How combine add-ons can help slash weed seed spread
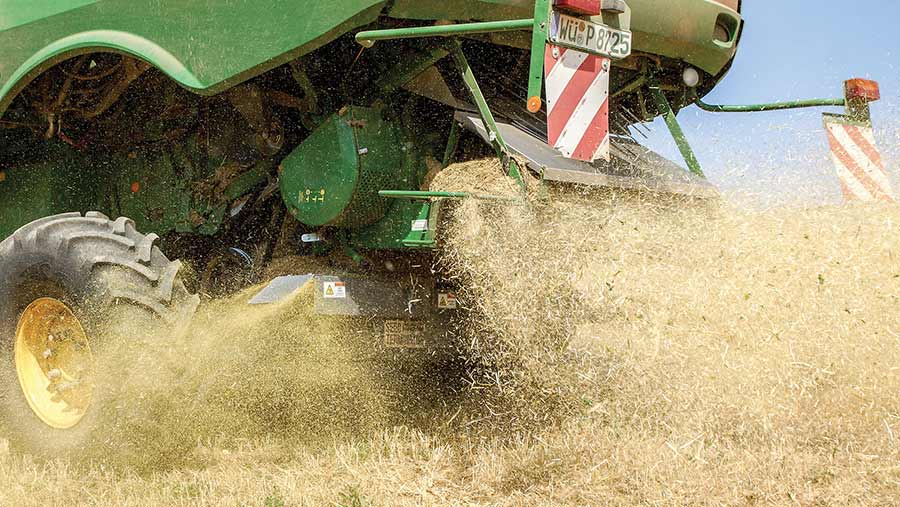
Combinable crop producers in the UK are being pushed into a corner when it comes to controlling herbicide-resistant grassweeds and it’s looking increasingly likely that the answer will come from mechanical methods, rather than a chemical can.
New and effective weed killers are notoriously difficult to get through European regulatory processes and the future of broad-spectrum herbicide glyphosate is still uncertain. Added to that, UK growers could be subjected to further restrictions or taxes on pesticides to reduce use as new agricultural and environmental policies evolve.
All this is leading to a rethink in weed control strategy and in the long term, harvest weed seed control (HWSC) is likely to become an important tool on UK arable farms, according to Niab weed expert John Cussans.
See also: Australian inventor builds herbicide-resistant weed seed crusher
Mechanical techniques
HWSC is a broad banner for several mechanical techniques – most pioneered in Australia – and is aimed at managing weeds that have escaped in-crop herbicide programmes by minimising seed return at harvest (see “Harvest weed seed control options”).
Harvest weed seed control options |
||
|
What is it? |
Viable in the UK? |
Narrow windrow burning |
Straw and chaff fraction dropped into narrow lines and burned. |
No – straw burning is banned in the UK. |
Direct baling |
Square or round balers are bolted to the back of the combine and collect all straw and chaff in bales. |
Unlikely – high-biomass crops in the UK mean power requirement is too high for combines to cope. |
Chaff lines |
Chaff fraction is funnelled into narrow rows behind the harvester and left to rot over winter. |
Possibly – allows farmers to concentrate problem into manageable strips. The long UK growing season may restrict time in rows between crops and generally benign conditions may see unsatisfactory weed seed kill rates. |
Chaff tramlining |
Chaff fraction is funnelled into tramlines in a controlled traffic farming (CTF) system. Seeds are killed in the harsh environment. |
Yes – several tramlining machines are now working in the UK with some success. |
Chaff collection |
Harvesters are modified to allow the separation of the chaff fraction. It can be dropped in the field and burned, collected and removed in carts or funnelled on top of the straw swath for baling in a separate operation. |
Yes – chaff-collection systems are being used in continental Europe, particularly in organic systems. Cost benefit and finding end use for the chaff may be factors that halt its uptake |
Cage mills |
Counter-rotating cage mills are integrated into the rear of the harvester. Weed seeds in the chaff are pulverised after passing through the mills, rendering them unviable. Control rates of up to 98% have been noted in Australia. |
Yes – seen as the Rolls Royce of HWSC, interest in cage mill technology is growing in the UK. One drawback is seed retention on problem UK weeds at harvest, so it is not highly effective on all species, such as blackgrass. Prime candidates for good control include Italian ryegrass, bromes and wild oats. |
Cutter bars |
Various machine designs cut the head of tall weeds above the crop before seed becomes viable. Examples include the CombCut, Weed Surfer and Zurn Engineering’s Cut and Collect. |
Yes – already well established in organic and some conventional systems for control of grassweeds in cereals, such as blackgrass and wild oats. |
Many of these involve capturing chaff, which contains about 95% of the weed seeds that go through the combine and have been a resounding success down under.
