Ontario farmer gets robot fleet to complete arable fieldwork
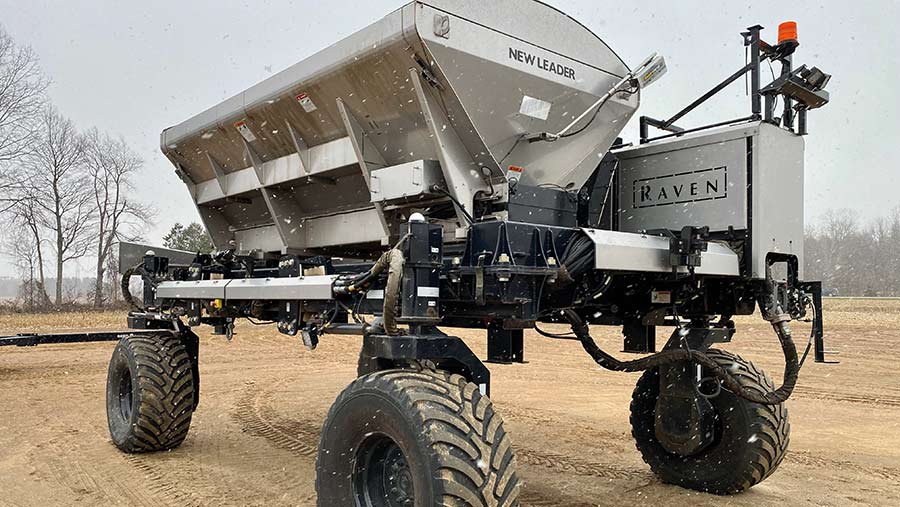
Chuck Baresich has been on a recruitment drive – but not in the conventional sense.
Over the past three years he has amassed a barnful of agricultural robots of all shapes and sizes, and hired a gang of technicians tasked with keeping them running.
Though initially employed purely on his own farm, they are now lent, leased and, in some cases, sold, to other agrarian technophiles within eight hours’ drive of his Haggerty Ag Robotics business, based near Bothwell, south-west Ontario.
See also: How to build your own tractor autosteer system for £700
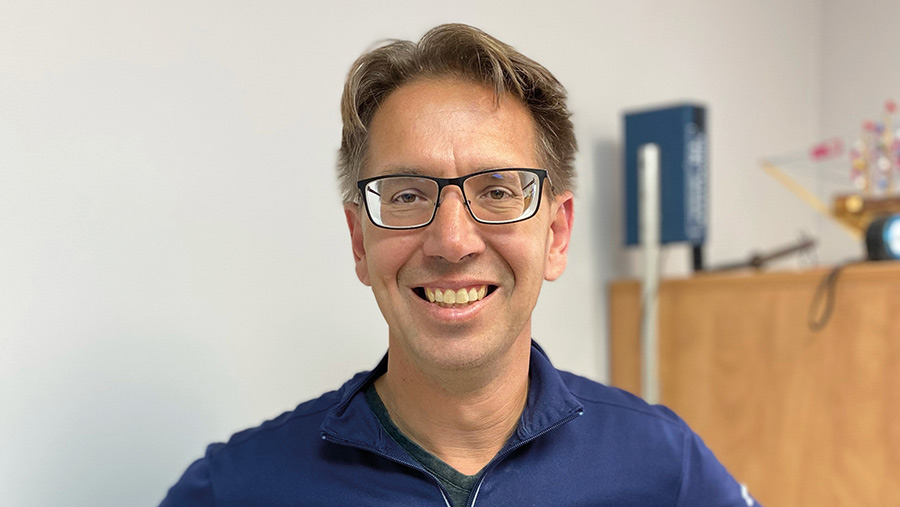
Chuck Baresich © MAG Mark Oliver
In most cases, interested parties are suffering from chronic labour shortages due to the diminishing appeal of seasonal, long-hour Canadian farm work combined with the shrinking and ageing of rural populations.
