NI farm transforms slurry and food waste into bio-LNG fuel
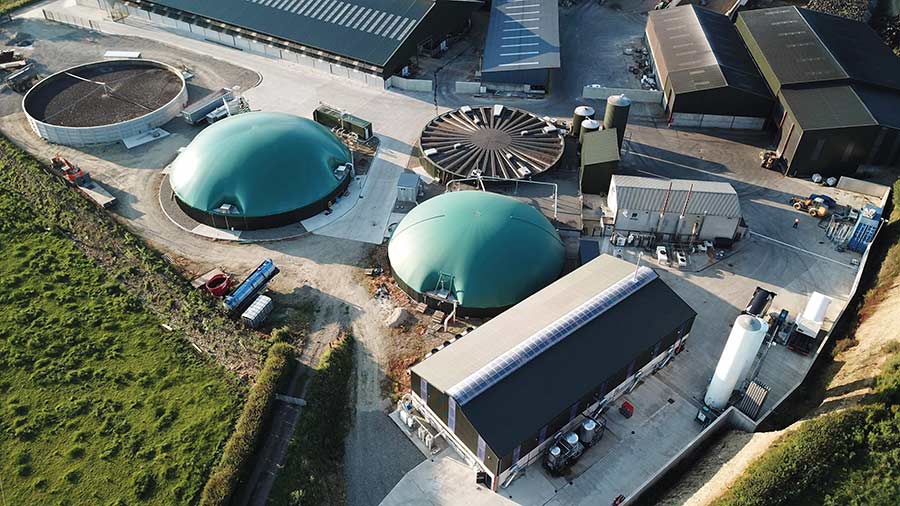
A multi-million pound diversification project has allowed an enterprising dairy farm to convert slurry and food waste into biofuel, as it looks to tap into the growing market for renewable energy.
Its high-tech cryogenic system purifies and liquifies raw biogas by chilling it in a series of heat exchangers to produce liquified natural gas (bio-LNG), which can be used to replace national grid-sourced electricity on dairy farms and diesel in heavy goods vehicles.
See also: Cornish firm creates kit to turn slurry emissions into fuel
The aim of the ambitious 20-year project at Greenville Energy, near Newtownstewart, County Tyrone, is to establish bilateral trade deals with local farms, dairies, food processors and supermarkets.
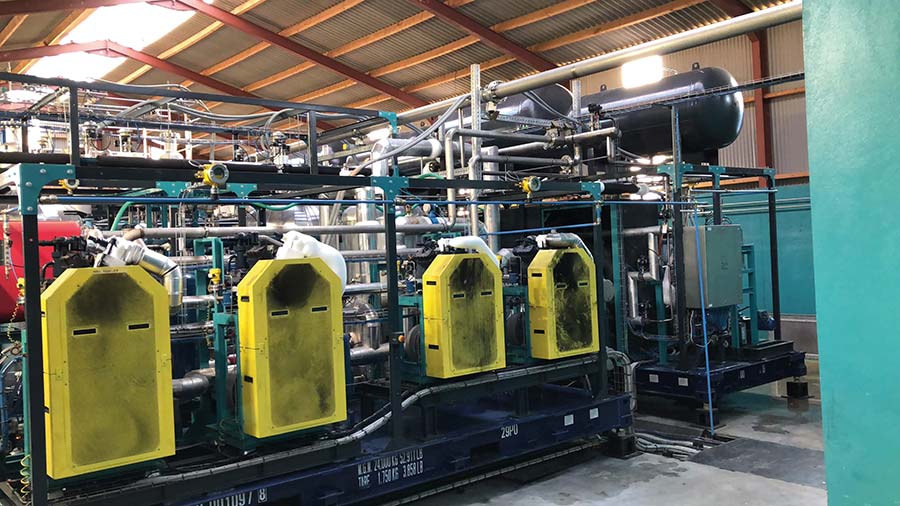
Liquifier compressors © Greenville Energy
These see their waste material processed through one of Greenville’s anaerobic digesters, with the harvested biogas then purified, cooled and pressurised to transform it into bio-LNG – a zero-emission, carbon-neutral fuel that is up to 30% cheaper than diesel.
This can then be returned to the feedstock provider and, in the case of one dairy customer, used to run a gas-powered engine, providing heat and power while slashing both its energy bills and carbon footprint.
Renewable energy
The bio-LNG plant is the latest addition to Greenville’s sprawling renewables facility, which is run alongside a 700-strong milking herd and 1,300 followers.
