How potato growers are saving costs with combi planters
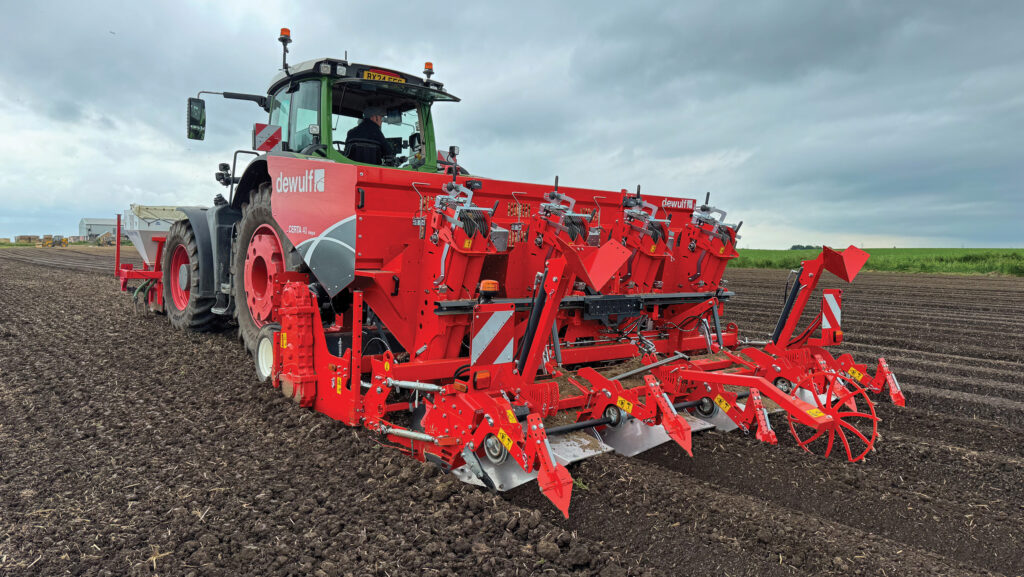
The combination potato planter market is hotting up, with four manufacturers now jostling for share as UK growers look to cut spend on crop establishment and reduce their reliance on tough-to-find labour.
These machines essentially combine a cultivator – typically a rotary tiller or power harrow – with a planter, allowing growers to trim the often high number of field operations by planting straight into prepared ground.
They have been popular in parts of mainland Europe for years and have been gaining traction here since Standen Engineering began importing the Cultivator-Planter range from Belgian firm Baselier in 2019.
See also: Video – camera technology improves marketability for potato growers
Buyers have largely been confined to the Grade 1 silts and black soils in Lincolnshire and East Anglia but are now appearing on slightly heavier and stonier soil types elsewhere.
Reduced cost is a key driver, with fuel, labour, and maintenance all lower when using a combination system rather than the traditional approach common on many farms that involves subsoiling, ploughing, ridging, bed-tilling, destoning/declodding and then planting.
Growers are also becoming more mindful of soil health, so are looking to work land less, particularly if producing for processing markets where skin finish is not a top priority.
Some processing contracts now allow whole crop delivery straight off the field without grading, as stone, clod and stem is removed at factory intake.
This allows destoners/declodders to be ditched, and use of tilth-making tools like bed tillers and power harrows rowed back.
Increasingly, larger farms are opting for two establishment systems – one traditional for heavier ground, and a combination planter suitable for the rest of the potato area.
Joining Baselier in the combi planter market over recent seasons are Grimme, AVR and, most recently, Dewulf.
