Twin fert spreader combo reduces passes and eases logistics
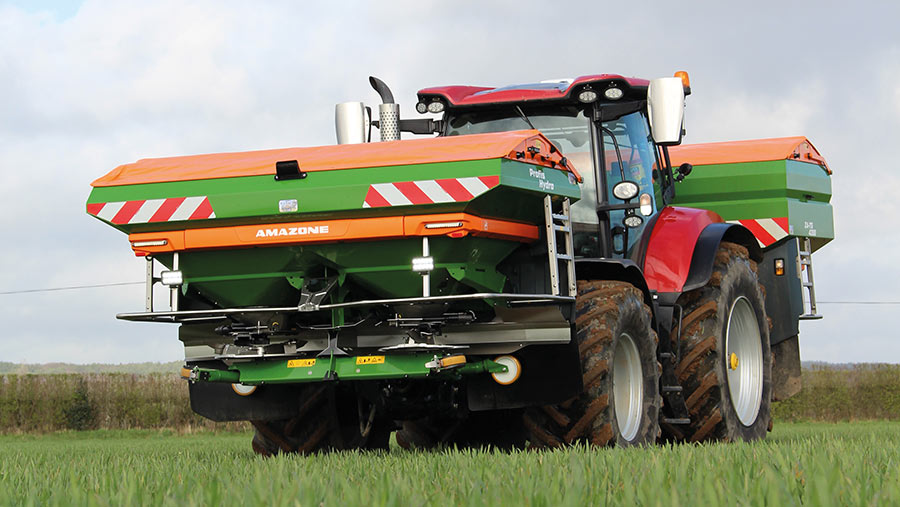
One of the first Amazone front and rear spreader combinations in the UK is allowing its Dorset-based owners to spread two products at variable rates in a single pass and has vastly increased carrying capacity for one-product applications.
Woodsford Farms’ manager Mark Edgecombe openly admits that when he first saw the combination at the Lamma show, he immediately dismissed the idea.
But, on further inspection, it actually had the potential to make life a whole lot easier, as his single mounted hopper was struggling to cover the 1,600ha with multiple products and passes.
See also: Simple 24m mounted sprayers for less than £30,000
The Velcourt-managed farm, which lies just east of Dorchester, actually relies on waste products for much of its soil nutrition.
It sources, stores and spreads about 40,000t of animal waste, sewage sludge and farmyard manure annually from neighbouring farms and has invested in a top-spec tanker and muckspreader to apply it.
In order to get a healthy balance of inputs, the soil is zoned to assess the value of the organic matter and pinpoint precise areas of fields that need a fertiliser top-up – significantly reducing costs compared to a blanket approach.
However, this system means variable-rate spreading plans are concocted once the crops have started pulling away in the spring and the manure has taken effect, inevitably putting more pressure on the spreader driver to get across the land quickly with different products.
Farm facts
- Woodsford Farms
- Size 1,600ha
- Crops Wheat, naked oats, lucerne, spring ahiflower
- Soil silt over gravel to chalky loams and clays
Single spreader
As soils vary across fields, this could mean travelling up every tramline and only switching on when passing over a zone that required a dose – then making a separate pass with another product.
“We made the switch away from urea and sulphur blended products when we jumped from 24m to 30m tramlines, as it led to some striping on the edges of runs – particularly with misty mornings affecting the properties of the product. This also meant we were going to have to make an extra pass,” says Mr Edgecombe.
His long-in-the-tooth, rear-mounted Amazone spreader was due for replacement and, after toying with trailed machines, he opted for an Amazone ZA-TS 4200 on the back and an additional ZA-TS 2200 at the front – upping carrying capacity by 2t and allowing him to spread two products in one pass.
