Buyer’s guide: Camera-guided sugar beet hoes
Mechanical methods formed the backbone of in-crop weed control in sugar beet before herbicides arrived, and some farms have continued with both approaches to this day.
However, with rising input costs and active ingredient losses, and resistance to herbicides making some species tougher to control with chemicals across rotations, the historical exodus from old-school techniques has been crunched into reverse.
Growers are also considering the benefits of hoeing beyond weed control, including aeration of soil around the plants, the release of nutrients and reduction of capping and associated run-off.
Advances in guidance technology mean wider machines capable of nippier forward speeds are now available, and this makes the investment in one of the latest self-steering hoes more attractive.
See also: Side-shift linkage options deliver pinpoint crop weeding
And the resurgence is not just in wide-row crops either, as conventional cereal growers increasingly look to steel as another weapon against problem weeds.
The sea change is betrayed by some high-profile manufacturer acquisitions in the mechanical weeding sphere, with Amazone and Lemken both snaffling up established equipment specialists over the past three years.
Funding
Another driver has been new Defra grant funding – applications for round one of the Farm Equipment and Technology Fund closed on 7 January and applicants will get up to £20,949 towards a 6m+ camera-guided hoe.
However, those worried about missing the boat may still be able to apply for money through the Farm Transformation Fund, which lists robotic weeders as an eligible item for a grant if the machine meets certain criteria.
See the gov.uk website for more information on the Farm Transformation Fund.
Drill width
Experts say the most important thing to consider when buying a hoe for weeding in sugar beet, or any other crop, is matching the machine’s width with the drill used for establishment.
Even with today’s RTK guidance systems, which enable sub-inch drilling accuracy and repeatable positioning, there can be some error in row width between drill passes.
This means using a 4m hoe behind a 6m drill, for example, runs the risk of taking out whole crop rows. Therefore, drill working width should always be divisible by hoe width.
The options
Here, we look at some of the options available. Although most of the focus is on sugar beet, all have the flexibility to be adapted to most other arable crops without too much stress.
All manufacturers offer bespoke builds and a similar and equally wide range of soil-engaging parts, crop protectors and options such as section control, band spraying and liquid or granule fertiliser systems, even if not mentioned in this article.
Einbock
Norfolk-based Terrington Farm Machinery imports Austrian firm Einbock’s Chopstar range of hoes into the UK, with the 360 the most appropriate for use in crops such as sugar beet.
Rear-mounted options range from a rigid five-row machine to a 13.1m 24-row hoe, which has a hydraulic retracting and double folding frame.
Those looking for a front-mounted version can choose from a rigid six-row setup, or an eight- or 12-row with a hydraulic folding triple frame.
As with most manufacturers, the depth wheel and soil-engaging parts are attached to the toolbar via a parallelogram configuration to facilitate contour following.
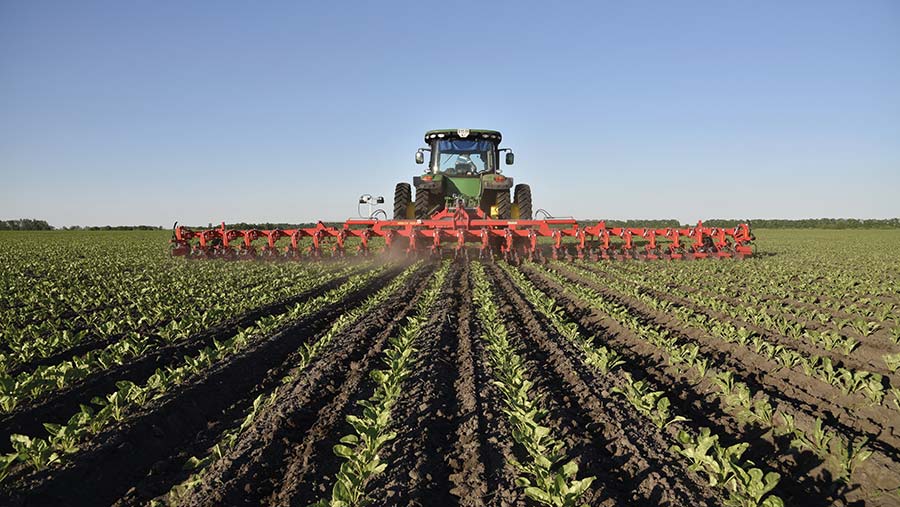
© Einbock
Although tine and point options are almost endless, Terrington typically sells machines for use in sugar beet with two Vibro-tines with 160mm duck foot sweeps, followed by a single Vibro-tine with a 180mm sweep, for each row.
