County Down farm offers free mobile slurry separating – with a catch
The typical business model for a large, mobile slurry separator is as follows: a contractor stumps up the cash to buy it and charges customers an hourly rate for the service.
But BH Estates, based in County Down, is aiming for an entirely different approach – separate the slurry for free, providing farmers give up the removed solids.
See also: NI farm transforms slurry and food waste into bio-LNG fuel
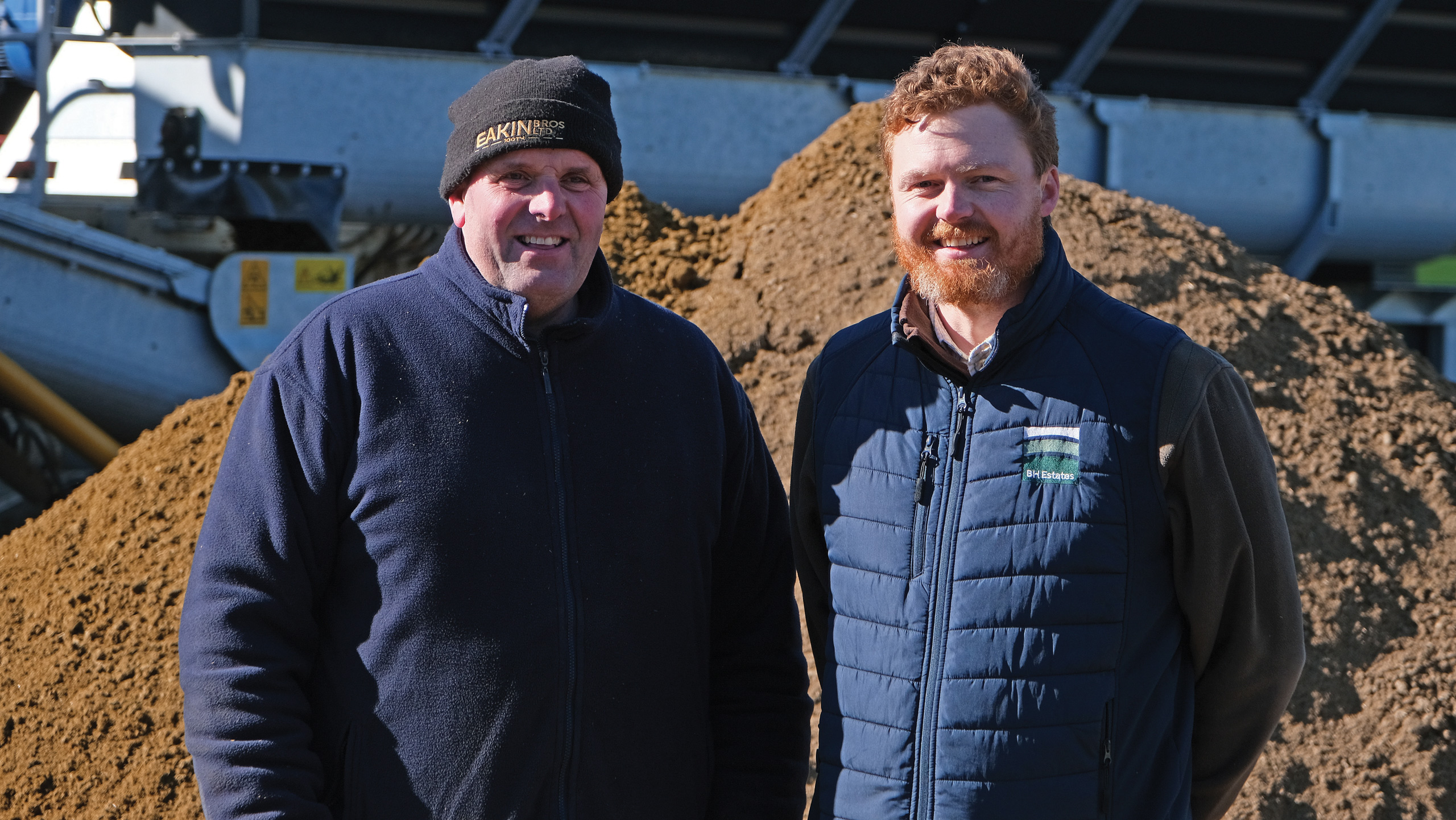
Ivor Lowery and Jack Blakiston-Houston © James Andrews
This fibrous material is then channelled through a 500kW anaerobic digester on the firm’s own farm (with a waste management licence), creating a credible feedstock that doesn’t require food-producing land to be taken out of production.