“Monotonous fieldwork is perfectly suited to a robot, which will work long hours without complaint or fatigue,” says Mr Baresich, who farms 1,400ha and manages a 1.2m bushel grain storage business in partnership with his brother, Justin.
“We’re always thinking about how we can operate more efficiently. The North American solution to improving productivity has traditionally been to make machinery bigger, faster and heavier, but we’ve now reached a plateau.
“Robots are already working in greenhouses and milking parlours, yet there has been little advancement in the arable sector. We’ve got cameras, autosteer and rate control on the sprayer, so I’ve often wondered why I need to be in the cab at all.”
According to Mr Baresich, the best way to manage the dwindling labour pool is to allow farmers more time to manage several tasks simultaneously and spend fewer vegetative hours piloting a tractor.
This has already been demonstrated by the likes of Iowan start-up Sabanto, with its fleet of small, autonomous Kubota tractors, and Australian firm Swarm Farm Robotics, which has a dedicated driverless platform.
Both have successfully matched the output of one monster outfit with several modestly sized machines, to the benefit of soil health and yield.
Gold rush
Dozens of autonomous tractors and tool carriers – concepts, prototypes and full production models – have appeared in the past decade.
Most of these come from start-up companies and research institutes, often basing their designs on widely available, and relatively cheap, components from the automotive sector.
Their aim is to develop a platform, or associated software, that will attract multimillion-dollar investments from the biggest names in the world of farm machinery.
Some are well designed and built, says Mr Baresich, while others are completely unsuitable for agriculture, making it a minefield for would-be buyers.
“The market for agricultural robots is like that of automobiles in 1910 Detroit. There might have been 200 manufacturers, but many of them were terrible and people ended up keeping the horse and cart.
“Over the following decade the few decent ones consolidated, and the rest went bankrupt.
“In the case of robots, you can quickly thin out the options by offering them a cheque to purchase one. These companies don’t have the resources to build multiple prototypes, so I sometimes discover that there isn’t actually anything to buy.”
One of the first mainstream models to go into production was the Raven Omnipower (née Seedmaster Dot) that, based on its sheer size, remains one of the most obvious like-for-like alternatives to a mainstream tractor – at least for broadacre agriculture.
It is now under the CNHi umbrella following its $2.1bn acquisition of guidance specialist Raven in 2021.
That puts it in direct competition with another, more conventional, CNHi offering, in the form of Case IH’s driverless but cabbed Magnum.
“Making the Magnum, or any conventional tractor, autonomous might sound inexpensive compared with developing a whole new platform such as the Omnipower, but it doesn’t necessarily solve the problem,” says Mr Baresich.
“Tractors with trailed implements are more difficult to control than self-propelled tool carriers, particularly when it comes to backing into corners, spotting implement blockages or detecting broken bearings.”
The same, he says, applies to so-called “crossover autonomy”, where third-party systems from the likes of Mojow, Sabanto or Tel Aviv-based Blue White Robotics are retrofitted to conventional tractors, allowing them to operate autonomously in the field.
However, they do have advantages, not least that the machine can still be driven conventionally between field and yard, and there is an abundance of tractors on which the kits can be fitted.