There is also the option of crop deflector plates or discs, with the former being the most popular option to minimise any crop damage.
Camera guidance is becoming more popular, and Einbock’s Row-Guard system comes with a separate headstock that facilitates 500mm hydraulic side shift.
Based on the Claas CultiCam, the cameras analyse leaf structure of the plants based on colour information and/or 3D surface models to keep tines away from the crop.
One camera is sufficient for accurate steering of a 12-row machine, but a second is required for larger models or where hydraulic section control is fitted to avoid misses or crop damage on headlands.
A 12-row Chopstar 3-60 with Row-Guard guidance retails at £35,000.
Garford
The company has been selling guided hoes since 2001, when it adopted the Tillett and Hague camera guidance system for its Robocrop hoe.
More than 20 years later, the same inter-row machine is still available to arable growers, alongside its more sophisticated inter-plant technology aimed at high-value crops.
In sugar beet, six-row, 12-row and 18-row front- and rear-mounted implements with guidance are available, with the 12-row option currently the most popular. Section control is also an option.
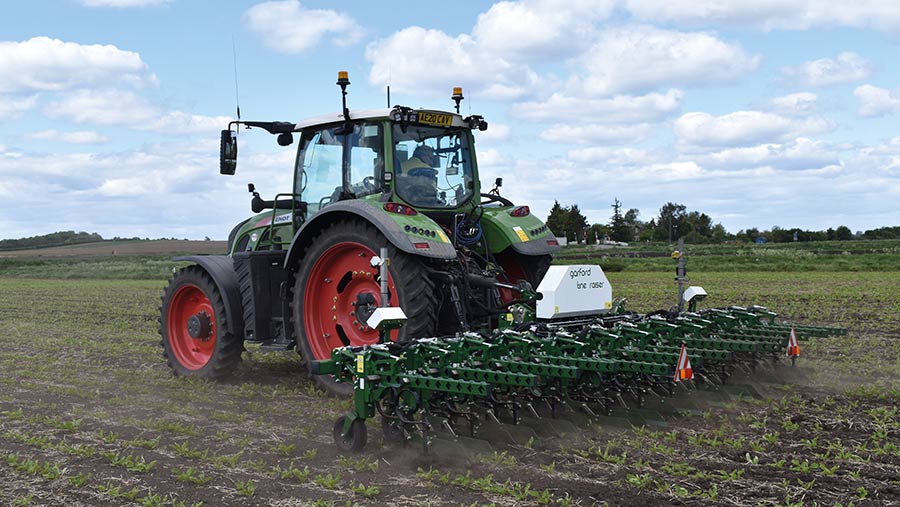
© Garford
Its tine frame is fully adjustable, so as well as working in sugar beet, each can be adapted to work in other crops, if required, including cereals and maize.
Garford’s technical sales manager, Allan Knight, says a forward speed of 12kph is common and higher speeds are possible due to the firm’s Pressure Down system.
Special pressure rams keep the soil-engaging parts in work, improving penetration in hard conditions, and the system also stops chatter and bounce when working at speed.
Nearly all Garford customers now opt for the guidance system, which works by cameras viewing the crop foliage to the front of the machine.
A computer then processes the images and picks up the higher number of green pixels associated with the crop and shifts the hoe accordingly.
It makes life much easier for operators, reducing fatigue, and increasing speed and accuracy – the standard inter-row model can work just 10mm from the crop.
The same camera system is used across all Garford equipment, whether salad, veg, cereals, maize or sugar beet, and can work 10 rows at 4.5cm to two rows at 80cm (pumpkins, for example).
A basic 12-row Robocrop guided inter-row hoe starts at £42,000.
Bednar
Two rear-mounted Rowmaster hoe models from Czech tillage kit specialist Bednar are available to UK growers through a large network of dealers across the UK, primarily Case IH franchises.
The RN_S is specifically designed for sugar beet on spacings from 45-50cm. There are four models in the range – a 3m six-row machine, a 6m 12-row, a 9m 18-row and a 12m 24-row.
The RN provides more flexibility, which will be appealing to contractors or farmers working in a broader range of row crops.
Row widths on the RN have greater adjustment, with working elements able to move from 40cm to 80cm spacing, and a ground clearance of 80cm, making it suitable for use in maize.
