Reaping benefits of auto guidance
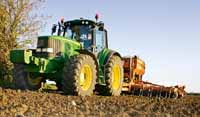
The savings you can make from guidance systems are pretty clear cut. Reduced overlaps in cultivations and combining can considerably cut down on time, fuel and wearing parts. There are also benefits from reduced operator fatigue and improved quality of work.
But there can be a substantial financial outlay involved. And your money will be wasted if you don’t get the right kit for what you want and don’t apply the technology correctly.
Tailored tackle
The basic principle of all guidance systems is that they steer you in a straight line. They also position you in the correct place on the headland to give you minimum overlap between passes or lands.
There’s a range of kit available. Manual systems are based on a light bar that tells you to steer left or right. Full automatic steering will adjust the course itself, and can even take into account corrections for implement drift on slopes.
The kit you install in the cab finds its position from a network of satellites and base stations. There are three levels of accuracy:
Low level: This uses a European network called EGNOS. A network of satellites and base stations corrects the satellite signal that you can receive for free to +/- 40cm. For a start-up cost of around ÂŁ1000 this is perfect for applications such as spreading fertiliser on grassland.
Medium level: This uses a subscription service to correct the signal. Accuracy and price vary depending on the specific service, but typically it would be +/- 10-30cm. At the lower end, this is suitable for spreading fertiliser and spraying, while drilling and combining would need an accuracy under 10cm.
High level: This uses a base station you purchase yourself (for around ÂŁ7500-10,000) to correct the signal. Accuracy is +/-2cm and there is no satellite drift – it will return you to exactly the same spot in the field every day and every year. This makes it ideal for bed-forming in potatoes, for planting vegetable crops, and for controlled traffic farming (see later).
The main benefit of auto-guidance is to cut down on overlaps. If you cultivate in lands, this can be considerable (see table). Multiply that up over the whole of a 400ha farm and that’s 40ha extra you may be needlessly cultivating for every single pass – a lot of wasted fuel and wearing parts.
When spraying, the overlap savings can be increased by installing auto-switching which shuts off valves on the headland. Systems cost ÂŁ1800-3000 and can deliver 2-5% additional savings on your chemical bill.
Headland turning and auto-switching can increase work rate. Overall this can be 13%, which is not just a time saving. Operators can focus on running the machine more effectively, rather than staying in a straight line. They can react better to changes in field conditions when cultivating, or crop flow over the header when combining, for example. Less to focus on means lower operator fatigue and potential for longer working days. Equally, highly skilled jobs, such as bed-forming, can be done to a high standard by staff with less experience.
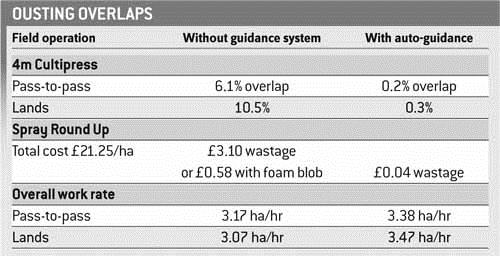
Set-up sense
The savings you can make from auto-guidance rely on accuracy, so correct set-up is vital. This starts with the tractor itself – wheelslip ruins automatic steering. Make sure you have the right ballast, tyres and tyre pressure and that the tractor is matched to the job you’re doing.
You also need to take account of machine offset. Many implements, especially drills, cover perhaps 10-20cm more width on one side than the other. Set up a line and carry out a couple of measured passes to gauge this with each implement.
Most of the higher spec kit will have a system to compensate for rough ground and slopes. Before you go into high accuracy work, calibrate it – this is very important.
Set up is also critical on auto-switching systems – you really need to take the time to do the fine-tuning to get the best out of it.
Tramline triumphs
Controlled traffic farming uses defined wheelings to reduce trafficked areas within a field. Research shows that in general 75-80% of a field is driven on in any one year, which has implications for compaction. So if you can stick to the same wheelings for every pass, soil structure improves, reducing the need for subsoiling and improving yields.
The easiest and most accurate way to ensure this is an RTK system. Importantly this will return you to exactly the same point in the field year after year. If you have a shift-track compensator for satellite drift, you will need to switch this off.
You need to plan this carefully – your cultivation system may be 4m, with a 6m drill on 24m tramlines. Then the combine will have a different axle width to the tractor.
Once you have a plan and have programmed it into your controller, write down the set-up line direction and start point for each field. If a technical error means you lose the data, you have wasted all your hard work setting up the system.
Then stick to it – getting the best out of controlled traffic farming takes discipline. So make sure all operators are sticking to the designated wheelings. You may need to change your wheelings periodically for crops such as potatoes, and they need maintenance – subsoil or level them up.
Three Golden Rules
1. Know the limitation of the system in terms of accuracy and performance
2. Set it up correctly – don’t discover an error after you have cultivated half the farm
3. Involve all of your team – you get the most out of it if everyone knows how to use the kit correctly
Case study
Tom Bradshaw, Essex
“It’s become second nature to use it for us, and I can’t comprehend farmers who don’t. You think you can drive accurately manually, but you can never do as good a job.”
With 1300ha (3200 acres) to establish, look after and harvest, it was the purchase of a new Challenger tractor that prompted the farm’s move to invest in the kit.
“We wanted to reduce overlapping and also cut down on those awkward triangles. We were aware you’d also get a saving in turning time and wearing parts.”
He estimates this adds up to almost ÂŁ20,000 over the entire acreage. “The biggest saving is the combine. We like to work in lands and now always leave an exact combine width. The driver can concentrate on settings, rather than worrying about where he’s going.”
An Omnistar HP subscription brings him a corrected signal accurate to +/- 5-10cm on equipment that would cost around ÂŁ8000 for the tractor and another ÂŁ6000 for the combine.
“There are a lot of small industries that have sprung up offering precision farming solutions. You need to make sure the company you go with can provide you with back up, because if you have problems, you need to be able to get hold of someone,” he notes.