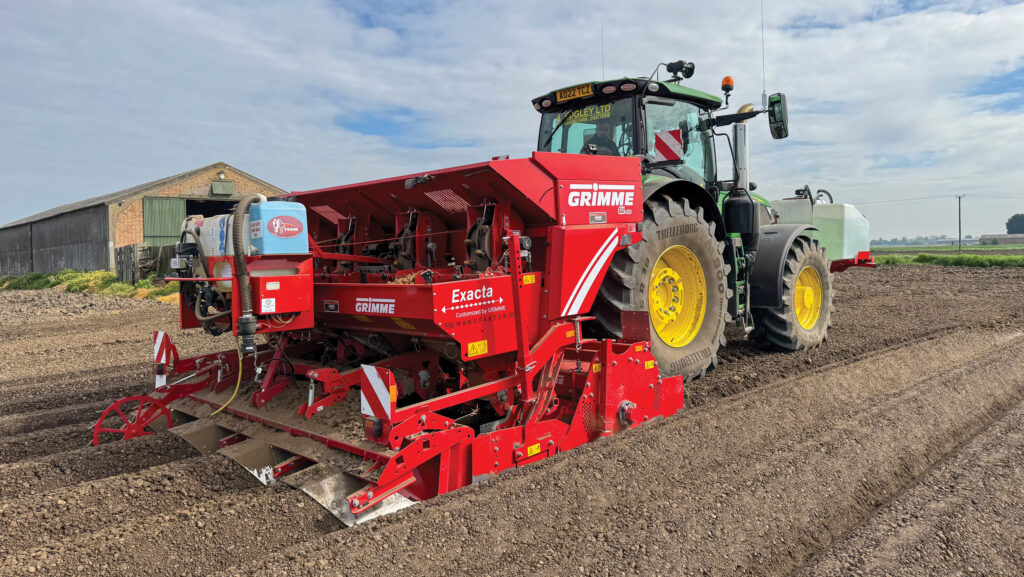
© Adam Clarke
A Edgley’s Grimme GL420 Exacta
Luke Edgley and his father Stephen have managed to almost halve their potato establishment labour bill since investing in Grimme’s GL420 combi planter.
The business grows wheat, pulses, sugar beet and potatoes across 470ha, all within a 10-mile radius of its base at Chatteris. There is also a proportion of land in environmental agreements.
Potatoes are grown for the fish and chip shop trade and Luke says the potato area has fluctuated over recent years, reaching a low of 100ha during the Covid pandemic. It is typically between 140ha and 160ha.
Some years ago, the firm used a two-row Standen Big Boy cup planter to get seed into the ground, but as its acreage grew, it needed to increase work rates.
This led to investment in a two-row Grimme GB215 belt planter in 2013.
At that time, on its heaviest clay loam soils, ground preparation consisted of a pass with a Cousins V-Form or Patriot, then a 6m power harrow, a three-bed bed-tiller, and a team of two or three destoners.
“We had six or seven staff at planting. Sometimes there was even one extra on the telehandler managing seed,” says Luke.
Spring 2021 was a slow planting season and staff were consistently letting them down.
Combined with ballooning production costs, it forced a decision to drop destoning/declodding operations for the first time the following year, instead relying on more vigorous bed-tilling with the addition of a packer roller to break up clods.
“It went well and we found it didn’t make any difference to the yield or quality of our crops. In some fields, we saw benefits.
“As there were no clods in the wheelings, it made life easier at harvest,” he explains.
In the same season, Grimme brought out a demo GL420 Exacta combination planter and, on the farm’s easiest black soils, it required just one prior pass with a power harrow.
On heavier soils, they found that a pass with the Patriot and one or two with the bed-tiller was enough to prepare an adequate seed-bed, convincing Luke that a combi system was the way forward.
“Depending on conditions, we’ve gone from up to seven passes to between two and four. That’s a big saving in diesel and labour. At £1,000 a week for tractor hire, we’ve cut costs there as well,” says Luke.
When quizzed about work rates, which are presumed to be slow, he says the operation is covering as much ground, on average, as before.
“On good going we can be doing more, up to 8ha a day. On cloddy, heavier ground we can be down to 4ha a day, but we are using fewer men and machines.”
