Remapped tractors boost performance for Cumbrian contractor
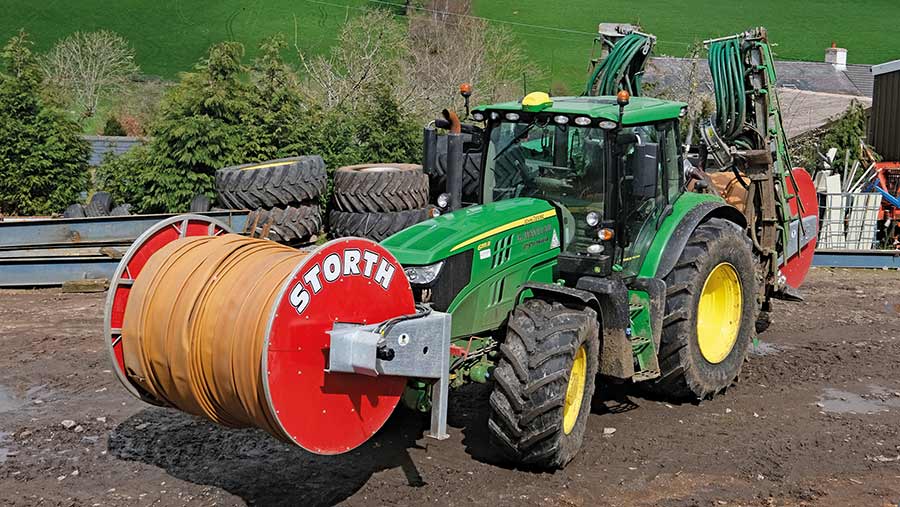
Dotted across the UK, our four Contractor Comment contributors will be giving us regular updates on the highs and lows of running an agricultural contracting business in their area.
Having introduced our Devon and Lincolnshire representatives in previous issues, it’s time to say hello to Cumbrian contractor Graham Hayllar.
See also:Â 8 new tractors arrive as A&B Contractors updates fleet
Business facts: G Hayllar, Arden Holme, Warcop, Cumbria
- Main services Forage harvesting, umbilical and tanker slurry spreading, muckspreading, spraying, fertiliser and lime spreading, grain crushing/crimping, cultivation work and drilling
- Other Workshop and steel fabrication, Cri-Man pump dealer, spare parts sales
- Staff Seven full-time, plus several part-timers and a few owner-operators
About the contractor
Graham Hayllar specialises in forage harvesting and slurry spreading in Cumbria’s undulating Eden Valley
Main contracting enterprises?
There is precious little arable ground in this area, so our work revolves around stock farming, particularly dairy and beef.
As a result, we spend most of our time producing forage to go in the front end, and dealing with the slurry that comes out of the other.
Each season, our two foragers pick up about 4,000ha of grass and 200ha of wholecrop, all of which is within about 20 miles of the yard.
Our customers tend to do most of their own mowing, but we’ve got a set of Claas front-and-rears to cover some of the area, and we have two rakes, seven trailers and three tractor-mounted buck rakes.
Slurry also keeps us busy. Up to now we’ve been running two umbilical outfits with home-made pumping trailers, one of which is pto driven and one that has its own engine.
These move about 50m gallons of slurry a year, which is a bit of a push at times, so we’ve just finished building another to give some extra capacity.
We also built a 12,000gal nurse tank so we can pump to more remote fields – something that’s getting a lot more popular as people are looking to make the most of the nutrients.
On top of this, we spread about 4-5m gallons with tankers, which also get put to good use hauling to the nurse tank.
Other services include spraying, fertiliser and lime spreading, grain crushing/crimping, cultivation work and drilling.
Any forms of diversification?
We run a workshop carrying out maintenance and repairs for local farmers/contractors and a steel fabrication business that builds everything from garden gates to sheds.
Running alongside these, we have a shop that sells spare parts and equipment, as well as Cri-man slurry pumps and separators.
