How alternative fuels are helping to reduce farm emissions
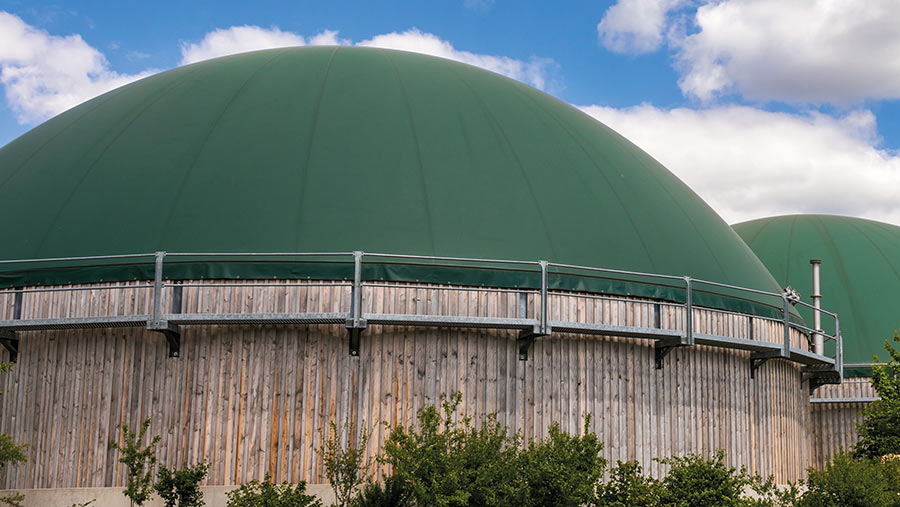
Diesel-powered transport and machinery have been under scrutiny globally for some time now due to their large environmental impact in the form of hefty CO2 emissions.
Recent years have seen the debut of all kinds of prototype farm machines – using everything from solar electricity to hydrogen as a power source – in a bid to reduce the sector’s carbon impact.
Although some alternative fuel solutions are still a few years away from being adopted commercially, there are opportunities to reduce on-farm kit emissions now.
See also: How close is hydrogen to being a viable farm machinery fuel?
Biomethane-powered tractors are being rolled out on farm, using an eco-friendly alternative to natural gas which can be collected and captured from slurry stores and anaerobic digester (AD) plants.
New Holland has been leading the way, with the first prototype of its methane-powered tractor concept launched in 2013. It Is based around the idea of using methane-filled gas cylinders in place of diesel tanks.
Fast forward to 2019 and the T6.180 Methane Power was debuted at Agritechnica, ahead of series production beginning with claims of being able to reduce CO2 emissions by 11% compared with a diesel equivalent, and overall emissions by 80%.
Now, in 2023, there are a number of these methane-powered beasts being used commercially on UK farms, including at Essex-based Sell Farming.
Ben Sell runs a mixed beef, sheep and arable operation with his brother Alex near the New Holland factory at Basildon. The fifth-generation farmers also operate a busy contracting business.
On top of this, the farm grows energy crops such as maize to supply the on-site AD plant.
Farm facts: Sell Farming, Basildon, Essex
- 400-head South Devon beef herd
- 150 Suffolk sheep
- 283ha (700 acres) of arable and energy crops
- 0.5MW gas-to-electric AD plant
Emission concerns
Conscious of the emissions spawning from both his livestock and arable enterprises, Mr Sell says that looking at what they can do as a business to reduce this is an area they are just starting to venture into.
“Something that is being talked about a lot is using direct drills and not releasing carbon from the soil.
“I feel at the minute we’re [the farm] not particularly doing the right thing – we’re still a predominantly plough-based farm and have a lot of problems with blackgrass and ryegrass in the area.
“Looking forward, one thing I am starting to look into doing is strip tillage.
“I feel at the minute we’re not in a position to go down that route in terms of a cereal rotation, but we could be enhancing the use of cover crops and using strip tillage for maize.”
However, they are already making considerable environmental savings through the use of the New Holland T6.180 Methane Power to replace a diesel-powered alternative.
The Sells were among the first to test a pre-production model, after being approached by New Holland to become a “field test” farm for the new methane tractor.
The purpose of this was to allow the tractor to be put through its paces in a real-life situation, with any feedback filtering into what would become the final commercial launch, explains Mr Sell.
“At the time, apart from seeing Corporal Jones’s van on Dad’s Army running on methane, I didn’t really know anything about methane power,” he says.
