Six of the best alternatives to diesel
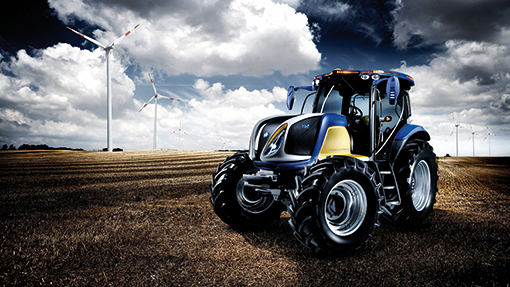
Diesel is less abundant and more expensive than ever. Oliver Mark goes on the hunt for the fuel best suited to power the tractors of tomorrow as the oil wells begin to dry up.
Diesel has been the number-one choice for ag-orientated engine makers across the world for almost a century. The original diesel tractor – the Benz-Sendling – first graced the world market in 1923 and since then we’ve become ultra-reliant on oil-burning engines.
But unless you’ve been residing self-sufficiently in the middle of the Amazon jungle for the past 10 years, you’ll have noticed fuel prices chewing an ever-growing hole in the bottom of your bank account.
In the UK it has trebled in the space of a decade and, if you shop around, you could pick up a litre of Coca-Cola for less. That has forced the hand of tractor companies – previously reluctant to change – to plough more of their research and development cash into exploring other forms of fuel.
See also Dissecting red diesel rules
Long-term price forecasts are hazy, but if the price of red diesel continues the trend it has set over the past 10 years then it will hit the milestone £1/litre mark by 2020. UK farmers could also be hit with a double whammy if they lose their tax relief for red diesel, as happened in Holland last year, and have to pay full price for their fuel.
And you won’t need a maths degree to work out that the implications – even for the average farm using 20,000-litres of fuel each year – will be like a Lennox Lewis right hook to the farm’s bottom line.
Opportunities
It’s not all doom and gloom, though. Farms are huge producers of energy – whether it’s producing and harnessing solar, wind or biomass – so many are potentially self-sufficient in the fuel department.
In this article we’re going to take a look at the six most viable options for fuelling the tractors of tomorrow. The major manufacturers have tried out some of them, while others have resulted in several backyard tractor builds by farmers in the USA.
How we ranked them
We looked at each fuel individually, considering 1) its availability and timescale for development, 2) the current level of research into it, and 3) its strengths and weaknesses.
In each of the three areas they were marked out of 10, giving a grand total out of 30. Total scores were then ranked to give a best-to-worst scale of potential.
Verdict
Even when the final emissions regulations have passed, it looks like tractor makers will still have to come up with novel, future-proofed ways of powering farm machinery.
The biggest problem now is that manufacturers have to throw almost their entire research and development budgets at reducing emissions from diesel engines.
Of all the potential candidates, methane looks to be the most realistic option – it’s closest to full production and is pretty efficient.
There are several other ecologically neat options, but the laws of physics hold a grip on almost all of them. The quantity and weight of batteries makes electricity and solar a no-go and producer gas is too cumbersome to be used realistically. Hydrogen fuel cells are efficient but too expensive to be used on farms.
The time will come when the price or quantity of diesel forces us to look elsewhere for fuel. But until then, it looks like our reliance on fossil fuels will remain.
Here’s a quick glance at how we ranked the alternatives. Click on the tabs for a more detailed review.
1. Biodiesel 28/30
2. Biogas 24/30
3. Fuel cells 22/30
4. Diesel-electric 20/30
5. Solar 18/30
6. Wood fuel 10/30
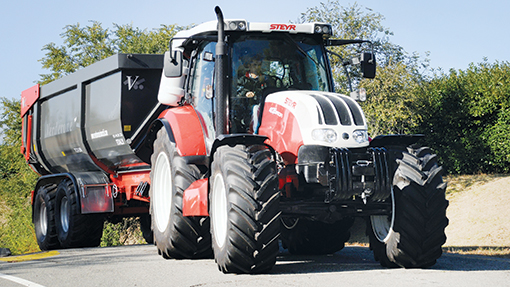
Has it been used before?
If you’ve toured any of the major European machinery shows you’ll have probably seen prototype versions of a biogas-propelled tractor.
Lesser-known Austrian tractor builder Steyr (part of CNH Industrial) had led the research and development race with its 136hp 4135 Natural Power model, which was launched at the Agritechnica show in 2011. However, it appeared at the 2013 event painted New Holland blue and badged as a T6.140.
The tractor is fuelled by methane, said to have the smallest carbon footprint of any fuel and produced from anaerobic digestion. At the last count there were about 40 agricultural AD plants in the UK, compared to 3,500 in Germany.