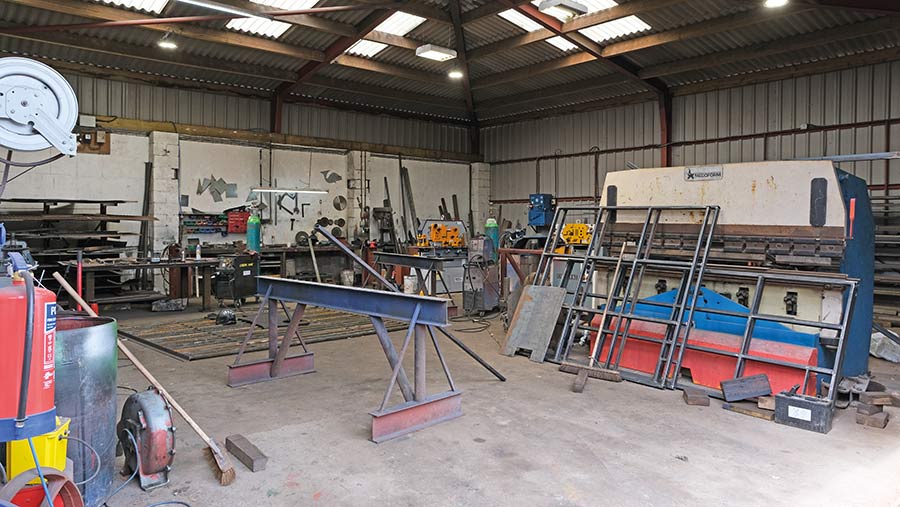
A big workshop allows Graham Hayllar to take care of machinery maintenance and repairs for local farmers and contractors © James Andrews
Most and least profitable contracting enterprises?
They’re all running on tight margins, but the jobs with the least wearing parts, such as spraying and fertiliser spreading, are probably the best. You can also cover the ground relatively quickly.
Interestingly, we saw a big increase in demand for fertiliser spreading when the prices went up as farmers were keen to have it applied accurately with a high-spec spreader, rather than with their more basic machines.
Cultivation work is at the other end of the scale. This area has particularly abrasive, sandy soils, so it’s hard to make any money on jobs where you pull a machine through the ground.
Ploughing is especially tough to justify as the metal is so expensive and it doesn’t last five minutes. Thankfully, we don’t do that much of it. Â
Biggest threats to your business?
Rising machinery prices are a problem, but one of the biggest concerns is the amount our customers get paid for their produce.
Almost all the work we do is funded by the proceeds of selling milk and meat, so if farmers get paid less and find it hard to turn a profit, so do we.
The phasing out of direct payments is another blow that will make it harder for them to make ends meet. Retailers need to be paying fairer prices to make sure farming in this country is sustainable.
Legislation also affects us, particularly in terms of muck and slurry spreading.
We’ve recently been struggling with some of the new store covers, which make slurry challenging to stir and empty, as well as trapping gases that can be dangerous to operators.
Fuel is another but, thankfully, we’re protected from this a bit as we usually get farmers to provide it.
Difficulties with staff recruitment?
We’re lucky to have a good bunch of staff, many of whom have been with us for years. However, when someone leaves, it can be tricky to find a replacement.
It’s not just us, though, everyone from shops and garages to construction firms struggle to find good staff in this area.
It’s partly because we’ve got an ageing population, but we’re also on the edge of the Lake District, which means house prices are high and youngsters struggle to afford living here.
What excites you about the season ahead?
We’ll be battling on doing more of the same, but it will be interesting to see how the new remote-controlled pumping trailer performs.
It would also be nice if we could have a grass season like the last one, with a run of dry weather so we can stay on top of the job.
Recent new machines?
Last year we swapped our old 850 and 950 foragers for a pair of 2019 950s that had been owned by a contractor in south-west Scotland.
For years we hired forage harvesters because the upfront cost of buying was so high. But now that we’re on our second pair of owned machines we are building up a bit of equity.