The duo behind the project is farm manager Ivor Lowry and managing director Jack Blakiston Houston who, in addition to overseeing the digester and a 350-cow dairy herd, runs his own chartered surveying business.
Keen to find more sustainable feedstocks for the plant, which primarily runs on grass silage and some local wastes, and aware of the need to improve nutrient management on many dairy farms, they hit on the idea of running a mobile separator.
This then led to them being awarded £4m funding from the Department of Agriculture, Environment and Rural Affairs (Daera) to run a three-year project to help reduce excess phosphorus from livestock slurry – the ultimate aim being to process the nutrients into an organo-mineral fertiliser on a large scale.
This is far wider than the farm’s own operation, but it has provided some financial assistance to get the service up and running.
Slootsmid SMS6
The separator they opted for is a high-capacity SMS6 mobile unit built by Dutch firm Slootsmid.
Despite the funding, BH Estates footed the entire bill for purchasing this; the hope being that the value of the feedstock produced will be sufficient for it to continue operating for free once the study is complete.
As the name suggests, the SMS6 runs six individual FAN screw presses (augers surrounded by mesh screens), each of which has a theoretical maximum output of 100cu m/hour.
Together, these promise a prodigious work rate, but Jack wasn’t interested in throughput and believes it shouldn’t be the focus when discussing the merits of these machines.
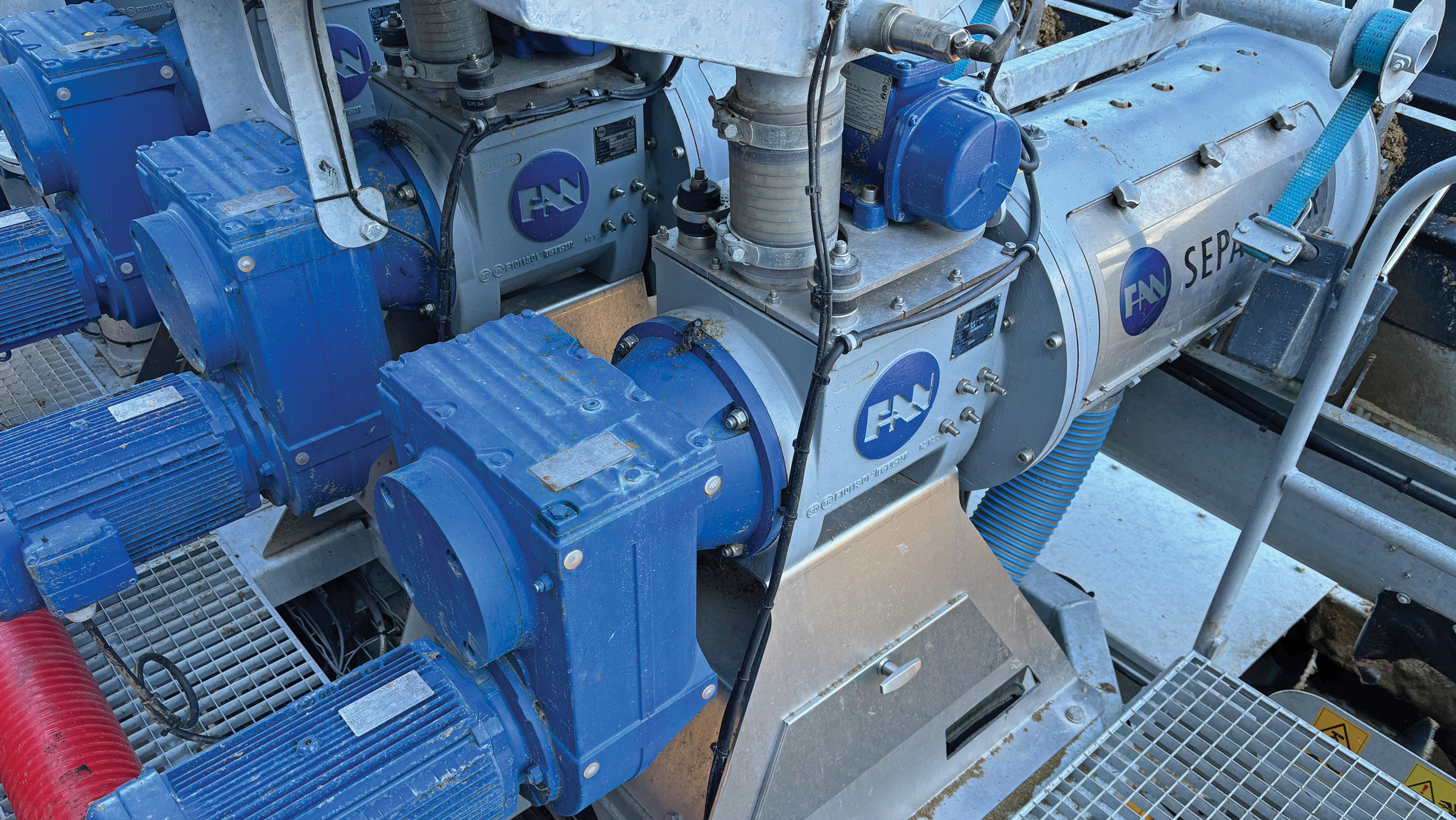
© James Andrews
“Maximum output figures are based on how much water a separator can process, so as soon as solids are involved this is going to be significantly lower.”
