Contractors build blackgrass-beating 24m weed wiper
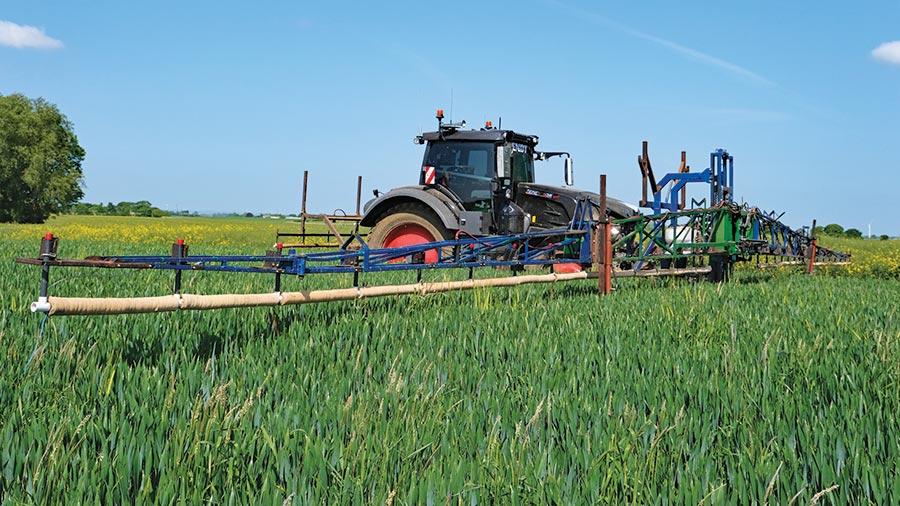
Unable to get the upper hand on rampaging blackgrass using conventional means, East Yorkshire growers Andrew and Michael Richardson went on the hunt for a more extreme method of control.
One of the tools that piqued their interest was Zurn’s seed-harvesting Top Cut Collect, but having had a demonstration, they deemed it to be too complex and prohibitively expensive.
They then came across the idea of an arable-scale weed wiper that would deliver a targeted dose of glyphosate to blackgrass plants without causing significant damage to the crop.
“Our neighbour, Richard Sadler [a former FW Farm Inventions Competition entrant], built one a few years ago and we could see that he was getting good results,” says Andrew.
See also: Contractor invests in Zurn Top Cut Collect blackgrass harvester
“But we thought we could tweak the design to better suit our needs – the main one being to mount it at the front of the tractor to give the operator better visibility.”
The brothers could also see strong demand for arable-scale weed wiping as a contracting service, so they needed to make sure the machine was user-friendly and tough enough to cover large areas.
Construction was completed last summer and the tool was put straight to work.
The pair say they went through the crop a bit later than they would have liked, but they still managed to achieve an estimated 70% reduction in seed return.
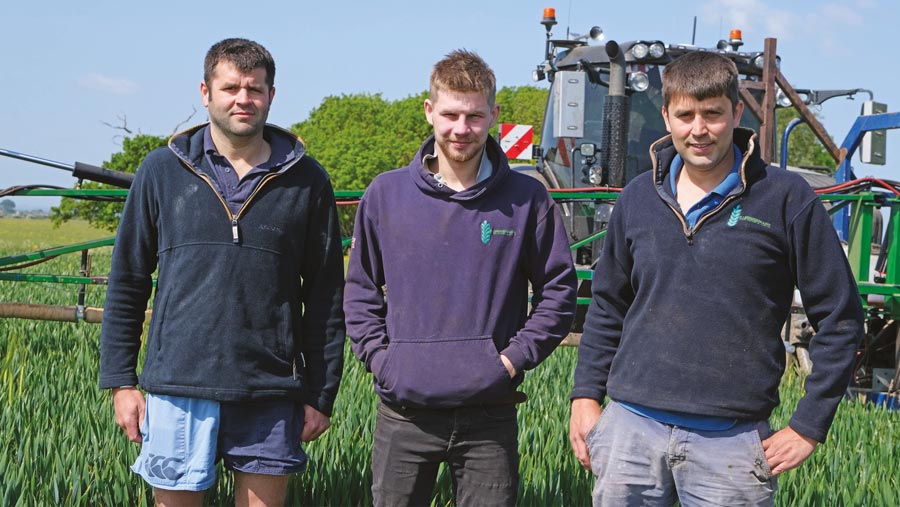
Andrew Richardson, Jordan Sizer and Michael Richardson © James Andrews
Part of this was down to the fact that each run receives a pass in both directions to maximise the chance of the sponges coming into contact with their target.