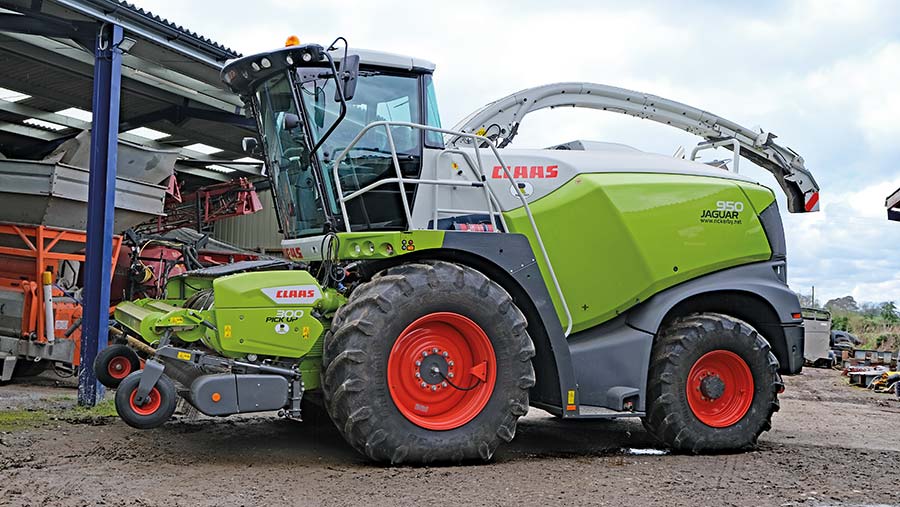
Two 2019-built Claas Jaguar 950s arrived last year on 1,200 drum hours © James Andrews
We still can’t quite stomach buying new, although we did consider it. The 950s seemed a far more sensible option, as we knew they’d been well looked after, and they cost about £100,000 less than a new model.
They had 1,200 drum hours on the clock and are fitted with premium liners, so they should last well enough.
Each came with a Claas grass pick-up and they share a 5.2m Direct Disc wholecrop header, which we used on the old machines.
This could do with being upgraded, but new ones seem ludicrously expensive considering they’re just a mower bed mounted in a frame.
We might have a go at making our own.
Last year we also added a pair of John Deere 6155Rs, upping our total number of tractors to seven.
These arrived when they were on about 1,000 hours and they were about £30,000-£40,000 cheaper than buying new.
I’m currently debating how long to keep these before I trade them in. We’ve always tended to run tractors to high hours, but it might be more sensible to upgrade these sooner while the value is still in them.
The slurry kit has also been updated, with all-new Oroflex pipe to replace the mix of ageing stuff we had before and a couple of Storth 1,000m random wrap reelers.
We also bought a 12m Agquip dribble bar, which was partly paid for with a Farming Equipment and Technology Fund grant.
Demand is increasing steadily for the dribble bar, but half of our customers are still requesting the splash plate.

Storth reeler and Oroflex pipe © James Andrews
Any significant repairs or breakdowns?
Thankfully, we haven’t had any significant breakdowns of our own for quite a while.
Part of that is because we keep on top of maintenance and try to fix problems before they get too serious and let us down in the field.
The tractors have also been modified by the Derv Doctor, which means they’ve had a lot of their troublesome components removed and they’re putting out considerably more power.
For example, both our 6830s are running fixed-vane turbos, rather than the complex variable-geometry originals, and they’re putting out about 200hp.
One has done 23,000 hours, the other is on about 15,000, and they’ve given very little trouble over the years.
We did have a bit of a drama with the younger one last season, when the lads were heading out of the yard with a convoy of silage trailers.
The hitch on the tractor in front wasn’t properly latched and the trailer popped off when going over a bump and crashed into the bonnet, smashing it and the radiator. The bill was covered by the insurance, but it ran to more than £5,000.
The R-series tractors have also gone well for us and we’ve probably had fewer niggly problems with these than we have with the 30-series.
The only notable gremlin recently was a faulty fibre-optic cable to the screen on one of the 6155Rs which Cornthwaites fixed for us under warranty.
We really rate the 6155Rs as they’re a handy size and go well, particularly when they’re tuned up to 200hp.
There have been a few more interesting jobs in the workshop this winter, such as rebuilding the transmission in a JCB Fastrac 2170, as the input shaft had sheared off. We did the synchros while we were in there too.
We also had to fix a park lock on someone else’s John Deere 6115R, which had failed because it had been engaged when the tractor was still moving.
It’s a simple enough fix, but it is right at the back of the gearbox, so it’s a cab-off job and everything else has to come out first.
