Universal dribble bar reduces costs for slurry contractor
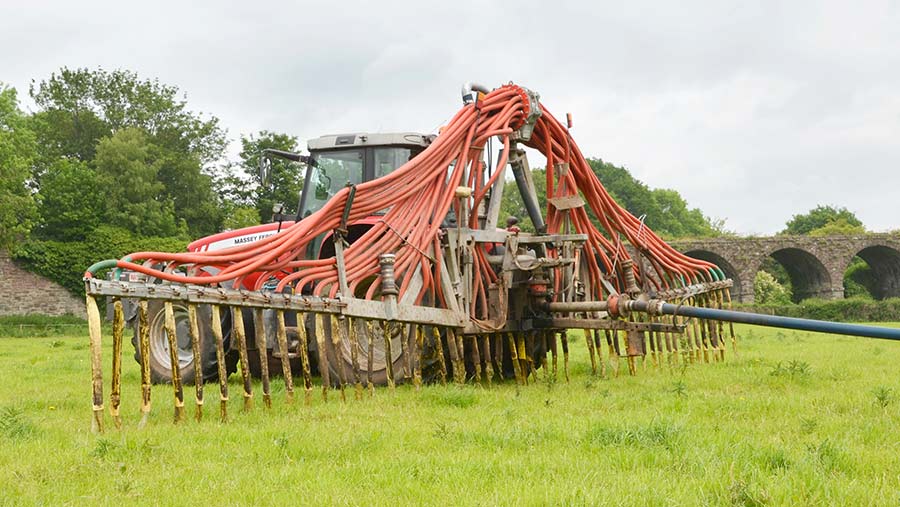
Contractor A&J Slurry has tried just about every brand of pump, reeler and spreading set-up going, but the firm thinks its latest dribble bar from Irish company Mastek has made the fleet close to ideal.
See also: Video: North Yorks contractor rates his high-tech slurry injection kit
Brothers André and John Cole spread about 400,000t/year and have been in the slurry game for the past 25 years.
The firm’s main spreading method is with umbilical systems, but having a tanker in its fleet can really benefit certain farms, as the lagoon isn’t always close by.
However, with a standard disc-injecting toolbar on the rear, uses for its existing tanker are limited when the customer doesn’t want to pay the additional cost for engaging metal, so having a system that can be taken on and off made sense.
Early days
“We started out initially as general agricultural contractors and almost accidentally ended up specialising in umbilical work.
To begin with, it was to fill the gaps between cuts of silage, or when the weather was bad, but it quickly became the mainstay of the business,” explains André.
“Our first machine was a single Spreadwise splash-plate setup, and within two years demand had grown to the point where we had to invest in a second system.
Pretty quickly we were looking at more efficient ways of applying the slurry – we liked the idea of dribble bars because of the limited surface contamination and reduction in smell and mess.”
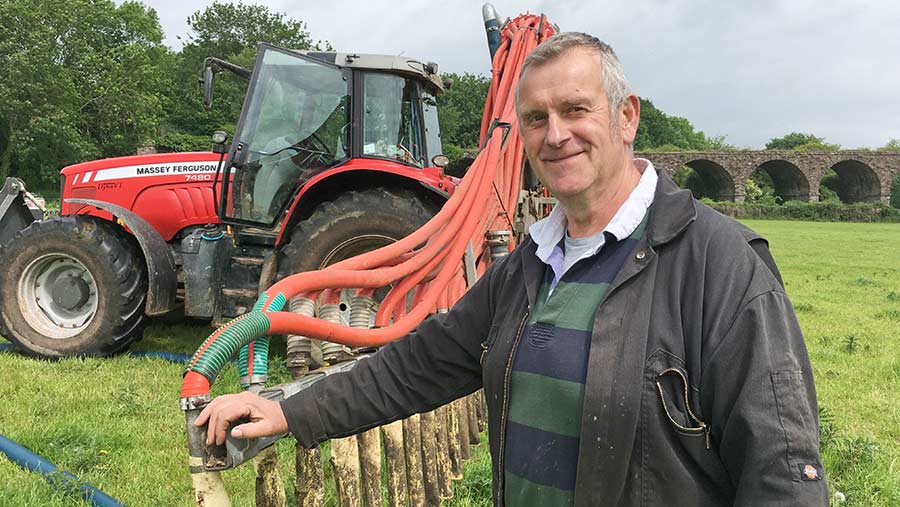
André Cole
Business facts: A&J Slurry Ltd, near Monmouth
- Work undertaken Umbilical slurry spreading and tanker application (400,000-450,000c m/year)
- Tractors MF 7718 & 7480, JCB 4220 Fastrac and 2 x NH T6.180s
- Slurry kit 2 x 12m Mastek dribble bars with Spreadwise umbilical systems and Bauer pumps; 11cu m Joskin tanker with 8m Mastek dribble bar; 2 x Mixit stirrers and GEA jetter
- Staff André and John Cole, plus two other full-time workers
With this in mind, the brothers invested in a 6m Spreadwise dribble bar – a setup also equipped with a splash-plate to allow for a thickening up in the liquid as the lagoon begins to empty.