But they also carefully designed the boom so that it can run at just 30cm above the crop. “We’re never going to get the plants hiding down in the canopy, but we take most of them out,” says Andrew.
At this height, the risk of significant crop damage is minimal, but some small areas will inevitably be lost, particularly if the tramlines are uneven.
So far, the tool has been used on the Richardsons’ own 220ha arable enterprise near Hull and they’re rapidly building up contracting work as word has started to spread.
At the time of our visit in late May, it was already booked solid for a couple of weeks, with some of the work considerable distances from their yard.
Andrew admits that the weed wiper won’t solve the blackgrass problem alone, but he sees it as another valuable tool that should make a considerable difference over time.
The farm’s agronomist, Michael Hirst of Greenwold (Yorkshire), also rates it and estimates that herbicide expenditure could be reduced by 20-30% as it helps lower plant counts over the next few years.
Building it
The starting point for the project was an old Cleanacres 24m sprayer that had been languishing in the nettles on a nearby farm.
It was purchased for a princely £800 and stripped down so that just the main frame and boom were remaining.
As the rig was going to be front mounted, the middle section of nozzles was removed so that the tractor wouldn’t be driving though applied chemical and spreading it over the crop.
They then fashioned a simple frame for this to mount on the rear linkage, with the arms providing height control.
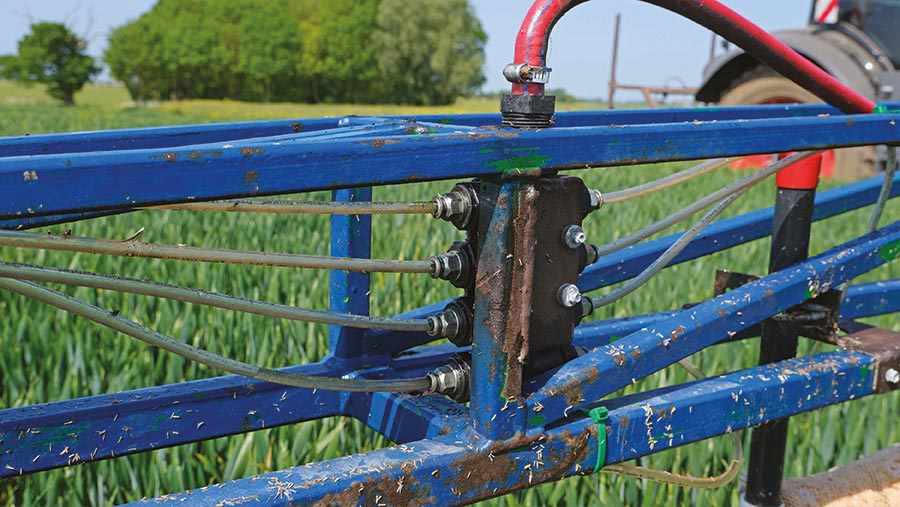
© James Andrews
One of the reasons the front boom can be run so close to the canopy is that the brothers fitted a pair of hydraulically adjustable legs to prevent it diving into the crop.
These are mounted in the centre of each wing, with each running on a narrow Vaderstad spring tine that supports the boom and provides a degree of suspension.
Operator Jordan Sizer has control of these using a pair of spool paddles on his Fendt 828, which he tweaks as he travels along the field.
Auto boom levelling was considered, but they soon ruled it out because it wouldn’t be able to read the terrain ahead and react fast enough.
