Contractor customises UK’s first Borger slurry separator
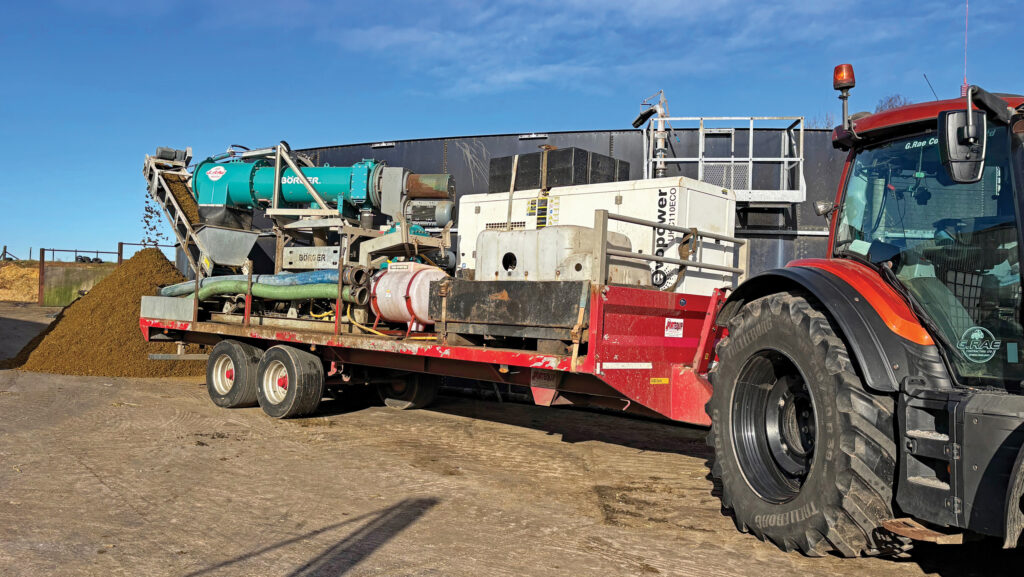
Several contractors are running trailer-mounted Borger RC150 separators these days, but Lockerbie-based Andy Rae was the first to do so in the UK.
Having pumped, hauled and spread millions of gallons of slurry over the years, he hatched a plan to incorporate high-speed mobile separation into his list of services.
See also: Farm bags a bargain by rebuilding self-propelled umbilical setup
The main appeal was the creation of a better quality fertiliser with nutrients more readily available to the grass.
But it would also allow his customers to free up valuable storage space, as well as prevent fibres being brought back into clamps during silage making.
As for the removed solid component, this could be applied with a conventional muckspreader at times closed to slurry application or used as a feedstock for an anaerobic digester.
Unlike existing mobile setups that would sit on farms for extended periods, he sought a machine that could rock up and process 1,000cu m or more in a sensible working day.
Not only would this be more efficient, but it would allow an operator to stay on-site to make sure the job was being done properly.
One option was to buy a machine housing multiple small screw presses, but the RC150 offered similar output in just a single unit and looked like a more cost-effective option.
Plus, it could be purchased mounted in a neat, galvanised frame with all ancillaries connected and run through high-tech control system.
Andy Rae’s mobile Borger RC150 specs
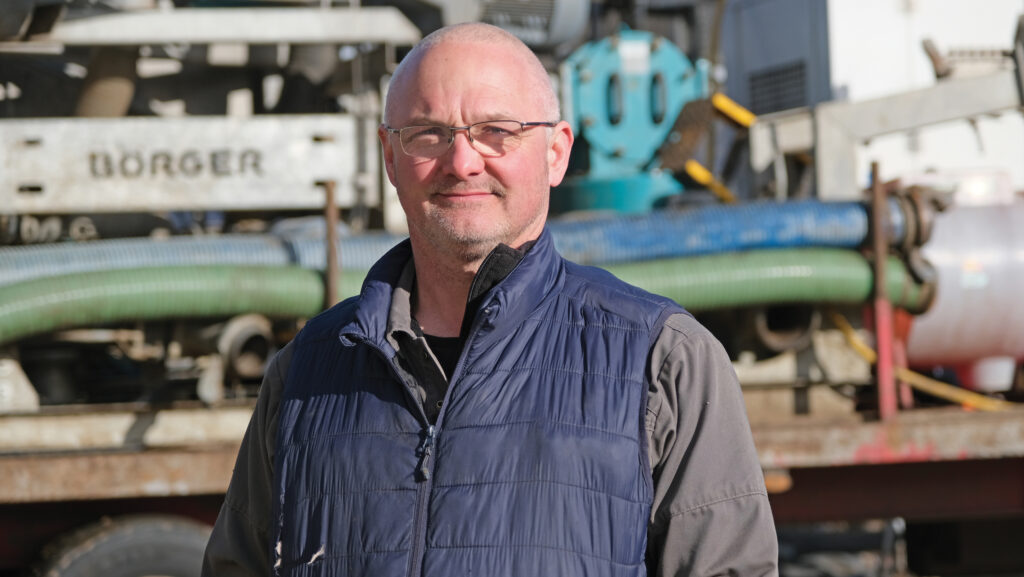
Andy Rae © James Andrews
- Separator Borger RC150
- Generator Evopower 110kVA
- Trailer 26ft Portequip flatbed
- Compressor 130cfm Atlas Copco
- Clean water tank 400-litre Enduramaxx
Making it mobile
The only problem was that it was designed for static installations, primarily next to large anaerobic digesters, where it could be hooked up to a three-phase electricity supply.
