Packing small bales eases the handling load
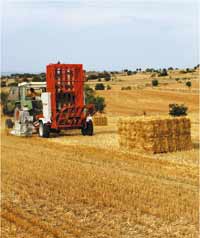
Designing machines that tie lots of small bales into one big bale-sized package isn’t easy, but a handful of makers have found clever ways of doing it. Peter Hill reviews the fruits of their labours
The McConnel Balepacker was first on the scene. It took bales directly from the back of the baler, assembled packs of 16 or 20 and tied them in a block using two strands of heavy-duty twine. Hey presto! A big bale package that broke down into man-size pieces to be lobbed into calf pens or carried into horse stables.
Some of these venerable devices are still in use today, providing an efficient means of loading small bales on to trailers for the journey back to the barn.
But they are outperformed in the majority of respects by machines that do a similar job using modern electro-hydraulics and computer control that do the job faster and more reliably.
The US-built Bale Band-It produces a 21-bale pack secured using two steel bands; the Canadian Bale Baron achieves much the same using four rows of heavy-duty twine; the Arcusin Multipack puts together 10-bale or 14-bale twine-secured packs and works separately from the baler.
Another key difference over the Balepacker is that these machines produce tightly-bound packages that are readily lifted by modern handling machinery and build into a solid load on a truck for long-distance haulage.
“It’s the best way to take labour out of the small bale business,” says Roland Woodcraft, the Beds-based straw and hay merchant who started importing the Bale Band-It seven years ago.
“We have about 20 machines out in the field, making packs of hay bales tight enough to pick up with a spike,” he adds. “Output is typically 400-450 bales an hour – but a new model is on the way that we’re told will handle closer to 600 bales an hour, while also being simpler with fewer moving parts.”
The operating principle will be the same, which on the current Bale Band-It sees each bale being tipped on end then lifted along a curved channel to be deposited on its side and lowered into the top of the assembly chamber.
The next bale goes on top, as does the third. Lowering them fully into the chamber triggers a hydraulic mechanism that pushes the embryonic pack into the compression chamber to make way for the next three. With seven rows of bales assembled this way, the pack is compressed and two 13mm x 0.5mm steel bands are tightly crimped around it. The completed pack is then pushed from the chamber on to a hydraulic ramp where it is gently lowered to the ground while baling continues uninterrupted.
The Bale Baron achieves the same result in terms of the number and configuration of bales in each pack, but it works from the bottom up rather than top down. Bales are channelled into a circular chute that rotates them 90 degrees before a stuffing arm pushes them one at a time into the bottom of the assembly chamber.
With three bales arranged on their sides on top of each other, the fledgling pack is pushed further into the chamber and the process repeated. With the seventh row is in place, two hydraulically-operated doors at the rear of the chamber close so the pack can be compressed, while four strings of heavy-duty twine are secured by Hesston knotters.
The pack is then pushed on to a roller chute and deposited to the ground to complete the computer-monitored non-stop process.
The machine’s importers, hay and straw merchants Nick and Jonathan Scrase, operated their own Bale Baron for the 2009 season and are confident they are on to a winner. “We packed about 35,000 hay and straw bales through the machine behind the Hesston 4590 baler without any glitches,” says Nick Scrase.
“The packing process is relatively simple with few sensors involved, and where a sensor is used, it’s in the form of an on-off microswitch.”
Working capacity at a claimed 600 bales an hour is attractive, as is the use of four strings of twine secured by a knotter design familiar to a lot of fitters throughout the country.
Knotted twine is also used on the Multipack B14 small bale packer from Spanish firm Arcusin.
However, the Multipack differs in assembling its smaller packs of 10 to 14 bales vertically rather than horizontally and working separately from the baler.
“You are introducing a second operation, but there are advantages in working separately,” says importer Stephen Gillman of Arcusin UK. “You don’t need a bigger tractor on the baler or a baler that has a good, strong towing point.”
The main operational advantages are, however, that a Multipack user can package other peoples’ bales – either at harvest in the field or out of season as a static operation in the yard. “In that sense, it’s a versatile and flexible machine,” says Mr Gillman. “You get the handling benefits of the bag bale-sized packages but without being tied to packing at the same time as baling.”
In operation, the Multipack picks up each bale, flicks it upright on to one end and then tips it sideways to lie strings-down across the assembly bed, where it is pushed into the vertical packing chamber. Once a pair of bales has been assembled this way, they are lifted by the floor and held in place by a clamping mechanism while the next two bales are arranged beneath.
This process continues until the last layer is lifted into place, at which point the pack is compressed and twine secured around it by a bank of knotters positioned in an easily accessible location at the front of the chamber. With the assembly process completed, the pack is lowered to the horizontal and slides to the ground.
“UK users tend to produce bales shorter than on the Continent so they tie them off using three strands of twine,” says Stephen Gillman. “But the Multipack will package bales up to 120cm long because there’s a fourth knotter available to secure the pack.”
The choice of pack sizes is a useful feature, he adds. “For straw and hay, a 14-bale pack is the most common, but inserting a restrictor reduces that to 10 for heavier haylage bales. I’ve also had interest in producing eight-bale packs, which would need a different size restrictor to ensure the same pack compression.”
When it comes to combining the man-handling convenience of small bales with the machine-handling efficiency of big bales there is a fourth option. This comes in the form of the MultiBale version of Krone’s BiGPack 1270 square baler, which can produce up to nine small bales, albeit with a fixed length of 120cm (47in), each secured by two lengths of twine and held together as a single package by six strings of twine.
For contractors with customers who want both conventional and big bales, it is a useful halfway house to the full-size packaging approach.