JMT’s 33-strong used Claas combine fleet in high demand
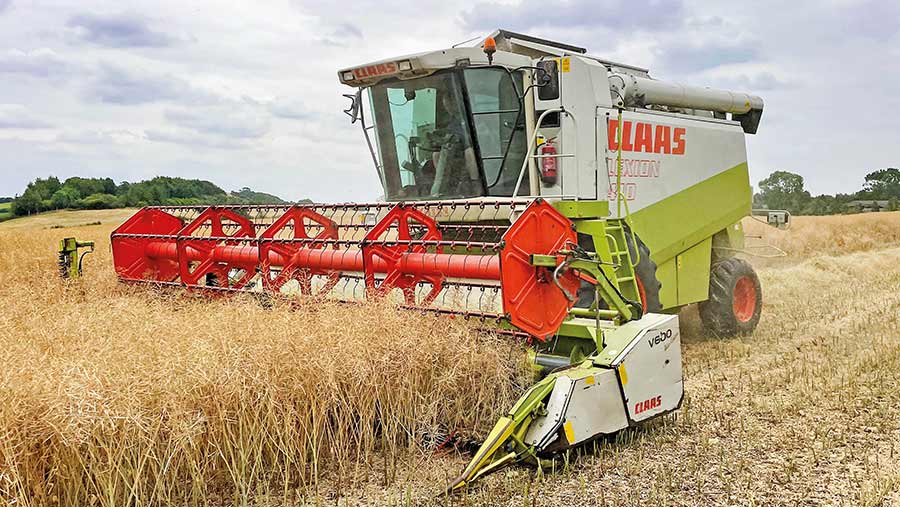
Breakdowns and repair bills are unavoidable irritations when running a second-hand combine harvester.
But for those who can’t justify shelling out for a new machine and don’t want to go down the route of using a contractor, it’s the most obvious option.
There is a third way though – hiring.
Warwickshire firm JMT Engineering has been in the business of renting out combines for more than 40 years and has amassed a sizeable fleet of 33 Claas machines during that time.
See also: Guide to buying a used hill-sider combine
Most of these hail from the 1980s, 90s and noughties, with the newest sporting a 2007 registration plate.
It’s a different approach to many other businesses that hire out more up-to-date combines, but it means the firm can cater for farms of all sizes.
The result is that those with fewer than 100 acres to cut get just as good a deal as those with more than 1,000.
JMT does this by charging a flat rate of £25/acre and providing each farm with a combine to suit their acreage.
So, while someone with a small area to cut gets a 1980s Dominator 96, a larger customer might take delivery of a Lexion 580 or 600 Terra Trac.
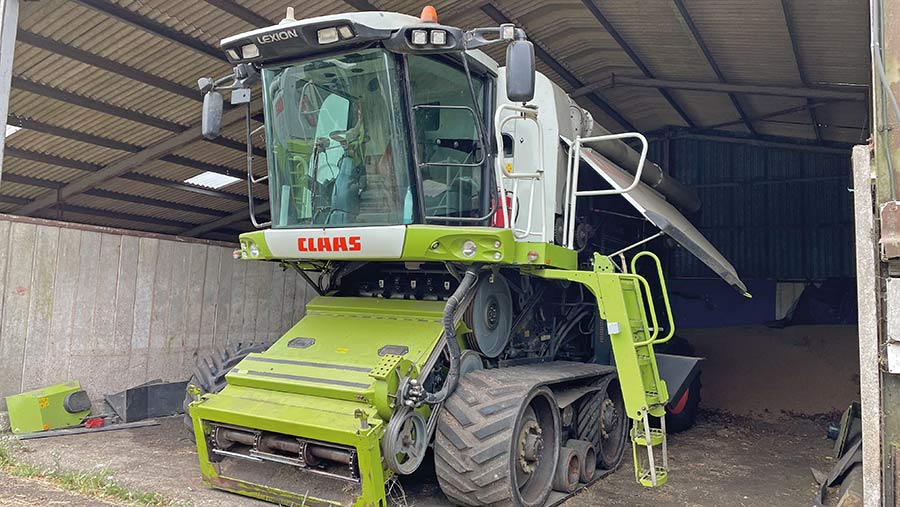
The newest machine – a Lexion 600 © James Andrews
Thanks to a huge stock of headers, customers are sent a model to match their farm and the crops they are cutting.
