Farm bags a bargain by rebuilding self-propelled umbilical setup
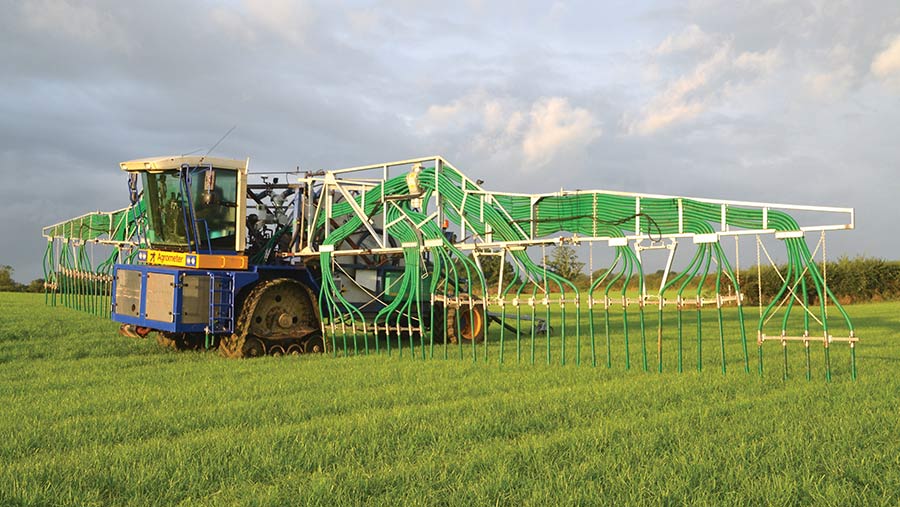
Umbilical slurry application might be a great tool to make the most of slurry nutrients while limiting compaction, but it can also be painfully time-consuming.
Somerset contractor Matthew Targett believes that in relatively small fields, more than 50% of the hours worked by an umbilical gang are spent setting up and then packing away the pumps, hoses and spreading kit.
Having run these systems for some 25 years to serve both their own dairy and some customers, the Targetts are experienced in the plus points and pitfalls of such an arrangement.
See also: 5 home-built pieces of slurry kit which improved efficiency
Vital stats – Targett Agrometer Pioneer 2001
- Year 2001
- Hours 9,150 hours
- Engine 175hp, 6.8-litre John Deere six-cyl
- Transmission Hydrostatic Sauer Bibus with variable displacement pump and motor (was Claas Dominator hydro)
- Umbilical hose on reel 600m x 100mm (4in)
- Boom 24m dribble bar
- Macerators 2 x Vogelsang (was single Samson)
- Tracks and tyres Front – 750mm-wide Stocks H-Track; rear – Goodyear 750/50 R26s
Until recently, the business had run a 24m dribble bar, bought second-hand in 2018.
“To make any form of umbilical application work, we’ve found it is essential to have a man and machine on a hose humper, which in itself feels like an inefficiency.
“But, more critically, with hundreds of meters of narrow, blockage-prone pipework, having a boom applicator employed to spread slurry from sand cubicles meant lots of stoppage time and bucket-loads of patience – which can be in short supply around here,” says Matthew.
To overcome that issue, a used McLanahan separator was procured from the Netherlands for the Targetts’ own dairy.
Immediately doing away with the issues of blockages and premature pump wear, it suddenly opened up a whole raft of spreading options.
“We had an opportunity to totally alter our approach to slurry management and really make the most of its nutrient value.
But with more than half of the time our umbilical gang was out being taken up in setting up and packing away the kit, there was still a massive inefficiency in the operation – we needed to radically alter the way we did things.”
While wandering the endless aisles of slurry kit at Agritechnica in 2019 an unusual machine caught his eye – a self-propelled umbilical rig built by Danish firm Agrometer.
With his interest piqued, he embarked on a research mission to see if it could provide the answer to his quest for greater efficiency.