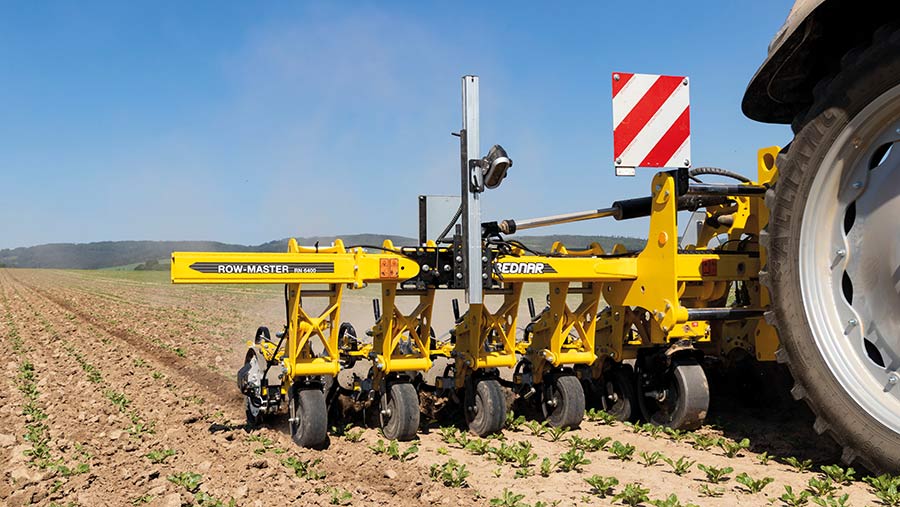
© Bednar
There is a 4.8m toolbar working six to eight rows, depending on configuration, a 6.4m machine weeding eight or 12 rows, and, finally, the largest 9.6m hoe capable of cleaning up 12 or 18 rows.
Bednar offers a deflector plate and disc for the protection of plants, with the firm’s Warren Rivers-Scott advising discs for those covering a large acreage, as they don’t wear as fast.
The usual array of tines and points are available for both the RN and RN_S, and significant adjustment allows operators to work as close to the crop as they dare.
To help with steering accuracy, Bednar uses the Claas CultiCam guidance system, which works from the two-leaf stage of the beet crop.
A 12-row RN 6000 S with guidance and LED light kit for night work costs about £36,000. A 12-row high-clearance RN 6400 with a similar spec would come in at £45,000.
Buyers can add a liquid fertiliser system, and its front-mounted Ferti-Box is an option for solid fertiliser. Requesting a split hopper adds the ability to undersow maize with grass.
A Ferti-Box with fertiliser and small seed application functions would add £25,000-30,000 to the hoe price.
Monosem
Though synonymous with precision drills, Monosem also builds inter-row hoes and its range is available through Fakenham-based UK agent Toucan Farm Machinery and its dealership partners.
The long-standing Super-Crop inter-row cultivator is still available, but due to increased interest in mechanical weeding over recent seasons, the firm updated its offering with the Multicrop.
One of the key differences between the Multicrop and other hoes is its depth-control wheels, which are 350x120mm, compared with the 300x100mm on many other machines.
This apparently enables it to carry the more robust build of the Multicrop, and double canister bearings extend depth wheel longevity and reduce maintenance.
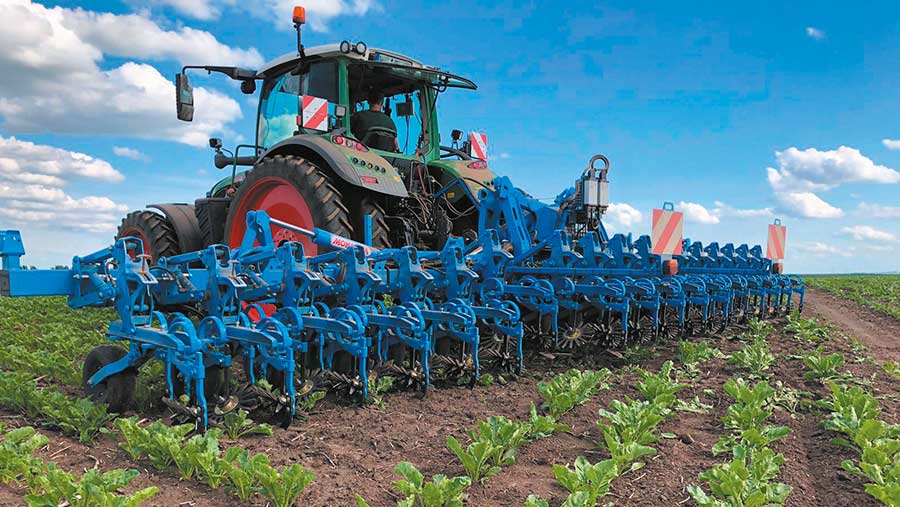
© Monosem
The hoe has a quick and simple tool-free depth-adjustment mechanism, with a T-Bar and linkage allowing the operator to tweak each row in 5mm increments independently.