That means those with oilseed rape receive a Vario model, or an additional header with rape extensions fitted.
The company also has a large stock of extras, such as side knives, lifters and dual wheels, so machines can be set up just the way the customer wants them to suit the conditions.
Regardless of its age or history, each of JMT’s combines gets a complete overhaul before it joins the fleet, as well as a comprehensive service before the start of each season.
“The last thing we want is one of our combines breaking down during harvest, so we get them up to scratch and try our best to make sure they are in perfect working order before the season starts,” says owner Mark Teverson.
If a combine does give trouble, he and his team aim to have it up and running by the next day at the latest.
All maintenance, repairs and wearing parts are included in the cost, but hirers do have to foot the bill or claim on their insurance if they break something significant.
The business is a family affair, with Mr Teverson’s wife Trisha running the office and sons Ian, Roger and Richard travelling the country to keep the machines in good working order.
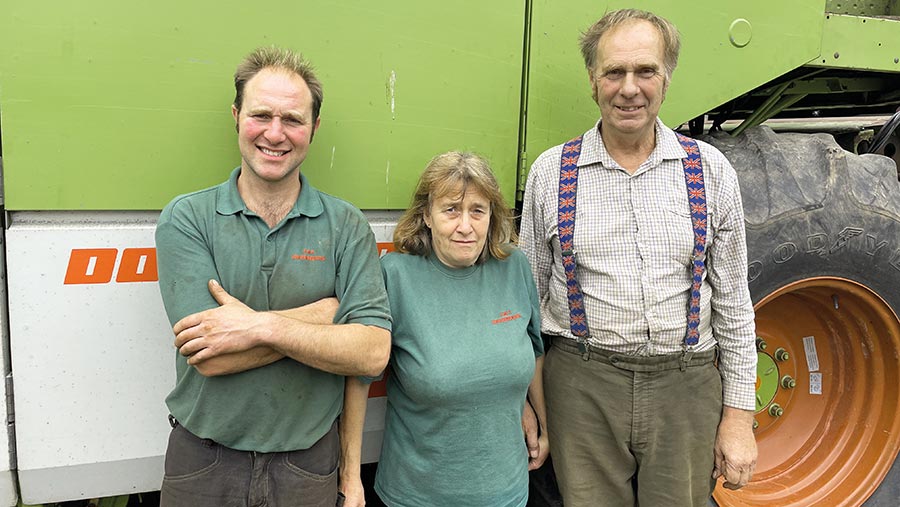
JMT Engineering owners Ian, Trisha and Mark Teverson © James Andrews
They are joined by two other mechanics, giving a total of five roving support vehicles looking after the hire fleet, as well as servicing and repairing a further 100 Claas combines.
Back at base, there are five additional engineers who fabricate parts and work on machines in the workshop.
The firm’s core customer base is in Warwickshire and the surrounding counties, but it has machines scattered as far as Cornwall, Norfolk and Essex.
Service machines are spread even further, in some cases right up to Scotland.
Many customers have been with the firm for years and they will keep the same combine from one season to the next. “I think there’s one in Essex that I haven’t seen for 10 years,” says Mr Teverson.
To get combines out to farms, JMT runs a mix of classic Foden and DAF HGVs with beavertail trailers.
However, if the destination is less than 70 miles from the yard at Bishops Itchington, Warwickshire, they tend to drive the machine on the road, with the header on a vehicle in front acting as an escort.
This method saves taking two trips with an HGV, which is required when there is a wide header to move.
Combines and headers
Mr Teverson started his combine hire business 45 years ago with a New Holland/Clayson M140.
However, his allegiance soon turned to Claas and he’s stuck with the German manufacturer ever since.
