Why Kent lime contractor commissioned custom Bunning spreader
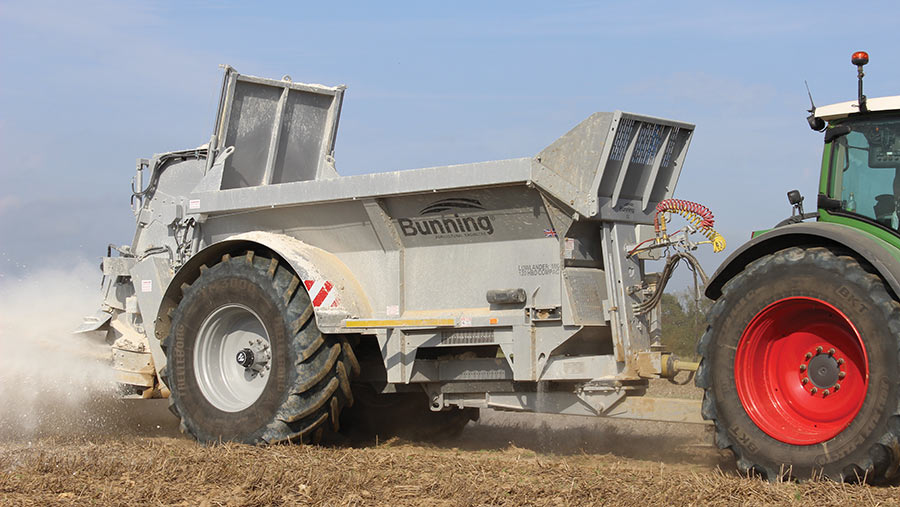
With just a bag of clothes in the back of his Ford Focus, Steve Pack’s career in soil nutrition began 12 years ago as he drove from the family farm in Hertfordshire to Kent to set up shop as a lime sales agent.
Steve then went independent eight years ago when R&T Liming was acquired by Agrii and he didn’t fancy working for a big organisation.
Instead, he built his own business that today operates throughout the county and a bit beyond.
See also: Forward-control Fastrac ups spreading output by 30%
Mutually beneficial
Steve Pack Agricultural Services specialises in soil nutrition, from GPS soil sampling through to the production, supply and spreading of lime and fertilisers.
The business employs five people and has a fleet of equipment including a fertiliser screening and blending plant (operated under subsidiary Newbury Fertilisers), two loading shovels, two bulk tippers and six spreaders – three arable scale and three for fruit.
These are operated mostly by sub-contractors providing man-power and tractor-power in a mutually-beneficial arrangement.
“The contractors get work for their tractors at a time of year when they have spare capacity,” Steve points out.
“And I have the use of skilled operators with modern tractors, as well as fewer big finance commitments, while retaining a financial interest in the spreading operations by owning the spreaders.”
The two Bredal K85 and K105 trailed spreaders that handle all the arable fertiliser applications have recently been supplemented by a specially commissioned Bunning manure spreader.
But it has yet to see any muck as its principle role is spreading chalk, and its bespoke build is a configuration that turns it into a highly effective machine for this task that has overcome logistics issues.
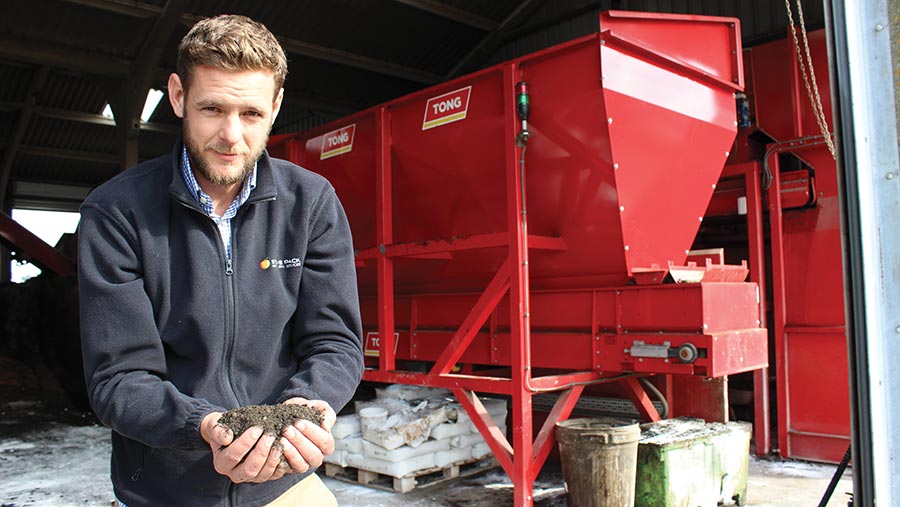
Steve Pack © Peter Hill
“The material sourced from two local quarries becomes very sticky when it’s damp, forming lumps as big as footballs and tending to bridge in the Bredal spreaders with their sloping sides and belt conveyors,” explains Steve.