All machines are custom-built to order, but sugar beet customers would typically request a 3m frame for six rows, 6.2m frame for 12 rows, or 9.4m for an 18-row version.
The 18-rower comes with hydraulically folding wings, so it allows operators to turn it into a 12-row hoe quickly and may appeal to contractors working behind a range of drill widths.
Beet in the UK is grown on 45cm or 50cm spacings and row widths can be adjusted easily by loosening a single swing bolt and sliding units up or down the toolbar, adding to flexibility if working across systems.
Having a long parallel linkage supporting working parts, the hoe has high ground clearance, which makes it suitable for both sugar beet and maize.
Guidance can be offered on Monosem machines and, in the UK, the same Tillett and Hague system used by Garford is preferred.
Toucan Farm Machinery’s Steve Twist says this is partly down to the ability to add or change cameras relatively cheaply, as the system is managed by a central control module, rather than having the electronics built into the camera units, as with competitor setups.
Hydraulic section control is an option, with the system run through a supplied Monosem Touch Mini terminal or the tractor’s Isobus.
A camera guidance-ready 6m, 12-row Multicrop geared up for sugar beet retails at £27,450, with the £25,000 camera system making a grand total of £52,450.
Ferrari
Ely-based Standen Imports sells mechanical weeders from Italian manufacturer Ferrari, with the Remolite currently the most appropriate for use in sugar beet.
The largest in its catalogue is a 6m, 12-row model, but Standen’s Richard Parrish says it is possible to build bigger, bespoke hoes on request.
The weeding element is standard fare – independent depth control via leading rubber wheels and up to five soil-engaging elements in each row, all attached to a parallel frame for contour following.
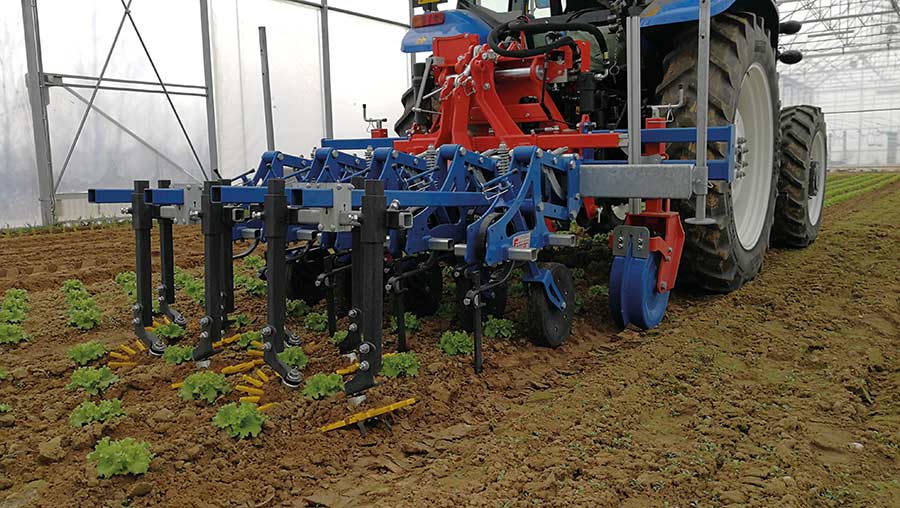
© Ferrari
Typically, the implement is fitted with sprung tines and duck-foot shares. Finger weeders for in-row weeding and following press wheels can be added where necessary.
Hoe guidance comes from the Claas CultiCam system, which hydraulically shifts the hoeing element from side to side on a headstock mounted to a three-point linkage.
The machine has flanged steel gauge wheels on the headstock, which cut into the ground to stabilise the hoe and prevent excessive movement, particularly on side slopes.
A 6m, 12-row Ferrari Remolite has a £19,750 list price, with an additional £28,500 for the CultiCam system taking the price up to £48,250.
For those wanting another level of sophistication, the firm also builds the Remoweed inter-row and inter-plant weeder, which uses an infrared optical bar to detect weeds and plants.