So, in theory, there are plenty of farms with access to fuel self-sufficiency across Europe. Surplus energy provided by anerobic digester-driven generators can also be sold to the national grid.
How does it work?
New Holland’s T6.140 uses a four-pot, three-litre engine that produces 135hp and 620Nm torque. Methane is stored at high pressure in nine steel tanks and the 50kg capacity should be enough for half-a-day of normal operation. There’s also a 15-litre diesel tank underneath, so once the gas is used up, the engine automatically reverts to diesel power.
It’s an ecologically-neat set-up – emissions can be cut by 80%, particulate levels trimmed by 99% and cost savings against oil-burning equivalents are 25-40%, according to New Holland. Methane-powered tractors should have a similar price to diesel-only versions, too.
There’s a snag, though – raw gas must be processed/filtered before it can be used in an unmodified diesel engine. The correct procedure adds a few thousand pounds to the cost.
It’s also worth remembering that if you plan to sell your homegrown gas to the national grid then it’ll need to have low moisture and sulphur contents to meet commercial natural gas standards.
Strengths
- Fuel costs cut by up to 40%
- Can be produced on-farm
- No major engine redesigns – can work alongside diesel
- Minimal horsepower loss (6-7%)
Weaknesses
- Gas storage capacity – biogas difficult to compress
- Filtering and compression system adds to the price
- Maize must be grown instead of food crops
Availability and timescale | 9/10 |
Current research | 8/10 |
Strengths v weaknesses | 7/10 |
Total | 24/30 |
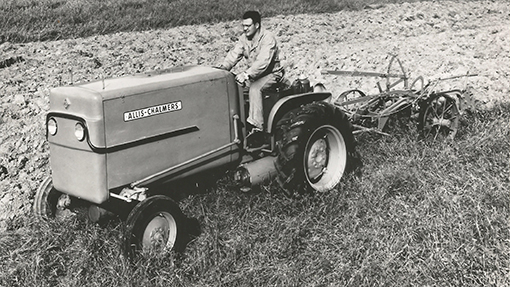
Has it been used before?
Though Allis-Chalmers had a fuel-cell tractor in 1959, New Holland is leading the current hydrogen-powered tractor research brigade. It is testing its second-generation prototype, where PV panels and a biogas plant provide electricity to generate hydrogen.
It is an efficient system but has one major stumbling block – cost. Fuel cells are currently pricey bits of kit, but economies of scale should see the cost tumble if the technology gets more popular in other industries.
In the future, electricity could be provided by wind, solar or biomass sources and hydrogen generated by the electrolysis of water. Farms can potentially use their own renewable electricity sources to extract hydrogen from water and it could even be possible to produce hydrogen without electrolysis having to take place.
New Holland has suggested the hydrogen-powered tractor could be on the market before 2020, but everything hinges on whether the cost of fuel cells drops.
How does it work?
Fuel cells consist of two electrodes sandwiched around an electrolyte. Oxygen (from the air) passes over one electrode and hydrogen (stored in compressed form in the fuel tank) passes over the other, generating electricity in the process.
The electricity is stored in a lithium-ion battery and fed to the driving wheels by an electric motor. The only by-product is water, so in emissions terms it’s a winner.
Powering a tractor with hydrogen would be, in the worst-case scenario, 55% efficient in terms of energy use, while a combustion engine is 40% efficient at best.
Strengths
- Hydrogen can be developed on-farm
- More energy efficient than an internal combustion engine
- Very few by-products
Weaknesses
- Expensive
- Needs a supply of electricity
Availability and timescale | 7/10 |
Current research | 8/10 |
Strengths v weaknesses | 7/10 |
Total | 22/30 |
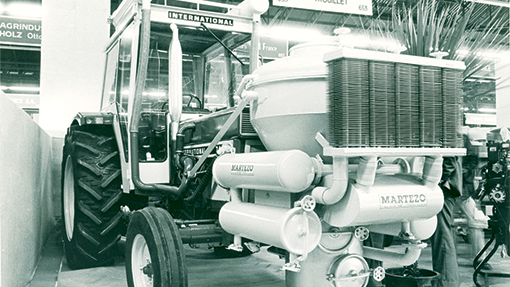
Has it been used before?
Fighting the corner of traditional sustainable energy forms is wood fuel or “producer gas”. We might not be too familiar with wood-fuelled machines in the UK, but wood has been propelling farm machinery since the start of the 20th century.
Petrol shortages made it a popular alternative during the First World War – the French and, in particular, the Germans used it widely. In fact, a company at the sharp end of modern technology – Fendt – built 1,600 wood-fueled machines around that time.
Kits were still built in France as recently as the 1980s for export to developing countries, but it has been 60 years since any serious research was done.
How does it work?