Instead, he suggests more weight should be placed on how effective they are at extracting liquid and producing solids with as high a dry matter content as possible.
“We set a minimum dry matter content of 25%, which is basically dry enough that you shouldn’t be able to squeeze out any liquid when you grab a handful, but the machine is capable of going up to 32%.”
The primary driver for pushing up this percentage, in BH Estates’ case at least, is that dry solids produce significantly more gas when fed into an anaerobic digester.
So much so that they can warrant running the machine well below its peak output in order to achieve maximum solid extraction, sometimes as low as 50cu m/hour.
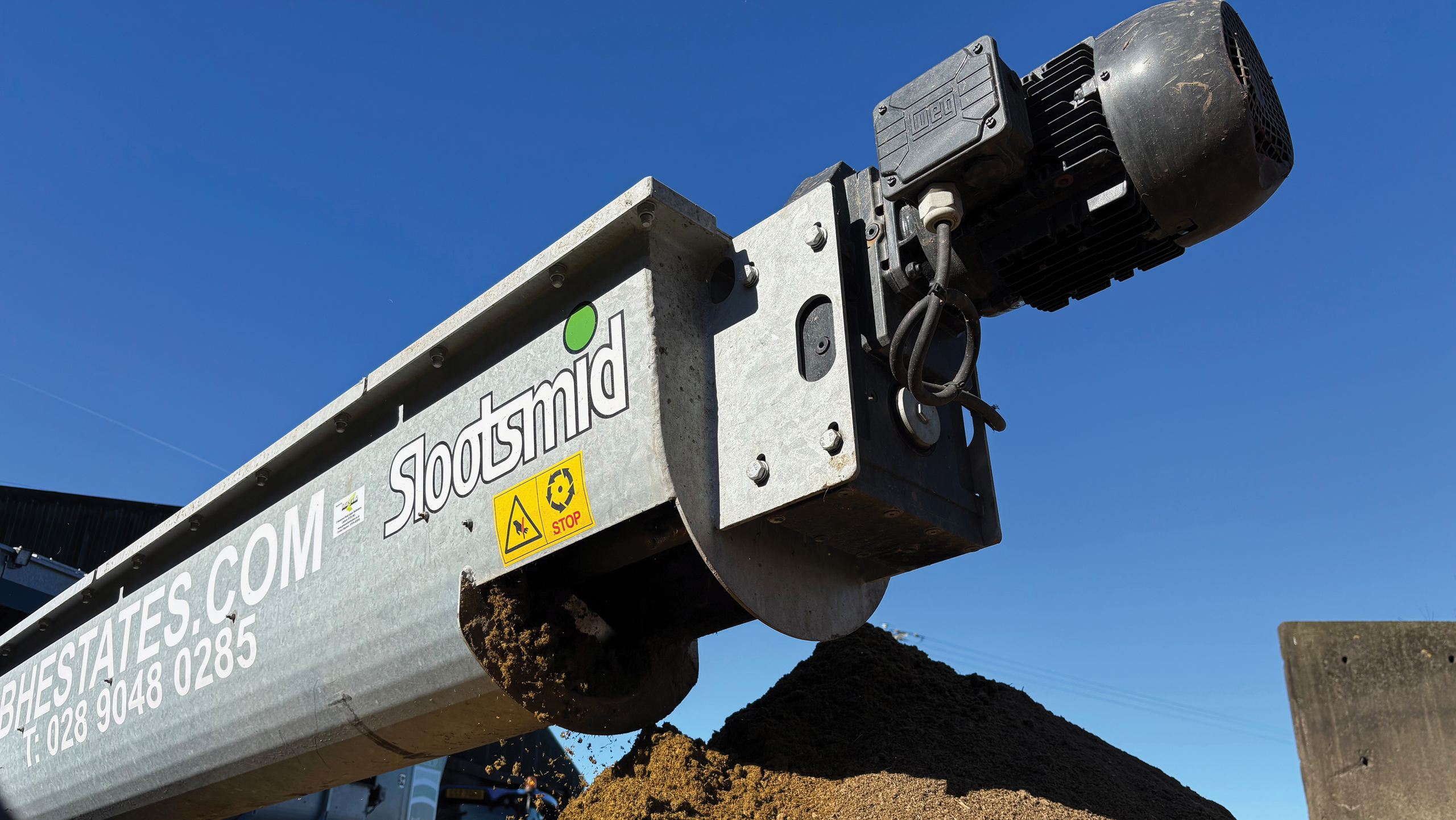
© James Andrews
Nutrient management
So far, there has been no shortage of customers, all of which are willing to hand over the solids in return for the service.
According to Jack, about 10% of these are motivated by nutrient reduction to prevent leaching or overloading their land and 20% are keen to free up storage space.
But the majority put greatest value on having higher-quality separated slurry which is both easier to spread and offers more efficient uptake of nutrients. Plus, there’s no risk of slurry fibres being left on the surface to contaminate future silage cuts.
The flipside is that some nutrients are being shipped off the farm. Based on BH Estates’ nutrient database, which covers a range of different systems, this includes roughly 5.3kg of nitrogen, 2.1kg of phosphate and 3.9kg of potassium per tonne of solid removed.