Each row unit then uses a pair of hydraulic arms with cutting blades to take out weeds as little as 1cm from the crop.
While this technology hasn’t made it into arable crops just yet, it may do in certain situations when beet is grown on the same farm as high-value horticultural crops, or if herbicide losses continue apace.
A single-bed, four-row machine costs £40,000, while a 12-row version is £150,000.
Hatzenbichler
Although not unique to Hatzenbichler, importer Opico’s mechanical weeding product specialist Richard Amphlet says its quick-coupler headstock will be a major selling point as mechanical weeding becomes more mainstream.
The demand for mechanical options in cereals is on the rise, and these are often grown alongside commonly hoed crops such as vegetables, sugar beet and maize.
Optimal timing of hoeing depends on weather, soil conditions and weed growth and, rather than having to tweak the setup, growers could opt to buy a ready-to-go toolbar for each crop. The operator can then drop one off and pick the other up without wasting time in the yard with a spanner when conditions are ideal.
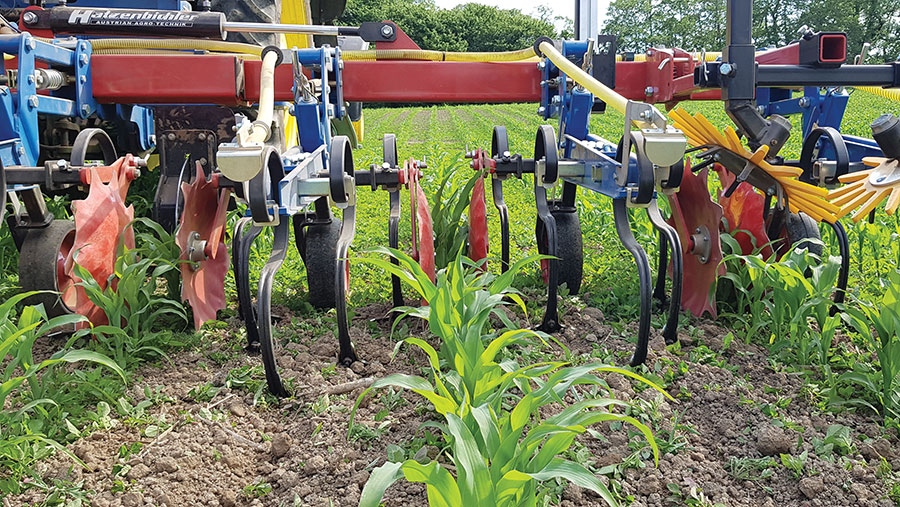
© Hatzenbichler
Hatzenbichler offers its three-point linkage-mounted headstock with manual or camera-guided hydraulic side shift, alongside three front or rear toolbar options.
These include a 3-18m toolbar with 12.5-30cm row widths for combinable crops, a 3-12m version with 35-50cm rows for sugar beet and the like, and a 3-12m option on 50-75cm rows for maize.
The first two come with one or three tines per parallelogram, fitted with Vibro-tines and duck-foot shares as standard. The third toolbar has three or five S-tines with A-shares as standard.
For those who don’t want to invest in multiple toolbars, there is still flexibility to adjust row spacing to different crops, with a simple bolt-and-clamp system allowing parallelograms to slide across the beam.
Mr Amphlet says guidance is essential for increased forward speeds, particularly at narrower spacings, and Hatzenbichler hoes are offered with the Tillett and Hague system.
Although customers can reduce the spec, two cameras are offered as standard to overcome any potential shadowing issues. This comes at negligible extra cost.
A 6m, 13-parallelogram, 12-row toolbar for use in sugar beet retails at £21,406, with a £32,793 headstock and twin camera-guidance system giving a total book price of £54,289.
Section control on that same 6m machine would add a further £14,978. Customers can expect a reasonable discount for the on-farm price.
Schmotzer
German mechanical weeding specialist Schmotzer was recently acquired by Amazone and updated its hoe range to include the Venterra 2K-series in 2021.
Working widths are up to 6m, which can accommodate 12 sugar beet rows on 45cm or 50cm spacing, but different sizes are available on request.
New KPP-L (large) parallelograms offer ground clearance of up to 100cm and, if specced with section control, can lift tines up to 50cm, so lengthens the working window if owners wish to use it in taller crops such as maize.