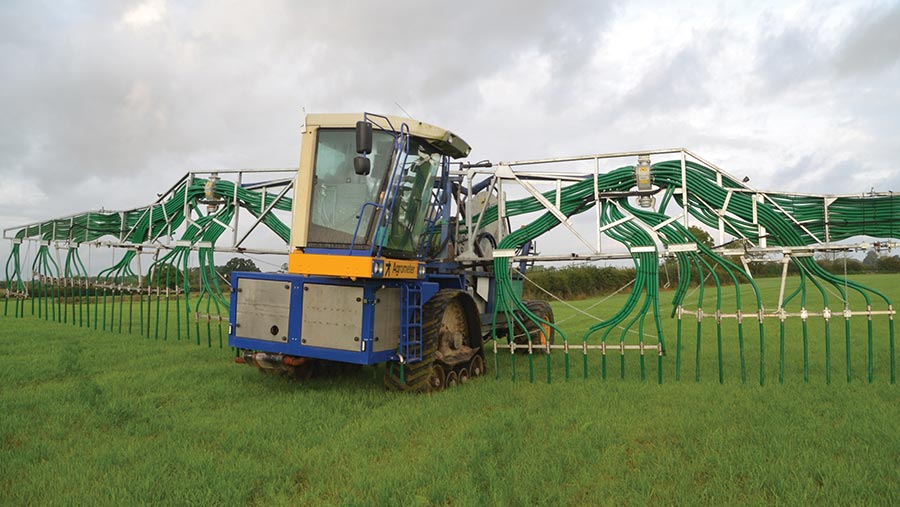
© Nick Fone
Why change?
“The 24m dribble bar we had before was a brilliant step on, allowing us to apply slurry to growing crops with many fewer wheelings.
“But with south Somerset’s small, awkward-shaped fields, quite often we couldn’t get into every corner, limiting the whole rig’s usefulness. And because of the time-consuming setup process, there was a temptation to overapply once you had the pipes reeled out.
“With its ability to spool out its own pipe and wind it back in again as it travels up and down the field, the Agrometer looked ideal. But then I saw the price…
“Up in the hundreds of thousands of pounds, the numbers being bandied about made the principle totally unviable for us, but I wasn’t prepared to give up,” says Matthew.
Business facts – Targett, near Castle Cary, Somerset
- Farmed area 500ha – 270ha grass, 130ha maize, 100ha winter wheat
- Livestock 500 Holstein milkers averaging 10,750 litres/year plus 500 followers
- Contracting Silage – grass 2,225ha, maize 283ha, wholecrop 40ha; baling – 10,000/year four and six stringers; combining – 400ha; drilling – 2,225ha; groundworks and building
- Machinery Tractors – Fendt 936, 930, 720 x2 and 718 x2, MF 7618 x2, JCB 4220 Fastrac; telehandlers – JCB Loadall 531-70, 532-70 and 532-60; shovel – JCB 435; forager – Krone Big X 780; combines – NH CX840 and CX760; balers – NH BB1290 and BB960; slurry – Agrometer Pioneer 2001 self-propelled umbilical rig
- Staff Matthew, Robert and Colin Targett plus 13 full-timers and another two to three part-time workers
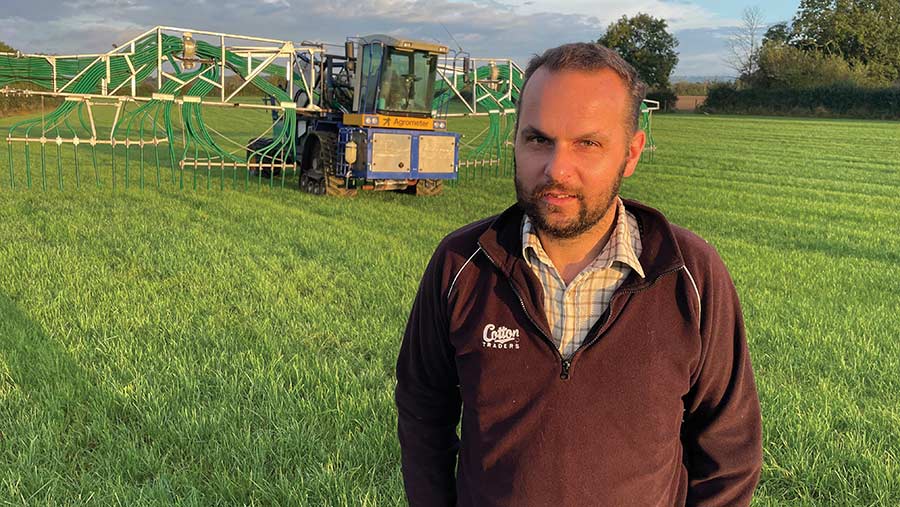
Matthew Targett © Nick Fone
Unafraid of buying well-worn second-hand kit, he started to scour the internet for used Agrometer machines and eventually found an 8,000-hour
Pioneer with a 24m dribble bar in northern Germany. Just £20,000 secured the unusual self-propelled spreader, a good chunk of which was funded by the sale of the existing 24m boom. But that was just the start of what was to become a long journey.