Widespread adoption is helping to turn the tide on weeds resistant to multiple herbicide modes of action, such as annual ryegrass (Lolium ridigum), wild oats and wild radish.
Whichever mechanical method is being used, Mr Cussans says it will be important to consider that each may be more or less effective, depending on target species.
“I don’t believe there is going to be one tool for the UK that everyone uses. It is more likely that different approaches will be needed for different weeds and we can already see that with one of our problem species, blackgrass.
“When you get to harvest, most of the seed has been shed. Lolium multiflorum [Italian ryegrass] holds on to its seed much longer and goes through a combine, so something like a seed destructor could be very effective,” he says.
UK research
Niab and Rothamsted Research are part of the EU-funded IWMPRAISE project, looking at a range of alternatives to herbicides, including precision mechanical weeding and harvest weed seed capture.
One of the key aims is to see how effective cage mill technology might be in the UK, with the concept – originally developed by Western Australian farmer Ray Harrington – transforming and simplifying HWSC and starting to attract serious interest here.
This year, those involved in the project will aim to do two things. Firstly, Rothamsted imported a standalone mill and will feed in viable raw weed seed from various UK species with different rates of chaff material to look at its efficacy.
The process will get some baseline data in a controlled environment for each species and will be complemented by Niab’s work in a commercial setting in Essex, where a large arable farm is using a Seed Terminator for the first time this harvest (see “Case study: Essex farm hopes to terminate ryegrass with cage mill”).
With the farm running two combines side by side, one with the Seed Terminator fitted and the other without, it provides a great opportunity to assess its efficacy. “We are going to see if we can put some well-designed comparisons in the field and overlay some small untreated patches so we can get a real measure of what’s going on,” Mr Cussans adds.
Agronomy shift
It is expected to be very effective on species that hold on to seed much later, such as Italian ryegrass, bromes and wild oats, all of which seem to be favoured by changes in agronomy practices – most notably a shift to “soil-first farming”, where cultivations are minimal.
Along with efficacy, there are a number of practicalities that need to be researched too, including how much seed is making it into a combine to be subject to the HWSC technique and how much goes into the harvested grain rather than being destroyed.
Mr Cussans says there is a danger that something like a seed mill could be prescribed to solve a problem, but seed losses at the header, seeds lodged and spread on the machine itself and weed seeds contaminating the crop grain could mean results aren’t as expected.
1. Seed Terminator
The Seed Terminator was developed and brought to market in Australia using the same concept as the original Harrington Seed Destructor, but with a slightly different design.
Integrated into the back of the combine, the Seed Terminator is mechanically driven, with the driveline from engine to straw chopper strengthened with additional pulleys and V-belts to deliver extra torque.
It uses the same two counter-rotating cage mills of previous incarnations, each with a central four paddle rotor and a set of screens.
As material moves through the assembly, weed seeds are subjected to four modes of action – shear, crush, impact and grind.
Seed Terminator says this results in a good kill rate at a speed range between 2,200-3,000rpm, maintaining efficacy under higher loads when harvesting conditions get tough.
While independent testing in Australia shows weed seed kill rates of up to 99%, in European conditions, high-capacity screens that enable the machine to cope with heavy crops will be used.
German-based company Zurn Harvesting has exclusive sales rights for the Seed Terminator in Europe after its launch at Agritechnica last year.
The company’s UK sales manager, George Dance, says these less-aggressive screens may result in slightly lower kill rates of 85-90%, depending on conditions.