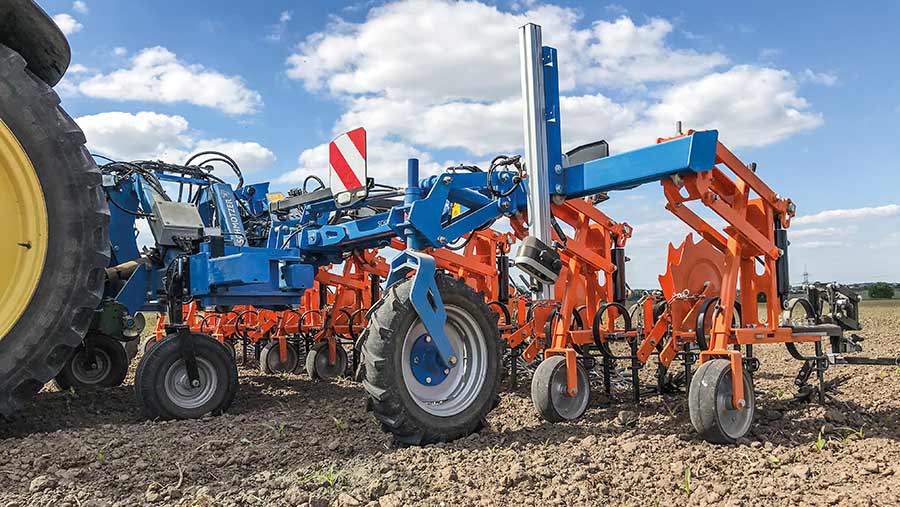
© Schmotzer
The machine carries three 160mm shares on each parallelogram in beet, with a fast-change system on the tines speeding up the process of replacing worn blades.
A range of row-protection discs can help shield small plants during early-season work, with the HSZ toothed disc the standard choice for most.
Finger weeders can be fitted to the back of the parallelogram for weeding in-row, while the firm’s tie-up with Amazone has resulted in the option of speccing an FT-P front tank for liquid fertiliser or in-row herbicide application when using the Venterra.
Guidance is branded as Horus Professional, but it is the same Claas system used on many other guided hoes.
List price for a basic 12-row machine with camera, shifting headstock and HSZ row-protection discs is about £44,000, increasing to £61,000 with section control and finger weeders.
Steketee
Following Lemken’s acquisition of Dutch company Steketee in 2018, its range of mechanical weeding solutions is now available through most of the firm’s UK dealerships.
Its standard inter-row hoe is the EC-Weeder which, like its competitors, can be set up and configured in myriad sizes and ways to suit the crop, environment, and customer needs.
Row widths range from 15cm up to 100cm, and off-the-shelf working widths extend to 13m, but the company has a 36m trailed machine working in French maize crops, so bespoke orders can be catered for.
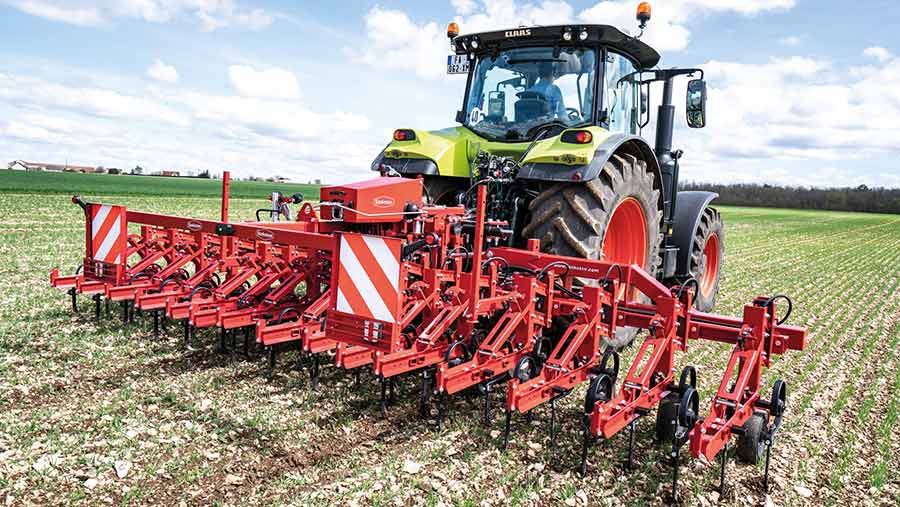
© Steketee
The toolbar attachments start with the Basic-Element parallelogram, which incorporates a crank-adjusted depth wheel. Various tine and blade options, crop protectors and following tools such as harrows or rotary weeders are then attached to the Basic-Element, depending on weeding or cultivation requirements.