Its initial AD plant – the first in Northern Ireland to be run purely on waste – was commissioned in 2012, with director Jason Mitchell keen to extract more value from the slurry and other waste materials on the family’s dairy farm.
There are now three digesters on site, two 2,200cu m units and one of just over 4,000cu m, that eat 35,000t annually.
Their diet primarily consists of cattle slurry and waste silage from the farm, combined with dairy sludge from processors, and fruit and vegetables from retailers.
The resulting biogas was originally used to produce 500kW of electricity for the grid, providing a valuable income stream while protecting the farm business from fluctuating energy prices.
“We’re self-sufficient in energy, and the 32,000t of organic digestate, which is high in nutrients and other trace elements, means we no longer need to buy any synthetic fertiliser,” says Jason Mitchell.
“Plus the land can be used to feed the cows rather than the digester, so we’re as close as possible to a circular economy.”
But, in 2017, he and general manager Dr Willie Moore set about exploring alternative uses for the excess biogas they were producing.
This led them to a potentially more lucrative market – purified bio-LNG.
A £3m investment in a specialist gas liquifying facility followed.
In doing so, Greenville became the world’s first small-scale LNG production facility and the first commercial project for its French creator, Cryo Pur.
The size of the system – LNG output is rated at 3.2t/day – was tailored to Greenville’s typical feedstock volume.
To give a sense of scale, a “small” facility on the world market churns out 150t/day.
Installation of the prefabricated “plug-and-play” apparatus, which was delivered and fitted on large skids, took just six months.
How does it work?
Cryo Pur’s setup converts raw biogas into liquified natural gas and liquified carbon dioxide with zero waste – providing two valuable commodities.
It essentially involves running the gas through a series of heat-exchanging vats, frosting and defrosting it at progressively more extreme temperatures to extract impurities.
First, it is drawn through carbon filters to remove any hydrogen sulphide, before the temperature is lowered to -40C.
This separates the small amount of water that would otherwise freeze and plug the pipes.
Further refrigeration takes it down to -90C, at which point the carbon dioxide is harvested. What remains is compressed natural gas (CNG) – pure methane.
This is a potentially useful fuel – New Holland sells a T6 Methane Power tractor with an engine designed to run on CNG – but Greenville takes it one stage further.
To transform it into LNG, which has a density 600 times greater than methane in gaseous form and six times that of CNG, the temperature is plunged to -120C and the pressure cranked up to 14bar. These conditions force the gas to liquify.
This part is energy intense, so relies on the relatively cheap electricity still supplied by a portion of the AD plant.
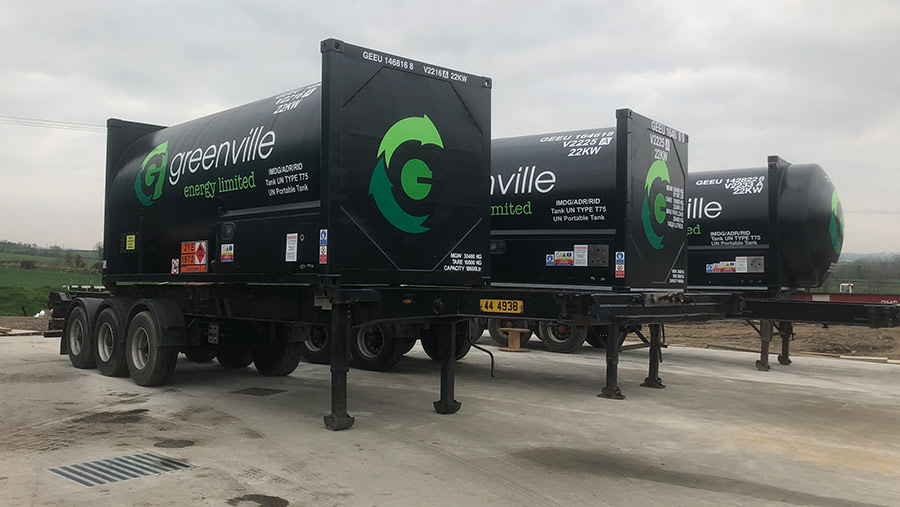
Tankers © Greenville Energy
The finished product can be stored for up to a month. It is transported in HGV trailer tanks that can each hold 19t, allowing Greenville to run a “drop and lift” exchange system to deliver the fuel to its customers.
The liquified carbon dioxide siphoned off early in the process, totalling 900t annually, can also be sold for ice blasting and chilling or freezing applications.
Powering dairies
Though LNG remains niche, Greenville has already found plenty of takers for its fuel.
