New Holland CR11 combine takes fight to Deere and Claas
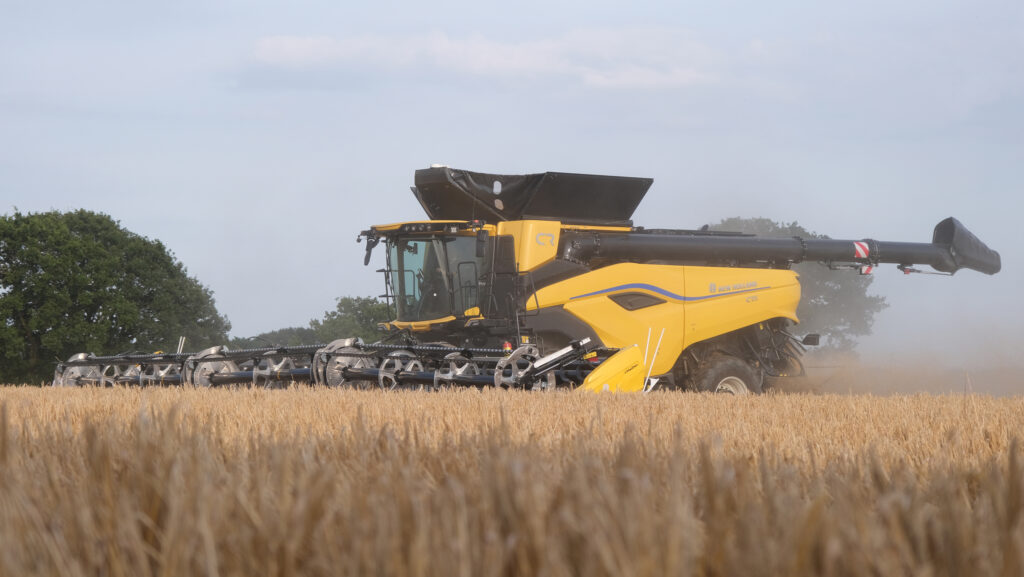
While New Holland’s flagship CR10.90 was busy setting a combining world record in a 2014 Lincolnshire wheat crop, its engineers were already working on a machine that could beat it.
A decade later, the CR11 and CR10 broke cover, promising higher outputs, fewer losses and lower fuel consumption than their predecessors.
Not only that, but the firm reckons both of these newcomers have the Claas Lexion 8900 and John Deere’s X9 licked when it comes to output and losses.
See also: Brace of John Deere X9 combines gobble 170t of wheat an hour
Doing this will require spot rates of well over 100t/hour to be achieved while throwing virtually nothing over the back – a feat the firm will need to demonstrate as the first few models make their way around the UK this harvest.
These two CRs have identical internals, so the only significant differences for buyers to consider are the engine output and grain tank size.
Rather than just turn down the power on the lower-output CR10, engineers have opted to fit a smaller 12.9-litre FPT Cursor 13 block.
Developing 635hp, this is smaller and less powerful than the engine used in the old CR10.90, although improvements to driveline efficiency mean it delivers greater performance.
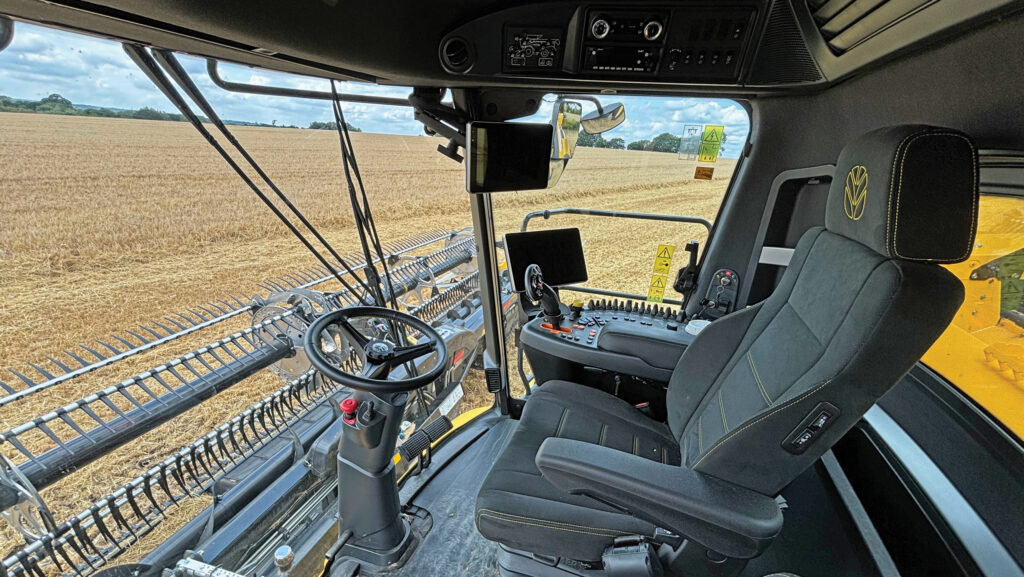
The cab © James Andrews
CR11s are considerably gutsier, with a 15.9-litre Cursor 16 that delivers 775hp – a full 75hp more than the 10.90. That said, this is still 15hp shy of what Claas offers in the Lexion 8900.