“It was advertised as being in working order and, to be fair, we drove it off the lorry and put it straight to work. However, that first day I immediately identified certain key weaknesses.
“Being the size of a large combine with just a steering rear axle meant it was a big, numb lump to move around our narrow lanes and through tight gateways. Long term it clearly wasn’t going to suit our work.”
With a few weeks in the seat that spring, Matthew had plenty of time to hatch a plan – a step-by-step modification programme that would see the 20-year-old machine receive a Trigger’s broom-style makeover, starting with a steerable front axle.
Modifications
Modification 1: Steering axle
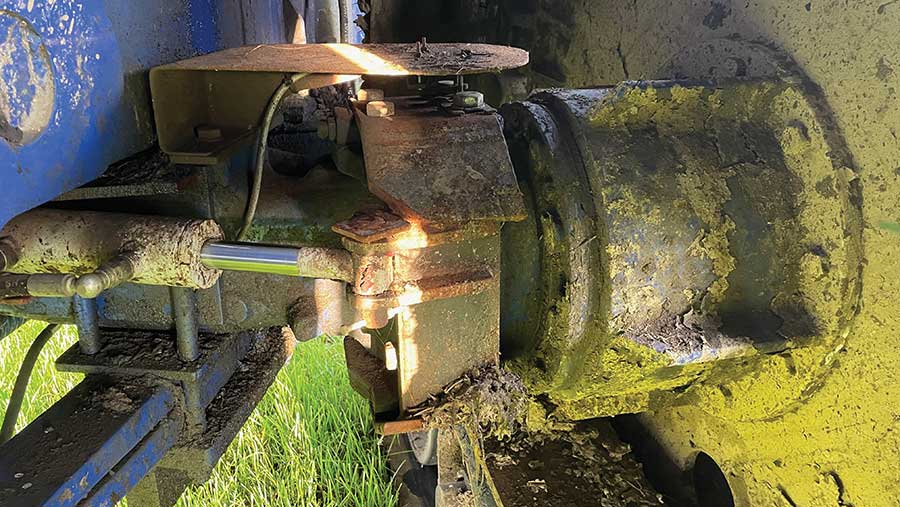
© Nick Fone
In addition to being able to point the big rig in the right direction, the new front beam needed to be equipped with proper brakes – the old Claas Dominator hydrostatic transmission was unable to exert enough stopping power when the 17t Pioneer got up to its 20kph top speed.
With steering and in-board anchors on the must-have list, Matthew ascertained the gearing ratio needed and from that was able to identify what axles might match the requirements. The choice was limited.
“There was one particular ZF axle that did everything we needed and, just by chance, Vicary Plant Spares had one from a burned-out machine.
“We took the plunge and handed over £3,000 – it was a punt. Once we’d removed the old beam and offered the new one up, we could see there was going to be quite a bit of extra work to make it work.”
Modification 2: Suspension
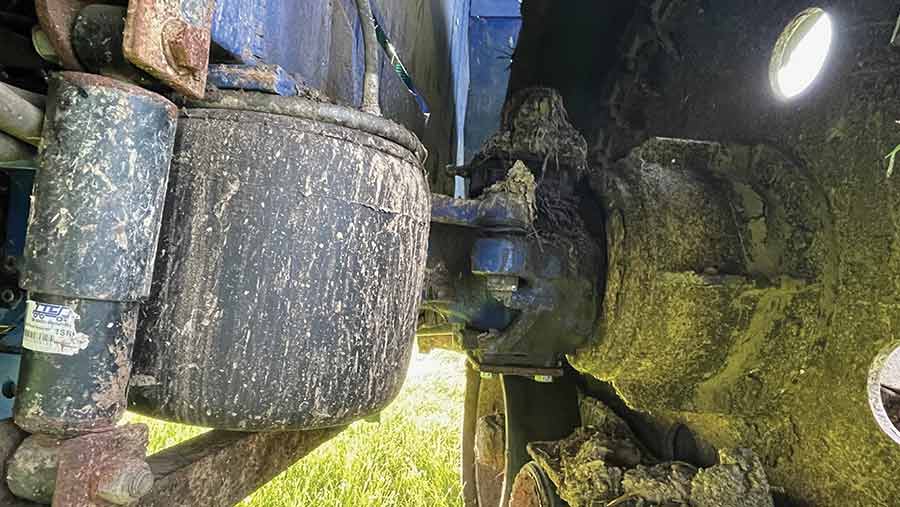
© Nick Fone
“From the start, I’d had the itch that I’d like to fit tracks, but doing that to an elderly machine without any suspension seemed harsh – we didn’t want it shaking itself to bits,” says Matthew.