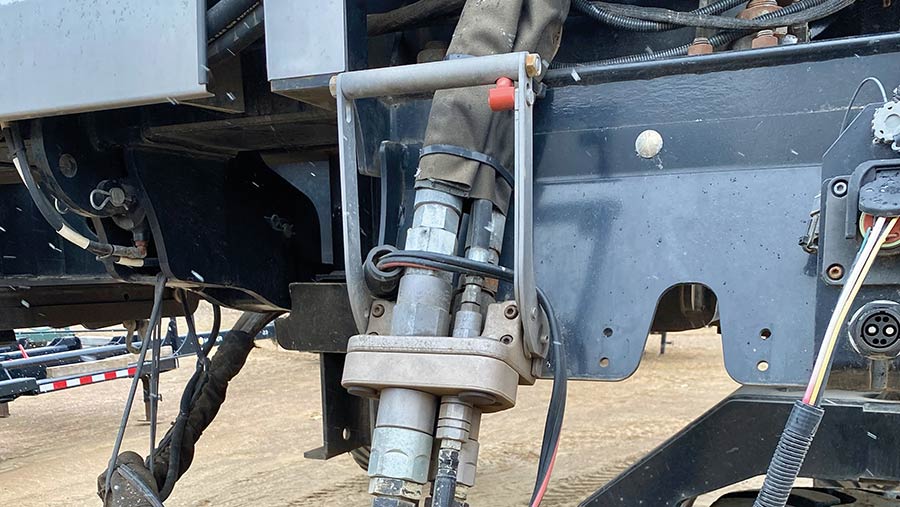
Hydraulic coupling © MAG/Oliver Mark
Developing implements
As well as selling, servicing and leasing autonomous tractors, Mr Baresich is busy designing specialist implements for them.
These include drills, sprayers and cultivators, which are being produced in collaboration with existing manufacturers.
“Drills are the hardest to develop because everyone wants something slightly different and there is no economy of scale when the market for them is so small and specialist.”
But he expects to have a prototype 12-row maize planter by the end of the year and an umbilical slurry spreading system is in the works, developed with Ontario-based Cadman Power Equipment.
Why an Omnipower?
Mr Baresich runs two of the 25 Omnipower models now operating in North America, the first having arrived three years ago.
Many elements of the platform are eminently conventional, such as the 175hp six-cylinder Cummins diesel engine and two-range hydrostatic transmission.
In Mr Baresich’s case, it carries a regular New Leader fertiliser spreader, albeit adapted with specialist mounting brackets.
Four-wheel steering provides telehandler-like manoeuvrability and, with a motor on each wheel, it can reach a top speed of 20kph. Maximum payload is roughly 12t, and implements are coupled via a standard hydraulic quick-connect.
Replacing the driver’s eyes are eight high-definition stereo cameras, combined with ultrasonic radars, that constantly observe the surroundings.
The ability of the software to spot obstacles is a work in progress to ensure the system can differentiate between maize stalks and people, pylons and trees.
“Safety perception systems aren’t ready yet,” says Mr Baresich. “And no one in the robotics space wants to be first on Twitter with a crashed robot.”
Transportation is the biggest logistical headache, with a purpose-built low-loader towed behind a telehandler or pickup to shift it between sites; loading/unloading takes about five minutes using a remote control.
“Moving it from field to field has to be a one-person job, otherwise it defeats the objective of autonomy. That same person can then start, monitor and refill the Omnipower as it works.”
For this reason, the platform is for now limited to spreading fertiliser, lime and compost, which also avoids the risk of inadvertently wrapping a sprayer boom around a telegraph pole or worrying about spotting a blocked nozzle from hundreds of metres away.
“It did 600ha in its first season [2020], though it wasn’t without its challenges. We had a big audience for its debut run but by the time we’d overcome connectivity issues, most of the visitors had gone home.”
It culminated in the completion of just 20ha of the 100ha first-day goal – a total that wasn’t achieved until well into week three.
“That sums up what it’s like being at the bleeding edge of technology. What you don’t necessarily think about is how much information and knowledge a driver has – and a robot doesn’t – when it comes to doing a job.
“The mission planning software needs to know everything – where to start and stop, which direction to drive, spreading speed, turning speed, the size of the headland, how close to get to an obstacle, what to do when the hopper is empty, and so on.
“Then there are all the subjective decisions on the part of the manager; can I trust it to stay 10ft away from an obstacle? Will it stop when I ask it to?”
This makes the investment in an autonomous tractor all the more daunting, even before the price has been factored in.