Part of the machine’s development process has seen components aerodynamically optimised to reduce power requirement (although this still stands at 80hp) and minimise disruption to the combine’s airflow.
The optimisation of parts is also claimed to reduce wear, with maintenance requirements relatively low and moving parts simple and straightforward to remove and replace.
The Seed Terminator has a magnet tray incorporated into the design to stop any metal going through the mill, and temperature, vibration and blockage monitoring is all offered to the operator on a standalone box in the cab.
Growers can fit the unit to most modern high-horsepower hybrid combine models, including John Deere, Claas, Case-IH, New Holland and Agco.
However, the firm also fitted one of the eight Seed Terminators working across Europe to a straw walker machine in Sweden.
The system retails for approximately £80,000.
Case study: Essex farm hopes to terminate ryegrass with cage mill
Italian ryegrass has the potential to become a very damaging problem across HJ Fairs & Son’s 2,000ha near Colchester, and farm manager Chris Barron is optimistic that a Seed Terminator can help turn the tide against the competitive grassweed.
The farm has issues with blackgrass, but it’s the ryegrass that is causing the most concern.
Mr Barron says the chemical tools are not up to the task alone and, with high weed populations in patches, the cost of hand-roguing would be significant.
“It isn’t at the stage where it is hitting our yields hard, but we need to get on top of it soon, before it is completely uncontrollable.”
The farm employs a number of cultural controls and has tried fallowing and wholecropping the worst fields, but no combination has provided an adequate long-term solution so far.
With coverage and interest in HWSC techniques increasing in the UK, Mr Barron spotted the impact mill concept that’s been used to such good effect against annual ryegrass in Australia.
Although unsure whether it will be as effective in the UK, the hope is that it will provide a significant reduction in seed return at harvest and begin to make a dent in the weed seed bank across the farm.
Mr Barron approached Zurn Harvesting and Seed Terminator to see if he could work with them and trial the first unit on UK shores.
“Both myself and the boss were keen on the idea, but we looked at the cost and didn’t know how we could justify the investment without seeing some results first, so we agreed a seasonal hire this year,” says Mr Barron.
The unit has been fitted onto one of the farm’s two Claas Lexion 760s with the help of a local engineer. However, a number of adaptions were required, including to the driveline and straw chopper geometry to make it fit.
At the time of writing, the unit had only completed about 160ha of work and any conclusions on performance were hard to draw, but Mr Barron suspects combine horsepower could be an issue. “This season is a good one to try it, because we are dropping straw and the crops aren’t big. That’s giving us the power we need, but in a normal year I don’t think the 760 would have enough.”
With the combine up for changing soon, if the Seed Terminator proves effective, the farm is likely to invest in a more powerful Lexion to cope with the power draw.
“In principle it should work well, but it isn’t going to provide a quick fix. It will just be another tool as part of our long-term strategy,” adds Mr Barron.
2. Redekop Seed Control Unit
Canadian firm Redekop specialises in retrofit combine kit and has now ventured into the HWSC market in Europe with its version of an integrated seed mill – the Seed Control Unit (SCU).
It has already attracted interest from major manufacturers such as John Deere, which showed the SCU on its stand at Agritechnica – perhaps a sign that the technology will become a factory option in the near future.
As with any manufacturer, Redekop claims advantages over the other seed mills on the market, such as the unit’s integrated design. All milled material is thrown into the straw stream of the chopper to improve residue spread and distribution, while minimising the dust and debris kicked up around the rear of the machine.