Inspired by the efforts of contractors on the Continent, he mounted it on a 26ft Portequip bale trailer, along with a 110kVA generator that would provide sufficient current to run the separator’s six motors.
While he was at it, he added a 130cfm Atlas Copco compressor for blowing out pipes and a 400-litre Enduramaxx clean water tank for washing down.
It was a sizeable investment, so he made sure there was adequate local demand before taking the plunge. “I needed commitment from a minimum of 20 customers to make it viable, and I didn’t want to travel more than 50 miles if I could help it,” says Andy.
“This would give me enough work to pay back the initial outlay in about three years.”
Covering the costs over this timeframe was essential because Borger make it clear that the separator’s internals would need to be completely overhauled every 6,000-8,000 hours, at a cost of about £16,000.
Andy placed the order in February 2023, had the machine running by late autumn, and it has been in high demand ever since.
Macerator and stone trap © James Andrews
How it works
The rig is entirely self-contained, meaning no additional pumps or ancillaries are required.
A high-flow lobe pump kicks off the process by drawing slurry out of the store and passing it through a macerator and stone trap.
Unlike the units found on dribble bars, this has a series of tough rotating carbon-steel blades that pass by static ones. These make light work of most solids, with scraper rope and hard plastic cow clogs the only items that have been known to stop them in their tracks.
Slurry is then fed into one end of the large, single separator which has a heavy-duty auger surrounded by fine, stainless-steel mesh screens.
The auger squeezes material against the mesh as it makes its journey to the other side, while liquid is taken away by a second lobe pump. Ideally, this is piped to another store, although it is possible to return it to the same one it’s drawing out of.
Efficiency drops a little when doing this as there will be a degree of double processing, but it’s still a viable option.
Meanwhile, solids tumble onto a conveyor belt, which either discharges them to the ground or a trailer.
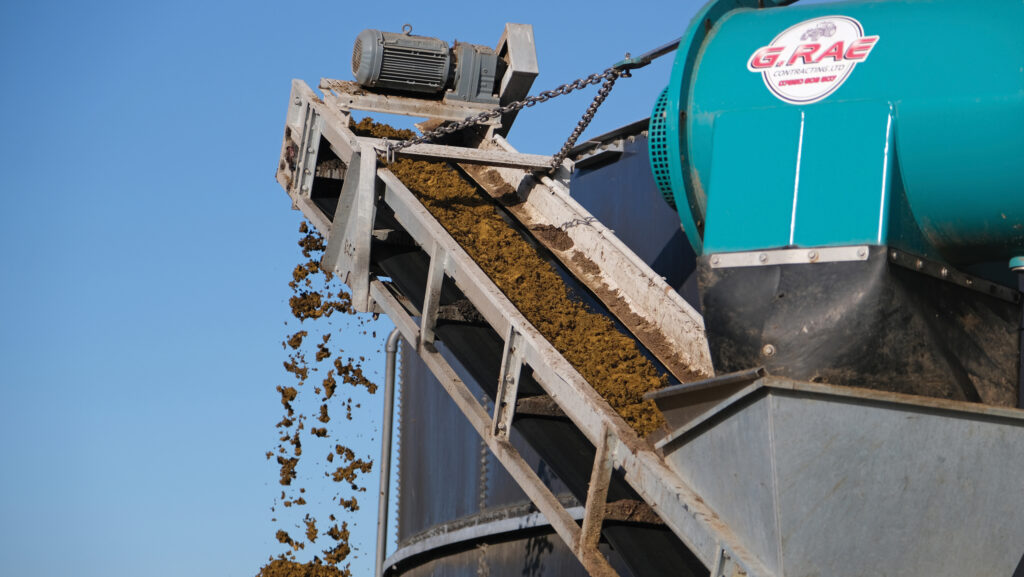
Separated solids © James Andrews
Output
The dry matter of these solids is determined by the position of a backplate at the discharge end of the auger – the closer this is wound in, the more liquid is squeezed out.
