Sprayer control systems updated
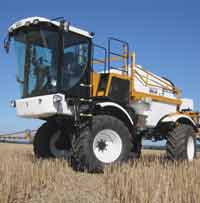
Sprayer control systems are continually being updated to help make the operator’s life easier. Peter Hill catches up with developments.
JOHN DEERE
John Deere’s AutoDilute system calculates the amount of clean water needed to achieve a required level of “dead volume“ dilution before automatically controlling the dilute-circulate-spray process
Sprayer operators may be required to use a more rigorous rinsing regime if the standard applied in France is adopted across the EU.
This recommends that after spraying in the field, any liquid remaining in the tank and the spraying system must be diluted by a factor of six before the operator may start cleaning out the sprayer in the field.
Ultimately, the system volume must be diluted by a factor of at least 100 to complete the cleaning process.
To help achieve that standard and make the most efficient use of clean water supplies, a part-automatic, part-manual dilution and rinsing system has been developed as an option for John Deere 700i trailed sprayers, and in fully-automatic form for 800i & 800i TF (Twin Fluid) models on which the entire process can be completed without leaving the tractor cab.
AutoDilute enables the operator to set-up a multi-cycle dilution and spraying-out process that is completed automatically.
A “sprayer rinse calculator“ is at the heart of the system it takes into account the “dead volume“ of the entire sprayer and the boom, the actual spray tank and rinse tank contents, the amount of clean water required for proper dilution and the number of cycles required to ensure the required dilution factor.
Having made the necessary calculations, the system tells the operator whether it is possible to rinse out the sprayer with the quantity of clean water available and how many rinsing cycles it will take.
Once the “start“ button is pressed, the system automatically initiates the dilution, rinsing process and spraying-out cycle, and repeats until the sprayer is completely clean and ready to use again.
Apart from making efficient use of clean water, the auto system is reckoned to be quicker and reduces risk of operator error leading to crop damage and/or environment contamination.
LEMKEN
Mid-range EuroTrain trailed sprayers, as well as the bigger Albatros and mounted Sirius models from Lemken are candidates for Müller terminals
Control systems and on-board electronics with ISOBUS compatibility have been introduced on Lemken sprayers to meet demand for machines with a higher specification and more sophisticated operation.
The German manufacturer has adopted the Müller Elektronik range of terminals for this purpose, although thanks to the installation of an ISOBUS-compliant on-board job computer and cabling, the sprayers can be operated through any ISOBUS standard terminal.
Lemken has three options for operators buying a terminal with their sprayer: the Basic, which will handle all implement functions and monitor in-field operations Basic Top, which adds a colour screen and USB socket for data transfer to computer-based job recording software and Comfort, which has a larger screen and additional functions.
In each case, the terminals come with a 24-function “joystick“ to mount on the tractor seat armrest and provide fingertip control of such things as boom folding, sprayer steering and section switching
Beyond simple control functions, however, the terminals can handle some more advanced roles, such as Slope Compensation, which adjusts the boom to slopes Distance Control, which lifts and lowers the boom at bout–end turns and Tank Stop for automatic filling to a pre-set volume.
Also available is a pendulum sensor to measure crop density and digital GPS functions such as mapping, steering guidance and spray control with progressive boom section on-off to avoid over-spraying on short-work.
The ISOBUS installation and terminals are available from £3577 (GPS capability adds £1616) on the mid-range EuroTrain and larger capacity Albatros trailed sprayers, and on the new Sirius mounted sprayer being introduced this year with 1600 and 1900-litre tank capacities and compact-folding aluminium boom.
HOUSEHAM
The Field Master unit’s steering guidance in the absence of tramlines – with straight line and curve modes – helps keep Househam’s AirRide self-propelled sprayers on track
Sprayer maker Househam has developed its own GPS control unit to complement the touch-screen vehicle instrumentation and sprayer terminal fitted as standard to its self-propelled applicators.
The Field Master unit (pictiured) provides steering guidance and field records, plus a database of pesticide products for reference and to help compile records quickly and easily.
The Guidance section of the instrument can operate in straight line and curved modes, giving the operator a sight line for accurate spray bout matching in the absence of the tramlines.
It also plots where the field has been sprayed, with areas that are double-sprayed highlighted in red, and both are totted up and shown with field maps that can be downloaded to an office computer and retained as part of the spraying operation records for crop assurance and traceability.
To minimise the amount of double-spraying, the Field Master system can operate an automatic boom section on-off control to reduce wasteful spray overlaps where bouts converge.
Individual field histories are set up by recording the first pass around the field. The record is then stored by Ordnance Survey grid reference, so that each time the sprayer returns to that field, the record is automatically opened to show previous treatments and prepare for recording the next one.
KNIGHT
Filling, rinsing and washing functions on the Knight 1830 self-propelled sprayer’s MAXImiser plumbing system can now be operated through the control terminal rather than a separate selector box
Electronic controls for operating the MAXImiser plumbing system on Knight’s 1830 self-propelled sprayer have been incorporated into the Müller terminals that already provide various control functions on the machine.
The MAXImiser system has fewer components and less fluid volume than conventional sprayer plumbing, resulting in a more efficient rinsing process that uses less clean water and produces less “spray out“ to crops at the end of a spraying job.
Moreover, it provides pressurised circulation of dilute spray mix through the spray lines, so nozzles react fast to on-off commands, an important feature for GPS control, says Knight, which is also available through the Müller terminals.
In addition to providing simple control of filling, rinsing and washing from the cab – with icons showing the function selected on the screen – the Comfort terminal (pictured) can provide steering guidance for pre-emergence treatments, visual and downloadable records of “where sprayed“, auto boom levelling and automatic GPS-based on-off control of boom sections to minimise over-spraying on short-work.
Also, because the terminals comply with ISOBUS standards for electronics, cabling and software, they can be used to operate other ISOBUS-compliant implements.
CHAFER STREAMBAR APPLICATOR A new version of Chafer‘s Streambar applicator for liquid fertiliser has an integrated metering mechanism instead of restrictors, which makes it quicker and easier to select different rates and extends the range of rates it can deliver. A sliding mechanism to select one of six different flow rates replaces restrictors on Chafer’s Streambar MultiRate liquid fertiliser applicator
The Streambar MultiRate can also be used on an EF3 nozzle body without needing an adapter and is more compact, so less vulnerable to damage in use or during travel between fields.
Two versions will be available – for 33cm and 50cm spacings – and initially the Streambar MR will be available to suit a sprayer with jet spacings of 50cm.This will be followed shortly by a 33cm version.
Advantages of the dribble bar over jets, says Chafer Machinery, include reduced risk of scorch thanks to the larger droplets it produces no impact on application pattern from different boom heights and individual feed to each of the four ports to ensure even application across the full working width.
A simple sliding mechanism is used to select one of six rate settings without having to remove the dribble bar and higher application rates than were possible with the previous design can be delivered.