Each Basic-Element unit can be quickly and easily shifted along the EC’s 80x80mm toolbar to match up with different crops.
Customers then have the option to add Steketee’s IC-Light camera-based guidance, which includes a camera, a touchscreen terminal/job computer and a parallel sliding frame to sit between tractor and weeder.
The system can be specced on new machines or bought separately to help steer older hoes, and works as close as 2cm to the crop at 15kph.
Options include LED lights to enable accurate night work and a joystick to manually control the headstock.
Additional cameras can be fitted for wider variants, which is useful in short work, and a quick hitch allows operators to swap between toolbars with different setups.
For sugar beet growers, Lemken’s Paul Creasy says 90% would be opting for camera-guidance systems. A 6m, 12-row machine with guidance has a list price of roughly £50,000.
Carre
Hoes from French manufacturer Carre are imported to the UK by North Yorkshire-based Keith Rennie Machinery, with the Econet range offering a plethora of setups to suit several crops, including beet.
The firm offers the Econet in trailed or mounted, rigid or folding and single- or twin-beam guise, depending on intended use. KRM’s Mike Britton says growers can order almost any size hoe, but the practicalities of large folding machines in the UK, particularly in terms of transport height or width, can be restrictive.
For sugar beet, there is a 9m, 18-row machine in the book, which will match up with some of the larger drills used across the cropped area.
Working elements include a heavy-duty configuration for crops such as maize grown on 75cm rows, and a lighter version for use in cereals and sugar beet.
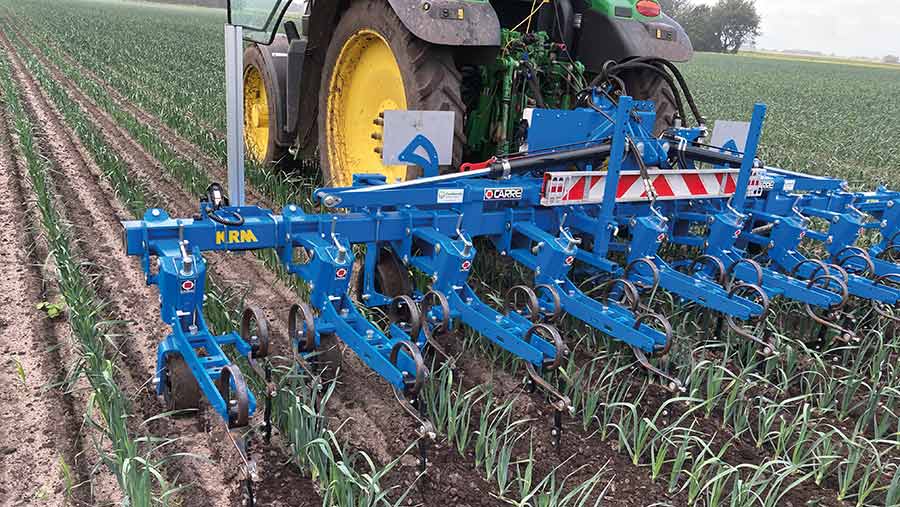
© Carre
The working depth and tine positioning are all adjustable without tools, so slight tweaks can be made quickly in the field.
Carre offers the choice of having the toolbar fixed or mounted on a headstock, which opens up the possibility of two guidance systems.
One uses paddles to physically feel out the crop rows and keep the hoeing elements hitting the target using a hydraulic side shift.
The second is a camera system, known as the SGI, which is essentially the Claas CultiCam rebranded, run from a simple touchscreen monitor in the tractor cab. Isobus hydraulic section control is an option.
A 6m, 12-row Econet SGI (including guidance) retails at £46,800, but buyers could expect a £8,000-£9,000 on-farm discount.
Thyregod
Inter-row hoes built by Danish manufacturer Thyregod are available through Norwich-based dealer BW Brewster and Son.
The TRV range comes in several iterations, with row spacing from 12.5cm to 90cm and widths from a rigid 3m machine up to the 18m of its Swingking trailed unit.