In an ideal world, it would be set to extract as much of the liquid as possible, but doing so causes a marked reduction in output.
As the name suggests, the RC150’s peak work rate is 150cu m/hour which, like output figures for all separators, is only achievable when working with wet slurry and not pressing it too hard.
If Andy pushes for high dry matter (up to 38%) in particularly thick material, the processing rate can drop as low as 60cu m/hour, but in an average sample it’s more like 100cu m/hour.
“If you’re just going to put the solids through a muckspreader there’s little to gain from getting it dryer,” he says.
“Most of my customers are more interested in maximising output, so I can reduce the amount of pressure and have slightly wetter solids.”
Even so, these are still relatively dry to the touch, with just the odd drop of liquid coming out when squeezed by hand.
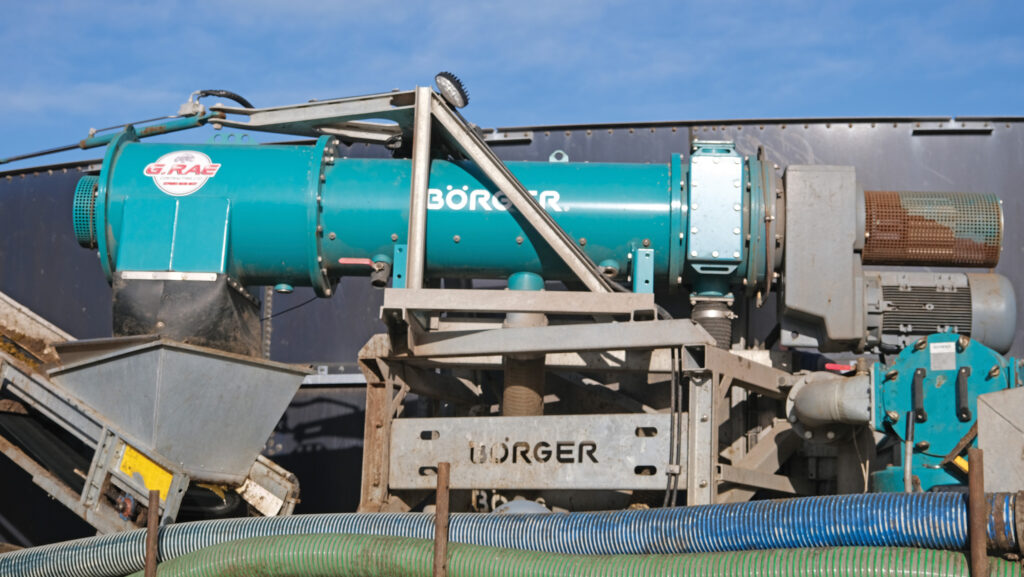
Solids from the single auger separator are sent up an elevator © James Andrews
Using it
All functions are controlled via a touchscreen display on the side of the machine, and it’s a relatively simple beast to get up and running.
Cleverly, once the settings have been dialled in, it will automatically tweak motor and pump speeds to maintain maximum output as the consistency of the slurry changes.
For example, if it suddenly thins, the machine will increase input pump speed to ensure the separator continues to work at peak output. Conversely, it will slow down if particularly thick material is introduced.
This is important in slurry that hasn’t been stirred as there is far more variation throughout the day.
Settings for different farms can also be saved in the system, which makes it much quicker to get up and running – 15-20 minutes on average.
“When it’s set right you can just let it get on with the job, but you need to be around to keep an eye on it,” says Andy.
“It works well for me as it gives me enough time to co-run the business – we’ve got 14 full-time members of staff, so there’s plenty of organising to do.”
All functions on the machine are driven by electric motors which means it’s both quiet and reliable – even the rams for operating the unloading conveyor are driven by an on-board electro-hydraulic system.
This saves putting hours on the tractor up front, other than those it clocks towing the unit to the farm or reeling out hoses.
Most of the noise comes from the generator, which is fairly unobtrusive as it runs at just 60% capacity most of the time. “You only need 110kVA when the motors are starting up, so it’s under very little strain for most of the day,” says Andy.