Raven charges roughly C$600,000 (£365,000) for the Omnipower with an implement which, as it stands, is limited to relatively few tasks given the shortage of attachments available.
“We’re hoping Raven develops a scaled-down version that is physically smaller and better suited to busy roads and smaller fields than those on the prairies of Saskatchewan where it was first developed.
“That will hopefully encourage more widescale adoption and, in turn, make it more attractive for manufacturers to develop specific implements for the machine – both in North America and Europe.”
Raven Omnipower
Engine Cummins six-cylinder diesel
Power 175hp
Transmission Two-range hydrostatic
Top speed 20kph
Weight 8t empty
Price C$600,000 (£365,000)
Alternative robots
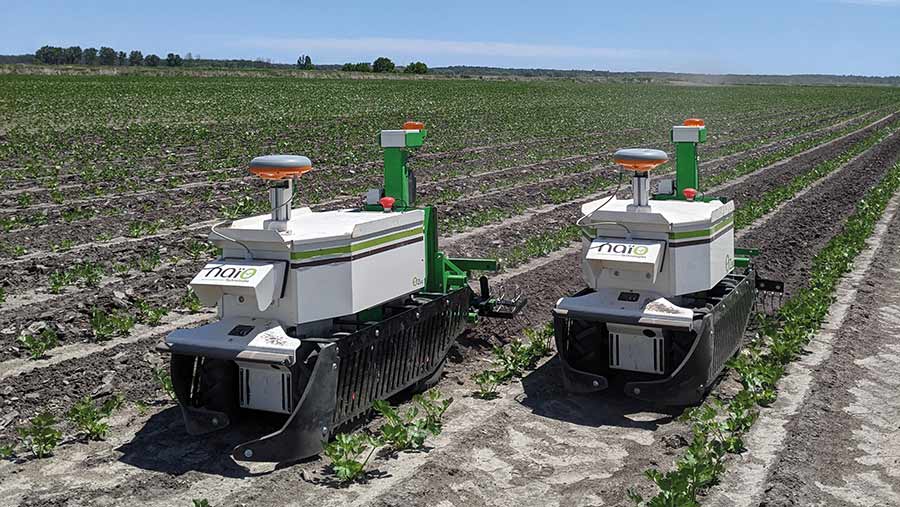
Naio Oz PXL farming robots © Chuck Baresich
Haggerty Ag Robotics now owns a ruck of smaller autonomous machines which are trialled on Mr Baresich’s own farm and others within 400 miles of his base.
They are also offered as part of a contract planting and weeding service.
“We realised the potential business was bigger than just applying a couple of systems on our farm so, last year, we hired five staff to support other agricultural and horticultural growers that want to use them.”
Machines on the Haggerty books include the Montreal-made weed-pulling Nexus, Naio’s Oz, Dino and Orio, and the tracked Korechi RoamIO.
There are also a handful of models that might be more familiar to European growers, such as the solar-powered Farmdroid FD20 now distributed in the UK by Opico, the diesel Agrointelli Robotti – one of which went to Home Farm Nacton near Ipswich – and a DJI drone with 40-litre/50kg capacity for spraying and spreading seed.
Research focuses on soil health and yield benefits, input savings and running costs.
“We’ve found that one robot is unlikely to do everything, and their suitability varies significantly depending on the farm type.
“A good example of this is the Farmdroid – it’s brilliant in that it can both plant and hoe, so is involved in more parts of the growing season, but it can struggle to handle the big weeds and heavy trash conditions that we often have in Ontario,” says Mr Baresich.
“There’s also the means of propulsion to consider. Battery power is appealing, but there are huge logistical issues to contend with in Canada – not least that the Naio Dino needs recharging after 4ha.
“By comparison, existing farm machinery is so efficient – it’s been developed to be that way for 50 years – so any widescale move to robotics won’t happen overnight.”
Either way, Mr Baresich expects exponential growth in horticultural robotics in the next five years, and broadacre agriculture to follow in the next decade or so.