At the older end of the spectrum the firm runs Dominator 96, 98, 106 and 108 models that were built in the mid-to-late 1980s.
One of these, a six-walker 106 with 17ft header, is approaching 5,000 hours and has an 80-year-old driver on the seat.
The next step up in modernity are five-walker Dominator Mega 204s and their six-walker sibling, the 208, which were the first combines to feature Claas’ APS pre-threshing cylinder.
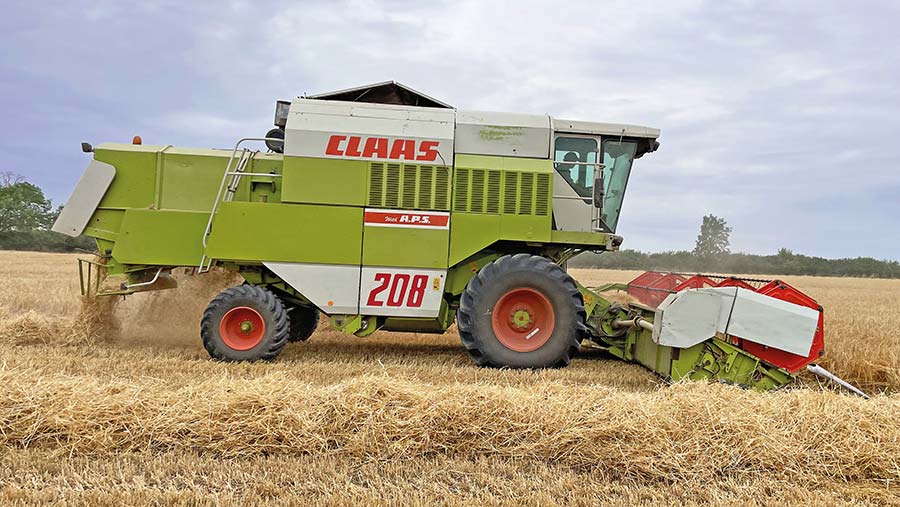
Claas Mega 208 © James Andrews
These would be happy cutting 500 acres or more, but they tend to go to farms with a smaller area than this.
A large chunk of the 33-stong fleet is made up of 400-series Claas Lexions, which range from small five-walker models such as the 410, 420 and 430, to the hybrid 480.
The business also runs a few of the newer 500-series machines and one 600 Terra Trac.
Mr Teverson avoids Medion, Tucano and Avero variants as there are fewer of these around and parts are harder to come by. Concentrating on fewer models also makes it simpler for his spare parts stock.
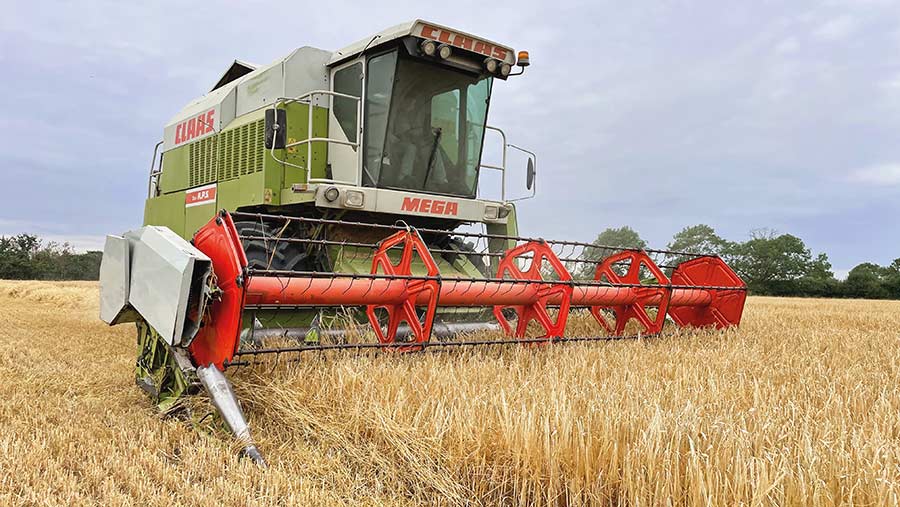
Claas Mega 208 © James Andrews
Complete overhaul
Many of the combines on JMT’s hire fleet arrived with some sort of ailment, such as a blown engine, failed hydrostat or crumpled back end.