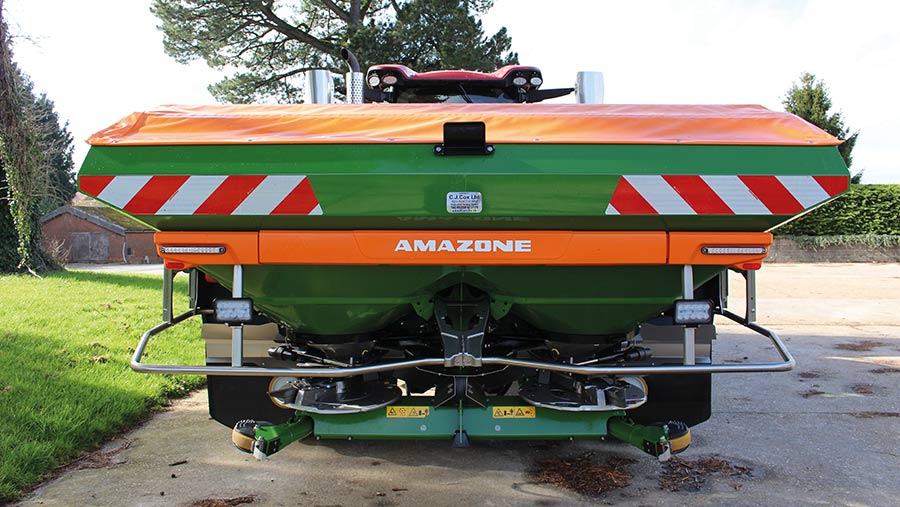
© MAG/Edd Mowbray
Logistics play a key part in day-to-day planning. The farm is spread over 40km, so a trailed machine appealed for road work, but its 12t hopper would have been far from ideal on the steep slopes of west Dorset. It was also essential to spread two products in one pass – something a trailed machine couldn’t offer.
He ended up keeping the existing spreader as a back-up because the trade-in was valued at just £1,500, meaning it was worth more to him as a spare machine than its cash value.
“We’ve always had a front weight on the tractor to keep the nose down when full, so it made sense to replace this with a hopper, allowing us to carry more and empty both evenly to help maintain spread patterns,” explains Mr Edgecombe.
“I keep a keen eye on residual values of machinery. As well as the price of two mounted units being half the cost of a trailed machine, the front spreader will be appealing to a small farm when I’m finished with it. I also have the flexibility to run the two spreaders on two separate tractors if necessary.”
Teething problems
Although the machines arrived more than a year ago, the front spreader – which is simply a standard rear-mounted model run in reverse – was used for the first time this spring due to extensive issues getting the Amazone Isobus system to communicate with the Case-IH Puma’s AFS screen.
The brand-new Puma was specced with a front Isobus connection and front hydraulic spool return valve but, when it was plugged in, the tractor couldn’t determine which spreader to place on the main screen.
The answer was to use an Amatron 4 box to run the front unit, but it took a lot of head scratching and many hours to get the system running sweetly.
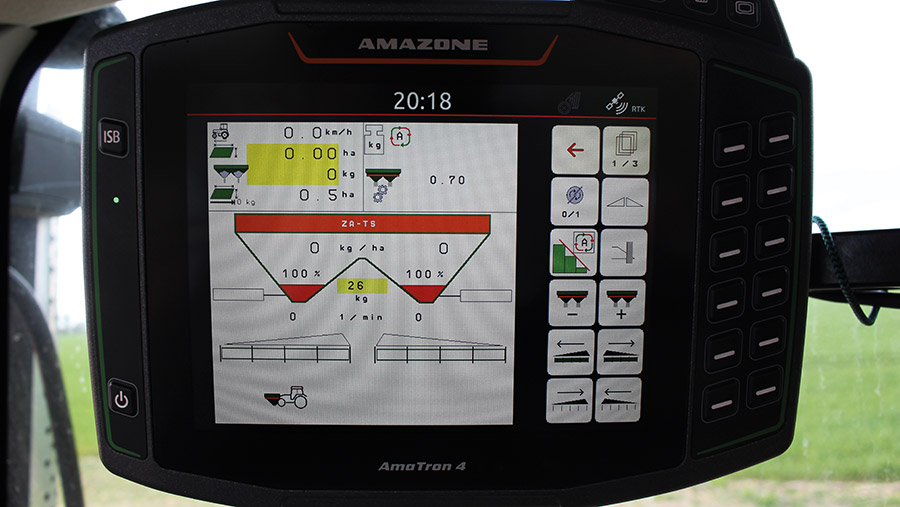
© MAG/Edd Mowbray
Mr Edgecombe also specced a bigger hydraulic pump to provide enough oil to run the two spreaders. The Puma’s standard 150-litre/min offering was upgraded to 170 litres/min, which, he says, copes well most of the time.
However, forward speed needs to be reduced when scaling steeper slopes to prevent a drop in disc rpm.
He added Amazone’s Argus camera system on the rear 4,200-litre spinner so the spread pattern could be constantly maintained.
The bank of cameras sits above the discs and monitors the granules as they are flung out, adjusting settings to allow for variations in weather so the drop point and pattern remain consistent.
However, as good as they are at notifying the operator when the drop point isn’t reached (usually due to wind), they are all too easily scuppered when using dusty products such as potash.