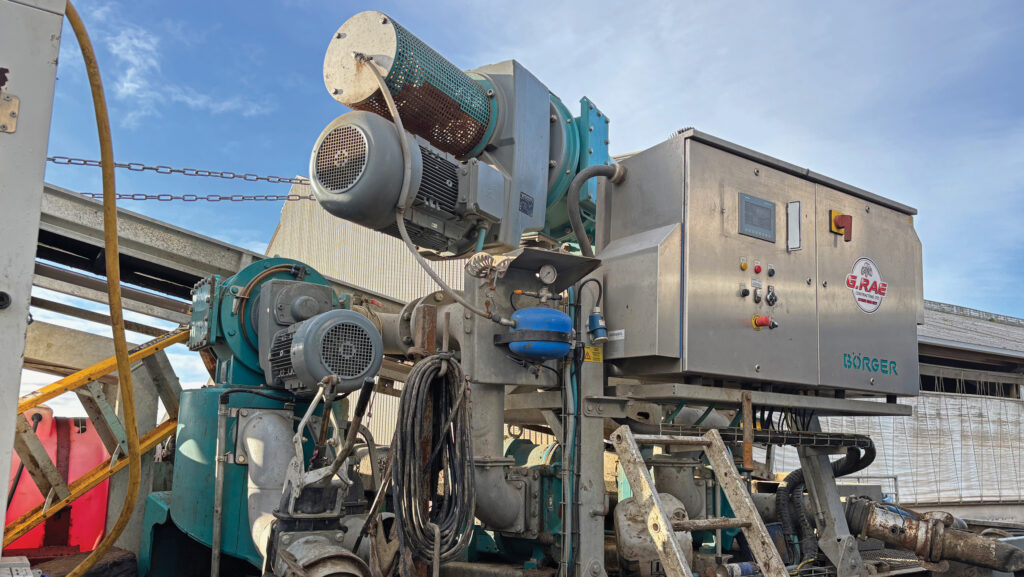
All electric drive is provided by a 110kVA Evopower generator © James Andrews
Reliability
That said, this is the only part of the system that has given any trouble, as the integrated fuel tank has suffered from condensation which leads to water getting in the fuel.
It recently got to the point where Andy had to fit an alternative vessel – a repurposed 230-litre plastic Team sprayer tank – which immediately solved the problem.
Maintenance of the two pumps is another consideration – the rubber lobes and metal wear plates needed to be replaced in the load unit after about 14 months of use at a cost of £600. The unloading side gets much less wear, so these are still in good condition.
With the value of the machine’s internals so high, farms that bed on sand are generally avoided as they would accelerate the wear too greatly.
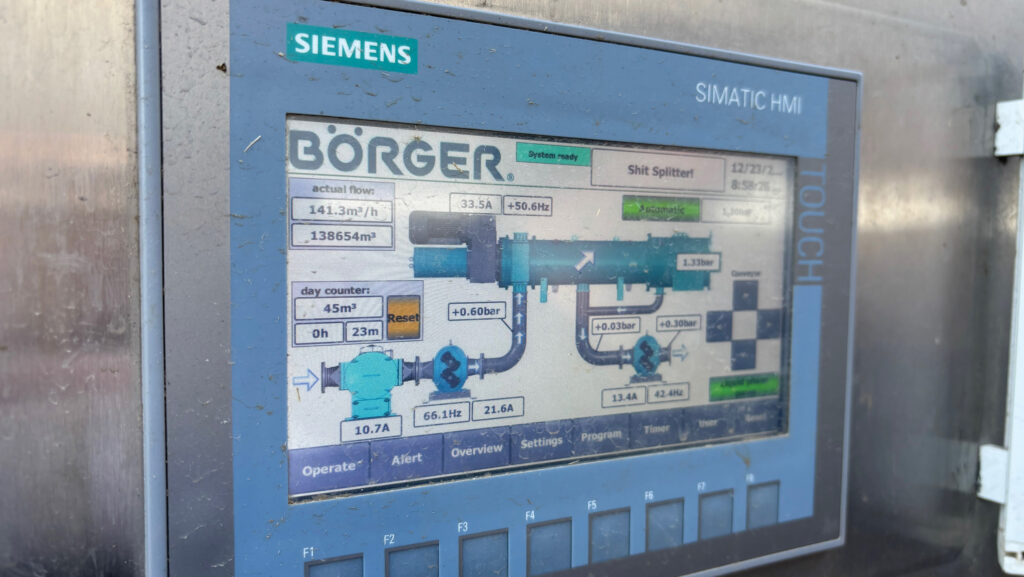
Farm-specific settings can be saved on the touchscreen © James Andrews
Future upgrades
Though the setup has worked well, there are a few things Andy would do differently next time.
Chief among these would be using a custom trailer with a mesh floor rather than a regular flatbed, so that any spills drop through rather than pooling on the top.
Getting it galvanised would also be a priority because much of the paint on the Portequip has already been eaten away by the slurry.
So far, the machine has clocked up 1,500 hours of separating time and 1,700 hours with the generator running, meaning he is on track to pay back the initial investment before having to refurbish the internals.