As the boom was never designed to take the lateral stress caused by the legs, the pair also welded in several reinforcing braces to give it additional strength. However, it does still flex more than they would like.
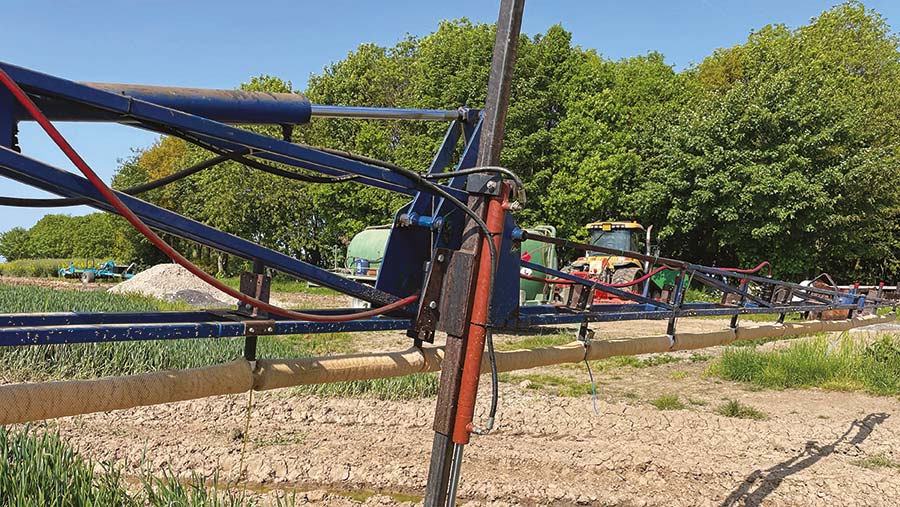
© James Andrews
Other adjustments to keep the boom hugging the ground include the original up/down and tilt functions, as well as positive and negative adjustment of the outer sections.
As these folded vertically originally, they were already capable of lifting independently, so just some minor modifications to the stops were required for them to drop below the line of the boom.
Operating these functions requires the services of all six of the tractor’s spool valves and there is a network of hydraulic lines to feed them.
“There was a lot of plumbing involved but thankfully we’ve got our own kit for making up pipes,” says Andrew.
Saturated sponges
For chemical application, they purchased a weed wiper kit with sponge rollers from the US at a cost of about £10,000, and this was adapted to fit on the underside of the boom.
Roller sections are fed by three 45-litre Fimco ATV sprayers – each featuring its own electric pump – with one supplying the rear-mounted boom and the other two feeding the left and right front wings.
Each is hooked up to a manifold that distributes chemical to the individual roller sections.
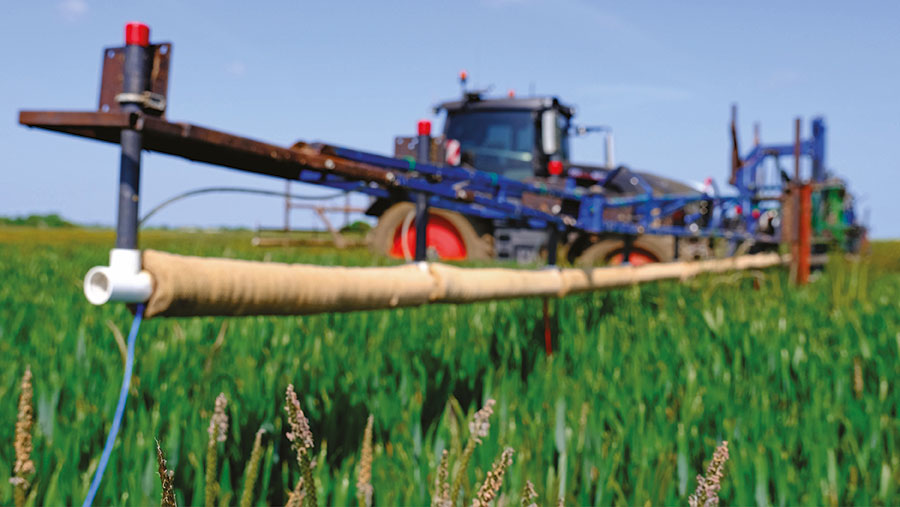
© James Andrews
The sprayers do not run continuously. Instead, they are switched on for just a short period before work starts until the sponges are saturated, but not dripping.