Running a wood-fuelled tractor is like owning a mechanical shire horse, requiring copious amounts of commitment and work. Wood must be felled, chopped and fed to the tractor. Even once it’s there and the fire is lit, operators must wait 20 minutes before there’s enough gas in the tank to get moving.
Chopped hardwoods such as beech (best when dried to 15% moisture) are loaded into a large upright cylinder. As the wood is heated to 1,000C, it produces carbon monoxide and nitrogen. Oxygen levels are carefully restricted to stop the generated gas from igniting.
The gas is directed through a cleaning unit to remove soot and ash, then through a cooling system to solidify tar by-products. These would otherwise clog up parts of the fuel system.
The clean gas – ready for a spark ignition – then travels through a specially designed carburettor, where it is added to air to burn in the combustion chamber. A 25hp Fendt G25 used about 25kg wood an hour and, at full bore, needed topping up with wood every three hours.
The machines weren’t without their problems, though. The bulky add-ons meant visibility was clearly an issue and the barrel couldn’t hold enough wood for a day’s work. So once oil was readily available again, gas kits were stripped off and tractors ran conventionally on diesel fuel.
Strengths
- Low cost
- Relatively clean
- Perfect for wooded areas
- Careful coppicing would make self-sufficiency pretty easy
Weaknesses
- 60 years since serious research
- 15% drop in power
- Requires regular emptying of the ash pan in the base of the generator
- Can provide 100% gas for petrol paraffin engines but only 50-60% fuel for a diesel
Availability and timescale | 3/10 |
Current research | 3/10 |
Strengths v weaknesses | 4/10 |
Total | 10/30 |
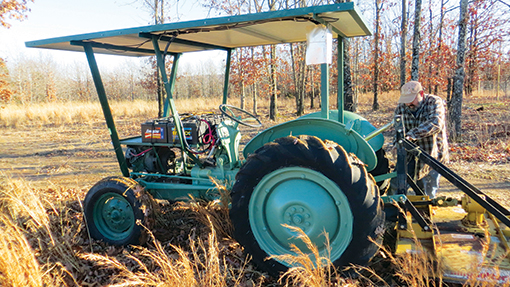
Has it been used before?
Alongside David Beckham’s right foot and Barbour coats, photovoltaic panels have been riding the crest of a fashion wave for the past 15 years. It’s not just house roofs that are home to PV panels – makers have branched out into solar-powered electric fencers, cattle feeders and small lawn-scale mowers.
Powering a full-sized tractor using the sun takes it to another level, though. One company to give it serious consideration five years ago was an Austrian firm called Heliotrac.
Its plans for an entirely solar-powered tractor included a 26sq m solar panel attached to the roof, which could adjust its orientation according to the position of the sun. The pivoting roof had the potential to make it up to 40% more efficient than fixed units.
Power output was expected to be a modest 4kW (5.5hp) and the company said it could run up to a day-and-a-half on slower-paced jobs. Heavier, more torque-hungry applications require more battery capacity, of course.
A few forward-thinking (mainly US) farmers have also had a go at bolting a canopy of panels to the tractor’s cab roof, catching the rays as it goes along and transforming them into electricity stored in rechargeable batteries powering electric motors.
How does it work?
An American – John Howe – has had a few goes, mounting four 24v PV panels in series on the roof of his Farmall Club.
The panels supply nine deep-cycle 12v batteries mounted on the tractor.
These, in turn, feed a 10hp DC motor mounted under the driver’s seat, although the tractor can also be plugged into a 120v AC grid source to charge the batteries.
Mr Howe reckons this can run the tractor for up to five hours on hay-turning duties. That means it might be perfect for small scale, subsistence-style agriculture.
It’s an efficient way of doing things, too – electric motors are more than 90% efficient, so solar panels could potentially produce enough power for most operations.
There’s no fuel wastage when a diesel engine would be idling, either, and sunlight doesn’t cost a penny.
Solar-powered tractors have two major shortcomings though.
The first is their capacity to store energy – you’d need a vast number of batteries to keep the tractor running. There’s also the problem of short winter days at high latitudes where keeping the batteries charged, let alone providing adequate power, might be difficult.
Strengths
- Fewer moving parts
- Potentially improved visibility
- Highest torque on start-up
- Infinitely variable speeds
Weaknesses
- Difficult to store adequate energy
- Panels take up space
- Only effective in places with long sunshine hours
- Not suitable for large-scale, broad-acre agriculture
Availability and timescale | 6/10 |
Current research | 7/10 |
Strengths v weaknesses | 5/10 |
Total | 18/30 |
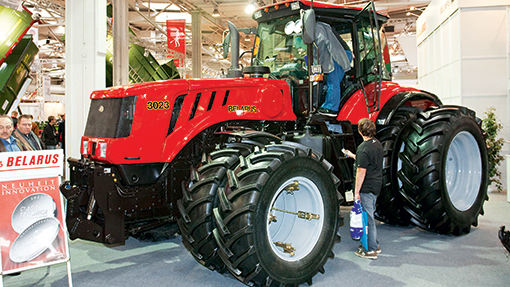
Has it been used before?