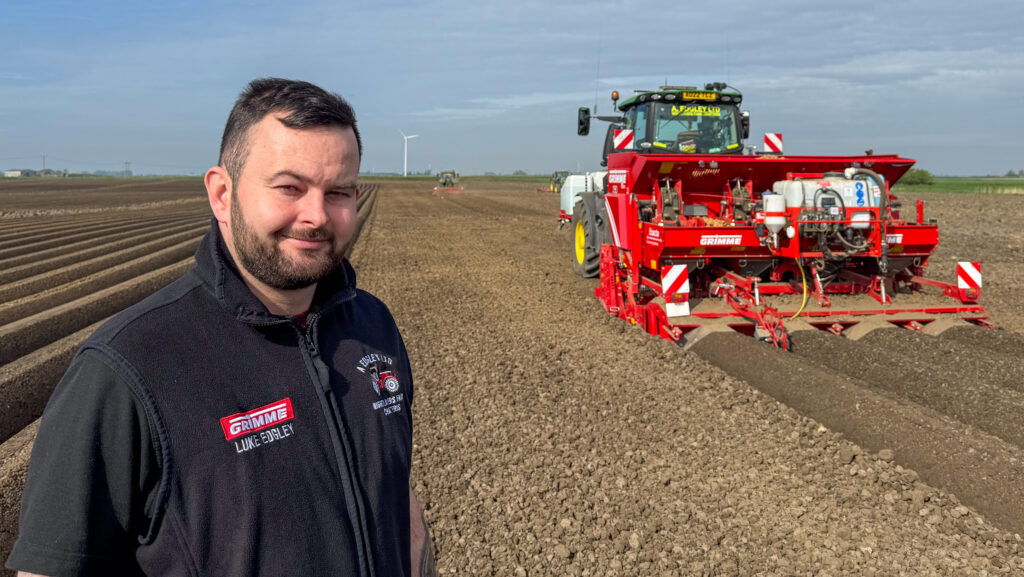
Luke Edgley © Adam Clarke
Better drainage
Another advantage is that the system is more weatherproof. Where beds were formed and destoned ahead of the planter and it rained, they often needed reworking to aid drying.
Conversely, prepared ground ahead of the combi generally drains well and, as the integrated rotary tiller is reworking the ground anyway, it doesn’t need stirring up ahead of planting.
When choosing the planter, brand loyalty to Grimme meant the farm didn’t consider looking at the Baselier, which was the only other option available at the time.
Initially, he wanted the most basic machine with manual drive, but Grimme made the decision to offer a high specification as standard, taking a few decisions out of Luke’s hands.
This meant the Exacta’s four planting units are hydraulically driven and having section control has provided further financial savings for the business.
“We were always over-planting by a few metres, then cultivating the end of the rows out. I’m a still bit cautious on the overlap setup, but it’s helped save a lot of seed.”
Another user-friendly feature is auto depth control. Connecting the Grimme system to the John Deere 6250R isobus, sensors on the front packer and rear shaping hood tell the tractor to raise or lower the link arms to keep depth even.
Luke says this works reasonably well through variations in soil type, but thinks a trailed machine might hold depth better than the current linkage-mounted setup.
Many GL420s would be on 400hp-plus tractors, but Luke opted to keep the machine as light as possible to avoid unnecessary soil compaction.
The only issue with using his John Deere 6250R is weight balance, with the planting rig weighing about 5t empty and a hopper full of seed taking it up to 6.5t.
The Edgleys made the decision to move to liquid fertiliser when the planter was purchased, so a 1,500-litre front tank was supplied, complete with 500kg of additional weight between the tank and tractor.
“It means I can run the tank down further and still have enough weight on the front to pick it up. For us it’s the perfect match.”
Other options include tungsten-tipped bed-tiller tines and plastic liners in the shaping hoods to help soil flow. There are also wheel track eradicators behind each tractor wheeling.
The machine was purchased in 2021 for £90,000, but retail price for a similarly high-spec model is now around £136,000 given inflation since the deal was agreed.