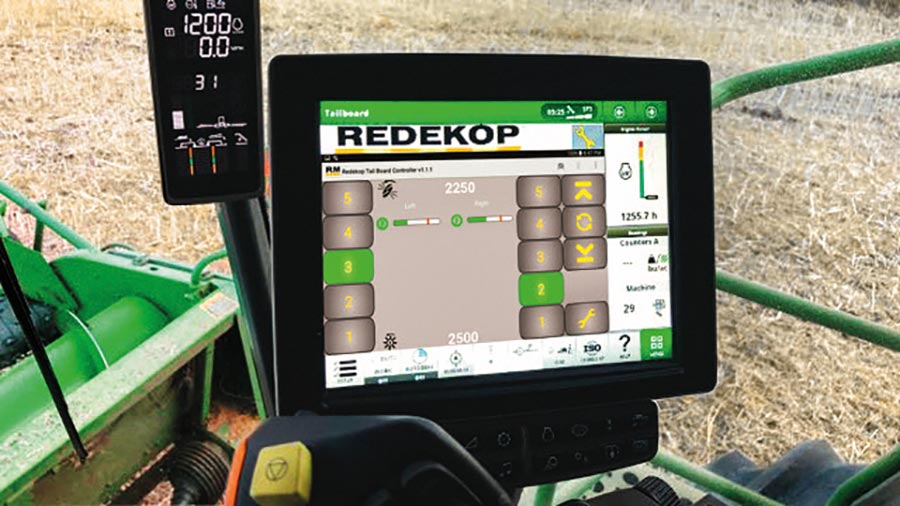
SCU can be controlled through the John Deere combine monitor
As the SCU moves with the chopper on its slide rails, access to sieves is easier. Electronics are also integrated, with Isobus enabling control of the unit through the combine’s operating terminal. There is also an option for a standalone screen where necessary.
The design of the internal mechanism itself is similar to other machines, consisting of two counter-rotating cage mills. However, the firm claims optimum kill rates with less power use – about 65hp under an average load.
The SCU is also quickly and easily engaged and disengaged via a splined drive sheave, meaning it can be turned off without removing any belts when dropping straw. This means horsepower isn’t wasted by running the SCU dry.
Installation is said to take about 30 hours and maintenance is minimal, with mills and fan blades coated with tungsten carbide for long life and lower operating costs.
The SCU will be sold across Europe by Oria Agriculture, a company specialising in bringing North American agricultural technology across the pond. One of its founders, Canadian Danea Armstrong, says at present the SCU is only available for John Deere combines, but kits for all other major brands will be available for harvest 2021.
Prices start at about £65,000 ex-installation, with overall cost varying depending on the combine make and model.
3. iHSD V12
The original trailed Harrington Seed Destructor was cumbersome and hard on the combine, so with levy money and help from the University of South Australia, its designers produced the iHSD, which integrated the technology into the back of the combine.
The first version was hydraulically driven and was beset with reliability issues, so manufacturer De Bruin Engineering has gone back to the drawing board and produced the all-new iHSD V12.
It has ditched the temperamental hydraulic system for a direct mechanical drive that has no gearboxes or 90deg transmissions, with just two belts and three inline pulleys now driving the impact mills direct from the engine.
The mills themselves have been turned from horizontal to vertical, fed by two high-speed cross-augers. A stone trap sits below the augers to avoid unwanted material being processed.
Being a simplified version of the iHSD, the V12 is likely to bring its purchase price point down to compete with more recent market entrants.
4. Tecfarm Weedhog
Western Australian company Tecfarm has taken a radically different approach to seed mill design with its new Weedhog, opening up the possibility of using the technology on smaller combines.
The company is a prominent supplier of chaff carts in Australia and these remain popular among mixed farmers, where chaff heaps are grazed by sheep or cattle.
However, sales have slowed since the introduction of seed mills, which offer a one-pass solution to controlling weed seeds without grazing or burning ahead of seeding.