Electricity is one energy sector the human race has pretty much mastered. Yet, electric-powered cars, although slowly growing in popularity, are still in their infancy.
That’s not to say electricity isn’t suited to the farming market – sprayers, spreaders and drills are already on the market and their ungainly chain-and-sprocket set-ups and long drivelines are well suited to being replaced by electric motors.John Deere already has its electricity generating (but not electrically powered) 6210RE tractor in production and several other manufacturers have demonstrated diesel-electric combination prototypes at machinery shows.
Swiss firm Rigitrac’s EWD 120 diesel-electric tractor is probably still the most radical example of the genre.
The tractor’s 120hp Deutz engine is able to provide 85kW (115hp), which powers four wheel motors in the tractor’s hubs and is capable of 65kph.
The Rigitrac’s electric wheeldrives run at 85% efficiency, compared with the 65-70% efficiency of the hydrostatic units on the Swiss maker’s standard machines.
How does it work?
here’s no need for a transmission or differential – mounting an electric motor in the hubs means each wheel is propelled individually and it avoids the heat, noise and inefficiency of a combustion engine.
It also means electric actuators can be used to accurately control functions that are usually hydraulically controlled, such as steering and linkage.
The pto could also be powered independently of ground speed.But it’s near impossible to power large tractors (above 50hp) by electricity alone. Powering implements is fine, but tractors are so big that the quantity and weight of deep-cycle lithium-ion batteries makes it a no-go.
There’s also the problem of the high voltages of batteries and motors required by a tractor – maintaining a 100kW, 500v system in wet conditions and carrying out repairs in the middle of a field is a recipe for trouble.
A far safer alternative, like most of the other fuel types we’ve covered, is to combine it with an diesel-burning engine.
Strengths
- Electric motors generate high torque at low rpm – low speed, high-power applications
- Low maintenance
- Infinite range of rotation speeds
- No idle – saves energy
Weaknesses
- High voltages potentially dangerous
- More complicated to service/fix
- Expensive
Availability and timescale | 7/10 |
Current research | 7/10 |
Strengths v weaknesses | 6/10 |
Total | 20/30 |
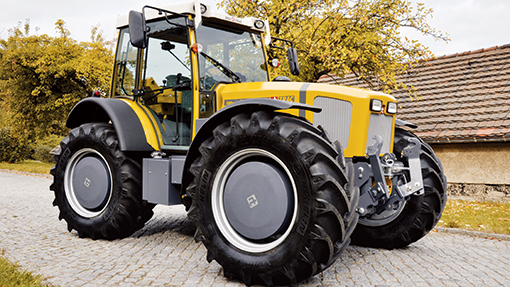
Has it been used before?
Since the first compression ignition engine was invented in 1892, oil has been the fuel of choice.
However, supplies deep under Earth’s crust are finite, so the focus has turn to making a more renewable form of diesel that can be used in the same engines.
The result is RME (rape-methyl-esther), which has emerged as the biodiesel success story. It is made from oilseed rape and can fuel most diesel engines without modification.
It is used either on its own or in a mix with diesel fuel and has been commonplace for about five years.
The biodiesel content of the average farm tank is about 10%, but it has several drawbacks. It pulls in moisture from the air which encourages water to build up in the tank.
It also provides a source of nutrition for bacteria already in the fuel and encourages them to multiply, which can block engine filters. These can both affect the running of the engine it fuels.
How does it work?
Biodiesel works in a similar way to mineral diesel. Burning RME reduces carbon monoxide, particulates and hydrocarbon emissions but increases the output of NOx.
However, modern-day engines with emissions-preventing gubbins attached don’t take kindly to high levels of biodiesel.
With the Renewable Energy Directive requiring 10% of transport energy to be renewable by 2020, biodiesel looks set to be the only form of renewable energy that is likely to be available on the required scale.
However, whether biofuels are the long-tern answer to fossil fuels is questionable because on a world scale the demand for food will be too high to commit large swathes of land to produce fuels.
Strengths
- A makeweight to begin the change to renewable fuels
- Can be used in current engines
- Affordable
- Available now
Weaknesses
- 10% less power
- 2-3% higher fuel consumption
- Prone to oxidation and water absorption – limited shelf life
- OSR for fuel takes up food-producing land
Availability and timescale | 10/10 |
Current research | 10/10 |
Strengths v weaknesses | 8/10 |
Total | 28/30 |