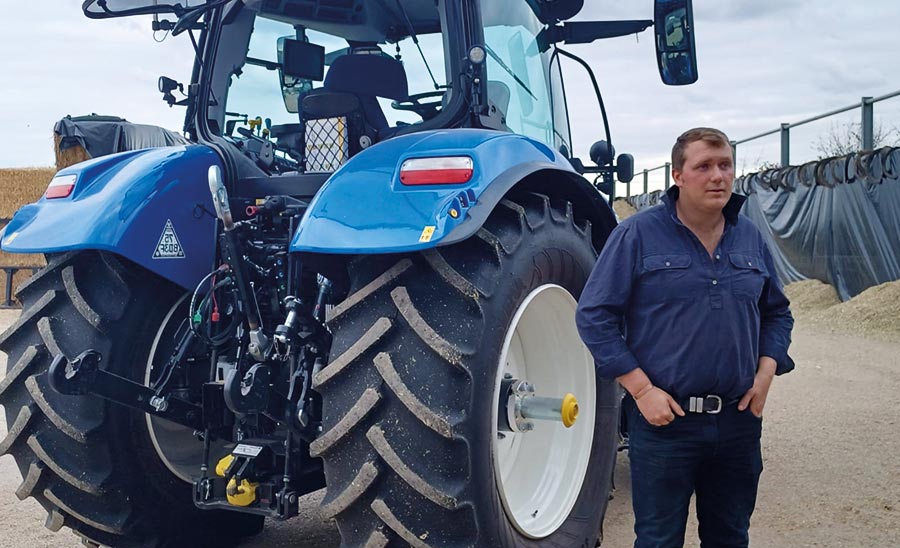
Ben Sell © New Holland
Pre-production testing
Keen to explore the potential of this biofuel, they received the first prototype in February 2021. “It was something very different, and very new, and we went into it with an open mind,” says Mr Sell.
That said, with a busy business he was apprehensive as to whether the methane tractor would be able to keep up with the high hours required of kit on the farm.
This was something New Holland wanted to test rigorously, across various operations – to see exactly what the tractor could, or could not do – and so he put it straight to work with a straw spreader used for bedding up.
“It was on for all of about 10 minutes and the torque just wasn’t there – you’d hit a firmer lump in the bale of straw, and it just didn’t have the torque to push it through. I remember thinking then it had an awfully long way to go.”
Feedback like this went back to the manufacturer for improvements to be made, and today Mr Sell is on his sixth test unit – the version which is now available commercially to farmers in the UK.
“What we tend to do is get a unit come out, we test it and do different bits and pieces with it and then they [New Holland] take it away after several months [to make improvements].”
Compared with that initial prototype, the current commercial version has come on leaps and bounds, says Mr Sell.
“If you had the two beside each other, the characteristics of this one now are totally different – it really is amazing how far they have come.”
On-farm usage
Today, the methane tractor has cemented itself as part of the fleet, says Mr Sell, and is used for a range of jobs around the farm.
“At this time of year on the feed wagon we’ve got a Teagle straw spreader that we do the feeding with as well, as we’re just feeding suckler cows, so we’re using the tractor with that.
“We’re getting a good seven to 10 hours out of it doing that.
“We also find that it’s fantastic for doing jobs like the spraying and the fertilising – it’s a nice little light tractor and very nimble.”
Mr Sell says it is perfect for amenity work such as hedgecutting and flail topping, too. “We also use it for rolling behind the cereal drill and, again, it’s fantastic for that.”
To keep fuel economy at its optimum, Mr Sell says he tries to avoid using the tractor for jobs that require high rpms.
“It’s perfectly capable of doing those tasks, but once you get above 1,500-1,600rpm, you start guzzling the fuel an awful lot quicker than you would be doing the lesser tasks.”
In terms of re-fuelling, he says the process is as quick and easy as with a diesel tractor, but with the added benefit of being cleaner to handle than diesel and odourless.
“I’ve actually done it [refuelled] in a smart shirt before,” he says.
Methane supply
Although the farm does have an AD plant, this is a gas-to-electricity digester, rather than gas-to-grid, so at the moment the methane to power the tractor is being supplied by New Holland.
In the future, Mr Sell says he is keen to look at being able to produce his own biomethane on farm to make use of the slurry from the livestock enterprises.
He is particularly interested in the Bennamann system which facilitates on-farm capture and conversion of methane to biomethane.
New Holland T6 Methane Power – key features
- Powered purely by methane, using a gas cylinder in place of a diesel tank
- Claimed to produce 98% less particulate matter and can reduce CO2 emissions by 11% and overall emissions (compared with the diesel equivalent) by 80%
- These emissions are even lower when using biomethane to power the tractor
Source: New Holland
The system is based on a layered lagoon cover. As well as stopping rainwater getting into slurry, this traps the methane emitted which can then be converted into fuel-grade methane.
“This would essentially couple on to what we’ve already got at the minute,” he says. “Though the infrastructure would initially be expensive, given the tasks that we’d be doing [with the tractor] it would pay for itself.”