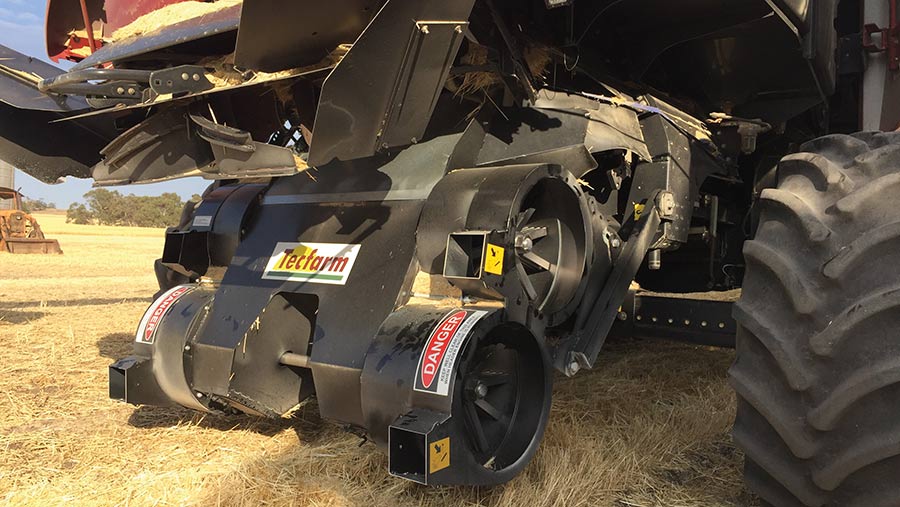
Tecfarm’s rotor arrangement has a much lower power demand than rival systems
With all other seed destroyers based on the Steadman cage mill design, which crushes material like coal into a very fine dust, horsepower requirement is high – about 80-100hp in most cases. This means that weed seed kill rates are very high, but they are only suitable for the top-end combines and wear and tear is a concern.
Seeing a gap in the market, ex-Bruce Rock farmer and Tecfarm founder Tom Lewis, along with son-in-law Matt Barrett-Lennard, looked to design and develop their own solution with a much lower power requirement.
Instead of the counter-rotating cage principle of competitors, the Weedhog uses two pairs of counter-rotating rotors enclosed in a chamber either side of the combine’s rear end.
Each rotor is made up of 18 rotor bars and the chaff fraction is fed into their path as they pass each other at 2,400rpm, about 500kph, smashing any weed seeds contained in the material.
Mr Lewis tells Farmers Weekly that tests with the prototype suggested a 90% direct kill of ryegrass seed. Field tests of the market-ready machine have shown a 75-85% direct kill depending on conditions.
This is in contrast to the more aggressive cage mill designs, which achieve kill rates in the high 90s, but have a much larger kill zone around the 360deg of the counterrotating cages.
Interestingly, development tests show that Weedhog’s system damages or scarifies surviving seed enough to encourage dormancy break or leave the seed open to pathogenic attack. This has seen overall control rates in stubble before seeding the next crop hit about 95%.
The concept also sees the very low mass chaff fraction find its way out of chamber relatively untouched, while higher mass seeds are smashed by the rotors, minimising dust and reducing blowdown requirements.
This, combined with the smaller impact area compared to the cage mill, means the Weedhog requires just 35-40hp, and this could be a major advantage for those running smaller combines or where crops are heavier and damper, such as northern Europe.
After finding a Perth-based engineering company to produce the Weedhog, the firm is now looking to establish the product across Australia after commercial release earlier this year. The initial design was for a Case IH combine, but tweaks are ongoing to enable to machine to be fitted to other major brands.
A Weedhog unit costs about A$60,000-65,000 (£33,000-35,800).
5. EMAR Chaff Deck
In 2017, a trial led by agronomy group Frontier investigated the effectiveness of the EMAR Chaff Deck and there are now several farms successfully using the concept across the UK.
Designed and made by Australian company Primary Sales, it essentially replaces the chaff spreaders and redirects the chaff fraction into 20-30cm bands in the combine’s wheel tracks. This sees weed seeds consolidated into wheelings and either left to rot or sprayed off with herbicide once germinated.
The Chaff Deck has been popular in controlled traffic farming (CTF) systems, as the compacted traffic lanes make a more hostile environment for the weed seeds. However, as long as a farm has RTK guidance and can fix A-B lines it can be effective, as the seeds are still confined in bands rather than spread across the field.
