Martin Desborough’s Tramspread and custom pumping trailers
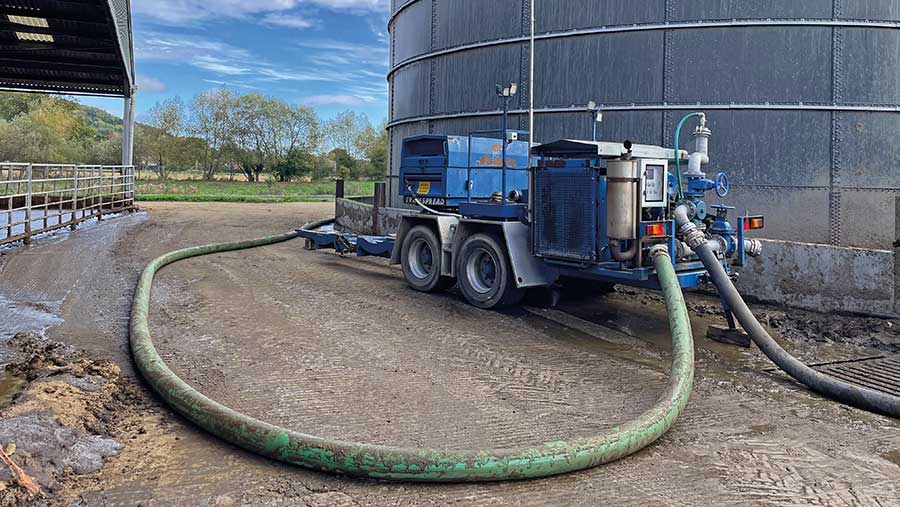
For the past three years, Herefordshire contractor Martin Desborough has been spreading slurry using a remote-controlled pumping trailer built by Suffolk firm Tramspread.
He purchased the 2015 model second-hand from a local contractor who was getting out of the umbilical game, complete with a reeler and two removable pipe spools that mount on the bed.
All in, the kit cost a considerable £50,000, but it gave him a self-contained pumping outfit that meant he could avoid putting hours on a tractor and keep his fuel use down.
See also: Expert advice on setting up the perfect umbilical slurry system
The only additional piece of equipment he needed to purchase was a dribble bar, which he borrowed from one of his tankers.
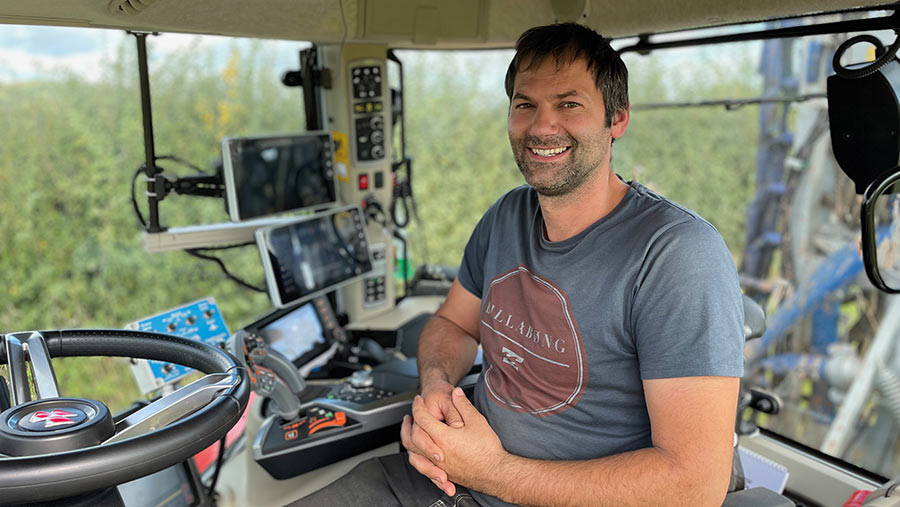
Martin Desborough © James Andrews
Initially, the trailer was controlled manually, so he had to take a member of staff with him to run the pump.