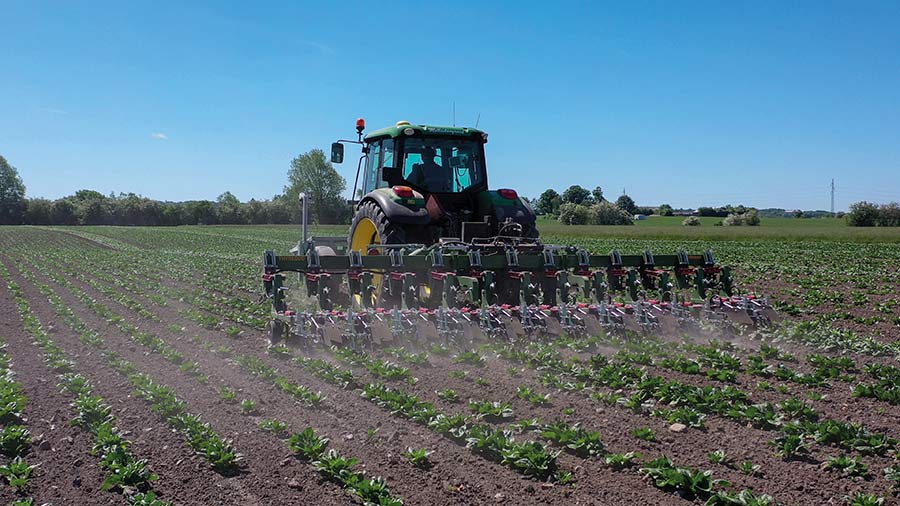
© Thyregod
Like some competitors, a generous 80cm ground clearance is one selling point, allowing its hoes to work without damaging taller crops at later growth stages.
Mechanical guidance or guidance using an optical camera system can be fitted on most models, with the toolbar shunted on a hydraulic side-shift headstock as it moves through the crop.
Section control and the typical range of tines, points, screens, and harrows are available to suit different crops and conditions.
Price for a 6m, 12-row machine with guidance is approximately £45,750.
User experience – things to consider before buying a guided hoe
Farm manager, Norfolk
Driven by the loss of herbicides, plus some problem weeds, Morley Farms in Wymondham, Norfolk, has been trialling a guided hoe in its sugar beet for the past two years.
Farm manager David Jones was offered the opportunity to use a 3m Steketee EC-Weeder in 2020 and a 6m guided version in 2021, and jumped at the chance to see how it would fit into his system.
While the Covid-19 pandemic made setup and support tricky, and scuppered any potential demonstrations during key weed-control periods, Mr Jones learned some valuable lessons.
Behind a 6m drill, the small 3m hoe obviously required more passes and resulted in significant crop damage on headlands.
In the second year, this was improved by having the wider version, but that was a lot heavier and with a small tractor on narrow row crops, wheelings were deeper.
Mr Jones says when buying a hoe, it’s worth considering the size of tractor available relative to the toolbar, making sure it’s appropriate for the implement without being overly heavy.
He also notes that overall machine setup and operation, including the guidance system, is not straightforward and a competent operator is required to ensure good results are achieved and damage to the crop is minimal.
Timeliness is why Mr Jones sees a hoe being used in a targeted way across smaller areas to get the best results, perhaps where there are specific problems such as the ryegrass in some fields at Morley Farms.
However, if only used across part of a farm’s beet area, it could make the circa £40,000-plus investment in a 12-row guided hoe difficult to justify.
“I certainly don’t think it will replace spraying. How it is best integrated with current systems and whether unit costs can be brought down is key, perhaps by using it for other purposes.”
Together with the British Beet Research Organisation, Mr Jones will be continuing to explore how and where mechanical weeding fits on the farm, with a view to providing informed advice to the sugar beet grower base.
Grower and contractor, North Yorks
The importance of a competent operator is echoed by North Yorkshire grower and contractor Nigel Coning, who harvests more than 800ha of sugar and fodder beet each year.
He invested in a 12-row Garford Robocrop camera-guided hoe with in-row and band-spraying capability four years ago, and has found it logistically tricky to fit it into his weed-control programmes.
Timeliness is critical to success with a hoe, and getting into crops in ideal conditions has been difficult over a large area when battling catchy weather.
Furthermore, Mr Coning services a wide variety of customers – from small livestock farms growing fodder beet to large arable units growing sugar beet – so conditions for the guidance system vary and sometimes affect accuracy.
The hoe has also been following his 12-row Vaderstad Tempo drill in most instances, which is heavy and leaves ridges between rows, making consistent hoe depth control tricky.
“In good conditions and on the right farm, it is a very useful tool, but due to our drill, workload and the type of customers we have, it has been difficult to make work and is something to think about before buying.”