JCB’s hydrogen-fuelled combustion engine examined
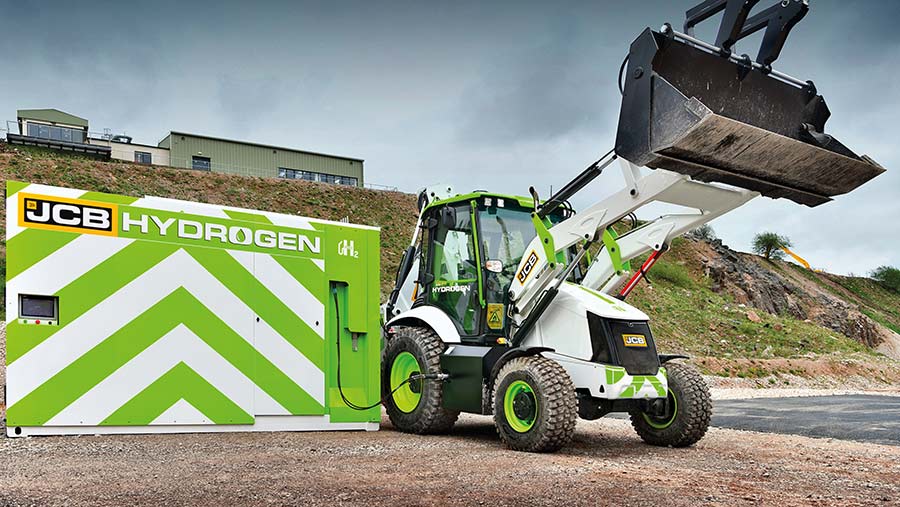
JCB is one of the first agricultural engine makers to successfully modify its conventional powerplants to run on compressed hydrogen, eliminating carbon emissions without any impact on performance.
Its gas-fired, four-cylinder, 4.8-litre motor develops the same power and torque as a Dieselmax 448 equivalent, the hardware is expected to cost no more and, with a bit of jiggery-pokery, it can be retrofitted to an existing machine.
Though still in the development stage, JCB expects to have the engine ready for pre-production by the end of 2022 – just two-and-a-half years after a 100-strong team of engineers set to work on the project.
See also: Cornish firm creates kit to turn slurry emissions into fuel
Exciting stuff, indeed, but the process of weaning farm machinery off diesel is unlikely to be a straightforward one – particularly as the market’s dominant forces are pulling in different directions.
John Deere is focusing on electric powertrains, New Holland has hung its hat on biomethane combustion and a handful of smaller players are experimenting with hydrogen fuel cells – leaving JCB as a lone ranger.
“We’re committed to combustion engines because they deliver high power and torque for agricultural applications,” says JCB chairman Lord Anthony Bamford.
“We also know a lot about them – the pistons, cylinders and crankshafts – and so do our dealers and customers, who have been maintaining and fixing them for years.”
“But, most importantly, these new engines are not inflationary. We can use existing components and production facilities, so there’s no reason why hydrogen-powered engines will cost any more than what we have now.”
Cutting carbon
Since starting production of its first Dieselmax engine in 2004, JCB’s Power Systems arm has been in a constant battle to suppress nitrous oxides and particulate tailpipe emissions.
It has been an expensive process, with the climb from Stage 4 to Stage 5 limits alone estimated to have cost the company £100m.
But with the government’s foundations for the road to “net zero” by 2050 now firmly laid, attention has turned to carbon.
This has led to a surge of investment from oil and gas multinationals in hydrogen energy, which doesn’t produce carbon emissions when burned.
How does the engine work?
JCB has managed to keep much of its standard combustion engine intact, with the bottom half, including the sump and four 1.2-litre capacity cylinders, identical to the existing Dieselmax.
It also has the same cooling pack and service points, and still runs a conventional variable-geometry turbocharger.
However, the old cylinder head and 2000-bar common rail injection system have been replaced by a completely different arrangement geared up to inject gas, rather than liquid.
It uses spark plugs to ignite the fuel, which is fed from five 1kg aluminium and carbon fibre storage vessels on JCB’s prototype 3CX backhoe, to four injectors on a pressurised rail.