But thanks to the team’s experience of repairing and maintaining these machines, and its access to spare parts, they are soon fettled into prime working condition.
In addition to the obvious repairs, all combines destined for hire receive a complete new set of belts and chains, a thorough bearing inspection and a comprehensive service, including the air conditioning.
Any components showing signs of wear are repaired or replaced using a combination of new, salvaged or remanufactured parts, all of which are kept or made on site (see Combine breaking and parts).
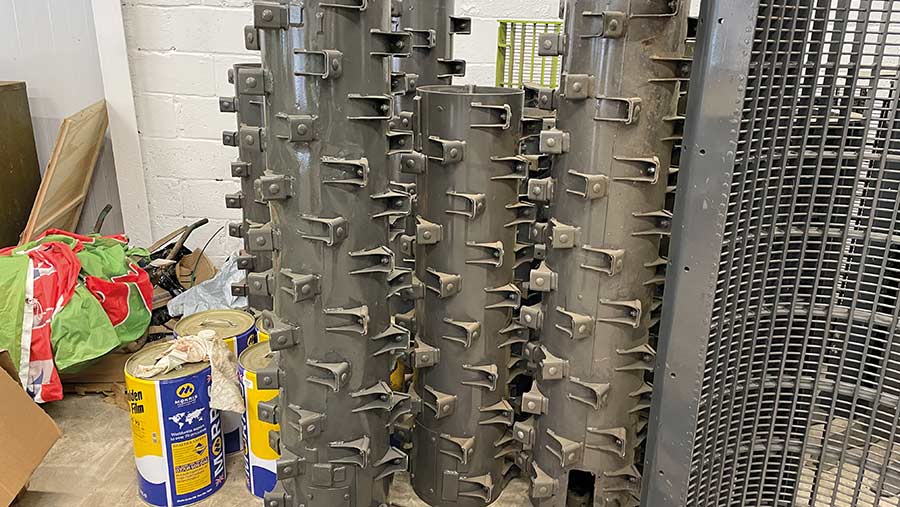
© James Andrews
The latest model to receive this treatment is a hybrid Lexion 480, which has had the standard overhaul, plus a fresh set of front rollers, a new APS drum and new main drum and concave.
Because the firm can justify doing so much work to a combine, previous workload is unimportant, and several members of the fleet are on 4,000 hours or more.
“We’re a bit obsessed with combine hours in this country, but in other parts of the world you see plenty with 10,000 hours or more on the clock,” says Mr Teverson.
“If they’re properly looked after, a Claas combine can still be reliable after doing that much work.”
Each winter, one or two combines are put through the recommissioning process so that they are ready for service the following season.
Constantly adding machines in this way has allowed Mr Teverson to slowly build up the fleet without having to put any combines on finance.
However, he doesn’t plan to expand much further as the team doesn’t have the capacity to look after many more. Instead, new machines will replace those that are sold when they get offered a good price for them.
So far, none of his combines have been taken out of service because they were deemed to not be cost effective to repair and he has lost only one to fire.
Part of this is luck, but they also help reduce the risk by sending all large machines out with a Hydrovane compressor for blowing off dust and chaff at the end of the day.
With 33 of their own combines and 100 others to maintain, the Teversons operate a year-round servicing operation.
“I give the staff a month off combines at the end of harvest, but after that they’re flat-out getting machines ready until the start of the next season,” he says.
In a bid to keep combines in prime condition, each customer is encouraged to make a list of faults while they’re driving, which are tackled when the fitter goes through it.
Once the combining season starts, the team is on call 24-hours a day to help keep people going.
