Is farm machinery getting too heavy?
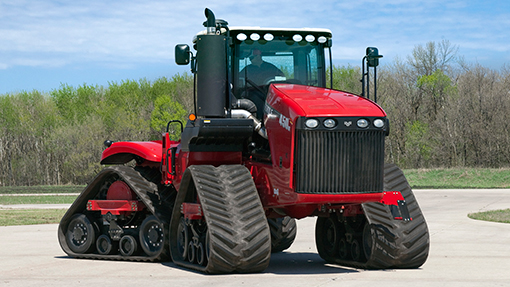
Compaction of soils is nothing new. Even the relatively lightweight machinery used in the 1960s and 1970s was capable of causing it if the conditions were wrong. Too many passes in the same tracks, excessive wheel slippage and too much pressure on the soil contact patch could all cause it.
Nature was able to help in the form of earthworm activity, freezing/thawing and shrinkage/swelling, of course. However, these benefits are less effective at greater depths, which is where the heaviest machines tend to do the most damage.
Problems really start when compacted soil gets wet. Compaction reduces water penetration and air circulation, increases surface run off and slows down residue decomposition.
Compaction can also do nasty things to your fuel bills during cultivations, particularly at depth.
In fact, the amount of power required rises exponentially the deeper the cultivator has to go. At worst it can cost 20% of your yield.
Are tractors to blame?
If you look at the weight of a 1975 75hp Ford 5000 and compare it to a 2013 75hp New Holland 4.75 Powerstar you’ll find there has been an increase in weight of just 4%. Given that the former was two wheel drive and the latter four-wheel drive, that’s not a lot.
Crunch the numbers with Massey Ferguson and John Deere and you’ll find a bigger difference but no more than you would expect.
Much more striking is when you compare an average-sized tractor from 1980 (75hp) with one from 2013 (150hp).
Taking a selection of 150hp machines gives an average weight of 6,000kg, more than double the 2,850kg average weight of the 75hp machines from 30 years ago.
And even within the 2013 150hp tractors there is a tonne of difference between the New Holland 7.200 and the Valtra N143.
What about other machines?
The increase in weight has been even more dramatic in other types of farm machinery. A six-row Herriau beet harvester from the 1980s weighed 12t while today a Holmer T4-40 weighs 62t fully loaded.
That increase has more to do with the bigger bunkers being fitted on beet harvesters than the tare weight of the machine. In fact, in any top-of-the-heavies ranking the top five would be occupied by beet harvesters.
Other machines can be surprisingly heavy too, though. Dammann’s three-axled self-propelled sprayer tips the scales at 23t while triple-axled chaser bins from Richard Western or Hawe gross at 39t.
Combines aren’t exactly pussy-footing around the fields either. Claas’s Dominator 105, the company’s flagship in the 1980s, weighed 12.9t with a full tank and 4.8m cutterbar. That gave it a ratio of 2.7t of weight per metre of cutterbar width.
Today a tracked Lexion 780 with 12m header weighs 32.6 tonnes fully loaded. However, it has the same 2.7t/m ratio.
Surely these big machines have a better power-to-weight ratio than in the past?
When it comes to primary tillage machines, the answer is, not really. This is because about 40-55 kg/hp seems to be required to transmit power effectively for draft work and this ratio doesn’t change as horsepowers rise.
Does putting on bigger tyres solve the compaction problem?
Theoretically, doubling the weight of a machine and doubling the area of the tyres that is in contact with the soil would maintain the same pressure. A fully-loaded 47t Ropa Panther beet harvester on four tyres, for example, has a higher axle weight than its bigger brother Tiger at 60t on six tyres.
In practice, however, the overall weight of a machine does matter since in field conditions is the weight is rarely spread evenly. A 60t beet harvester running unevenly in wet conditions can cause great damage.
Could even bigger tyres help? Maybe, but anything wider than the current 1,050mm size starts to get unfeasible. It also means the manufacturer has to reduce the width of the machine or oblige drivers to have to have an escort every time they go on the road.
Of course, larger diameter or taller tyres can achieve the same effect, but raising the centre of gravity isn’t ideal either.
Are there any other clever solutions out there?Â
Central tyre inflation systems can help but they are still expensive items and the driver has to remember to actually use them. Their advantage is that low pressure and better traction can be achieved in the field, while higher pressure improves handling on the road.
What about more axles?Â
Continental manufacturers like Kotte and Fliegl are increasingly fitting four axles to spread the load, but it’s not a cheap option.
Holmer offered a rear axle on its beet harvesters with four tyres instead of two to reduce ground compaction, but it turned out to be too expensive and difficult to operate.
The problem is that extra axles often come at the expense of machine functionality – a four-axle beet harvester, for example, would leave little space for the cleaning turbines.
What about tracks?
Tracks are being fitted to more and more machines, including pea viners, potato, sugar beet and forage harvesters, and do cut ground pressure Grimme’s Rexor 620 beet harvester exerts a force, when fully laden, of 152kN/sq m, while the tracked Maxtron, with similar bunker capacity exerts only 111 kN/sq m.