By capturing and collecting his own methane, there is also potential to sell any excess gas in the future – making it an even more attractive opportunity, he adds.
In terms of the cost to supply compared with diesel, Mr Sell says it is complex to quantify as it involves converting bars of pressure into the equivalent litres an hour.
But he has identified working the tractor at 1,500-1,600rpm to be the sweet spot for savings when running methane over diesel.
In the long term, Mr Sell reckons this kind of technology will offer a significant cost benefit to farmers, as well as the environmental advantages.
But he believes a government incentive will be required to get alternative fuels rolled out on farms at a wider scale.
“They’re [the government] putting a lot of pressure on us as farmers to try to achieve net zero by 2050, but in order to reach that goal, I really do believe that the government will need to provide some kind of incentive.”
He says grant funding to subsidise the cost of processing equipment or infrastructure – like the Bennamann system – would be really helpful.
Fuel of the future?
Mr Sell says that while he doesn’t believe alternative fuels can fully replace diesel power just yet, these tractors do have a valuable and important place within machinery line ups – particularly if powered by farm-produced methane.
“Ultimately, [the methane tractor] isn’t going to be a tractor to replace all tractors, particularly with our contracting. It has a place on-farm, but I don’t think it could annihilate its diesel counterparts. [On the contracting side] the longevity we’re finding just isn’t as great on some of the higher engine load tasks.
“In the summer, we do put an 18t silage trailer behind it and will use that to bring in grass. The beauty of using it for those jobs is that you’re always using it for return journeys back to the farm, so it’s easier to refuel.
“If you’re a livestock farmer or you have AD you are creating methane. It’s a waste product, and if you’re not capturing it, it’s only going to go back into the atmosphere.
“In the long term, with the right infrastructure and the right advice, I feel like farmers could produce their own fuel, on their own farms, which will create a much more circular process.”
Electric advantages in Norfolk
A loader, telehander and ATV are part of the electric-powered fleet at Stephen Temple’s farm in Norfolk.
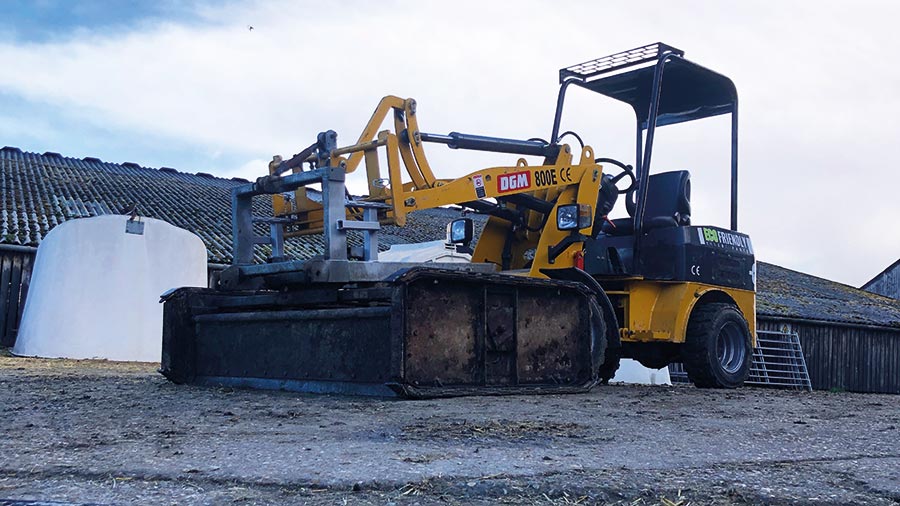
Stephen Temple’s DGM 800E electric loader © Stephen Temple
Together with his wife, Catherine, he runs a 130-head dairy herd at Copys Green Farm and grows a variety of crops such as lucerne and winter beans (grown as a co-crop with oats) for feed, as well as winter and spring barley for seed.
This is on top of the on-site cheesemaking business which is supplied with the milk from the Brown Swiss herd.
Over the past 15 years, the Temples have been making a conscious effort to improve the sustainability of their business, which has largely focused on energy and fuel efficiency due to Mr Temple’s background in engineering.
“As an engineer, I’ve always been interested in energy – when I was working overseas in Malawi for many years, I was working on reducing energy consumption on tractors. It’s something I’ve been involved in for a lot of years.”
This desire to be more energy efficient has seen the Temples install an anaerobic digester plant which produces 170kW of electricity – fed via the slurry from the dairy herd and maize silage – and supplies the farm, the cheesemaking and the farm cottages, with excess exported to the National Grid.
They have also moved to a strip tillage system, having previously been plough-based. As well as the benefits to the soil and soil carbon, the move to strip tillage has reduced passes in the field and therefore diesel consumption.