This triggers an alert in the cab when the cameras can’t detect where the product is landing.
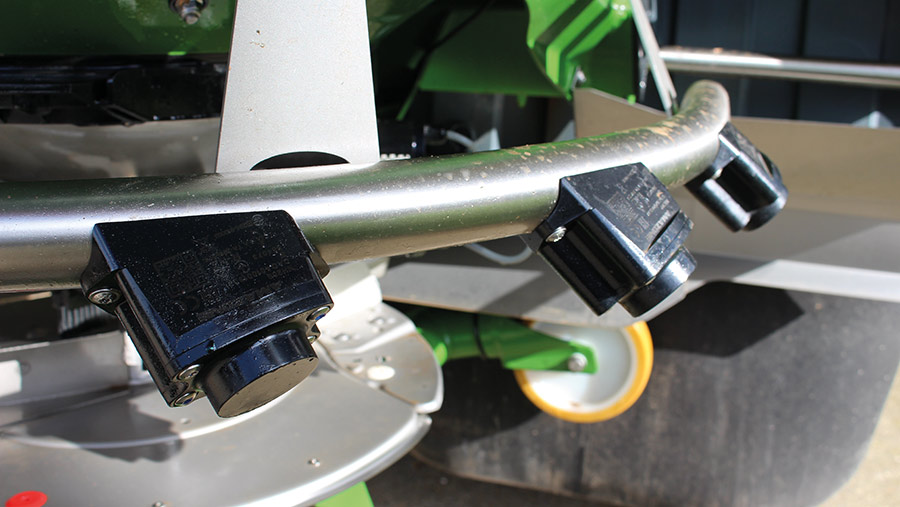
© MAG/Edd Mowbray
In the field
The aim is to have the spreader set up with phosphorous and potassium in the front and urea in the back, all running from variable-rate maps. Operating speeds are around 20kph and can be pushed up to 25kph when the going is good.
When both spreaders are hooked on, the front one recognises it is mounted in reverse and will spin the discs in the opposite directions to fling granules away from the tractor.
The throw forwards is between 25-30m, and it will shut off well in advance when approaching a headland.
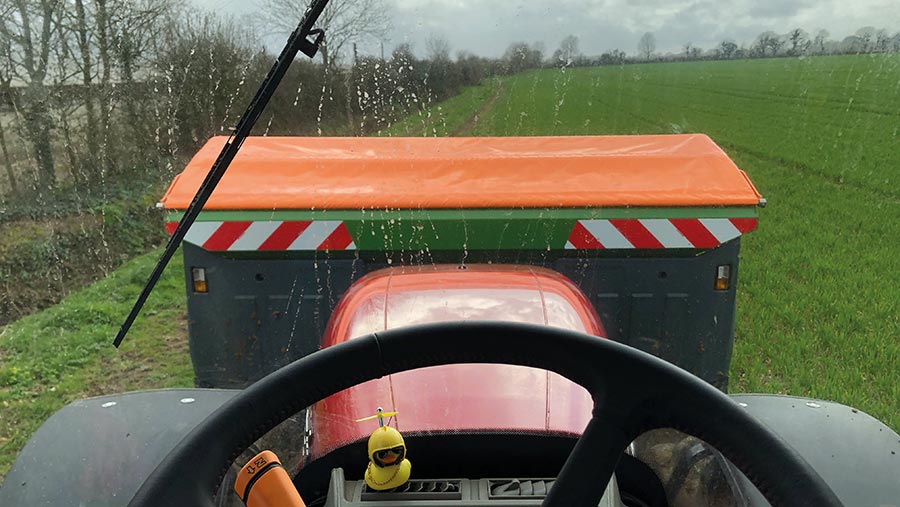
© MAG/Edd Mowbray
The mapping on the in-cab screens paints the spread distance in front of the tractor and, as speeds alters, the shutters adjust to maintain the correct rate.
Currently, the farm is applying the same product front and rear.
This allows the operator to manage the weight balance between the two spreaders by running the front unit on half rate until the fuller rear spreader is down at the same level – both then empty at identical rates to allow the weight to drop evenly.
The extra capacity has allowed some of the bigger fields to be completed in one hit rather than coming back for a refill.
A number of 600kg bags have also been ordered to help fill the spreaders quicker, without having to empty the hoppers completely to squeeze in a full 1,000kg bag.
One of the most obvious issues is pulling out on to roads as the extra length makes visibility tricky, but Mr Edgecombe says a set of cameras will be installed to simplify things.