This element is still a work in progress, as laser-like accuracy is required to get a consistent mix of light hydrogen and heavy air – and thus a consistent power output – in the 72 milliseconds between injection and combustion.
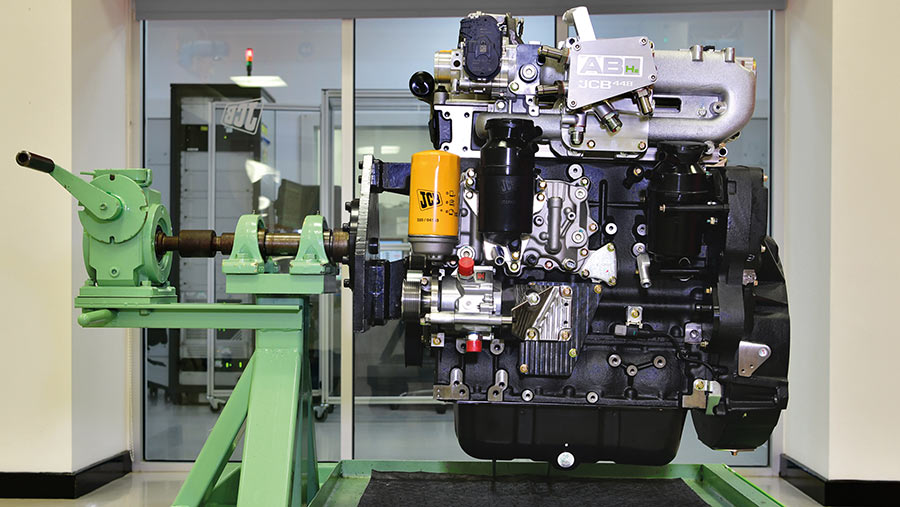
© JCB
Timing of the spark is also essential – too early and the engine will knock, which isn’t conducive to a long life; too late and it won’t burn efficiently and completely.
Unlike the efforts of BMW and Ford in the noughties with their Hydrogen 7-series and “Tiny” research vehicle, respectively, JCB reckons it has found a way of running an exceptionally lean mix of 1% hydrogen and 99% air.
This fuel-light blend solves the major challenge with hydrogen combustion – keeping the temperature down to minimise the amount of nitrogen oxide emissions that need to be cleaned up with a selective catalytic reduction (SCR) module.
And with no carbon going into the engine, no carbon dioxide comes out.
The main by-product is water, so making sure all the vapour leaves through the exhaust is essential to avoid it loitering around the combustion system.
To minimise the risk of any problems, owners will probably have to use specialist engine oil that carries more anti-corrosion agents to avoid emulsification and, conversely, fewer carbon dispersants because hydrogen is far cleaner burning.
What’s performance like?
JCB currently has a team of white-coated technicians monitoring emissions, power, torque and fuel consumption, as well as the influence of things such as cold weather and altitude on those parameters.
So far, power and torque curves are near-identical to the diesel-powered version.
We saw the first prototype running at 1,500rpm and there was little to distinguish it from an orthodox oil-burner, aside from a softer, turbo-dominated engine note – akin to that of a petrol.
What’s the catch?
With the technology now at a relatively advanced stage, questions will fall on exactly how potential customers get their mitts on the fuel.
Production is currently limited – hydrogen accounts for just 5% of the world’s energy supply and half of that is considered “grey”, meaning it is produced from natural gas in a process that causes vast carbon emissions.
But the government is aiming to phase this out in favour of “green” hydrogen, which is produced by running excess electricity produced by offshore wind or solar farms through water to split the hydrogen and oxygen atoms.
At present, this only accounts for 4% of supply but there’s plenty of capacity to increase it – particularly as wind farms are paid millions of pounds a day to switch off their turbines when the energy being produced outstrips demand.
And on 17 August, the government announced its hydrogen strategy, which suggests that it could account for 20-35% of the UK’s energy consumption by 2050.
However, it remains far more efficient to exploit the electricity as a power source where possible, rather than using it to produce hydrogen.
“Hydrogen combustion is only 20-25% efficient from well to wheel [from the point of harvesting the energy to using it as a means of propulsion] versus with 25-30% for hydrogen fuel cells and 80-85% for electricity,” says Simon Buckley, knowledge transfer manager for zero emissions mobility at KTN.