For farms with excess nutrients, this helps reduce their loading and make better use of the nutrients they do apply, but for others there is a reduction in the amount of nutrition they’re putting back into the soil.
In the case of the Daera-funded project, this work is showing some merit for mechanical separators as a means of reducing nutrient loading.
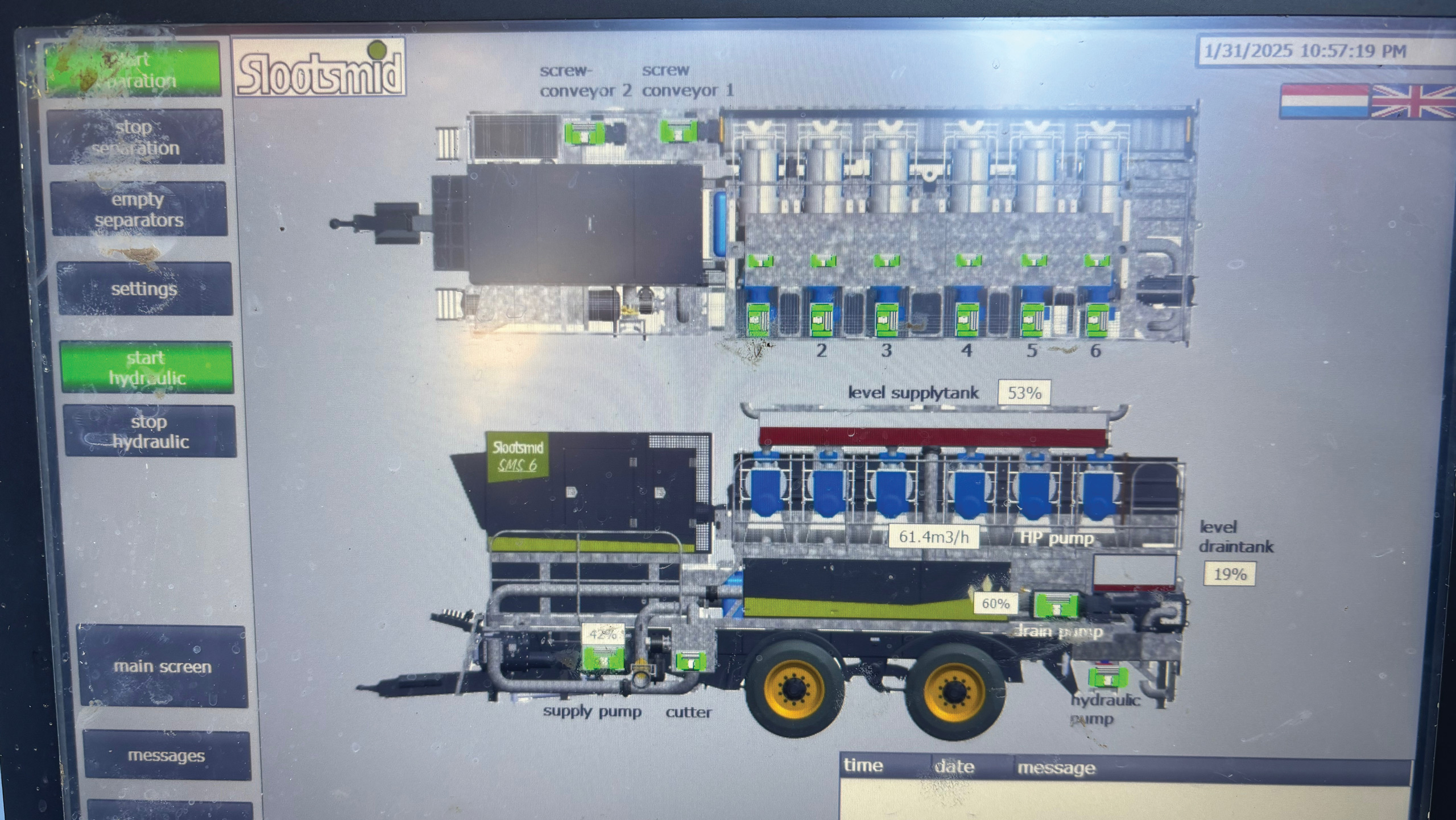
© James Andrews
How it works
Each of the SMS6’s screw presses has its own electric motor which, like all functions on the machine, is powered by a 165kVA three-phase generator.
This unit is overkill once the machine is up and running, but the extra power is needed to take the strain when all motors start up at once.
Slurry is pumped in via a macerator and stone separator, which chops up or removes any foreign objects, before it’s routed into a large buffer tank mounted above the separators – a bit like a header tank in a central heating system.
Slurry runs into each of the units by gravity and the machine’s control system maintains the flow by ensuring the level in the buffer vessel never drops below 55%.
Dry matter adjustment is achieved by opening or closing flaps on the end of each screw press – the tighter these are shut, the longer the slurry is held in the presses and the more it is squeezed.
Altering each of these manually would be a time-consuming affair, so Slootsmid built an electronically activated linkage that allows all to be controlled together.
As liquid is purged from the slurry, it trickles into a communal collecting tank, before another pump sends it to a separate store or back to the one it is drawing out of.
Cleverly, the pumps feeding the buffer tank and the one drawing out of the drain tank can communicate so there’s no risk of it either running dry or overflowing.
Plus, this allows the machine to automatically alter its work rate as it draws in slurry of varying consistency.
As for the solids, these drop out of the end of each separator into a collecting auger that transfers it to a large diameter unloading auger. This is hydraulically adjustable, allowing it to be positioned over a trailer or to discharge directly onto a yard.
All of the SMS6’s functions are controlled via a touchscreen display positioned at ground level, making it easy to fine-tune the settings and monitor performance.
Also included on the machine is a clean water tank and pressure washer for cleaning down, which can be used with disinfectant.

© James Andrews
Reliable so far
In four months of ownership the SMS6 has processed some 30,000cu m of slurry across 44 farms and has given very few problems.
The only hiccups have been a few foreign objects getting stuck in the multi-blade macerator. “It’s very tough and will chew through most stuff, but we have had it jam up with lengths of slurry scraper rope – on one occasion it had to be burned out with a blowtorch,” says Jack.
Another unforeseen problem is that the ultra-dry solids can blow away in high winds when being discharged from the auger.
To combat this, they have ordered a sock to go on the end, just like you’d find on a combine spout.