The cheapest and most readily available option came in the form of a trailing arm and air bag arrangement from an old HGV low-loader, but incorporating it meant stretching the chassis and moving the engine bay forward.
Not an overly complex job, but it still took a couple of experienced pairs of hands two weeks to do between other tasks.
Modification 3: Tracks

© Nick Fone
With the urge to scratch the aforementioned itch, Matthew’s next job was to source a set of tracks.
Reasoning that something purpose-designed to be retrofitted would make for a straightforward installation, he looked at the various aftermarket options primarily destined for combines.
He eventually found a second-hand set of John Deere-branded H-Tracks for sale.
Originally developed by Leicestershire farmer Steve Heard, commercial versions of the green-and-yellow units were built by dual-wheel specialist Stocks.
They cost £5,000 and, with a set of hub spacers machined by a local engineer, they were bolted straight on to the ZF axle.
Modification 4: Steering setup
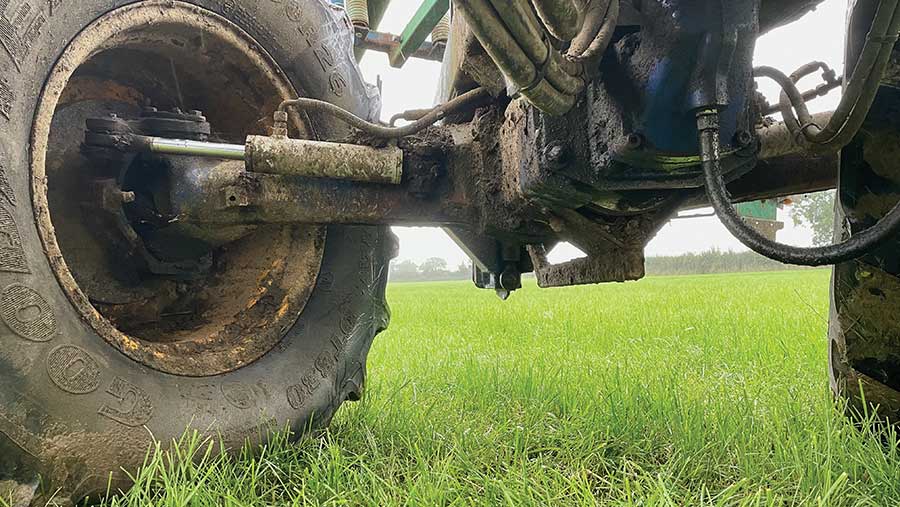
© Nick Fone
Getting the steering set up correctly proved one of the biggest challenges. Initially, a wheel angle sensor on the rear axle was employed to provide a control feed to the front.
But there was an issue – it quickly became apparent that the original steering system’s hydraulics couldn’t match the additional load exerted by the tracks’ bigger contact area.
Revised plumbing and pipework gave the front steering cylinders priority flow from the main orbital valve and an angle sensor up front controlling a spool valve for the rear wheels finished it off.