Comparatively, the figure for diesel is roughly 20%.
“In theory, that means you could run four electric HGVs using the same amount of energy as one hydrogen combustion engine.”
The added processes involved in producing hydrogen also make it expensive.
It’s currently £11/kg depending on type and purity, which is roughly double the price of white diesel (and significantly more than rebated red), and the lack of infrastructure makes it difficult and costly to transport and store.
However, JCB anticipates it working in a similar way to the diesel supply chain, with mobile gas trailers delivering to rural locations.
The pressurised vessels the gas is delivered and stored in are likely to be owned by a fuel company, but farm businesses would need to acquire a “refuelling station” with a built-in cooling system and pump to store the gas at roughly 450bar.
The idea is to decant from this into a machine’s fuel cylinders, where it is held at 350bar, in a process that takes less than 10 minutes (based on a 0.5kg/min fill time).
An alternative for some landowners might be to have an on-site solar farm that can provide the electricity required to produce hydrogen.
When will the engine be available to buy?
JCB is aiming to start pre-production by the end of next year, with the engines drip-fed into its agricultural and construction ranges.
But how many it builds is entirely dependent on hydrogen supply and the associated infrastructure.
“The technology is fast becoming available, but a lot of the progress relies on solutions being put in place to allow farmers to do their jobs in an economical manner,” says Mr Buckley.
“For that to happen, the price of hydrogen needs to come down a lot – to cost parity with red diesel. But that also applies to electricity, which is reliant on batteries getting cheaper and energy density increasing.”
Other alternative low-emissions power systems
Batteries may be dominating the transition to zero tailpipe emissions in the automotive sector, but the jury remains undecided on the case for high-horsepower farm machinery and other large, specialist vehicles.
“We need more evidence of the pros and cons of each,” says Mr Buckley. “There are plenty of factors to consider, including duty cycles, cost of ownership and developments in automation and robotics.”
“Economically, if you can use batteries then they are the best solution. Though the upfront cost is higher, electricity is the cheapest and most efficient source of power – particularly when it is produced locally by wind turbines, solar panels or an anaerobic digester plant.”
However, batteries have a low energy density, which currently limits them to stop/start jobs that allow for a period of recharging – such as feeding or bedding on a dairy farm.
Tractors, combines and foragers requiring long stints of high power suit combustion engines, though Mr Buckley points out that the most practical option now may not be the same in 30 years.
“Increased automation and changes to farming practices may mean moving to smaller tractors that could be battery powered, or to hybrid combinations of battery-hydrogen or battery-biomethane to balance cost with energy density.”
Batteries
JCB already has seven battery-powered machines, including a 1.9t mini excavator and 525-60E telehandler.
There are also a handful of sub-50hp tractors on the market but, of the household tractor names, John Deere and Fendt lead the way with their 174hp Sesam and 67hp e100 Vario, respectively.
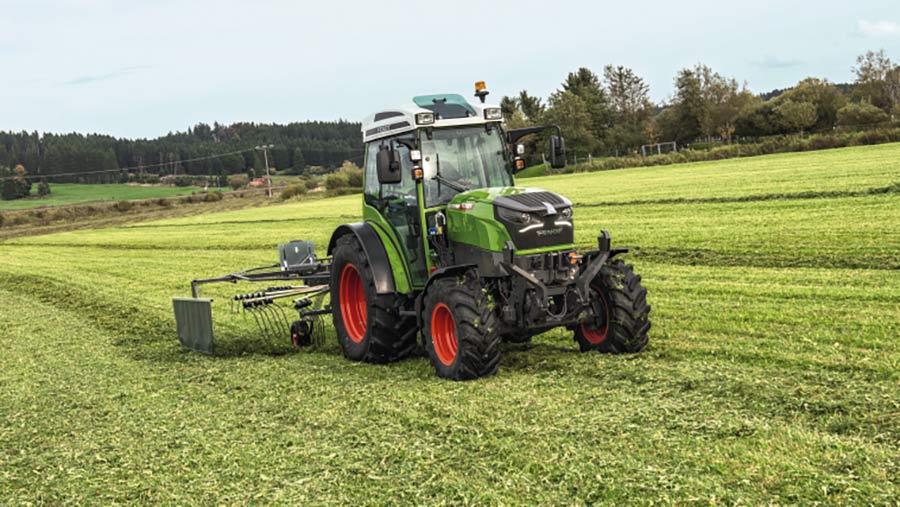
Fendt e100 Vario © Fendt
However, both have limited energy capacities and, for any increase in power outputs, the quantity and weight of batteries required renders them impractical and too expensive.