Clean grain storage capacity is 16,000 litres on the CR10, with its bigger sibling pushing this up to 20,000 litres, both of which are emptied via high-capacity augers with standard unloading rates of 159- and 210-litres/sec respectively.
On the CR11, this allows the entire contents to be jettisoned in just over a minute and a half.
At this speed, topping off trailers can be a risky venture, so there’s the option of slowing the unloading rate to something more manageable.
A hydraulically adjustable pivoting spout also comes as standard to help accurately direct the torrent.
Various cutterbar formats are available in widths of 10.6-15m (35-50ft), although most UK machines are expected to go out with a MacDon FD2 Flexdraper.
According to New Holland, only the two largest of these (45ft and 50ft) can push the CR11 to its full potential, so those that struggle to manage a table of this size will probably be better off with a CR10.
Large-diameter rotors
Pushing the combines to achieve such high outputs has required a complete reworking of the threshing, separation and grain cleaning systems.
This starts right at the front, where a wider 1.7m intake housing has been fitted, complete with front face adjustment and lateral tilt.
From here the crop is fed into a so-called “dynamic feed roller”, which accelerates the material and splits it into two streams feeding each longitudinal threshing and separating rotor.
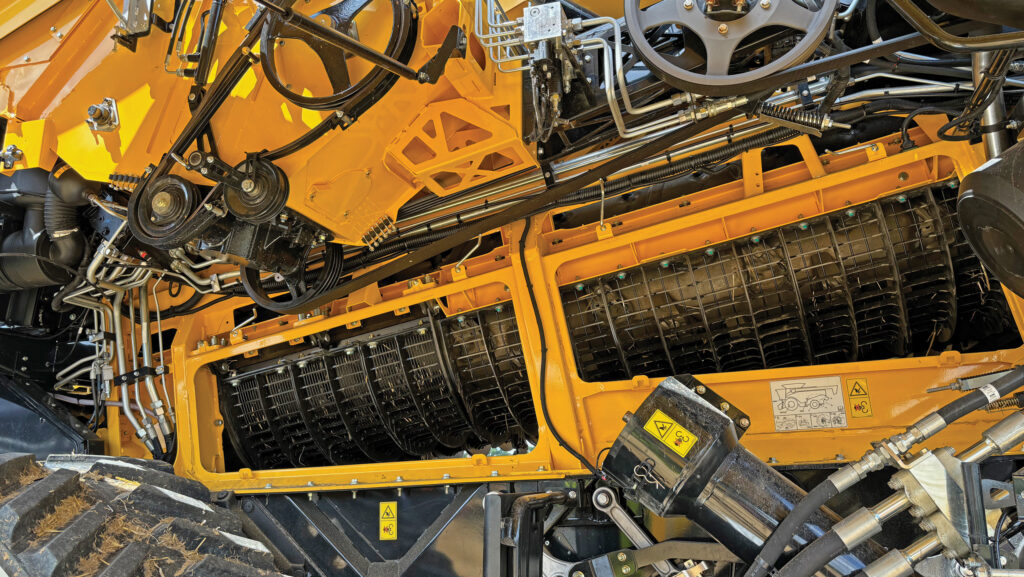
The rotors © James Andrews
Beneath this, there’s a stone trap to stop foreign objects going any further into the internals. There’s the option of opening this hydraulically so operators don’t have to grovel in the dust.
