Amazone, Claas and AgXeed team up for driverless tech
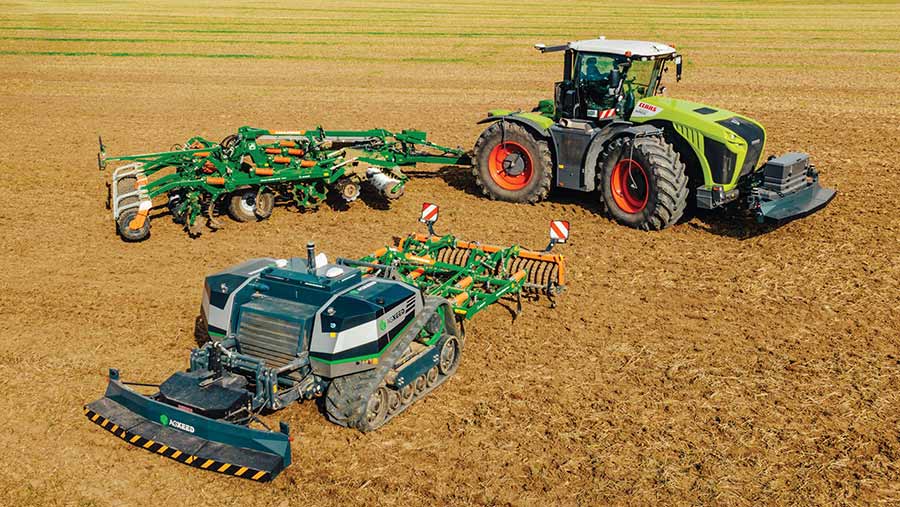
Next-level planning, control and remote monitoring systems for driverless machines and tractors are being developed by a new consortium of companies.
Implement manufacturer Amazone, tractor maker Claas and the driverless tractor pioneer AgXeed – in which the former two have minority investments – have formed 3A (Advanced Automation & Autonomy) to combine their respective expertise.
They are keen to have others join their group.
See also:Â Driverless tractors: Which manufacturer is leading the race?
They recognise that for higher levels of automation than are currently available, implements and power units need to operate as an integrated system.
They must be able to monitor the work they are doing and react accordingly through, for example, automated operation of hydraulic valves and three-point linkage.
In addition to paving the way for “intelligent” operation of driverless machines, the companies believe such technologies would be helpful in relieving the workload of on-board operators, and enable unskilled staff to achieve the best outcomes in field work.
The first fruits of the partners’ work are software products that connect tractors and implements to the work planning and implementation processes through isobus.
Amazone AutoTill for cultivators such as the Cenio heavy tine and Ceus disc and tine units can, for example, automatically detect when there is a risk of clogging and sends instructions to the tractor to adjust the working depth and/or speed accordingly.
Claas Autonomy Connect, meanwhile, provides the interface for the implement’s monitoring inputs and handles the task plan, which can be prepared in the Claas FMIS (farm management information system), or in the AgXeed portal when the Amazone cultivators are used with an AgBot.
Performance monitoring
A fourth manufacturer, vegetation control equipment specialist Muthing, is trialling a mulcher loaded with sensors.
Its aim is to monitor the output and temperature of its electric drive, alongside slip and speed fluctuations of the rotor belt drive and levels of vibration – which, if excessive, could highlight a blade-damaging impact.
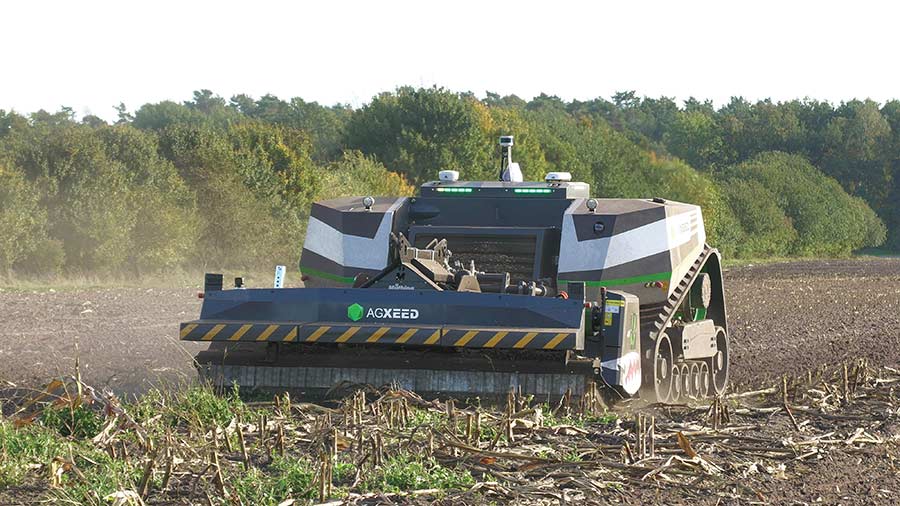
The sensor-equipped Müthing mulcher on an AgXeed AgBot © AgBot
The machine, which has so far worked across some 700ha on an AgBot since last autumn, is also equipped with a data recording control unit and uses 3A principles for communication between the mulcher and driverless vehicle.
Further development will enable the machine to regulate the AgBot’s ground speed to account for variations in load.