A Edgley’s Grimme GL420 Exacta spec list
- GR300 rotary tiller with four 90cm row cup planters
- Single-row hydraulically driven planting elements
- Section control and variable planting next to tramlines
- 2t seed hopper (1.6t fixed with 400kg extension)
- Auto depth control
- Hydraulic pressure adjustment on shaping board
- Priced from £136,000
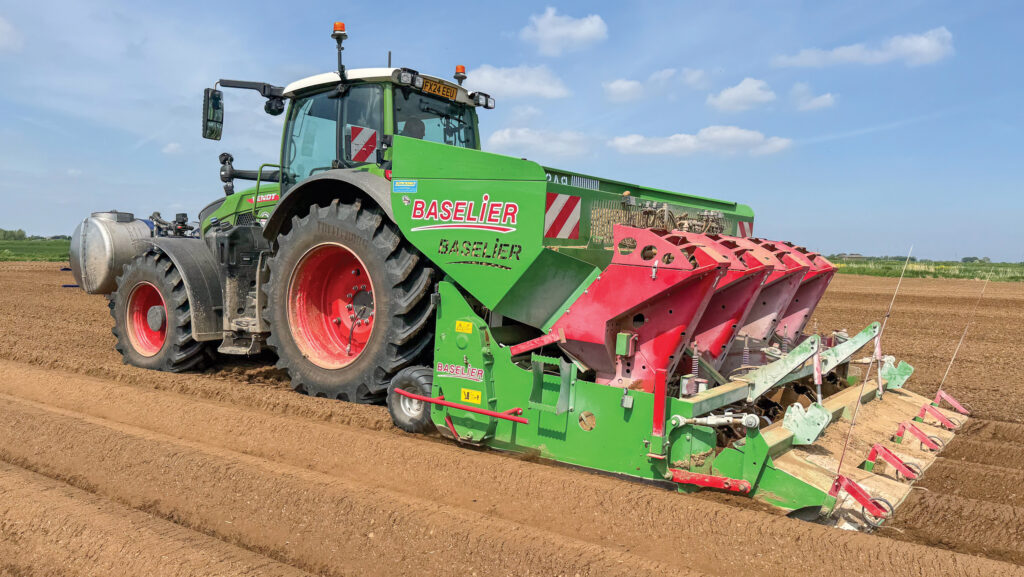
© Adam Clarke
Baselier offers consistency for TH Clements
Producing veg crops across 4,500ha of Lincolnshire Grade 1 silts, TH Clements near Boston has a lot of kit to manage, so removing passes from the potato planting process has been welcome.
In 2021, it moved from a Standen SP440 cup planter to a Baselier Cultivator-Planter to simplify establishment of its circa 240ha of potatoes grown for the pre-pack market.
Head of farming Neil Sharpe says spuds slot into a seven-year rotation that includes various brassica veg, vining peas and wheat on a 60-40 split of rented and owned land.
Between 50% and 60% of the crop is Maris Piper, with the remainder a mix of white and red varieties area based on customer requirements.
The business takes several approaches to preparing land ahead of potatoes, with a proportion flat lifted, ploughed, rotavated, power harrowed once or twice, and then planted.
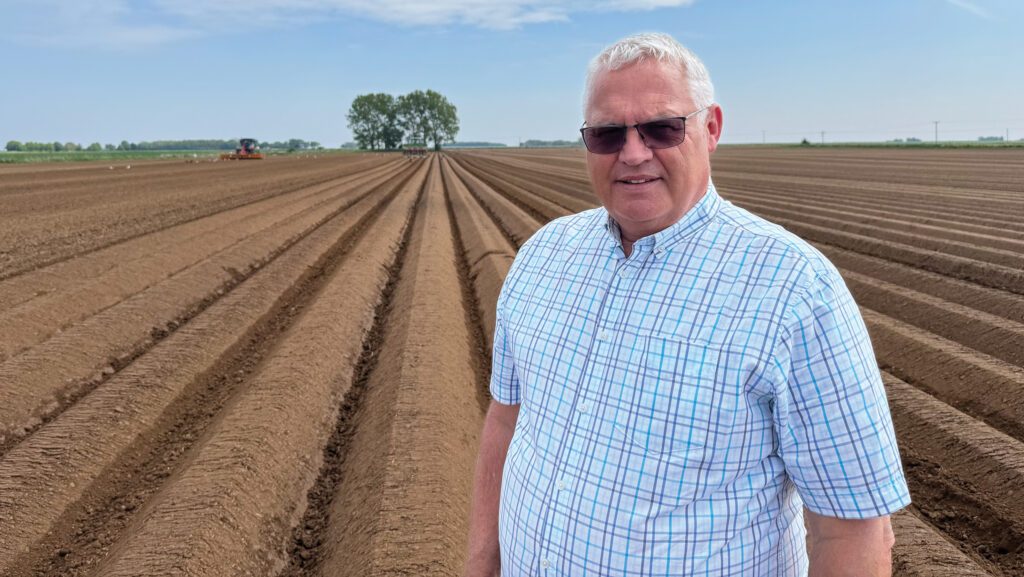
Neil Sharpe © Adam Clarke
Aiming to make the ground a bit more friable before land preparation and to avoid overworking it, the firm has been experimenting with cover crops over recent seasons and Neil says results are looking promising.
In some fields, a Hutchinsons Veg Mix cover crop is established using a Kverneland DTX cultivator with broadcast seeding unit in the autumn.