Tracks, however, come at a price around ÂŁ40,000 more when fitted to combines or beet harvesters.
How much bigger can tractors get?
From a purely technical point of view there is no limit to power output – many construction machines have 3,000hp under their bonnets. Moreover, the biggest ag tractor ever made (the 900hp Big Bud 9600) weighed 45t and was 6.1m wide.
In western Europe, however, there are practical and legal constraints to making machines any bigger. Paul Freeman, Quadtrac product manager at Case IH, believes the challenge is whether the industry can repeat the trick of the last 30 years: double horsepower but within more or less the same dimensions.
A 1970s Steiger Panther III pushed out 325hp and weighed 15.3t, for instance, while a Quadtrac 620 has 620 hp and weighs 26t.
A hypothetical 900hp machine for western Europe faces a number of issues. Tracks can go wider – Case already offers a 910mm version – but making them longer would mean redesigning running gear and reducing the turning circle. “A commensurately larger fuel tank, say 3,000 litres, would be required but already most of the back end of a Quadtrac is fuel tank,” he says.
Radiators would need to be bigger but tractor makers are already finding this a problem, not least since Tier 4 compliant engines run at higher temperatures. Finally, the machine would need to weigh around 40t to transmit power effectively.
Why can’t machinery makers cut the weight of machines?
Car manufacturers have managed to cut the weight of steel in their vehicles to 70% of what it used to be. Lighter, high tensile steel, aluminium and plastics have helped to make up the difference.
So why can’t ag machinery makers do the same thing?
It’s simply that the sheer amount of steel required to provide the required strength makes cutting weight on farm machinery hard. Aluminium has started to make inroads into agricultural engineering. Biso’s 12.3m combine header, for example, weighs around 10% less than a comparable all-steel one but it adds 10% more to the price of the header.
German trailer manufacturer Fliegl offers versions of its ASS398 trailer in aluminium, weighing 7,000 kg, more than 2t lighter than the 9,200kg of the steel version. However, there’s a 20% price premium attached to it.
Is Controlled Traffic Farming the answer?
Given that 75% of soil damage occurs on the first pass of a machine, CTF looks to restrict wheelings to just 15% of the land and is really starting to gain traction as a farming system in the UK.
Making the change can be expensive, of course, since rotations, cropping and machine widths have to be matched up.
But as a way of minimising the damage from heavy machinery CTF has the potential to cut fuel use, reduce compaction and greatly reduce the damage from big heavy machines
Model | Type | Weight (kg) | hp | kg/hp | kg/axle |
---|---|---|---|---|---|
1980s | |||||
Ford 5000 | 2wd | 2,680 | 75 | 35.7 | 1,340 |
MF185 | 2wd | 2,594 | 75 | 34.6 | 1,297 |
JD 2130 | 2wd | 3,110 | 75 | 41.5 | 1,555 |
2014 | |||||
NH 4,75 Powerstar | 4wd | 2,800 | 75 | 37.3 | 1,400 |
MF5410 | 4wd | 3,800 | 75 | 50.7 | 1,900 |
JD 5070M | 4wd | 3,850 | 78 | 49.4 | 1,925 |
Weights of ‘average’ 150hp tractors now
Model | Type | Weight (kg) | hp | kg/hp | kg/axle |
---|---|---|---|---|---|
NH 7,200 | 4wd | 6,590 | 155 | 42.5 | 3,295 |
Fendt 515 | 4wd | 6,400 | 150 | 42.7 | 3,200 |
JD 6150M | 4wd | 5,930 | 144 | 41.2 | 2,965 |
MF 6616 | 4wd | 5,900 | 150 | 39.3 | 2,950 |
McCormick X7.450 | 4wd | 5,750 | 150 | 38.3 | 2,875 |
True heavyweights – tractors
Model | Type | Weight (kg) | hp | kg/hp | kg/axle |
---|---|---|---|---|---|
Tractors | |||||
Quadtrac 620EP | Tracked tractor | 24,405 | 628 | 38.9 | 6,101 |
Challenger 875E | Tracked tractor | 19,321 | 590 | 32.7 | 4,830 |
JD 9560R | Articulated tractor | 18,842 | 560 | 33.6 | 4,711 |
Claas Xerion 5000VC | Wheeled tractor | 17,450 | 517 | 33.8 | 4,363 |
True heavyweights – other machinery
Model | Type | Weight (kg) | Load (kg) | Axles | kg/axle |
---|---|---|---|---|---|
Holmer T4-40 | SP beet harvester | 62,000 | 30,000 | 3 | 20,667 |
PMC 1089 | SP pea viner | 31,450 | 2,250 | 3 | 10,483 |
R Western GR30 | Grain chaser | 39,250 | 30,000 | 3 | 13,083 |
Claas Lexion | Tracked combine | 32,615 | 9,875 | 2 | 11,370 |
Dammann | SP sprayer | 23,000 | 13,000 | 3 | 7,667 |