Modification 5: Transmission
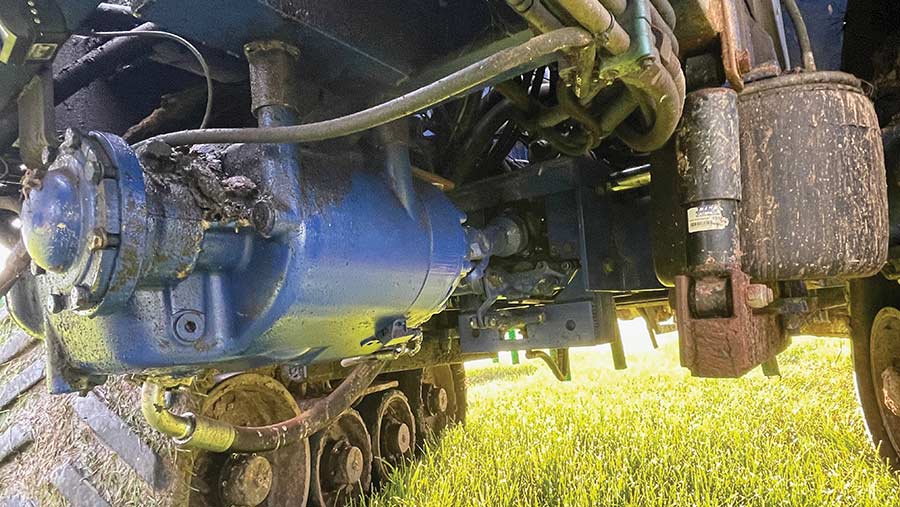
© Nick Fone
Limited in both power and torque, the original Claas Dominator hydrostatic driveline made the Agrometer painfully slow on the road and desperately underpowered in the field.
Having done his research, Matthew decided that it needed a more modern hydrostat employing both a variable-displacement pump and variable-displacement motor.
He found an unused unit from an unfinished engineering project for sale on eBay and, with no other bids lodged, he won it for a bargain £300.
Put together by German hydraulic specialist Sauer Bibus, at the engine end it employs the same Danfoss swash-plate used on New Holland’s flagship combines.
At the other end, a Walterscheid gearbox combines with a Danfoss swash-plate drive motor to provide propulsion to the front axle (similar to the setup used in certain Claas-branded telehandlers).
A secondary hydraulic feed off the side of the pump provides oil to the hydraulically driven rear beam, engaged simply with a solenoid valve activated by a switch in the cab.
With the drive lever handling pump output and a separate pedal to alter motor swash-plate angle, it’s now possible to control transmission speed and torque independently.
As well as removing the need for an additional three-speed range box as employed on the original Dominator hydrostat, the Agrometer can now travel faster (up to 25kph) – despite its somewhat tired 175hp John Deere engine being one of the few components as yet untouched.
Modification 6: Macerators
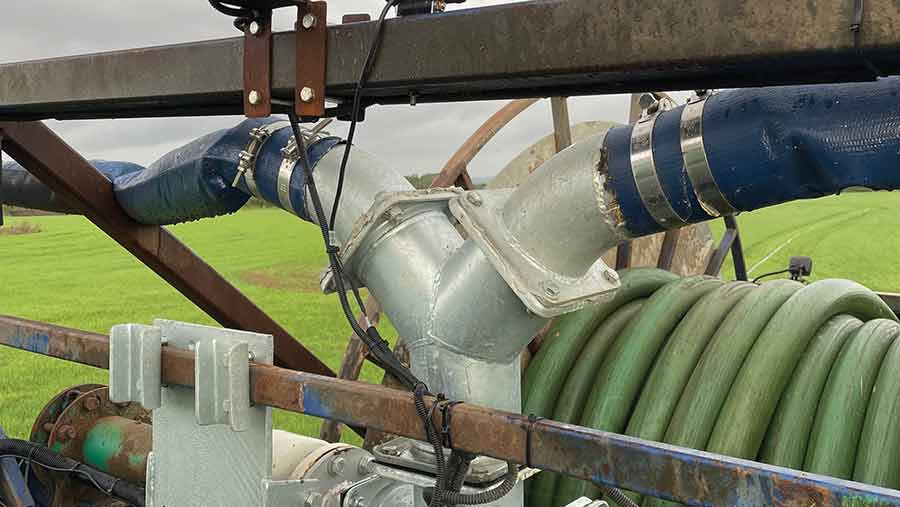
A simple Y-piece now splits slurry to the two Vogelsang macerators with a flow meter monitoring application rates and a Trimble receiver providing guidance © Nick Fone
When it arrived, the Agrometer had a single Samson macerator situated in the centre of its 24m boom.
That meant the 50mm-diameter pipework to the furthest outlets had to be in excess of 12m and would have to go round two bends – not exactly conducive to blockage-free flow.