Pretty quickly this became the tool of choice, with most customers choosing this as their preferred means of application over the basic splash plate, which prompted the purchase of a second rig, and a third soon followed. Both were 6m Spreadwise dribble bars.
“We saw the demand for umbilical work shift from being year-round to becoming much more biased towards the spring and summer,” explains André.
“The first and second setups each did about 15 years service, but farming had moved on and we needed to cover wider widths. We replaced them with two SlurryKat booms – a 7.5m and a 9m.”
These units carried out the work well, as long as they were looked after, but running them for more than 300 days a year wasn’t ideal and something a bit more robust was required to deal with the workload.
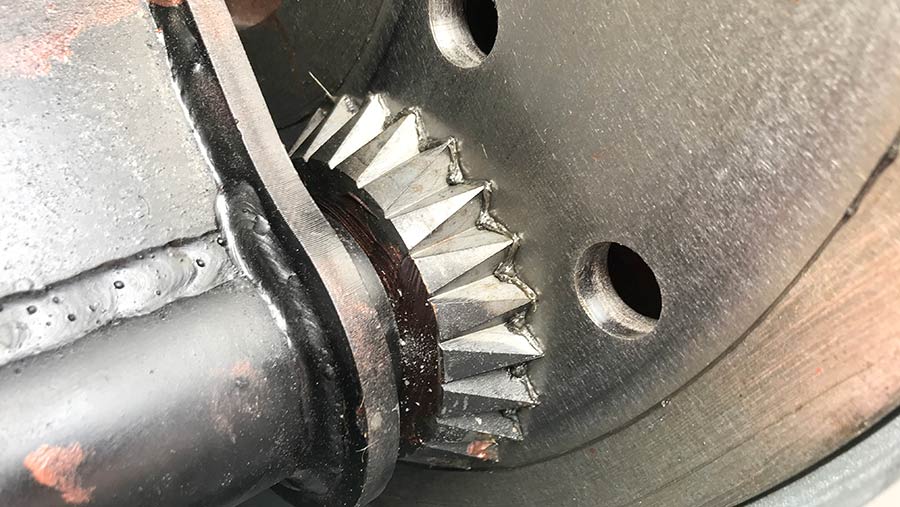
The internal workings of the macerator – serrated discs to shear off fibrous material as it exits the hose outlets
New approach
Keen to find out what was new on the market, the Coles started hunting at shows and kept being drawn to the unfamiliar Mastek brand.
The Irish firm’s dribble bars looked to have a much stronger build and, with the macerator mounted up high, the booms could fold tighter.
The pair were almost immediately sold on the concept and ended up putting their name down for a 10m rig.
“We liked the new dribble bar, but there was one major fault. The air intakes on Mastek’s own in-house-built macerator had a tendency to block and slurry wouldn’t get to the outer boom tips,” says André.
“To get around this, we changed to a Vogelsang macerator and ran it for a few years, but with extra demand for spreading on growing cereal crops, it quickly became apparent that we needed to look at a new rig to fit with the tramlines and avoid trampling crop.”