“This has made getting chalk to the field at the right time for spreading one of my biggest headaches because on-farm delivery logistics were completely weather-dependent.
“I didn’t dare tip in the field if there was any likelihood of rain, and we often lost spreading days because of that; it was immensely frustrating at times.”
Bringing in the new Bunning Lowlander spreader – specially built to Steve’s requirements – has resolved this issue thanks to its vertical body sides and chain-and-slat conveyor.
It has also given the two horizontal beaters and large diameter high-speed discs, with two thumping great vanes on each, the ability to smash any clumps and lumps.
“It has completely transformed the logistics challenges we had before,” says Steve. “I run two bulkers for delivering chalk and fertiliser, and now don’t lose any sleep over tipping the chalk a week or two before it’s due to be spread.”
Accurate application
Regardless of the “blunderbuss” treatment of the liming material, tray testing has revealed the twin discs will reliably spread chalk evenly to 18m, which ties in nicely with increasingly common 36m tramlines.
At the same time, it copes with application rates of typically 3-8t/ha at 14-16kph, so there are big outputs to be had, and the large body outlet and its guillotine door, which can lift a full 1.5m if needed, means rates in excess of 10t/ha can be handled with little loss of pace.
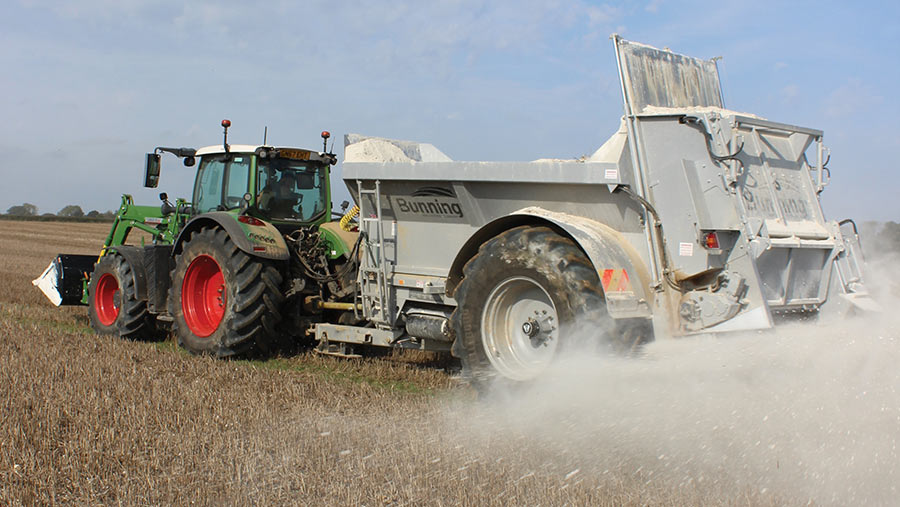
© Peter Hill
Although labelled Lowlander Mk4 120 HBD Compact, the spreader is a quite different beast from the standard model.
But Ben Johnson at Bunning emphasises it uses components and assemblies proven on other spreaders in the company’s extensive range, just brought together in a different configuration.
An 18t ADR axle underpins the machine’s 16t carrying capacity beneath a 1.25m-wide body, but the spreading assembly is a 1.5m unit with 1.1m-diameter discs to provide maximum output and working width.
To cope with its dense chalk loads, the spreader also has a heavier-duty gearbox and higher-capacity hydraulic motor than standard – the former to cope with the significant torque required to achieve slow bed speeds with a dense product, and the latter to provide the power needed.
The bed chains are Bunning’s regular 16mm items used across its range but with about one-third more box section slats to position them closer together. This avoids any “pulsing” as the chalk is transferred out the back.
Scrapers are welded to every fourth slat to prevent any build-up of material on the deck.
Smaller body
The short body of the Compact model provides maximum manoeuvrability but, as contractor Dan Tong notes, combined with the heavyweight kit at the rear, does make the machine a little light on the drawbar – despite it being filled with up to half a tonne of steel ballast – with some “hitch chatter” setting in during road travel.
The narrow body is used to accommodate the 800mm tyres that Steve insisted upon while keeping overall width within 3m.
“It’s important to be able to travel on the field while also limiting our impact on the soil, and since we have 800mm tyres on our two Bredal fertiliser spreaders, that’s what we wanted on the Bunning.
“We did look at a tyre pressure management system, but an over-the-tyre setup looked too vulnerable for our work and there were concerns about axle strength with a feed through the hub.”