However, after just a month of use, he invested a further £10,000 in an SIL remote system with additional diverter valve and pipework, which he fitted himself.
Now he can travel to a job with the pumping trailer towed behind the dribble bar and the reeler mounted on the front linkage.
The only time he has to bring someone else with him is if he needs to stir the slurry.
The success of his first trailer, and the fact that he had some of the parts already in stock, prompted him to build a second unit without remote control.
This primarily gets used for double pumping, but can also step in if he needs to have two umbilical setups running at the same time.
Specs
Tramspread Contractor Trailer
- Engine 170hp FPT six-cylinder industrial
- Pump Bauer SX2000
- Compressor Atlas Copco
- Priming setup Honda engine with Bauer vacuum pump
- Flow control SIL remote-control system
- Cost £50,000 second hand, including pipe spools
Martin Desborough’s pumping trailer
- Engine 135hp Perkins 6354.4 six-cylinder turbo
- Pump Bauer SX2000
- Compressor CompAir
- Priming setup Honda engine with Bauer vacuum pump
- Flow control Gate valves
- Build cost £18,000
Tramspread trailer
The Tramspread Contractor Trailer sits on twin axles and has a 170hp FPT industrial engine mounted at the rear, running a Bauer SX2000 gearbox pump.
This will self-prime when connected to a tower store, but for lagoons it has a Honda petrol engine hooked to a small Bauer vacuum pump that pulls slurry through the system.
An Atlas Copco compressor is mounted in the centre for blowing out at the end of each job, and the front section has space for two spools of pipe – about 2,200m in total.
An additional spool can also be carried in the front linkage-mounted reeler.
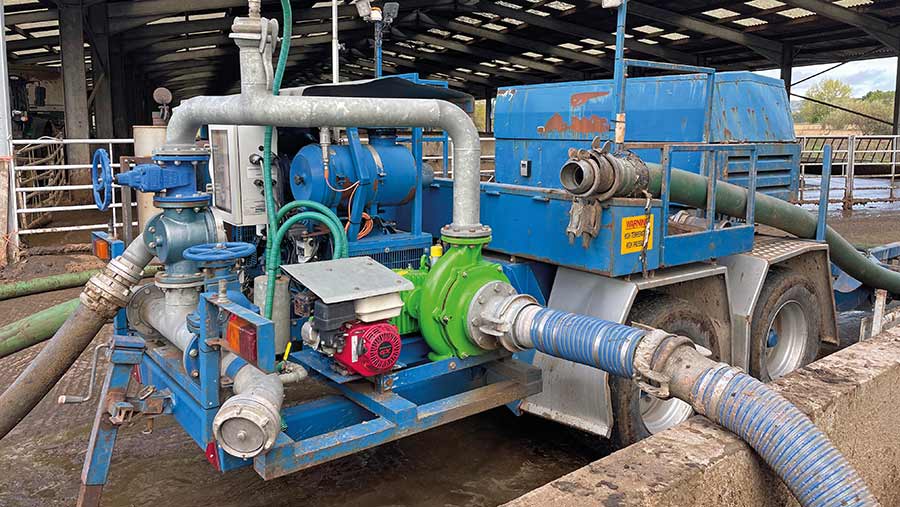
© James Andrews
Thanks to the remote system, all engine and compressor functions can be controlled via an LCD display in the tractor cab.
This works via a radio signal, allowing Mr Desborough to start and stop the engine, control the throttle and operate a diverter valve so that slurry will return to store, rather than flowing down the pipe to the dribble bar.
He can also run the compressor when the field is finished to blow the pipe clean before rolling it back up.
This usually has sufficient power to clean the pipe without him needing to push a sponge through.