Wider boom
Rather than opting to go the whole hog and shell out for a 24m setup, the Coles swapped their first 10m for a 12m dribble bar.
They were concerned that a wider boom might not last the test of time, given the fatigue generated by constant whip and yaw.
A move to a 24m setup would also have necessitated a complete change of the business’ pipework – some 4,500m – swapping from 4in and 4.5in to 5in and 6in pipes.
After doing their sums, the brothers didn’t feel this level of investment could be justified when offset against the extra return it would generate.
The change to a 12m boom saw a return to Mastek’s own macerators – this time modified with vents on each pipe to avoid the issues with blockages.
“We took a close look at how Mastek had altered the design – it was clearly built to last much longer than anything else on the market.
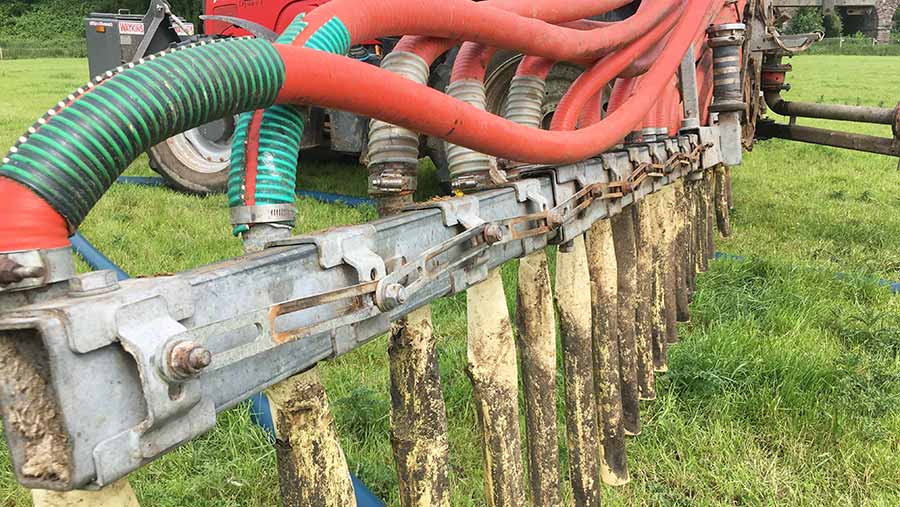
The telescopic boom sections use a simple yet clever linkage arrangement to pull the hoses out to the required spacing
It has circular rotating knives, which mean you don’t have to keep reversing it, and they stay much sharper,” says André.
It’s proved to be the right decision – after five years’ service they have been reliable and hardly required any maintenance.
The booms also come in for praise, as the brothers’ output has risen and it is easy to swap from arable to grassland work.
Universal bar
Having been convinced by Mastek’s design, last year the brothers invested in another of the Irish firm’s dribble bars – this time an 8m boom to fit on the rear of their 11cu m tanker.
The clever thing about the universal dribble bar is the ability to fit it to any type of tanker without the need for an additional linkage. Instead, it clamps onto the rear access hatch of the tanker in place of the normal rear door.
“We’d bought our tanker with a 3m disc injector, but we found it was so much slower and our customers weren’t prepared to pay extra for the service.
The running costs were also much higher, as all the discs had bearings,” says André.
“We didn’t want to just rely on a splash plate, but we also didn’t want to have the expense of changing the tanker just because we wanted a dribble bar. For about £9,000, the clamp on Mastek made perfect sense.”
It scores highly for its light weight compared with an injector, and by employing a single hydraulic service with an electronic diverter valve, it is impossible to fold the booms while the macerator is running, so it’ll never run dry.
“Although it’s not out every day, having the tanker on the fleet adds an extra element of flexibility – we can cater for the increasing number of larger dairy units with more ground away from the base.
“Over 90% of our customers are now converted to dribble bars because of the reduced smell and ammonia loss, and also because slurry is viewed as valuable fertiliser,” says André.
“And because of the reduced sward contamination, they can get the cows back out on the grass that much quicker. For us, they’ll remain the preferred method of application.”