This starts to die off in January/February before a final glyphosate application to ensure a complete kill ahead of any soil being moved.
“On some fields, we’ve been able to go straight in with a power harrow and Baselier planter and that’s done the job.
“It could offer us a significant cost saving and we’re also mindful of our carbon footprint now.
“I wouldn’t want to quote figures, as the system is still a work in progress, but it’s showing immense promise and the planter is central to its success,” says Neil.
He says he looked at a range of planter options before deciding to go with the four-row Baselier combi, drawn in by its simplicity and ease of use.
Baselier offers hydraulically driven elements, but most customers choose the land wheel drive option that’s easy to use for any operator.
Neil’s machine – which is up to a tonne lighter than the competition – brings together a FA380-W hook tine cultivator and cup planter with Marathon planting elements.
Tungsten-tipped hook tines and a 500kg hopper extension – taking capacity up to 2t – were optional extras.
Consistency of depth and seed spacing have stood out since its arrival, and a row of wheels at the front of the machine help it follow the ground well to improve accuracy.
The Marathon planting elements feature a cup designed to handle larger or longer seed.
Neil says it easily deals with the farm’s typical seed splits of 35-45mm and 45-55mm, but has struggled to eliminate doubles when planting 25-30mm seed. However, he points out that most cup planters would fare similarly with such small tubers.
For 2024, the rig is hooked up to a brand-new Fendt 728 with central tyre inflation, giving the operator the ability to drop pressures easily and reduce the risk of root-restricting compaction issues.
Combined with wheel track eradicators, he has no concerns about the operation’s impact on soil or crop health.
“The operators like it and we’re saving on a tractor and passes [during land preparation]. We’d have another one and see no need to consider anything else just now.”
TH Clements’ Baselier Cultivator-Planter spec list:
- FA380-W hook tine cultivator with Marathon cup planter
- Four 90cm rows with spindle depth adjustment
- 2t seed hopper (500kg from optional extension)
- Ridging discs with spring pressure adjustment
- Nine depth wheels with tractor profile and hydraulic adjustment
- Tungsten tipped hook tines
- Priced from £75,000
Dewulf taps into UK market with Certa 40
Belgian root crop machinery specialist Dewulf has been making a combination planter for the 75cm rows preferred by the European market for a couple of years.
Having noticed the growing demand in the UK, it is offering its linkage-mounted Certa 40 Integral four-row combination planter on 90cm row widths for the 2025 season.
Farmers Weekly went to see it on demonstration in Norfolk in June and it has a similar look to Baselier’s version, with a row of wheels at the front of the machine.
Michael Gott, sales manager for UK Dewulf dealer AgVantage, says these have a slightly larger diameter than the competition to better carry a greater weight, which in part comes from the machine’s hefty 3t seed hopper.
Operators can control or adjust almost all the machine’s different elements from the cab, including tiller and loosening tine depth, and the hydraulic automatic seed depth control on the openers.
Covering discs behind the planting elements achieve a good bed shape by keeping the hoods full of soil. These can be specced scalloped instead of smooth to work better in sticky conditions.
The bed tiller’s rotor cover is nylon lined to ease soil flow in sticky soils.
The hood is also spring loaded and can be pushed down by hydraulic rams towards the rotor from the tractor seat during operation.
This cleans the hood and eliminates the need to do so by hand.
The tunnels on each planting unit have manual adjustment, allowing operators to tweak the gap between them and the cups to suit seed size. This helps it handle large and small seed alike.
Miss detectors help ensure the planter is achieving target plant populations and, on each individual row, the operator can alter the percentage of the plant population target achieved.
This is useful when using the optional tramlining system, as it can place more seed in rows adjacent to tramlines and prevent too many oversized tubers at harvest.
Other options include tungsten tipped tiller tines and erosion stops on the back, which create dams between the ridges to help stop surface run-off.
Michael says there are already a couple of machines sold off the back of 2024 demonstrations. A full spec model will cost potential buyers about £120,000.