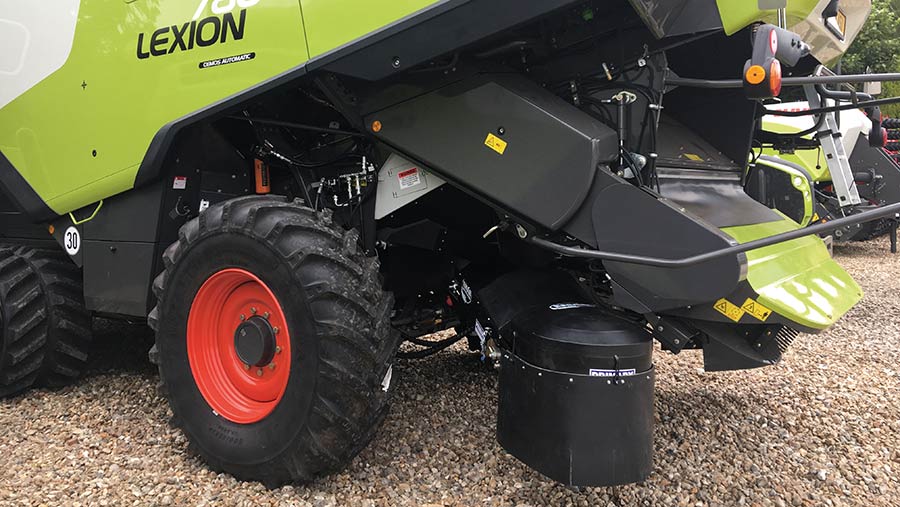
Chaff Deck lays material in wheelings to rot or be sprayed off with herbicide
Frontier’s crop production technical lead Paul Fogg says that initial research focussed on blackgrass, as it is the main concern for many growers.
Blackgrass typically starts shedding seed in early July, depending on the season, so working out how much seed could be captured in the combine was the first key question.
In its first year and in a hybrid winter barley crop, about 30-50% of blackgrass seed was retained in the heads and showed there was a potential to make significant reductions in seed return in earlier harvested crops.
Their work has since monitored the Chaff Deck working in a whole range of crops over a longer period and has proven that blackgrass populations can be consolidated, with a six-fold increase in plants/sq m in chaff lines compared to the rest of the field.
With weed species that hold on to seed for longer, such as ryegrass, the potential will be even greater.
The Chaff Deck has been proven able to cope with higher biomass crops in UK conditions and pioneering UK users have worked with Primary Sales to finesse design to optimise performance.
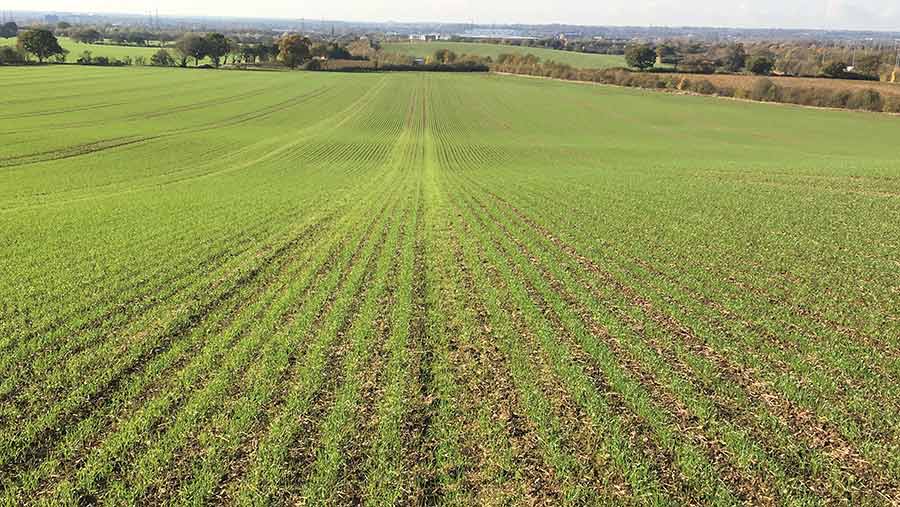
Brome shown germinating in 20-30cm bands, where it can be more easily targeted
One example is that the straw chopper can now be disengaged without lifting the Chaff Deck up with it, meaning users can drop and bale straw and still reap the benefits of chaff tramlining.