Kit list
- Foragers Claas Jaguar 950 x2 with grass headers and 520 wholecrop header
- Tractors John Deere 6195R, 6155R x2, 6150R, 6830 x2 and 6430
- Umbilical slurry kit Three home-made pumping trailers, home-made 12,000gal nurse tank, Storth reelers x6, splash plates x2, 9m and 12m dribble bars, home-made tower stirrer, home-made lagoon stirrer
- Slurry tankers Abbey 2,500gal, Conor 2,250gal, Conor 2,500gal twin-axle, Redrock 2,500gal twin-axle
- Muck kit Bunning Lowlander 75 and 105C rear-discharge muckspreaders; Shelbourne Reynolds 1600 side-discharge
- Spreaders KRM Bogballe fert, KRM Bredal lime
- Handlers Manitou MT1233 S, Boss forklift and John Deere 653 loader on 6430
- Sprayer Case IH 3,600-litre trailed
- Grass kit Claas Disc front-and-rear mowers, Liner 2900 rake x2, Cherry Products buck rake x2, Moutton buck rake
- Silage trailers Bailey 12t x2, home-made 12t x2, Fraser 10t, Triffit 10t, Wootton 10t
- Cultivation kit Amazone five-furrow plough, 6m Simba levelling harrow, 3m home-made front press, 6m trailed press, 6.3m Flexicoil Cambridge rolls
- Drills Amazone 3m combi, 4m Vaderstad Rapid, 6m home-made grass seed drill
- Other Wakely crimper/crusher
Did you complete any overwinter projects?
This winter’s build was a third umbilical pumping trailer, this time fitted with a remote-control system so one person can go spreading solo if they need to.
The starting point was a base from an old generator, which has a large, flat fuel tank built into it.
We then mounted a V6 Mercedes engine from a forager on the top to spin the Cri-man pump, as well as a 250cfm CompAir compressor, both of which are tapped into the main fuel tank.
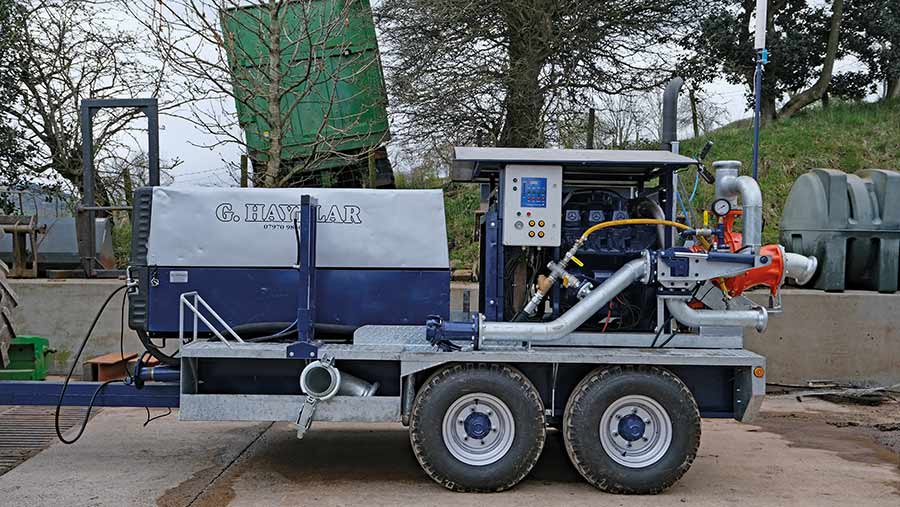
A third umbilical pumping trailer, complete with remote control, was built over the winter © James Andrews
Rather than run another small petrol engine for priming the pump, we opted for an air system that’s powered by the compressor.
We’ve had success with these on our other trailers and like the fact that they’re so simple.
There’s also a three-way electro-hydraulic system on board that operates the main divert valve, pipe clamp and hydraulic jack to level when operating.
We shopped around for the remote-control setup, eventually settling on a version from Hollin Applications in Durham.
It was a bit of a fiddle to wire this into the machine, but Chris Hunter in the workshop has got it up and running now. All in, the project cost about £20,000.
Current contractor frustrations?
Weather apps are one of my biggest frustrations. Before them, farmers used to look at the forecast on a Sunday and that would almost set the work for the week.
But now everyone is glued to their apps 24/7 and it can wreak havoc with our workload, particularly when they’re wrong – which they often are.
On one occasion a couple of years ago, the apps suddenly started saying the weather was going to break when there was quite a lot of grass down.
We had customers panicking on the phone, so we hired in some extra foragers and staff and worked through the night to get everything done.
I got into the house at about 7am to find that they’d changed their mind and it would be dry for the foreseeable future.
It cost us a fortune and our own foragers were then parked up in the blazing sun for a couple of days doing nothing.