AVR Ceres 450 gaining UK interest
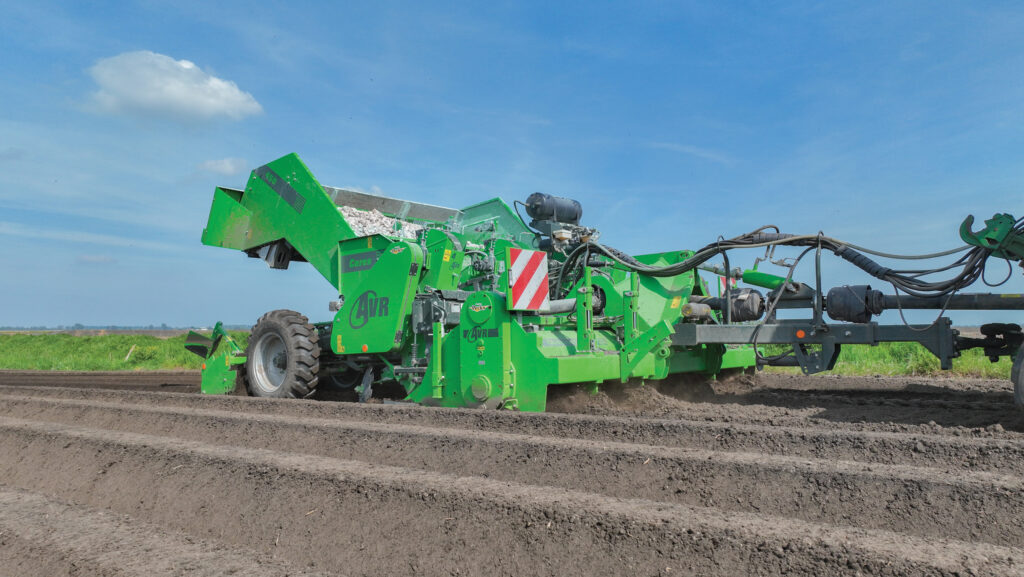
© AVR
Another relative newcomer to the UK combination planter market is Belgian manufacturer AVR, with a handful of machines now sold in England since establishing a dealer network and offering on-farm demos over the past two seasons.
The firm’s western Europe sales manager Kristof De Ruyck says it has been making cultivator-planter combinations for several years and they now make up 80% of its planter sales in Belgium.
This is helped by a regional focus on processing potato production, which has pushed growers to look for efficiency and cost savings as returns are lower than in the fresh market.
While the trend towards processing is slower in the UK, it is gathering pace and AVR is now pushing for sales of its combination planters through its growing dealer network.
It offers a nimbler mounted combination planter, the Ceres 440, which can be specced with a front-mounted MultiForce rotary cultivator and/or a Compact rotary cultivator to the rear.
However, Kristof says its flagship Ceres 450 trailed planter is likely to prove the most popular option for British growers.
This is because it suits higher horsepower tractors and offers greater flexibility when adding liquid or granular fertiliser or pesticide applicator options to the planting rig.
AVR believes the vast majority of customers want to control the machine via GPS, so there is no mechanical option. Instead, all four planting elements are hydraulically driven as standard.
The hydraulic drive allows the operator to adjust planting density from the cab, which is particularly useful for rows adjacent to tramlines or dead beds where more seed helps reduce oversize tubers.
The company’s control system lets operators run two additional applicators – such as liquid fertiliser and in-furrow fungicide – through the one touchscreen unit.
This flexibility means that the Ceres 450 can fit seamlessly into any existing setup.
According to AVR, its ridging hood is a standout feature, as it requires less pulling force than the competition, offering potential fuel savings for the user.
There is plenty of automation on the Ceres 450, with the option of an automatic tipping bunker – a hefty 4t on 90cm machines – and sensors on the ridging hoods to keep them full and at the right pressure.
A slope sensor can also help adjust the cup belt agitators, reducing the risk of doubles or gaps in each row.
Kristoff says the automation options and touchscreen are designed to make life easier for new operators or those on the machine for short periods each year.
“You can do a lot of good things with a planter, but also a lot of things wrong, so it’s important to start in the right way and not make things too difficult.
“There are many examples of how the machine has been made simple,” he adds.
Available through Malpas Tractors and TR Machinery in the west and G&J Peck in the east, there are about 35 options on the planter.
Kristoff says most UK businesses will opt for all the bells and whistles.
Growers can expect to pay £107,000-£112,000 for a high-spec Ceres 450, including the cultivator (typically an AVR GE-Force hook tine).