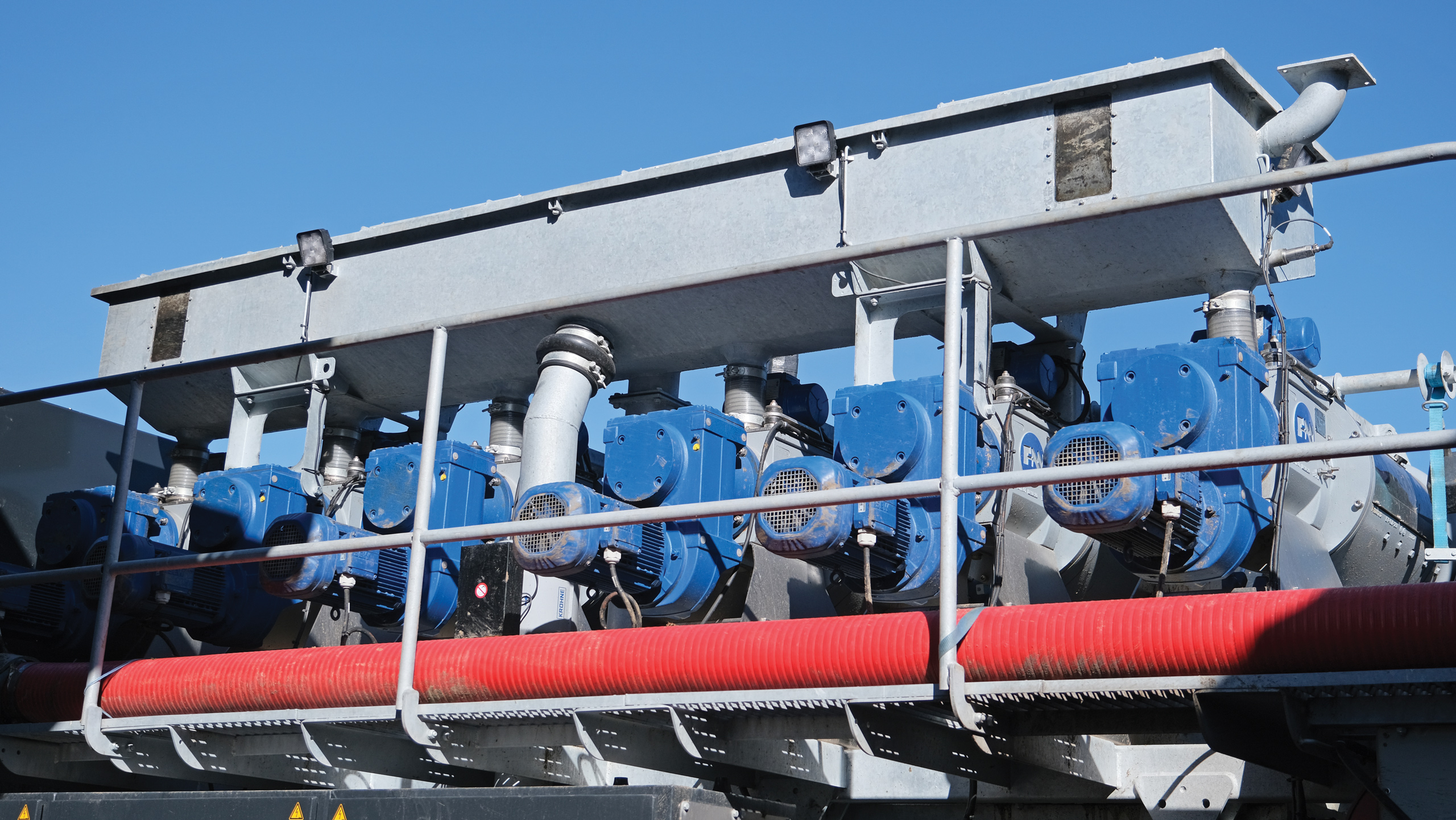
© James Andrews
Viability
Jack is assessing the viability of the system to determine whether they will be able to continue offering it as a free service.
Several factors will play into this, such as how many tonnes the separator can process per year, how much it costs to run and how fast it depreciates in value.
Haulage costs are another consideration, which are affected by the quality of the solids produced. For example, the higher the gas potential of each tonne, the lower these costs will be.
It’s still early days, but the basic stats look promising. “Our working assumptions indicate that one tonne of separated solids is equivalent to 0.75t of grass silage in terms of gas yield,” says Jack.
“So as long as the process doesn’t cost more than growing, harvesting and clamping that amount of crop, it should stack up.”
Slootsmid machines are imported to the UK and Ireland by County Antrim dealer Genesis Distribution and the current price for an SMS6 machine is £480,000.