Jordan then keeps an eye on them and tops up the chemical before they dry out.
To avoid turning each sprayer on manually when priming the sponges, he has a simple control box in the cab with an on/off switch for each.
All in, the project cost about £20,000, which was a sensible amount for the work it does, says Andrew.
“It does a very specific job and we’ve only got a three- to four-week window in which we can use it, so it’s not worth investing in anything too expensive.”
Driving it
Because the boom is front mounted, Jordan has a good view of the task without having to crane his neck.
However, his hand is always poised over the spool paddles and joystick so that he can make constant adjustments.
Thankfully, the tractor runs on RTK guidance and because all the farms he visits drill using GPS he doesn’t have to worry about steering.
However, for anyone that’s working wider than 24m, he does have to make new wheel marks.
Working speeds of up to 9kph are possible on flat fields with an even crop, but 5kph is the average.
“I’ve generally been going slower this season than last as the tramlines are so rough due to the wet spring,” he says.
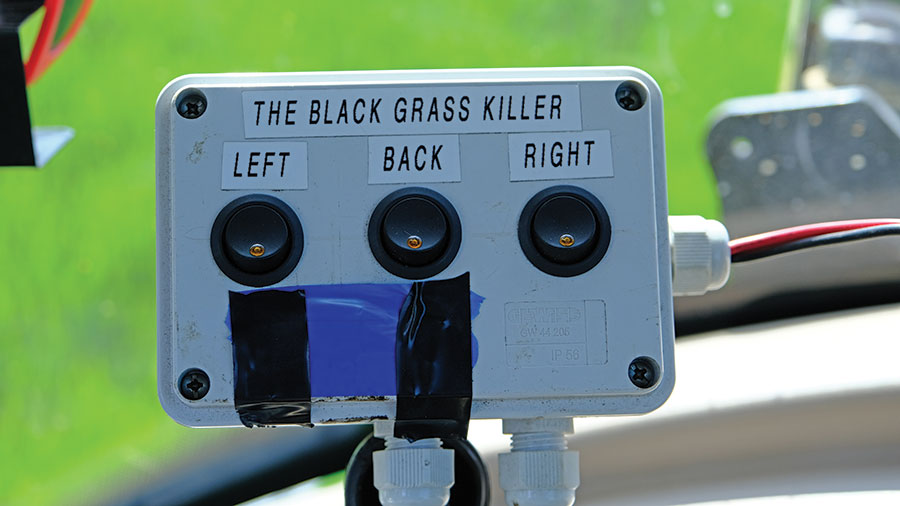
© James Andrews
As for timing, they aim to hit the blackgrass just before or during flowering.
This means most plants are likely to be tall enough to touch and there’s little chance of them having got to the stage of producing viable seed.
To maximise efficacy, only genuine Roundup products are used rather than the cheaper generic versions. Experience has shown that the 480g formulations have the most suitable viscosity for the application.
This year, the Richardsons are planning to do second and possibly third passes on their own crop to try and catch any plants that were too small during the first application.
Modifications
A list of modifications is already being drawn up for next season.
Chief among these is extra boom strengthening to make sure the tool stands the test of time, but there’s also talk of fitting an electro-hydraulic spool block.
This would allow all boom functions to be run off the tractor’s load-sensing hydraulic line, with just one electronic control box for Jordan to operate in the cab.
A bigger dilemma is whether they extend the boom to fit in with their new 32m tramlines.
This would add complexity, as they would still need to work at 24m for contacting work, plus it could well be too large to handle.
Currently, the thinking is that they will probably end up making a separate set of wheel marks.