In most cases, these are two-way deals that see waste organic material from big dairy processors transported to the Greenville plant to feed the digester, and a liquified version of the gas returned to the factory to provide a renewable source of energy.
Food processors, distilleries and supermarkets can also send their waste to the plant as a feedstock and get recompensed in zero-carbon fuel to run HGVs.
This symbiotic relationship is made greener because delivery and collection can now be completed using a dual-fuel lorry powered by both diesel and bio-LNG.
Lakeland Dairies, a co-operative based in County Cavan, Ireland, was one of the first to pen a deal with Greenville.
At its peak it uses 4MW of power, and 15-20% of this can now be supplied via an LNG-powered generator – a Schmitt Enertec gas fuelled engine that runs 24 hours a day.
This is significantly cheaper than grid electricity for Lakeland Dairies, and less susceptible to volatile natural gas prices.
Long-term goal targets HGVs
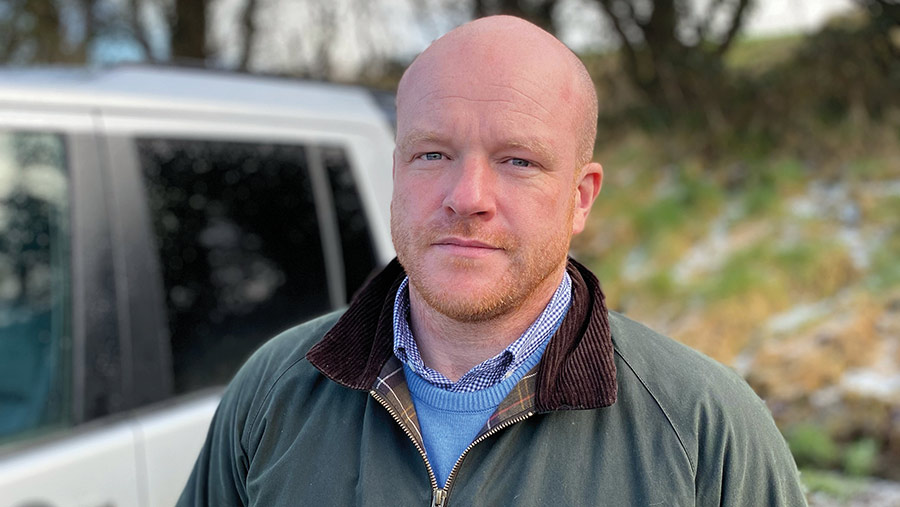
Dr Willie Moore © Greenville Energy
For Greenville, the major appeal of cracking LNG production was the promise of vehicle fuel, allowing it to tap into the vast HGV and construction machinery markets where a cost-effective alternative to white diesel is highly desirable.
As well as the appeal of lower fuel duty, hauliers can also get a “renewable transport fuel certificate” and, according to Dr Moore, the only practical means of achieving that is to move to bio-LNG.
“It’s currently the only viable alternative to diesel. Everyone is talking about electrification, but it’s too impractical – the grid can’t handle it – and hydrogen is years away from becoming mainstream, and far too expensive.
“That leaves biomethane. CNG is often considered simpler and quicker to produce than LNG, but it’s not a long-term solution – hauliers say the engines running on it produce less torque, they’re too slow to refuel and they have a limited range of about 300 miles.”
The gas also needs to be transported at 250-300bar pressure in a thick vessel, meaning an empty lorry will weigh 28-30t and leave very little carrying capacity.
“In short, bio-LNG is the only show in town. It can provide HGVs with a range of about 1,000 miles, which is comparable to diesel and keeps transport logistics largely the same, it’s simple to handle and 19t can be transported on one lorry.”
The major downside of bio-LNG? Getting a sustainable supply of organic material to supply the whole HGV market…
Expansion opportunities?
Although Greenville’s setup is based on a conventional AD plant, of which there are around 700 on UK farms, the added LNG facility was both costly and complex to establish.
But it is a growing market, with several companies now developing small-scale production systems comparable to that of Cryo Pur.
And, better still, the HGV market will likely have an insatiable appetite for the end product.
There are myriad factors that will influence the viability of similar projects, including how much the fuel will be worth – which will be partly determined by government incentives – and the availability of high-yielding feedstock.
Finding a home for the digestate is also a perennial challenge, and one that could be made all the harder to overcome should application windows be tightened.
“The biggest issue is ammonia emissions from spreading the digestate so, to minimise that and optimise the benefits, the digestate needs to be run through a separation system.”
“All the nutrients coming out of the digester already existed – we’re not making any more – so it’s about making the best of them.
“In doing that, hopefully we’ll be able to double our LNG output in the next few years.”