Quick charging also relies on a good electricity supply, which is never a sure thing in rural areas.
Progression could be supercharged by Toyota’s development of solid-state batteries that have triple the energy density and can be filled in a fraction of the time.
Advantages
- Silent operation
- Efficient powertrain
- Relatively cheap fuel
Disadvantages
- Long recharge time
- Specialist required for servicing/repairs
- Low power density
Electric cable
John Deere has also developed a concept tractor that can be connected to the grid.
Rather than banks of batteries under the bonnet, the GridCON is permanently fed by a cable that is reeled in and out on a drum and robot arm as it travels.
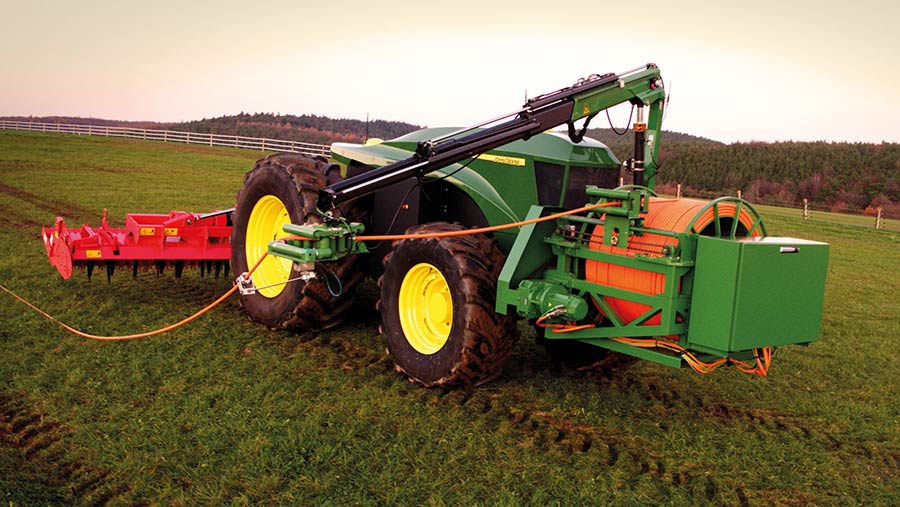
John Deere GridCON © John Deere
As a result, it’s good for 400hp and weighs just 8.5t – the same as a 6195R at half the power.
Advantages
- Loads of power
- Comparatively lightweight
- Silent operation
Disadvantages
- Cable connection impractical
- Risk of handling huge voltage
Biomethane
Biomethane is a strong candidate to replace diesel and shares plenty of similarities with hydrogen – not least, the ability to use it in a modified internal combustion engine.
New Holland is leading the way with its compressed natural gas (CNG) powered T6 tractor and is rumoured to be working on a liquified natural gas (LNG) version that will offer a significantly extended range.
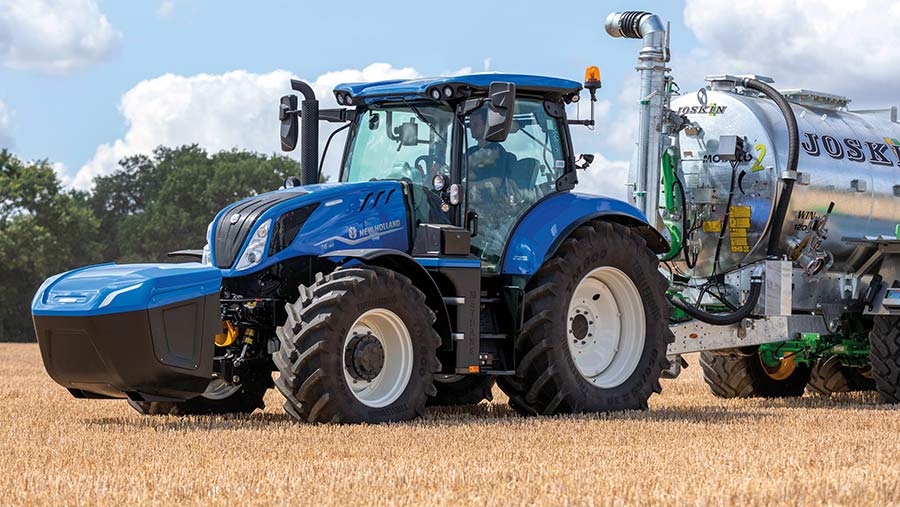
New Holland methane tractor © New Holland
One of the major attractions is that it can be run on methane sourced from an anaerobic digester plant, making sourcing and transporting it far simpler than hydrogen.