To reduce fuel consumption further and make use of the on-farm electricity generation, Dr Temple has incorporated a number of electric-powered vehicles into his machinery fleet over recent years.
This includes an electric John Deere Gator – which he uses for bringing cows in for milking – as well as an electric forklift used for moving the milk around for cheesemaking.
He trialled a Faresin electric telehandler but did not feel it was a suitable electric alternative for his farm.
“The design isn’t really ready for farm use as far as I can see,” he says.
“The cooling air intake was right behind the wheel, so as soon as you drove into the straw yard it got covered up with straw and wouldn’t work, so the oil overheated. In construction, it would be fine, but not in agriculture.
“We’ve also got a little electric articulated steer handler which I want to convert,” he explains.
“At the moment, when bedding our cubicles we’ve got to walk behind a petrol-powered straw blower, which works extremely well, but the problem is that it’s got a petrol engine, with a very hot exhaust, and is very close to straw – so we go through a fire extinguisher or two a year.
“My idea is to put that [the straw blower] on the forks of the [electric] handler, and power it from its battery. That’s a project for the future.”
Leaning on his engineering skills, Mr Temple is currently working on building a machine that is based on the Tow and Fert sprayers – which are designed to maximise the efficiency of fertiliser.
“These are only petrol or pto-powered, so if we want an electric one, we’ve got to build it ourselves. We’ve got the chassis made and we’ve tested the pump and nozzle,” he says.
“We now just need to finish welding and get it painted up and ready for use.”
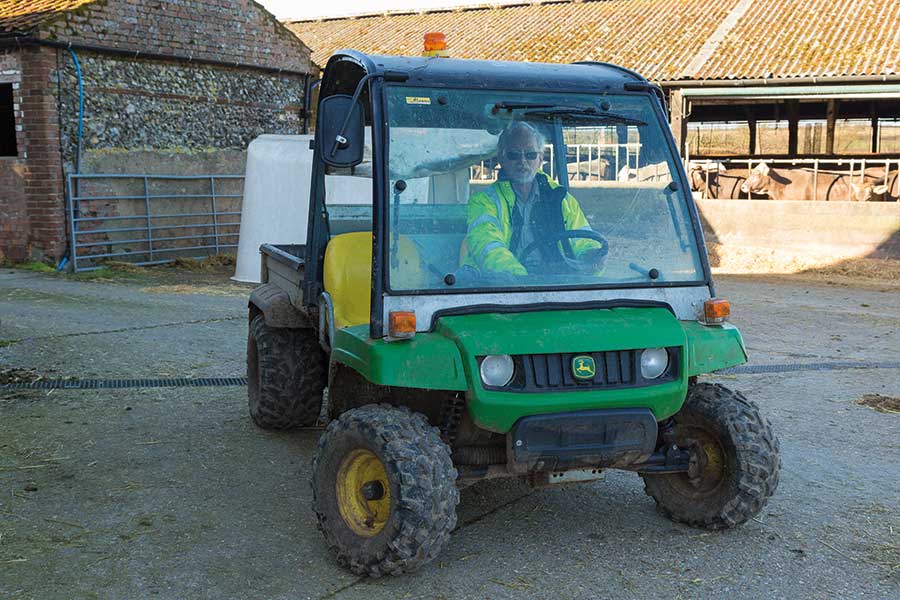
Stephen Temple in the electric Gator © MAG/Judith Tooth
All cars on the farm are electric too, including a recently bought electric pick-up to replace an old Land Rover Defender.
While there is an obvious cost-saving benefit from being more efficient with energy, Mr Temple says the environmental advantages and emission savings are hugely important to him.
“Global warming and climate change is the biggest threat to mankind – the planet will survive, but not in a format that’s kind to humans.
“The more I can reduce waste, the happier I am. If we can avoid buying fuel in, that’s all for the good of the environment.
“People are concerned with the cost of dealing with climate change, renewable energy and being environmentally conscious, but we’ve found that pretty much everything we’ve done has saved us money or made us profit.”
While Mr Temple has the setup on farm to make electric-powered kit work, he believes that wider adoption of alternative fuels is likely to be limited by the significant investment required.
It is this cost that is currently preventing him from looking at other fuel options such as methane.
“I looked at methane a few years ago, when diesel prices were lower, and the cost of putting the kit in to clean up the biogas to make biomethane, and then to compress it into a tank to fuel a tractor, was not competitive with red diesel.
“The methane tractors also don’t really have enough range for a day’s work [for us], when you’re working five miles from home.”
Hydrogen power is also something he does not envisage being part of the plan anytime soon.
“It’d be better to wait for battery technology to evolve – which it’s doing incredibly rapidly at the moment.
“If you’re going use hydrogen, it has got to be made renewably from electricity otherwise you might as well just use diesel.”