To overcome the issue, two Vogelsang macerators were purchased and positioned in such a way that
each one handles half of the outlets, with a simple Y-piece in the 100mm pipework behind the reeler splitting the flow of liquid.
Although this was a simple fix, it’s an arrangement that relies on back pressure from the macerators to ensure an even flow and, to do that, it needed a consistent 100cu m/hour of feed from the lagoon pump.
That necessitated a switch to 150mm supply pipe. Having given more than 20 years’ service, the old 100mm umbilical hose was well worn and due for replacement anyway.
Because the Agrometer carries 600m of pipe on its own reeler and picks up and lays down as it goes along, rather than dragging it, pipe wear is minimal.
What has the project cost?
While the initial £20,000 laid out on the 8,000-hour Agrometer may have been relatively small compared with the purchase price of a new machine, the cost of the various modifications has not been insignificant.
The two macerators came in at £7,500, the H-Tracks cost £5,000 and the steering axle £3,000.
The transmission was a steal at £300, taking the overall outlay on heavy metal to just shy of £36,000.
Factor in the labour taken for the project – estimated to be approximately four months of work for two people – and you’re looking at a total bill of well north of £55,000.
Was it all worth it?
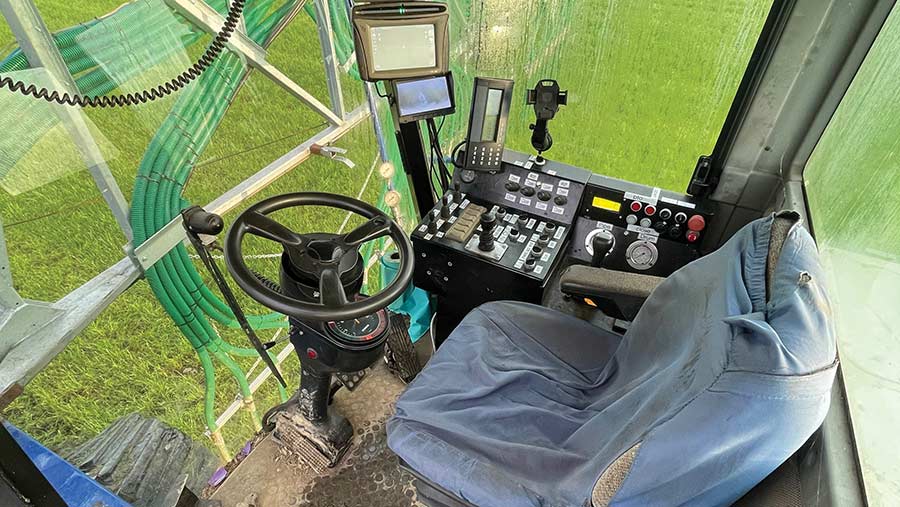
© Nick Fone
“Overall, the project has been a success, but it is by no means perfect,” says Matthew Targett.
“With its new transmission controls it’s a complex bit of kit to drive, so you can’t bung anyone on the seat.
“However, it has solved our primary goal of reducing the unproductive time taken setting out hoses and putting them away.
“We now just run a supply pipe to the field, bang some pegs in the ground and hook the Agrometer’s hose up.”
The way the Danish machine works is very different from any other umbilical setup. Initially, the operator unrolls a length of pipe from the gateway across the middle of the field, 90deg to the direction of travel.
Work then starts at the furthest point from the gate, the self-propelled unit running first to one end of a bout while feeding out hose. When it reaches the end the driver rotates the cab to face back the way they’ve just come and the reeler starts to haul the pipe back in.
In effect, the machine travels twice over the ground – up and back in its own wheelings. That means at any one time it’s only ever applying slurry at half rate, doubling it up to achieve the desired dose.
“The single biggest weakness of the Agrometer is that it covers the ground twice. That said, I’m convinced we’re still running across less area than we were with the spreading tractor and hose humper.
“But there’s still room for improvement. The reason for going to tracks was a good one in principle, as it spread our footprint without going too wide.
“At 750mm wide, we’re not running down nearly as much crop as we would have been with 900mm-wide tyres and we can stay afloat just about anywhere.
“Those tracks do take a lot of driving though, and they put an awful lot of strain on the steering. I wonder if we should look at swapping back to tyres.
“If we could find a big, tall tyre that had the same contact patch as a track, would it be more forgiving? I think we need to try a set of old 710/75 R42s to test the theory.”