Cornish firm Bennamann also recently developed a means of harvesting methane from slurry lagoons to be converted to fuel.
Like hydrogen, biomethane-powered vehicles aren’t zero emissions – they still produce nitrogen oxides and particulate matter, though this can be dealt with using existing emissions control systems.
Net carbon emissions are low because the fuel is produced from feedstock that absorbs carbon dioxide during its growth.
Advantages
- Can be burned in a combustion engine
- Relatively easy to produce on farm
- Closest to production
Disadvantages
- Doesn’t eliminate nitrogen oxides and particulate matter emissions
- Limited range on CNG
- Needs to be stored carefully to avoid leaks
Hydrogen fuel cell
Hydrogen fuel cells are more efficient than hydrogen combustion engines, which means less fuel is required to go the same distance.
The process sees hydrogen mixed with oxygen in a fuel cell to produce energy and water, with the electricity produced used to top up batteries that power an electric motor.
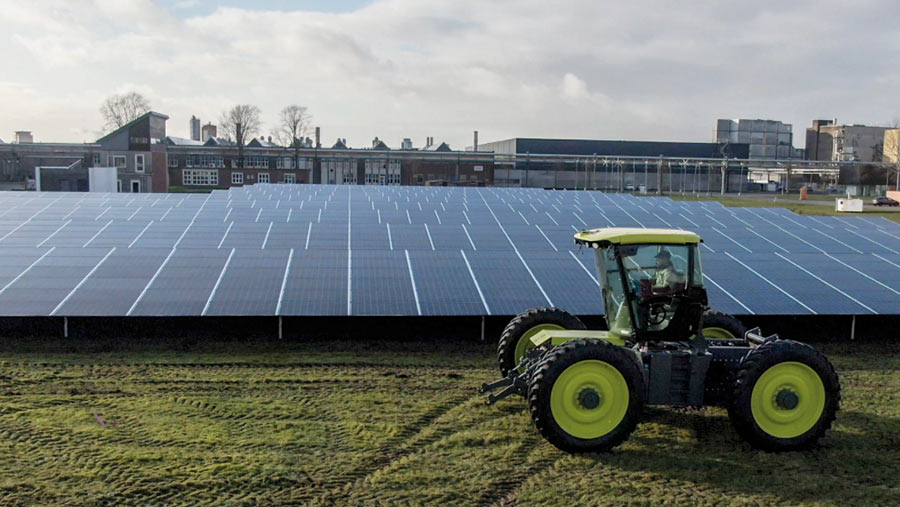
© H2trac
Dutch firm H2trac has developed a hydrogen fuel cell tractor – the EOX-175 – which is roughly 160hp and has a drivetrain like that of an electric car.
Likewise, JCB has also built a prototype 20t excavator using hydrogen fuel cell technology but expects it to cost twice as much as a diesel version (about £300,000).
Advantages
- More efficient than hydrogen combustion
- Good power density
Disadvantages
- Expensive
- Fuel supply challenges
- High-tech
Hydrotreated vegetable oil
Hydrotreated vegetable oil (HVO) and biodiesel are two short-term fixes that can be used in conventional internal combustion engines and help to reduce carbon emissions.
Some agricultural and construction machines are now running on HVO – a diesel substitute made from vegetable oils or waste oils and treated with hydrogen.
Due to the carbon dioxide absorbed by the plant material, the net carbon dioxide footprint is lower than fossil fuels, but tailpipe emissions remain the same.
Advantages
- Reduced carbon footprint
- Same performance as diesel
Disadvantage
- Short-term fix as carbon tailpipe emissions are not eliminated