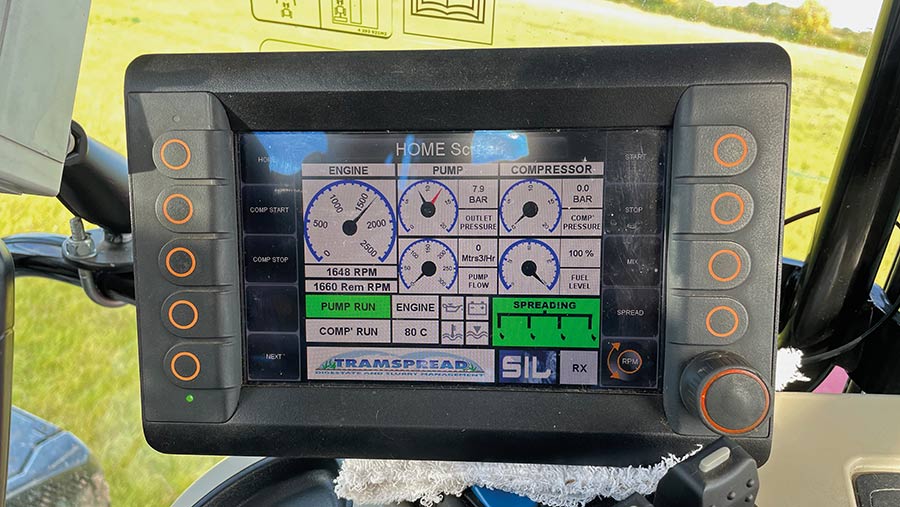
© James Andrews
Dribble bars
Mr Desborough’s first dribble bar was an 8m with single macerator made by engineer Dave Rea, but he has since upgraded to a 12m Tramspread version with double macerators, twin shut-offs and variable boom geometry.
This allows him to cover the ground quicker and avoid overlaps, as well as helping him keep the boom level on sloping ground to maintain an even distribution.
There is also a built-in flow meter, which feeds into his GPS system to produce application maps that can be downloaded and given to the customer.
For arable work, he has a 24m Tramspread dribble bar, also fitted with twin macerators and variable geometry.
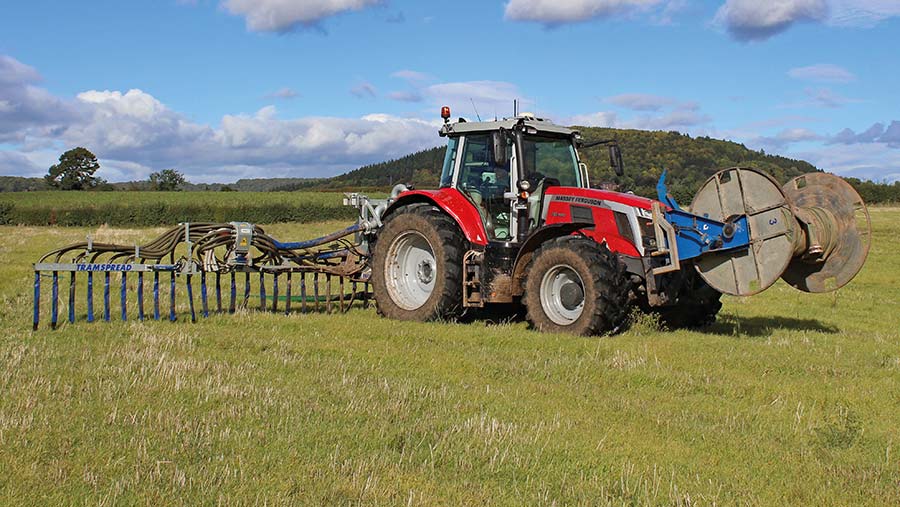
Pipework feeds a 12m Tramspread dribble bar with twin shut-offs and variable-geometry boom © James Andrews
Both are pulled by his 2022 Massey Ferguson 7S.190 with Dyna-VT transmission.
This came auto-steer ready, but he opted for a Topcon setup rather than the factory-fit option as it offered more scope for monitoring and recording the slurry operation.