Measuring 600mm (24in) in diameter, the twin rotors are 40mm wider than those used on the CR10.90 and slightly longer, which means they can cope with considerably more crop.
Plus, the mix of standard, spiked and hybrid rasp bars helps improve threshing efficiency.
The latter are taller than the standard rasp bars and have a greater sidewall angle to help accelerate the material as it passes through a stepped section of the rotor cage, positioned between the threshing and separation zones.
This gives the crop the opportunity to expand before being squeezed again, helping to free any grains trapped in the mat of straw.
Double cleaning area
But it’s no good shovelling copious amounts of crop through the machine if the sieves can’t cope.
To take this out of the equation, New Holland has doubled up the cleaning area.
There are now two top sieves, two bottom sieves and two clean grain augers feeding into a massive elevator that whisks it into the tank.
A nifty side-shaking function has also been incorporated to make sure grain is evenly distributed over the sieves.
This is controlled using air pressure sensors that detect how much air flow is making its way through the crop.
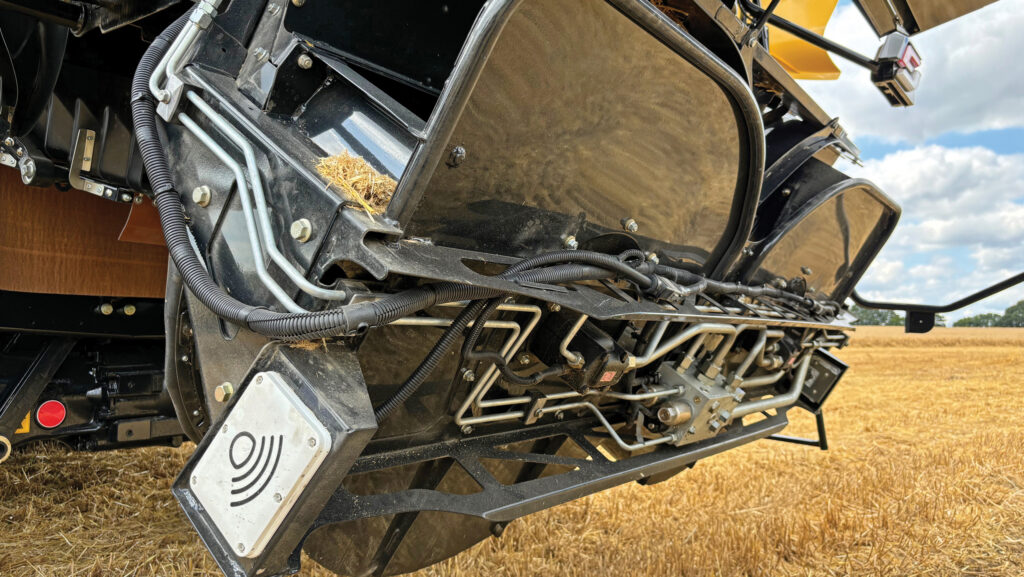
The straw and chaff spreader © James Andrews
If one senses a drop in pressure, because the thickness of grain is too great, it’ll trigger a set of electric rams to shake the relevant section, thus levelling it out.
The grain pan and both top sieves can shake independently which, as well as the crop distribution role, offers slope compensation of up to 28%.
Residue management has been improved too, with a combined straw and chaff spreader than can evenly distribute over distances of up to 18m.
The straw chopper has been designed to spin the opposite way to previous incarnations, which means it grabs material directly off the rotors, rather than having the complexity of a belt to transport it.
Once chopped, the straw and chaff drop into a dual disc spinner. This is controlled by a radar system that constantly monitors the quality of the spread pattern, before adjusting the rotor speeds and vane angles to suit.
Simplified driveline
You’d think all this extra crop processing potential would require bags of extra power.
But engineers have got around this by massively simplifying the driveline, all of which starts by mounting the engine longitudinally at the same angle as the rotors.