When purchasing a Chaff Deck, customers are provided with a kit that includes the frame that mounts on to the combine chasses and side skirting that diverts chaff onto conveyors. These are made from cleated 24oz draper belt with V-tracking for self-alignment.
Moulded covers with rubber skirts finish the assembly, which is designed to positively place the chaff in tramlines. It is adjustable to suit any wheel track setting of the combine and installation should take about 20 hours.
As with Redekop’s SCU, Oria Agriculture has exclusive rights to distribute the EMAR Chaff Deck in Europe. Kits are available for all major combine brands and retail prices start at about £15,000 ex-installation.
6. Chaff collection kit
Chaff capture has been gaining interest in Europe, and not solely for weed control purposes.
Two French manufacturers – Thievin and Tierhart – have been offering retrofit turbine kits to manage chaff at harvest for many years, initially aimed at controlling weeds in organic systems.
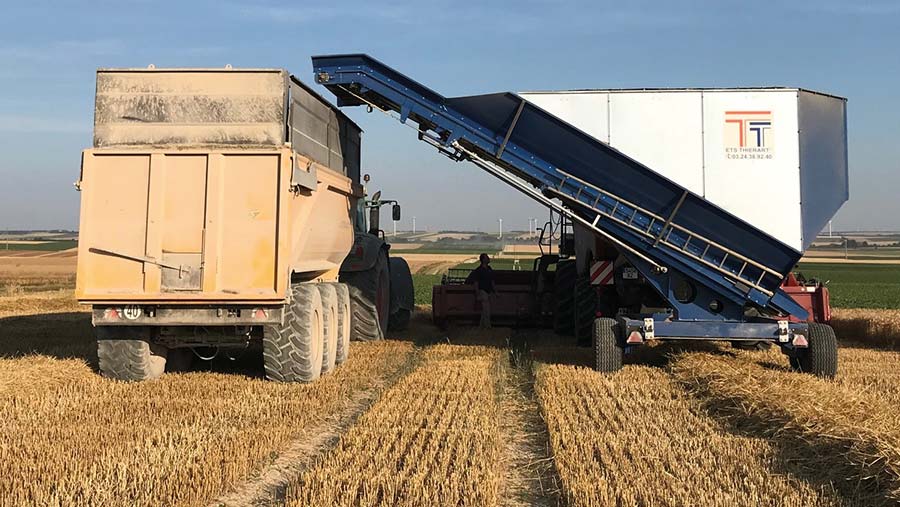
Tierhart’s chaff collection system uses a conveyor to load the material straight into a trailer
The kit options can either direct chaff on top of the straw swath for baling or blow it into a trailer, either towed behind the combine (chaff cart) or driven alongside with a tractor.
Globally, the method is proven to significantly reduce weed seed return, but a stumbling block for adoption in Europe has always been cost and what to do with the chaff once it’s captured.
In France, collected chaff is mostly used for poultry litter or biogas feedstock, but an EU project has also looked at its potential in ethanol production.
Tierhart offer a very simple turbine for small combines with sub-6m headers, or its V3 turbine that enables the operator to either blow chaff on the swath or into a trailer.
The V3 costs about €20,500 (£18,500) ex-installation. It also produces chaff carts for collection behind the combine, some of which tip chaff in a pile on the field and the more sophisticated have a conveyor system to load into trailers. Prices range from €25,000-€41,000 (£22,500-£37,000).
Could exhaust gas be harnessed to kill weed seeds?
Researchers at Denmark’s Copenhagen University have shown heat generated from a combine’s exhaust system has the potential to kill weed seeds and could be integrated into harvesting operations in the future.
Several weeds, including blackgrass, cranesbill and mayweed, were subjected to temperatures of 75C, 85C, 110C and 140C for two, four and six seconds.
The lowest two temperatures were not hot enough to reduce weed germination after all exposure times.
Some seeds were still able to germinate after 4s exposure of 110C, while exposure to 140C for 4 and 6s repressed germination of all species.
The research concluded that there might be merit in developing combines in a way that exploits exhaust gas to either kill or reduce the ability of weed seeds to germinate before they are returned to the field.