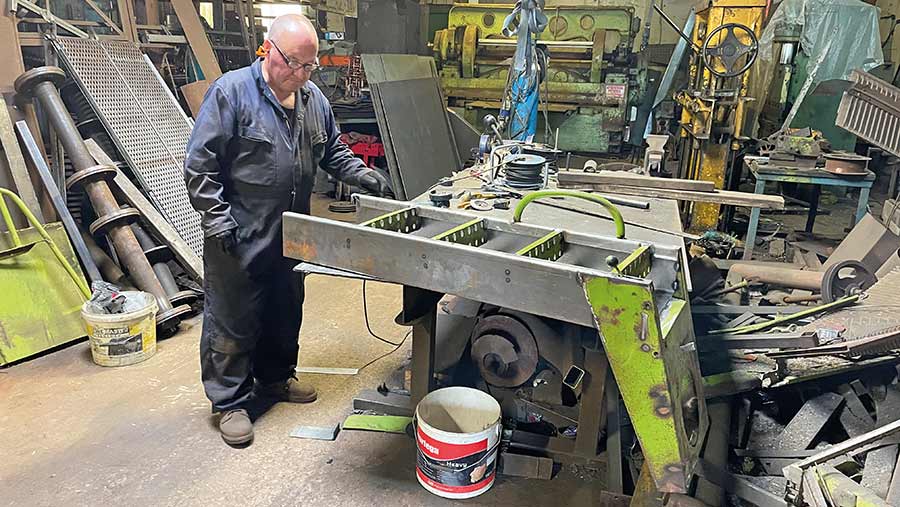
© James Andrews
Combine breaking and parts
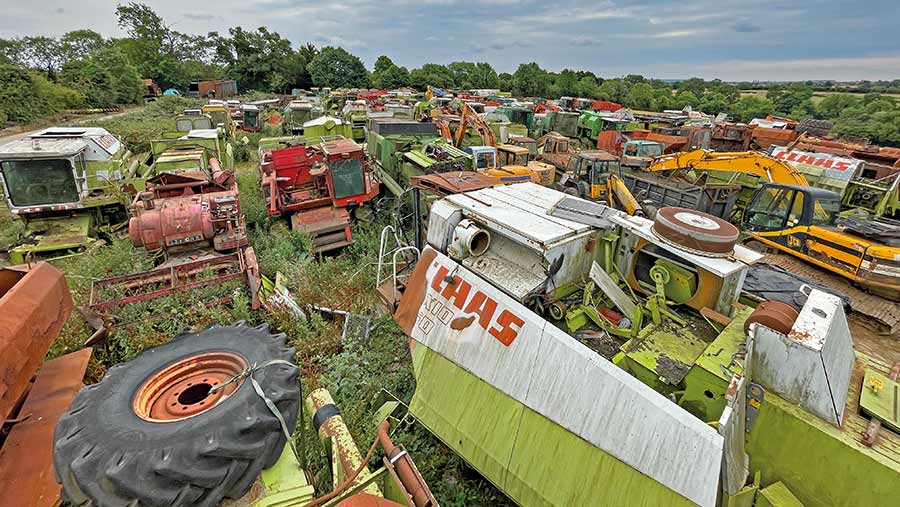
© James Andrews
In addition to its combine hire business, JMT Engineering has a yard brimming with 150 breaker combines.
Many of these are fire damaged or crumpled Claas Lexions and Dominators, but there are also New Holland, Massey Ferguson, John Deere, Laverda and Case models laid to rest.
Some of the most popular parts are removed and put into secure storage as soon as the machines arrive, but the partially stripped carcasses are left in the graveyard so that they can be raided when calls come in for less common items.
To complement this stock of used components, JMT imports most of the regular replacement parts for Claas combines and some from other brands.
These include everything from bearings, belts and knife sections to new drums and concaves.
One all-too-common part is the variator pulley for a Claas Lexion, which fails due to a lack of greasing.
It’s awkward to do, as there are four grease nipples, some of which can’t be reached without adjusting the drum speed.
However, it is important, as a big Lexion can destroy one in 300 acres or less.
Genuine replacements cost more than £4,000, but JMT has sourced a version that comes in at about £2,000.
An on-site engineering workshop fills in the gaps, remanufacturing parts such as steps, front rollers, sieves and augers.