Unlike the CR10.90’s driveline, which went around the houses, the CR10 and CR11 are largely run straight from back to front.
They’ve also opted to send drive to the rotors via a CVT transmission which, as well as being efficient, gives the option of reversing things to clear any blockages without leaving the seat.
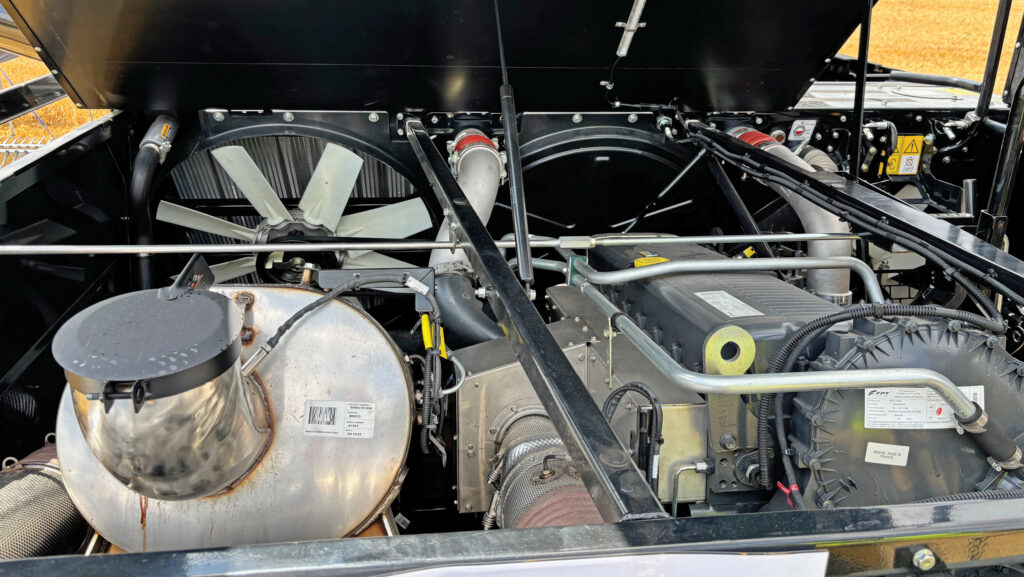
The engine bay © James Andrews
The majority of major components are now shaft driven, with no chains whatsoever and just a handful of belts, most of which are located on the unloading system.
An added benefit of this setup is that there are very few grease nipples and none that have to be tended to daily.
Efforts have also been made to keep the engine bay free from dust and chaff build up.
As well as having a cooling system that draws fresh air though the area, the exhaust manifold is boxed in to prevent any combustible materials coming into direct contact with it.
Same cab, new tech
New Holland hasn’t gone to the trouble of introducing a new cab for these combines, but it has made some tweaks to the level of technology on board.
Firstly, there are now two of the firm’s latest Android-based Intelliview 12 screens, which have sharper graphics, easier-to-navigate menus and a visualisation of the machine that shows all the main settings.
There’s also a slicker automatic headland turn system and the option of a 360deg camera kit that gives operators an aerial view of the combine and its surroundings.
On top of that, buyers are able to install an near-infrared sensor on the clean grain elevator that feeds on-the-go protein measurements to the screen.
Those running more than one machine in the same field can share settings to improve efficiency and produce combined coverage maps which makes yield recording more accurate.
Creature comforts include high-spec leather or cloth seats, a new multi-zone climate control system with the addition of floor level outlets, and a handwash station by the steps.
The CR10 and CR11 are currently working their way around the UK carrying out demos, with the first examples due to arrive on farms ready for harvest 2025.
CR10 vs CR11 specs |
||
|
CR10 |
CR11 |
Engine |
12.9-litre, six-cylinder Cursor 13 |
15.9-litre, six-cylinder Cursor 16 |
Max power |
634hp |
775hp |
Grain tank capacity |
16,000 litres |
20,000 litres |
Unloading speed |
159 litres/sec |
210 litres/sec |
Threshing and separating |
Twin 600mm (24in) threshing and separating rotors |
|
Grain cleaning |
Twinclean setup with dual upper/lower sieves and clean grain augers |
|
List price (excluding header) |
£825,417 |
£916,285 |