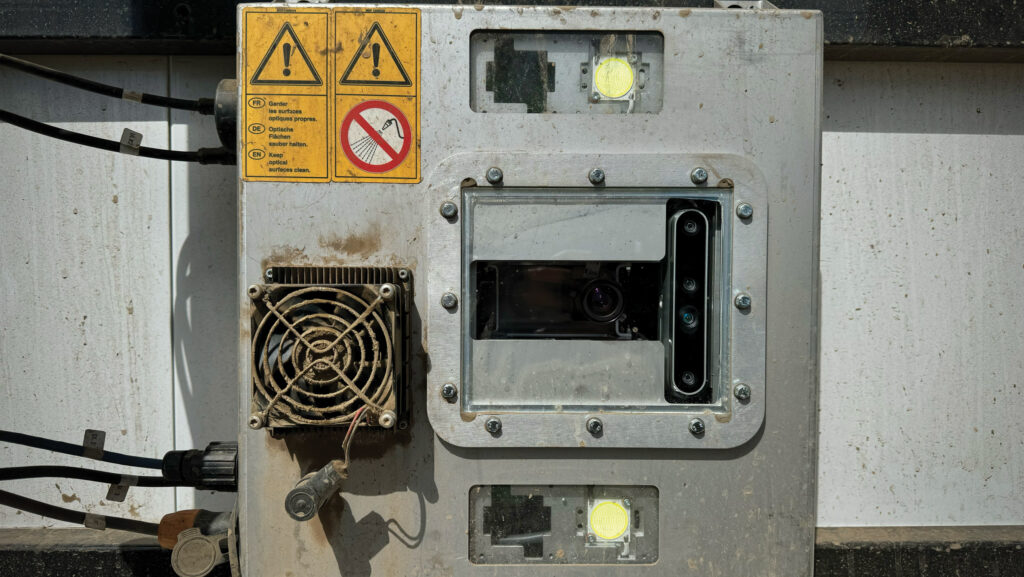
© MAG/Oliver Mark
Ecorobotix has developed its own nozzles for the job, which are slightly narrower than a conventional 110 flat fan to maintain the target spray pattern.
There should also be little in the way of drift to worry about, with the protective skirts attached to the hoods averting any breeze and significantly increasing the number of potential spray days.
Though this means operators are running “blind”, they can check for blockages by cycling through each nozzle on the tablet.
Such issues are exceptionally rare, says VCS – in part because of the fine filters incorporated into the plumbing system, and also because the nozzles apply a fraction of the liquid of a conventional crop sprayer over the course of a season.
Filling the tank
Application rates are set just like a normal sprayer, with outputs equivalent to between 200 and 500 litres/ha.
However, actual usage rates are likely to be about 10% of that – typically about 35 litres/ha – so the Ara can often run for several hours between top-ups.
The spray concoction is carried in a 300-litre tank on the front linkage.
Alongside this is a larger 600-litre vessel for fresh water, which allows operators to refill the mix tank in the field, and flush out the nozzles at the end of a job.
Given that it’s impossible to know how much chemical will be required, VCS suggests mixing about 50 litres to get started.
After a short run, the software will calculate a reliable average usage rate and the quantity required for a given area.
In most cases, the system is set to run at about 3bar, with an automatic regulator maintaining this pressure irrespective of whether a single nozzle is open, or all 156 are called into action at one time.
Typical output is roughly 4ha/hour at a forward speed of 7.2kph and an application rate equivalent to 200 litres/ha.
Liquid is transferred from front to back by a hydraulically driven pump, with the pto connection on the rear purely required to run an alternator that maintains charge in the batteries.
The cameras run on a 24V system, with the rest on 12V.
This means it has an exceptionally low power requirement, with the tractor barely breaking sweat and diesel usage rarely exceeding 4 litres/hour.
The only limiting factor will be linkage lift capacity; the front tanks weigh 1,250kg when full, and the rear unit is 1,160kg.
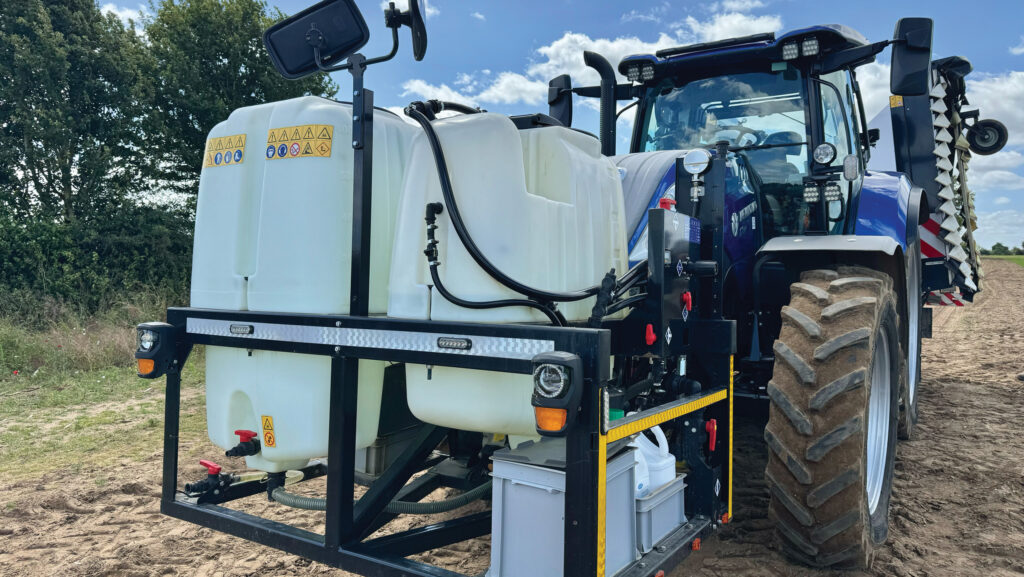
© MAG/Oliver Mark
Timed applications
According to VCS, one of the perks of a spot-spraying system that uses far less chemicals is that applications can be proactive rather than reactive.
Unlike conventional fence-to-fence sprays timed to hit as many weeds as possible, the drastically lower cost of applications allows owners to make planned, periodical passes with the Ara.
As a result, growers should have cleaner fields, less disease ingress, and healthier plants that aren’t inhibited by regular doses of herbicide.
This approach may also reduce workloads, particularly for contractors who, rather than racing between fields during peak seasons, might have the luxury of planning spraying work to fit with their schedule.