JCB handlers get a new engine
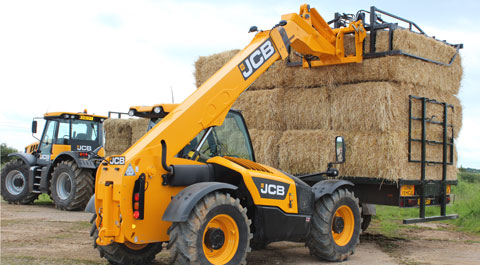
JCB has built a new emissions-friendly engine that will power its pivot steer loaders and telescopic handlers from mid-September.
But rather than just bung the new block in its existing machines, the maker has taken the opportunity to make a few improvements: Loadall models get bad-boy styling, joystick-mounted gear change and transmission dump integrated into the brake pedal. They’ve also had a few cab tweaks, been fitted with a quieter fan and gained high back-off brakes that pull the pads off the disks.
Pivot-steer TM machines, meanwhile, get higher lift capacity, better hydraulic flow and an improved lock-up torque converter that means the transmission is less power-hungry. They will be fitted with the joystick-mounted gear change, too.
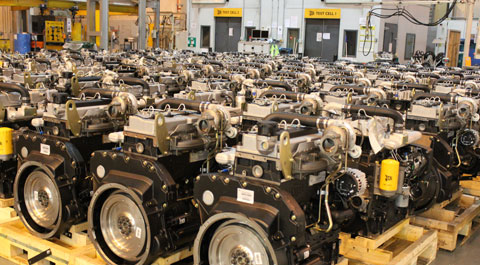
By employing up some rather-clever electronic witchcraft, JCB has got its new Ecomax engine to meet Stage 3b emissions regulations without having to treat the exhaust gasses.
That means no diesel particulate filters and no AdBlue. It does have an EGR system though, which cools some of the exhaust gasses and pumps them back into the engine.
The maker claims the new four-cylinder block develops 15% more torque than the old one, 10% more power and uses 5% less fuel. Service bills are said to be similar to the old one with service intervals sticking at 500 hours and it runs on a standard grade oil.
If the machine is to be exported to a country that runs higher-sulphur diesel, a JCB dealer can recalibrate the engine, effectively putting it back to Stage 3.
The engine is assembled by JCB Power Systems at its factory in Foston, Derbyshire.
JCB has managed to cut down the amount of diesel particulate coming out of the engine by getting a clean burn in the cylinder.
This is thanks partly to a high-pressure common-rail injection system and re-designed piston bowl that helps improve combustion.
The variable-geometry turbo also plays an important role, as does the EGR cooler, which takes heat out of the exhaust gasses before sending them back into the engine.
A Delphi electronic control unit mounted on the side of the block accurately controls all of these systems to ensure the right amount of air and fuel is sent to the cylinders.
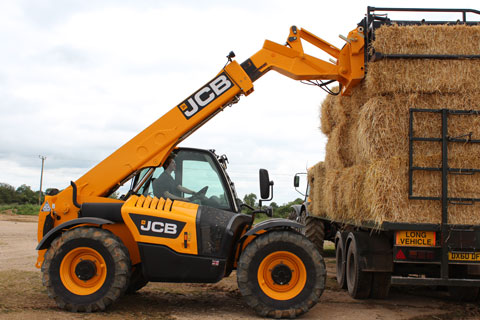
As well as the new engine, mid-range Loadall models (125- to 145hp) have had the gearshift moved to the top of the main joystick – before it was a twist grip on the steering column – and some models have the forward/reverse shift mounted there, too.
Moving the transmission dump to the brake pedal is a handy addition and means full power goes to the hydraulic system without driving against the brakes. JCB says this reduces wear and cuts fuel consumption during bulk handling jobs such as loading grain lorries. It can be switched on and off via a dash-mounted switch.
There have been a few tweaks in the looks department and the main change has been to the engine cover. This is slightly more angular and has a series of vents in the top of the cover that blow air upwards, rather than onto the ground like the current model does. This means it should kick up less of a dust cloud and the air filter should last a bit longer.
In the cab, there is a new dash layout and the seat has an operator presence switch, which means it won’t go anywhere unless a bottom is parked on it. The upper door gets a beefed-up latch mechanism with settings to hold the it ajar as well as fully open.
Replacing the TM310, the TM320 pivot-steer loaders benefit from a cab refresh, a new instrument cluster and the outside gests a bit of cosmetic work, too.
On both the TM320 and TM320s, the front axle has been shifted forward, boosting lift capacity by100kg, and they get a lock-up torque converter in gears 4, 5 and 6 that means less power is lost through the transmission.