Using it
As well as making slurry spreading a one-man job, the trailer has stopped him putting hours on another tractor and saved a considerable amount of fuel.
This is because the driveline from the engine to the pump is so much more efficient than running through a tractor transmission.
Performance has been good, but the gearbox on the original pump did pack up a month into his ownership, landing him with a bill of more than £5,000 to replace it.
The original Honda priming pump engine also started playing up at a busy time, so he bought another to sit in its place.
Other than that, it’s been trouble free and the remote system works well, even in hilly areas.
Due to its constant exposure to corrosive slurry, rust is starting to break through the paintwork, so it would benefit from a touch-up.
Mr Desborough is also considering adding an additional flow meter on the pump itself.
Any discrepancy between this and the flow meter on the dribble bar will show if there are any leaks in the pipe run.
Second trailer
Thanks to some of his customers requiring slurry to be pumped over longer distances, Mr Desborough decided to invest in a second pumping trailer.
However, rather than buy a new one, he set about putting one together himself.
This was made simple by the fact that he had many components in his possession already, thanks largely to modifications made to the original trailer.
This included a Murphy engine control unit, a pump with broken gearbox, most of the pipework and a Honda engine that was difficult to start.
He began by sourcing a second-hand Perkins 6354.4 turbo engine from a Massey 525 combine that had been abandoned in a field.
It was on just 2,500 hours and he paid £800, having been assured it was a good runner.
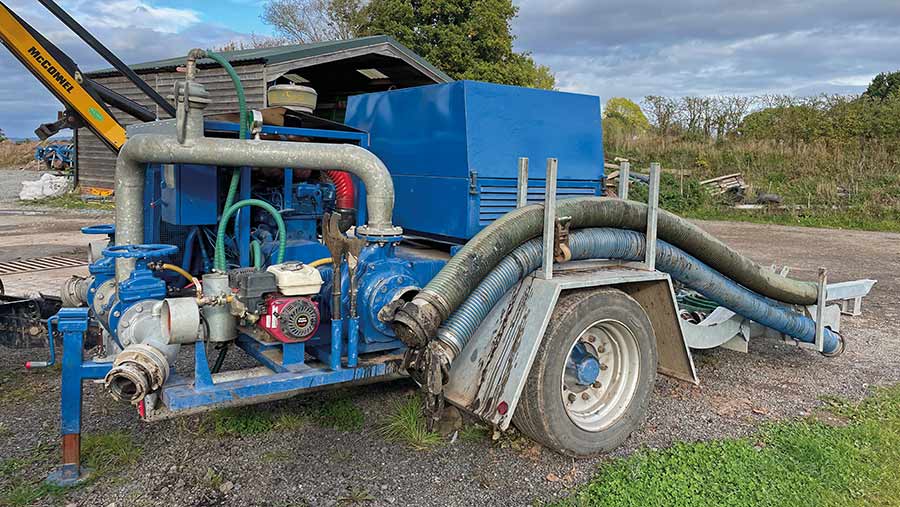
Martin Desborough made use of existing components to assemble his second pumping trailer © James Andrews
Tramspread used these engines in some of its earlier pumping trailers, so he knew the Murphy control system would be simple to connect to it.
The only significant modification was to replace the cable stop with an electric one. It was also treated to a new radiator, exhaust and custom-made fuel tank.
Much of the trailer’s construction was put in the hands of local mechanic Dave Rea.
He built the chassis up on a single lorry trailer axle and fabricated twin pipe spool holders on the front, in a similar fashion to the Tramspread.
Once completed, the chassis was galvanised to protect it against corrosion at a cost of about £1,700.
As for the pump, Mr Desborough got hold of a worn-out example with a good gearbox and asked a local engineer to make one good unit out of the two.
He also got his original Honda engine running by fitting it with a new carburettor.
A CompAir road compressor was sourced on eBay for about £2,500 and this was hooked up to the same fuel tank feeding the Perkins engine. All in, the build came to about £18,000.