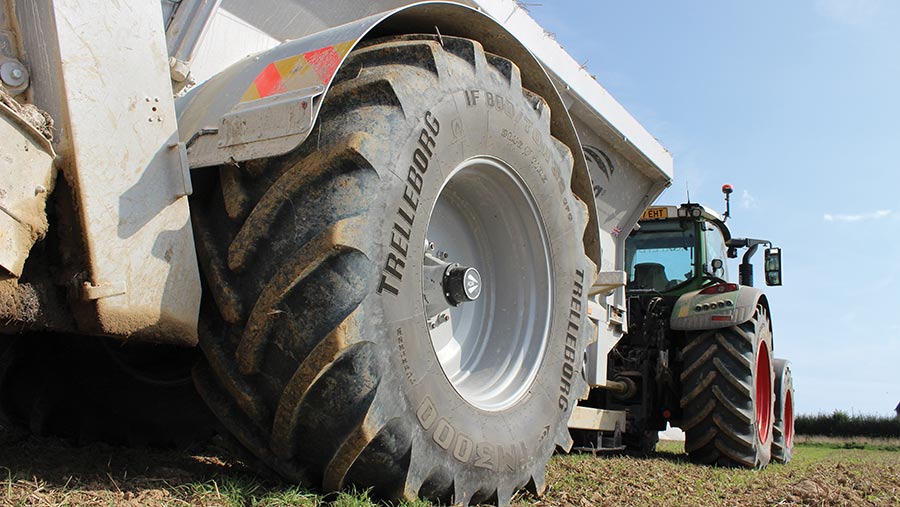
© Peter Hill
Trelleborg TM3000 IF 800/70 R38 CFO tyres are installed beneath some robust-looking mudguards, complemented by the even more flexible tyres on Dan’s 246hp Fendt 724 Vario – BKT Agri Max VF-Flecto in sizes VF 710/60 R42 at the rear and VF 600/60 R30 on the front.
The tractor is equipped with a Cargo 5X 85 loader, which easily reaches over the tall sides of the big spreader, along with Topcon guidance using a dedicated screen.
There is also a Topcon Apollo controller, which uses the spreader’s axle and drawbar weigh cells to regulate the required application rate according to forward speed while also responding to a shape file for variable-rate spreading, which is used for most jobs based on Steve’s soil sampling.
Newbury Fertilisers
Steve Pack’s Newbury Fertilisers operation also uses some bespoke kit, in this case a screening and blending package put together by potato equipment specialist Tong Engineering.
The crop nutrients business has its roots in Sheppy Fertilisers and produces several unique products, including a novel one high in phosphate that Steve says is proving popular with growers.
Minimising dust when blending and spreading has been a key aim of the custom plant, successfully tackled by using the relatively gentle action of Tong potato webs for screening and then mixing with compost for spreading.
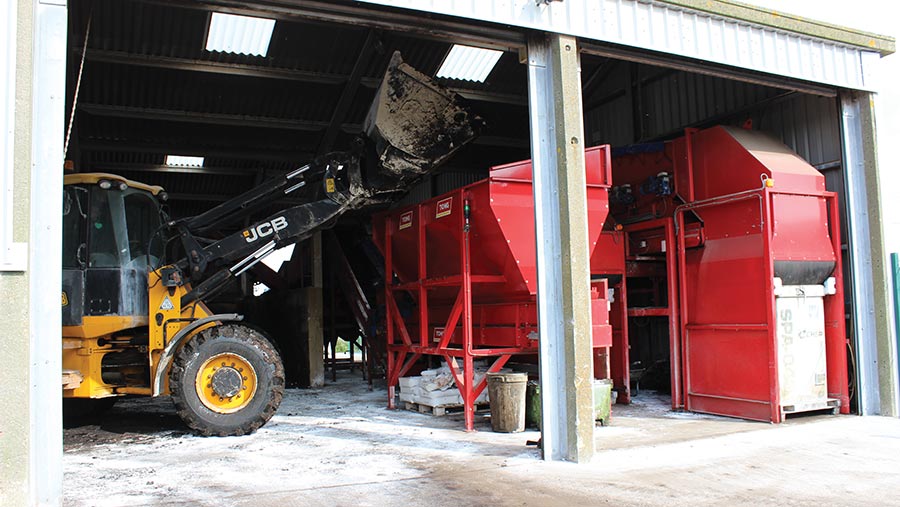
© Peter Hill
Beyond the reception hopper and conveyors are 10mm and 20mm screening webs, with any over-sized material passed through a crusher before being returned to the bulk, which is gently mixed with compost in a blending barrel.
“All fertilisers are hygroscopic, so any very fine particles readily stick to the damp compost and this significantly reduces the amount of dust produced when we’re spreading,” explains Steve.
“The finished products spread beautifully to 20m from our Bredal machines and, of course, they also supply organic matter and nutrients from the composted material.”
In addition to products for grassland and arable crops, the blending plant produces fertilisers for fruit and vines, and growers in this sector can also call on a lime supply-and-apply service involving another bespoke spreader.
The unit commissioned from Land-Drive normally operates with an overall width of 1.55m, but by flipping the wheels it can be narrowed to just 1.35m to work in vineyards.